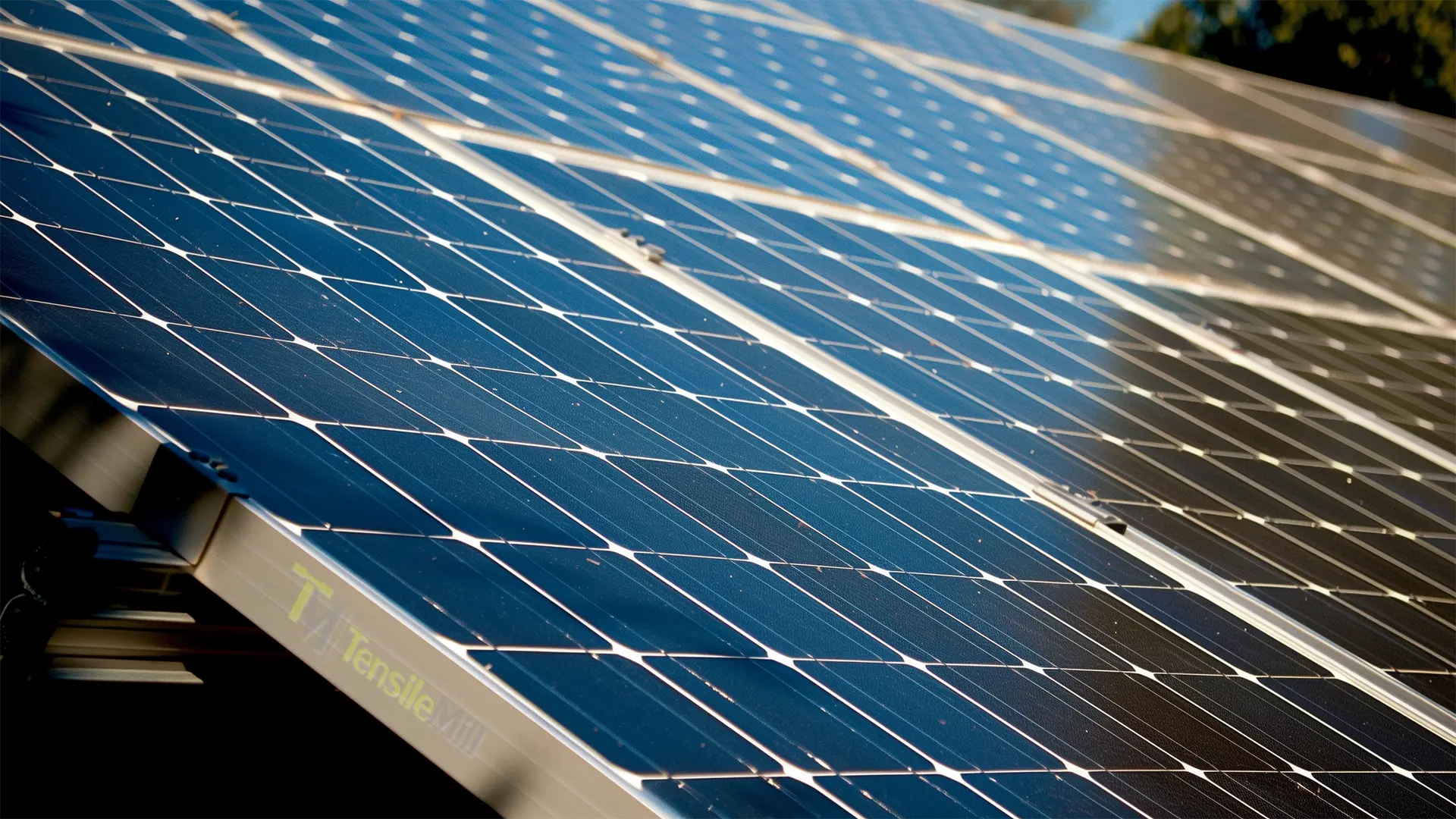
In the quest for sustainable solutions to the world's growing energy needs, renewable energy has become an integral part of innovation and environmental stewardship. At the heart of green technologies - such as solar panels, wind turbines, and bioenergy converters - lies a diverse array of materials, each selected for their unique properties and abilities to convert natural resources into usable energy efficiently. These materials are not passive components but are actively involved in renewable energy capture, conversion, and storage.
Renewable energy systems' efficiency and durability depend heavily on the materials used in their construction. Solar panels require high light absorption and conversion capabilities to efficiently transform sunlight into electricity. Similarly, materials used in wind turbines, including those for the blades and structural components, must be of exceptional strength and fatigue resistance to withstand the physical stresses of wind energy conversion.
However, the demand for materials that combine high performance with environmental sustainability presents a significant challenge. These materials must be capable of withstanding a variety of stresses over their operational lifetime, including mechanical load, temperature variations, and exposure to harsh environmental conditions. However, they must also be produced in a manner that minimizes environmental impact. This includes considerations for the energy and resources consumed in their production, as well as their recyclability and life cycle carbon footprint.
In light of these challenges, the importance of tensile testing in the development and optimization of materials for green energy becomes clear. This rigorous evaluation process is pivotal in advancing renewable energy technologies. Hence, tensile testing of materials will be a main topic in our exploration of renewable energy, bridging the gap between material science and sustainable energy solutions.
