International standards: ASTM E4 and ISO 750001
Test standard: ISO 898-1: 1999, ISO 898-2: 1992, ISO 898-6: 1994, ASTM F606-07 GB/T 1231-2006 and other industry standards.
Description
The Servo Hydraulic Universal Testing Machine 2000kN provides a reliable testing solution for evaluating materials' mechanical properties. This state-of-the-art test device is thoughtfully designed, featuring a solid structure and utilizing a hydraulic-operated tensile grip. Furthermore, its two distinguished test spaces facilitate both tensile and compression testing with maximum accuracy, making it a crucial asset for laboratories and the industrial quality control sectors.
This computer control servo hydraulic universal testing machine is mainly used for max. testing force, tensile strength of bolt and nuts, etc fasteners.
It adopts precision Italian ATOS servo valve hydraulic power pack to load, high precision load cell to measure testing force, photoelectric encoder to measure displacement. It is three closed-loop control (constant load, displacement, strain).
Bolts grade: 8.8, 10.9 and 12.9
Bolts specification: M6- M56
TM-SHM2000 Class A | |
Class | A |
Max. testing force (kN) | 2000 (449617.88 lbf) |
Accuracy of testing force | Φ15-Φ70 |
Round specimen diameter range (mm) | 10-70 |
Flat specimen thickness range (mm) | 120 |
Flat specimen width range (mm) | 800 |
Tensile space (mm) | 700 |
Compression space (mm) | 8.8 grade ≤M56 10.9 grade ≤M52 12.9 grade ≤M48 |
Bolt test specification | 250 |
Max. piston stroke (mm) | Φ15-Φ70 |
Power supply | 220V / 480V ±10%, 50Hz, three phase |
Work environment | Room temperature~ 40°C Relative humidity≤ 80% |
Dimension of load frame | 43.30x46.85x124.00-inches 1100x1190x3150 mm |