What is Tensile Testing?
Tensile testing, also known as tension testing, is a procedure in engineering and materials science, where a material is subjected to controlled tension until it fails. This testing method is necessary for understanding the strength, ductility, and fracture point of materials. It serves as a foundational component in assessing their suitability for different applications, including renewable energy technologies.
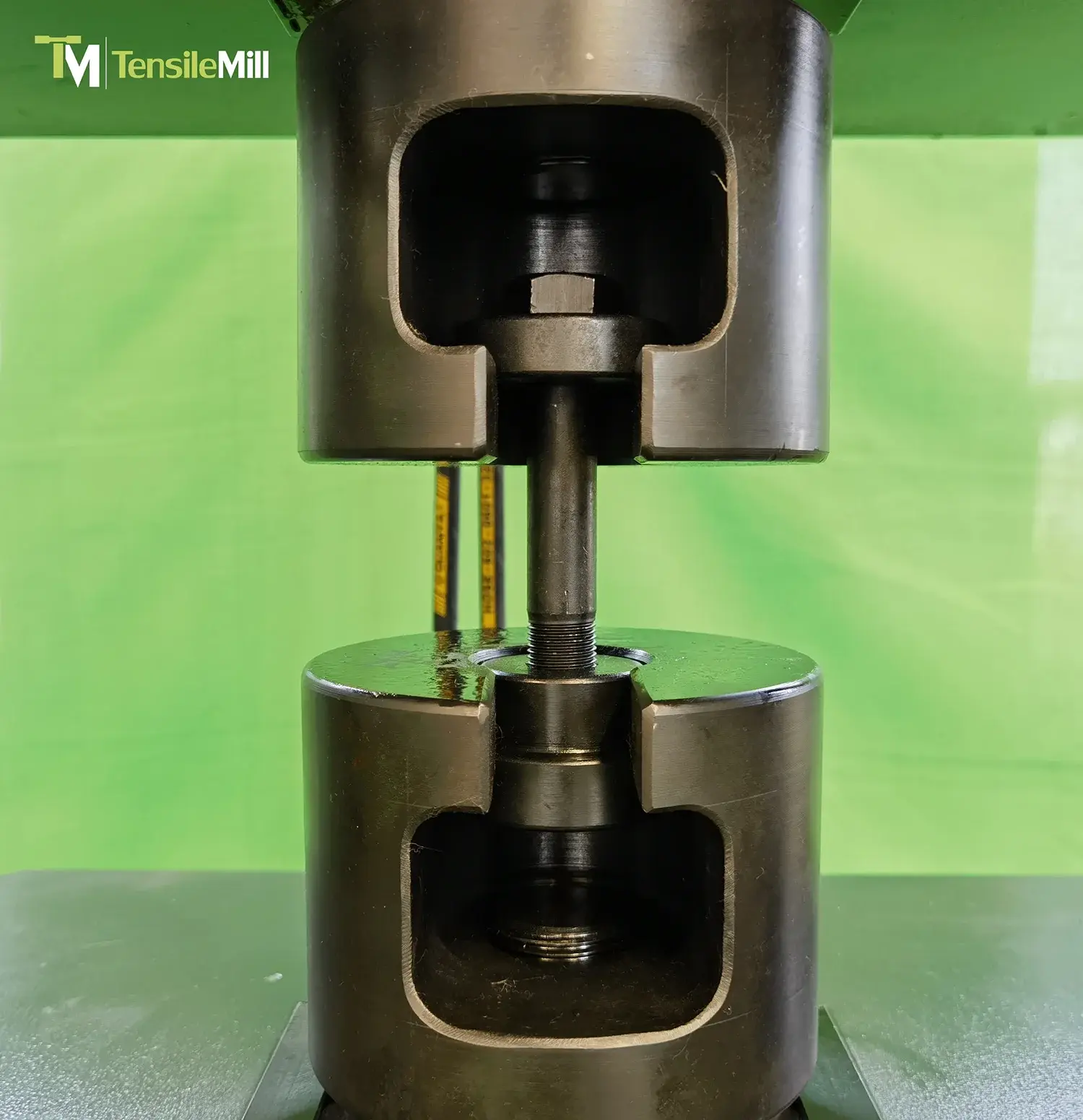
At its core, tensile testing aims to measure how much force a material can withstand before it breaks and how much it can stretch, thereby providing vital data on its yield strength, ultimate tensile strength, ductility, and strain hardening characteristics, among others. The process involves preparing a sample, often of a specific shape and size, and then pulling it apart with a tensile test machine at a constant rate until it fractures. The equipment used, such as grips and extensometers, plays a significant role in accurately measuring the force applied and the material's elongation.
Tensile testing should never be underestimated, especially for clean energy systems. Materials must be able to endure an array of stresses over their operational lifetime, including significant mechanical loads and environmental conditions. By determining the mechanical properties of materials through tensile testing, engineers can make informed decisions about material selection, making sure that renewable energy systems are both efficient and durable.
Tensile testing also extends beyond material strength and ductility. It is instrumental in quality assurance, material selection for specific applications, research and development of new materials, and failure analysis. Through tensile testing, industries can verify that materials meet the required standards and specifications, preventing failures and ensuring product reliability.
The Significance of Tensile Testing in Renewable Energy
The significance of tensile testing in renewable energy technologies extends far beyond simple material evaluation. This form of testing is essential for determining the strength and failure points of materials used in green energy systems like wind turbines and solar panels.
Renewable energy sectors, such as wind and hydrogen energy, heavily rely on tensile testing for material selection. For instance, the choice between fiberglass and carbon fiber for wind turbine blades hinges on tensile testing results. They reveal that carbon fiber's superior stiffness and strength can lead to more efficient energy capture. Similarly, high-strength composite materials used in hydrogen storage tanks are subjected to tensile testing to verify they can safely contain hydrogen under extreme pressures.
Tensile testing's relevance stretches to renewable energy infrastructure integrity. It aids in the development of components like wind turbine blades, making sure they can handle environmental impacts while maintaining efficiency.
The choice of tensile testing equipment is crucial, reflecting the unique demands placed on materials by the renewable energy sector. The equipment must offer precision, flexibility, and reliability, and comply with international testing standards, to accurately assess the sustainability and efficiency of the materials and components tested.
Moreover, in the burgeoning field of hydrogen technology, mechanical materials testing, including tensile testing, is vital for evaluating materials that must operate safely under the influence of hydrogen. This includes components used in hydrogen production, transport, storage, and energy conversion, where materials are challenged by hydrogen's propensity to cause embrittlement and weaken structural integrity.
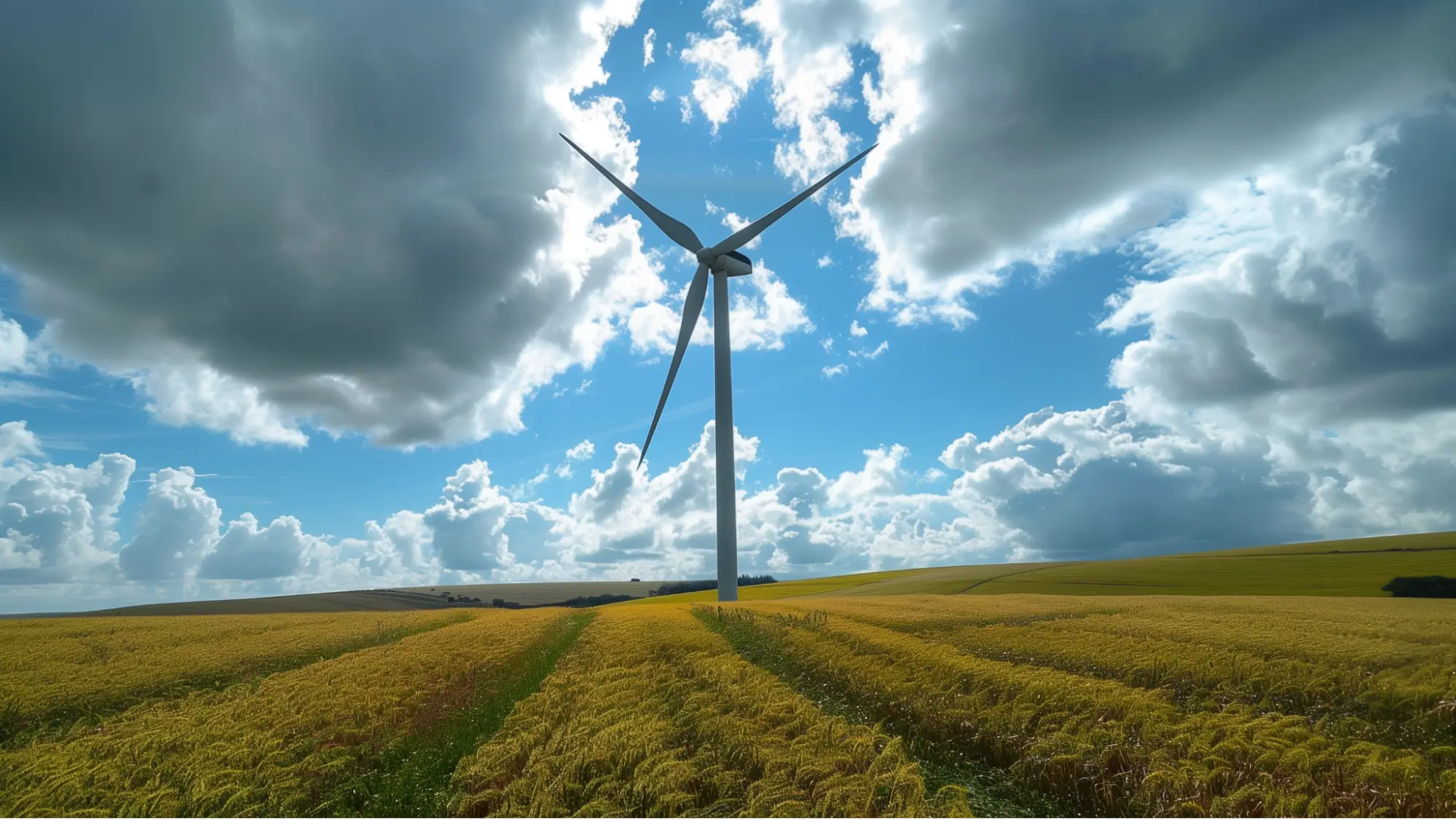
Types of Materials Used in Renewable Energy Systems
To harness, convert, and store energy generated by renewable sources, green energy systems rely on materials of different kinds. These materials are selected based on their unique properties, which contribute significantly to renewable energy technologies' efficiency and sustainability. Here are a few examples of such materials:
Solar Energy Technologies
Photovoltaics (PV): High-purity, low-cost silicon is widely used in PV modules for its efficiency in converting sunlight into electricity. Innovations such as thin graphene layers enhance these properties further, reducing costs per watt and improving durability with more robust packaging.