Dimension of control cabinet | 45.27x34.25x25.60-inches 1150x870x650 mm |
Weight | 19,840 lbs / 9,000 kg |
Servo Hydraulic Universal Testing Machine 2000kN Load Frame Structure
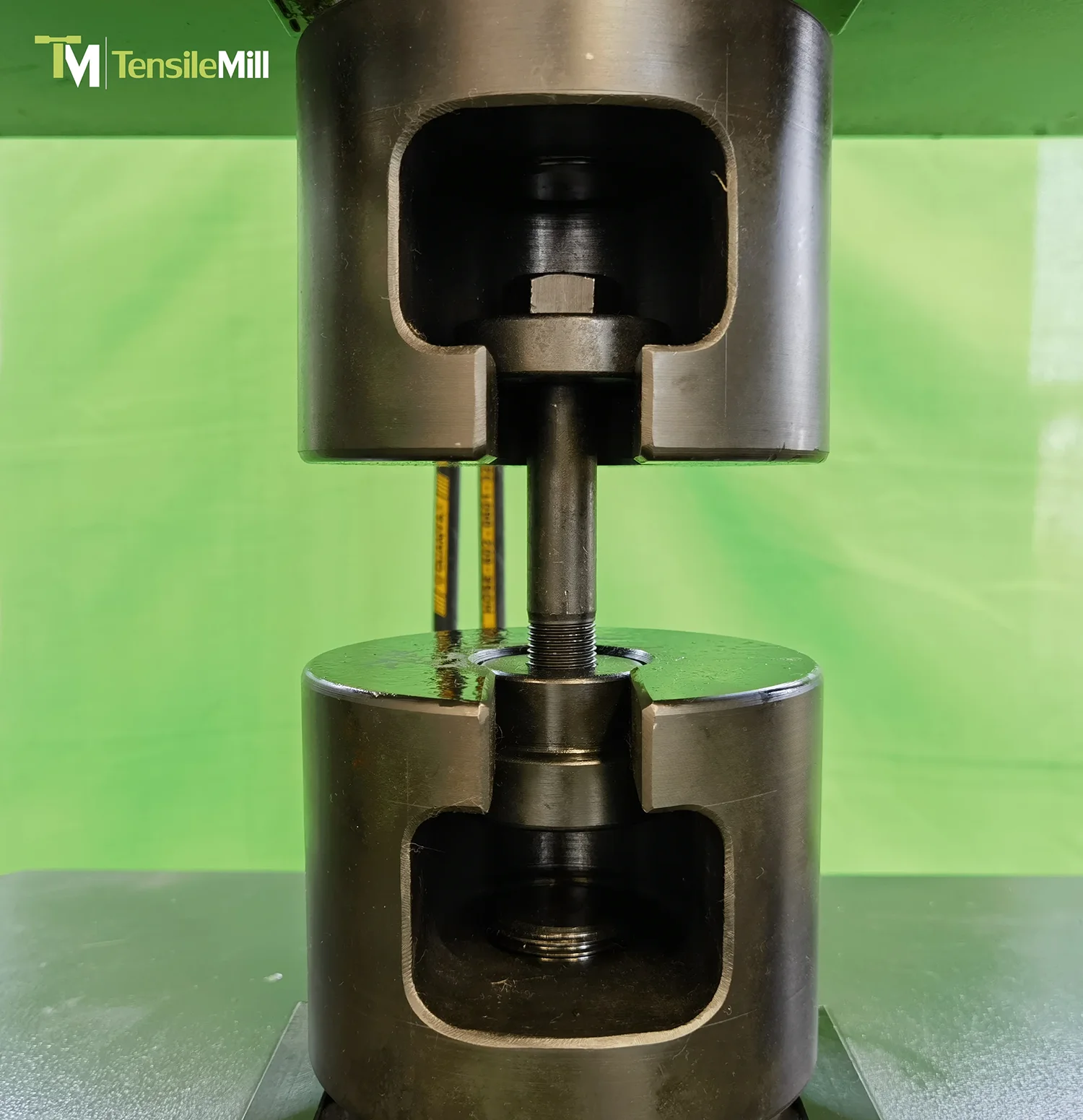
- It features a structure with 4 columns and 2 leading screws, ensuring the utmost durability.
- The hydraulic-operated tensile grip facilitates ease of operation.
- The upper test space, located between the upper crossbeam and the moving crossbeam, is designated for tensile testing. Meanwhile, the lower test space, positioned between the moving crossbeam and the workbench, is intended for compression and bending tests.
- High accuracy is achieved as the load cell directly measures the testing force.
- The chain-type transmission system is straightforward to maintain.
- To prevent aging and wear issues, the oil cylinder's clearance seal does not utilize O-seal rings.
- The half-open tensile jaw seat surpasses the fully-open type, ensuring the mouth of the tensile jaw seat remains free from deformation and 100% prevents slippage during tensile testing.
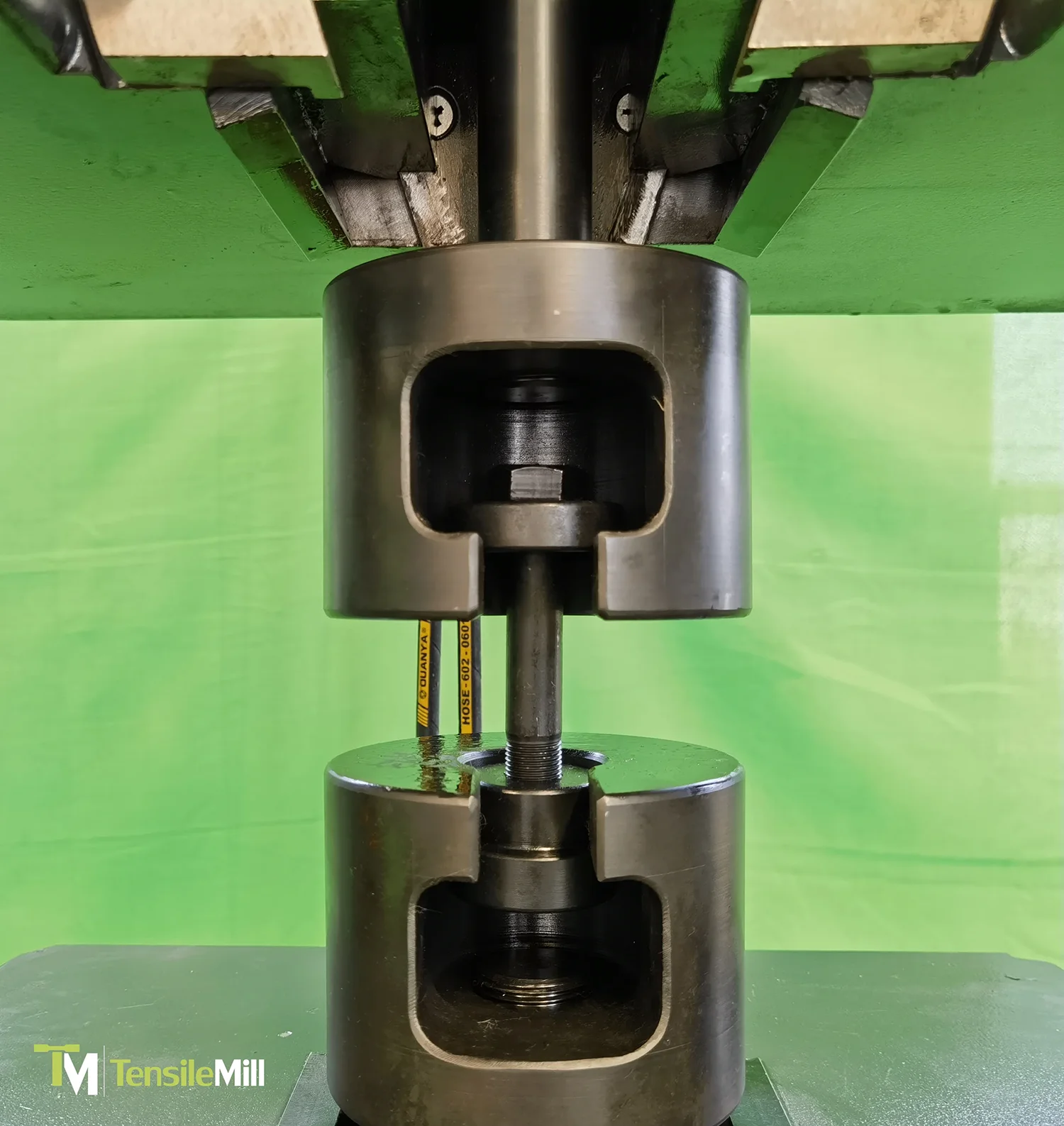
Servo Hydraulic Universal Testing Machine 2000kN Standard Configuration
Name | Description | Qty. | |
Main machine | Load frame | Dual space, class 0.5 | 1 set |
Load cell | Built in the load frame | 1 set | |
Displacement encoder | 1 set | ||
Motor and speed reducer | 1 set | ||
Power pack | Servo valve | Italian ATOS brand | 1 set |
Oil pump | Japanese NACHI brand | 1 set | |
Oil pump motor | 1 set | ||
Solenoid valves, Filter | 1 set | ||
Cooling fan | 1 set | ||
High pressure oil hoses | 1 set | ||
Grips and fixtures | Bolt and Nut Tensile Holder | according to the customer's bolt and nut's grade and diameter | 1 set |
Compression platen | 210x210mm | 1 set | |
Controller | AD-18000 | 1 set | |
Software | MaxTest | 1 set | |
Accessories | Operation manual | 1 set | |
Software manual | 1 set | ||
Warranty card | 1 set | ||
Quality certificate | 1 set |
Servo Hydraulic System for High Strength Nut and Bolt Testing
Servo hydraulic universal testing systems are a crucial role in the industry. They ensure the quality and reliability of nut and bolt systems. Such systems provide precise and controlled testing conditions, allowing manufacturers to assess the strength, durability, and performance of fasteners with the highest accuracy possible. In its turn, you get meticulous product safety, reduced downtime, and improved overall efficiency.
Servo Hydraulic Universal Testing Machine 2000kN Software Operation
Maxtest testing software is applied to all kinds of material testing machines, such as electromechanical UTM, hydraulic servo UTM, screen display hydraulic UTM, and horizontal tensile testing machine, etc. It only needs change it's configuration files.
It is a powerful testing software supporting four different load cells and eight different extensometers measuring. It supports clip-on extensometer, large travel extensometer, video extensometer, etc.
Control system based on DSP technology, PCI-E control card, total three-closed loop control (load, displacement, strain). It can execute constant loading rate control, constant displacement control, constant strain control and program control.
It real time display load, displacement and extension, multiple curves, like load-time, load-displacement, load-extension, stress- strain, etc. These points, like yield point, Rp, Rm, Elastic Modulus can be marked on the curve.