Concentrating Solar Power (CSP): CSP systems use heliostats or mirrors to focus sunlight, heating molten salt to drive turbines. Advances in materials, like high-nickel content alloys and supercritical CO2 systems, facilitate reduced scale operations and lower costs through additive manufacturing.
Wind Energy Technologies
Wind energy sustainability emphasizes not just material efficiency but also economic viability. Siemens Gamesa's advancements illustrate this with larger, smarter turbines. These innovations necessitate materials that defy the square-cube law through better aerodynamics and the use of high-quality manufacturing processes and materials like glass-carbon hybrid composites for lighter, stiffer blades.
Energy Storage Technologies
Electrochemical energy storage, particularly lithium-ion batteries, dominates current energy storage solutions. This technology is materials-intensive, requiring industrial chemicals, precious metals, and rare earth elements. Efforts are ongoing to reduce costs and enhance efficiency by optimizing materials and manufacturing processes.
Next Generation Materials
The Department of Energy highlights the importance of innovative materials across renewable technologies, focusing on advanced composites, engineered polymers, and low-density/high-strength metals or alloys. These materials are ideal for harsh environments, offering improved thermal and degradation resistance, high-performance functionality, and lower energy costs.
Hybrid and Composite Materials
Renewable energy applications often make use of hybrid and composite materials for their unique properties. For instance, wind turbine blades and solar panel frames may incorporate composites for lightweight and strength, enhancing energy capture and generation efficiency.
Analyzing Tensile Test Data
Analyzing data from tensile tests is a basic need for understanding materials' mechanical properties. Tensile test data interpretation involves several key parameters.
The stress-strain curve is a fundamental aspect of tensile testing, representing material's response to applied force. Initially, the relationship between stress (force per unit area) and strain (deformation) is linear, where the slope defines Young's Modulus, indicating material's stiffness. This part of the curve helps determine how well a material can withstand mechanical loads without deforming permanently.
Yield strength is identified on the curve as the point at which the material begins to deform plastically. This means it won't return to its original shape after the load is removed. This value is crucial for designing components that endure operational stresses without permanent deformation.
Ultimate tensile strength (UTS) is the maximum stress a material can withstand while stretched or pulled before breaking. It is a critical measure of a material's capacity to resist breaking under tension. For renewable energy materials, a high UTS indicates a capability to withstand extreme conditions, such as high wind speeds for turbine blades or stress from load-bearing in solar panel frames.
Elongation at break, expressed as a percentage, measures how much a material can stretch before breaking. This property indicates material's ductility, a vital factor for materials that need to absorb high levels of energy without fracturing, such as shock absorbers or components that face cyclic loading.
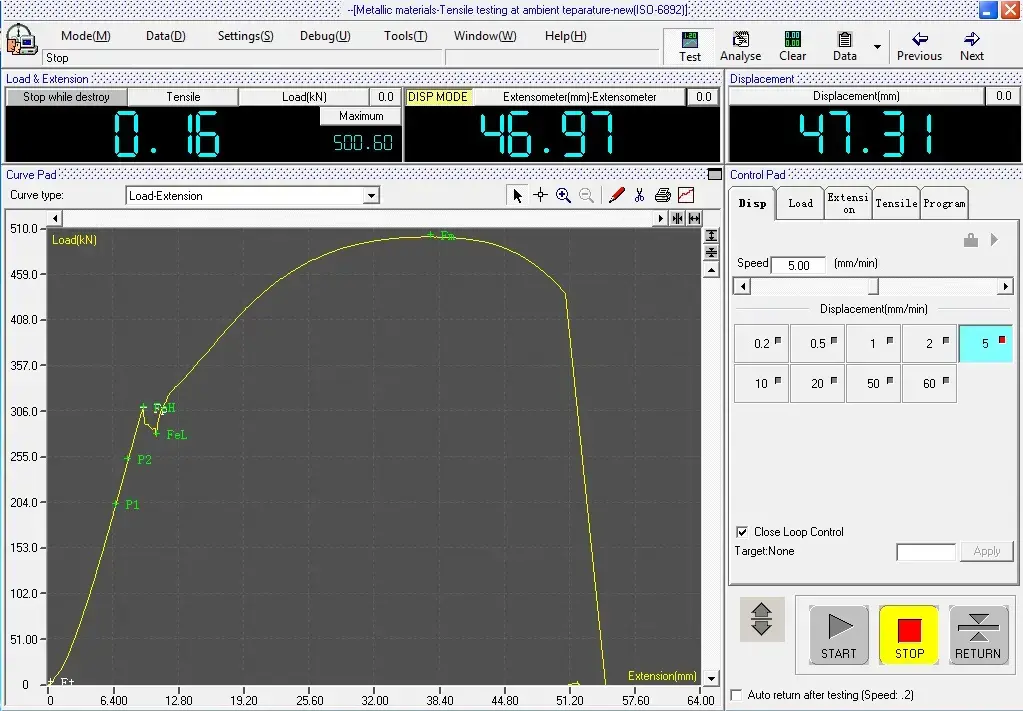
Importance of Reliable Tensile Testing Equipment in Renewable Energy
Throughout the previous sections of this article, we saw that proper equipment is more than just a checkpoint. The choice between high-quality and substandard testing equipment can significantly influence renewable energy technologies' durability, efficiency, and safety, impacting economic viability and environmental sustainability.
Consequences of Choosing Substandard Equipment
Choosing inferior tensile testing or specimen preparation equipment can have dire consequences. Inaccurate testing can lead to incorrect assessments of mechanical properties, such as strength, ductility, and fatigue resistance. For instance, wind turbine blades that have not been adequately tested for tensile strength and fatigue resistance may fail prematurely, leading to costly repairs and downtime. Similarly, solar panel frames and structural supports that do not meet strength requirements could succumb to environmental pressures, compromising the entire system's integrity.
The economic implications of unreliable testing equipment extend beyond the immediate costs of component failure. Indirect costs, including lost production, increased maintenance, and potential safety hazards, can substantially increase renewable energy projects' operational expenses. Furthermore, failures attributed to inadequate material testing can tarnish companies' reputations, leading to a loss of investor confidence and potential legal liabilities.
Advantages of High-Quality Tensile Testing Equipment
Conversely, selecting high-quality tensile testing equipment and tools for tensile specimen preparation offer numerous benefits. Accurate and precise testing ensures that materials selected for use in renewable energy systems are optimally matched to the demands of their application. This approach to material selection helps in maximizing the efficiency of renewable energy systems, thereby improving their economic and environmental performance.
High-quality testing equipment, capable of simulating a wide range of operational conditions, allows for comprehensive evaluation of material behavior under stress. This capability is crucial for developing innovative materials and components designed to advance renewable energy technologies' performance and sustainability. Moreover, compliance with international testing standards, ensures that testing results are recognized and validated globally, streamlining the certification process for advancing materials and technologies.
Introducing Our Servo Hydraulic Universal Testing Machine
In every sector where precision in measurements carries significant weight, from aerospace to automotive, and notably in industries like renewable energy, the demand for reliable, high-precision equipment is a must. Our Servo Hydraulic Universal Testing Machine 2000kN is designed to meet this critical need for an array of applications. This advanced testing machine is our solution to the industry's call for equipment that delivers precise, reliable results.
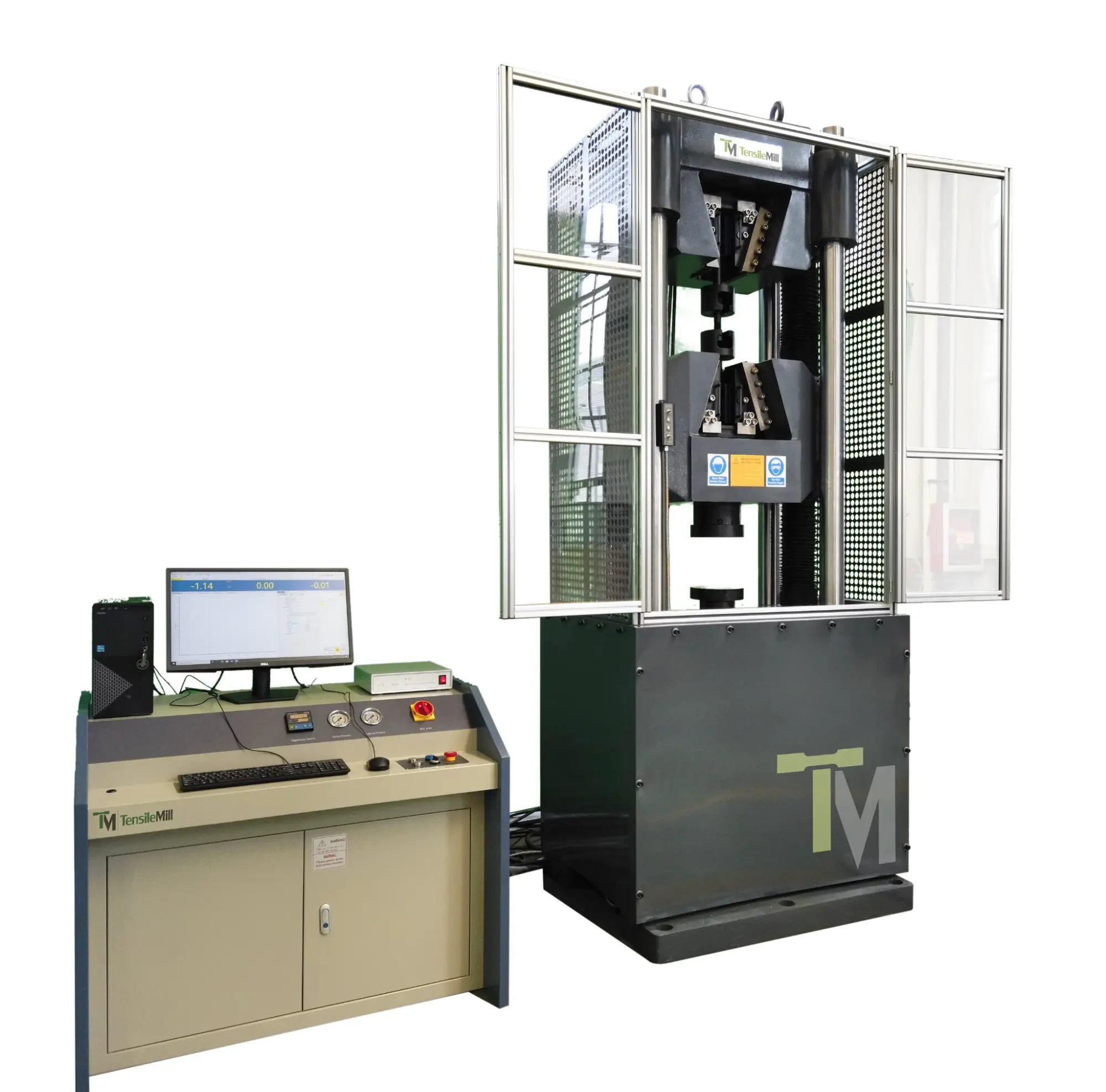
This cutting-edge testing device is not just a piece of machinery, but a leap in quality assurance for materials that are used in many industries. In compliance with international standards such as ASTM E4 and ISO 750001, and capable of conducting tests under industry benchmarks like ISO 898 and ASTM F606, this Servo Hydraulic Universal Testing Machine is engineered for versatility and precision. Its design incorporates a robust hydraulic-operated tensile grip and dual testing spaces, allowing both tensile and compression tests to be executed with maximum accuracy.
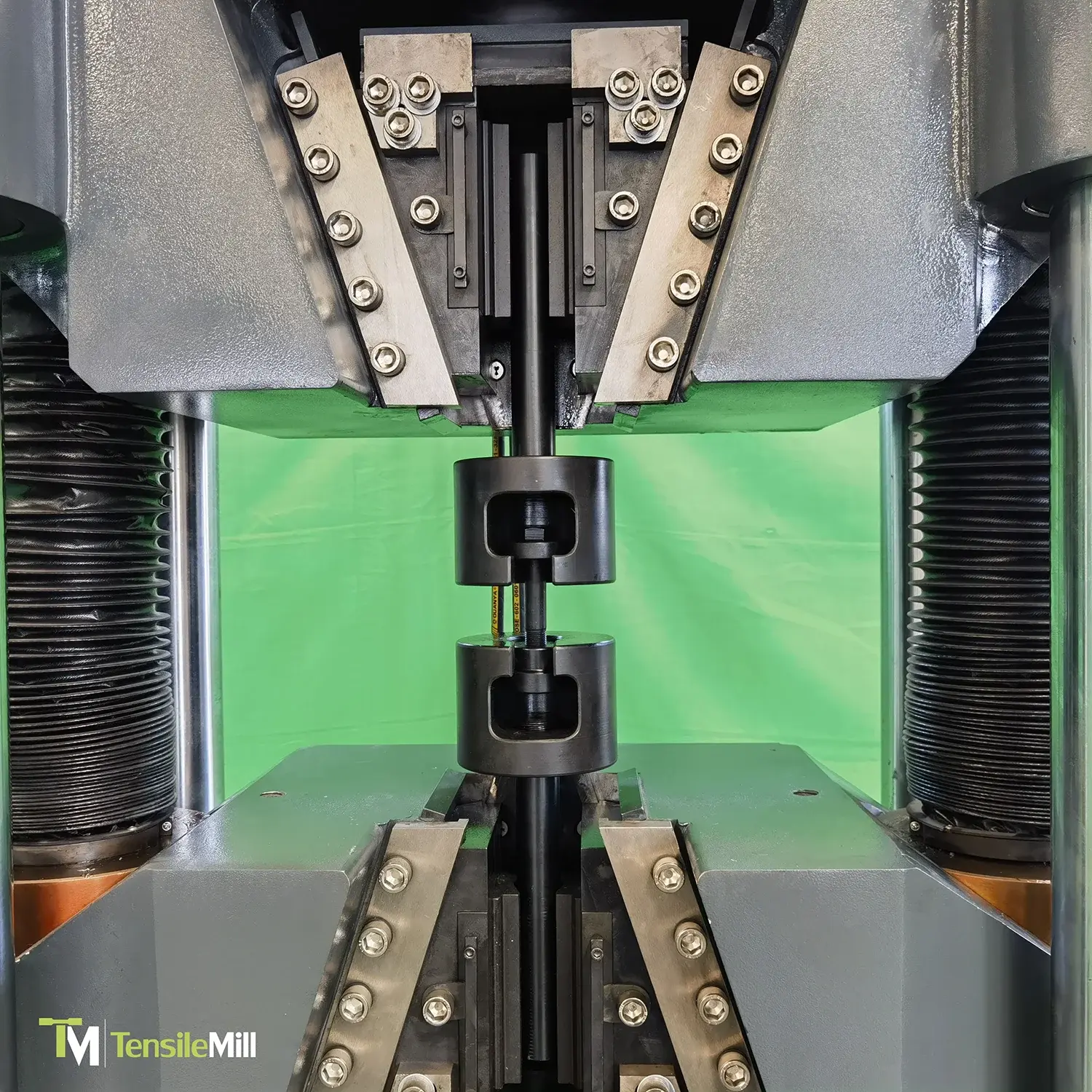
The significance of this machine in energy-renewable material testing lies in its servo-hydraulic system, specifically designed for high-strength nut and bolt testing. Such precision guarantees fasteners' reliability, a critical component of renewable energy systems' safety and efficiency. The sophisticated control system, based on DSP technology, enables three-closed loop control (load, displacement, strain), facilitating constant loading rate control, displacement control, strain control, and programmable control to suit varied testing requirements.
Moreover, the accompanying Maxtest testing software expands its utility, supporting multiple load cells and extensometers. Our software is capable of displaying real-time data, multiple curves, and critical points like yield point and Elastic Modulus on the curve. This enhances the machine's analytical power, providing invaluable insights into material behavior under stress.
The Role of Standards and Certification in Renewable Energy
By establishing a common set of criteria for design, performance, and safety, international standards facilitate the widespread adoption and integration of green technologies. Regular reviews and updates by international committees of technical experts help to make sure that these standards evolve with technological advancements and changing regulatory requirements.
Certification, in turn, verifies compliance with these standards. It acts as a risk-mitigation tool, especially helpful for small-scale projects seeking financing. The International Renewable Energy Agency (IRENA) has identified over 570 standards in the “green” energy field, highlighting their importance in the successful deployment of renewable energy technologies. However, gaps have been identified, particularly in standards covering post-installation aspects such as operation, maintenance, and repair, signaling an ongoing need for development and refinement.
Tensile testing standards, such as ASTM E8/E8M for metallic materials, are fundamental in renewable energy. These properties guarantee the durability and reliability of components like wind turbine blades, solar panel frames, and support structures against environmental challenges.
Components in Renewable Energy Systems Evaluated for Tensile Strength
There is a huge list of components evaluated for tensile strength in renewable energy systems. Here is a list of these components:
- Wind Turbine Blades: A key component of wind turbines, these blades are made of carbon fiber and fiberglass, which are tested for strength and fatigue resistance.
- Solar Panel Frames: Structures that hold solar panels; typically made of aluminum or steel, requiring durability tests against environmental stressors.
- Photovoltaic (PV) Modules: The active component of solar panels that convert sunlight to electricity; materials like silicon undergo tensile testing for efficiency and durability.
- Support Structures and Foundations: For wind turbines and solar farms; must endure loads, vibrations, and weather conditions, often made of reinforced concrete or steel.
- Nacelles of Wind Turbines: House critical components like the generator and gearbox; materials tested for resistance to dynamic loads.
- Rotor Shafts and Bearings: Required for wind turbine operation; undergo tensile testing to ensure they can handle mechanical stresses.
- Hydrogen Storage Tanks: Key to hydrogen energy storage; materials need to withstand high pressure and prevent hydrogen embrittlement.
- Electrical Cables and Connectors: For energy transmission; tested for mechanical endurance without compromising electrical performance.
- Bioenergy Converter Components: In bioenergy systems, components like digester tanks and piping are tested for strength and chemical resistance.
- Gearboxes and Drive Trains: In wind turbines, these components transmit power from the rotor to the generator; materials are tested for durability under varying loads.
- Mounting Systems and Racks for Solar Panels: Ensure stability and orientation of solar panels; materials are tested for load-bearing capacity and longevity.
- Seals and Gaskets: In all renewable energy systems, these components prevent leaks and protect sensitive parts; materials are tested for elasticity and tensile strength.
- Blade Pitch and Yaw Control Systems: For wind turbines, these systems adjust blade orientation; components are tested for operational reliability under load.
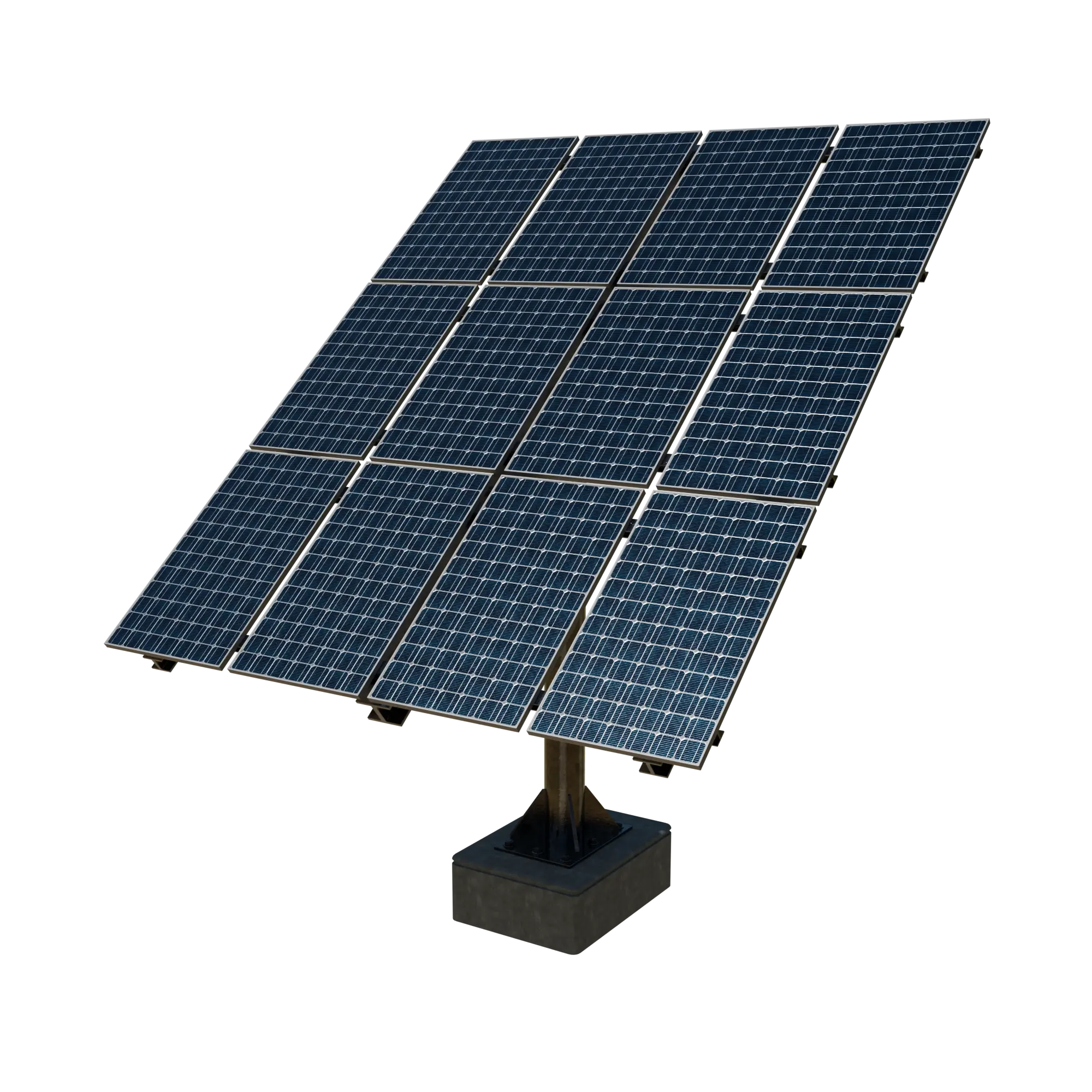
The Economic Impact of Tensile Testing in Renewable Energy
As we can see there are a number of reasons why tensile testing is important. The selection of materials, influenced by tensile testing, balances performance with cost-effectiveness. For instance, the shift from fiberglass to carbon fiber for wind turbine blades, prompted by tensile testing insights, has resulted in blades that are not only lighter but can also lead to increased energy capture efficiency due to their superior stiffness and strength.
Although carbon fiber may reduce blade mass by up to 25% compared to fiberglass, economic factors such as cost must be considered in material selection. Tensile testing helps identify materials that offer the most efficient blend of performance, durability, and cost-efficiency, leading to more sustainable, efficient, and economically viable renewable energy solutions.
Moreover, renewable energy has a substantial economic impact. In Scotland, for instance, the renewable energy sector, with its comprehensive supply chains, supports significant economic activity. This industry generated £6.1 billion, supporting 13,600 full-time equivalent employment directly in 2021. Including spill-over effects, the sector supports over £10.1 billion of output, over £4.7 billion of Gross Value Added (GVA), and more than 42,000 jobs across the Scottish economy. As a result, this demonstrates the fact that the renewable energy sector makes a substantial contribution to the economy, underpinned by rigorous material testing and innovation.
Advancing Renewable Energy with Tensile Testing
From wind turbine blades to solar panel frames and hydrogen storage tanks, tensile testing guarantees durability and performance, guiding material selection to make sure that each component can withstand its operational environment.
Further reinforcing the significance of tensile testing, we have seen how the choice of materials - shaped by rigorous testing - marries environmental sustainability with economic viability. The transition from fiberglass to carbon fiber in wind turbine blades, for instance, underscores the delicate balance between performance enhancement and cost-effectiveness, a balance that tensile testing helps to achieve.
We have also highlighted the necessity of selecting high-quality tensile testing and specimen preparation equipment. The Servo Hydraulic Universal Testing Machine 2000kN exemplifies cutting-edge solutions, so renewable energy companies can rely on precise, reliable results to drive forward their innovations.
For those seeking further information or assistance with services related to tensile testing or tensile sample preparation, TensileMill CNC is at your service. You can contact us directly or request an online quote. Our team is dedicated to supporting all your material testing needs. We understand the complexities involved in renewable energy and are committed to providing the tools and expertise needed to navigate material testing challenges. Get in touch with us today to learn how we can help enhance the sustainability and efficiency of your renewable energy projects.