Service Plan
TensileMill CNC Service Plan available – Keep your equipment running at peak performance with Preventative Maintenance (PM), ISO 17025-certified Calibration Services for Universal Testing & Quality Control Equipment, and expert training. Contact your TensileMill representative to find the best plan for your needs.
Test Report:
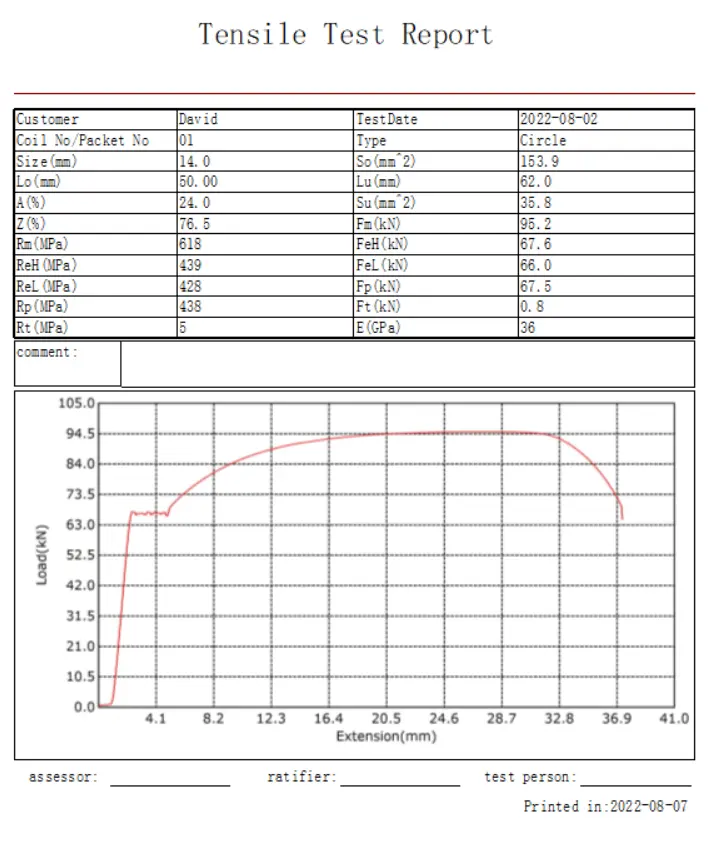
Video
Universal Testing Machine - Tensile Testing with Extensometer
Universal Testing Machine - Bending Test
GenTest: Next-Generation User-Friendly UTM Software
Why should I choose your UTM?
At TensileMill CNC, Inc., we know that testing large-scale or high-strength materials requires robust, accurate, and reliable equipment.
The Servo-Hydraulic UTM – 2000kN is engineered for heavy-duty applications such as structural steel, rebar, pipelines, and aerospace components. It combines high-capacity force delivery with precision measurement through a calibrated high-resolution load cell system.
This system offers automated control, advanced data acquisition software, and seamless integration with your lab’s workflow. Each unit includes custom fixturing, machine setup, and optional on-site training to ensure smooth deployment and immediate readiness.
To receive a personalized quote or explore custom configurations, contact us at 877-672-2622, email sales@tensilemillcnc.com, or submit your request online through our quote form.
What after-sales support is available for the UTM?
When investing in heavy-force testing equipment, comprehensive support is critical to long-term reliability and performance.
We provide full post-sales service, including installation assistance, calibration support, annual preventative maintenance, and access to our expert support team for technical troubleshooting.
For assistance, contact our support staff by phone at 877-672-2622 ext. 3, email support1@tensilemillcnc.com, or use our online ticket system for priority handling.
Our commitment to fast response times and expert guidance helps ensure your 2000kN UTM remains operational and accurate over the long term.
What is the lead-time for the 2000kN Servo-Hydraulic UTM?
The UTM is a high-capacity, custom-built system.
Typical lead-times range from 4 to 6 weeks, depending on the specific testing configuration, fixturing needs, and region of delivery.
TensileMill CNC coordinates every phase—from order confirmation and production to shipping and final setup—to make sure the installation timeline fits your testing goals.
Contact our sales team at 877-672-2622 or sales@tensilemillcnc.com to discuss your application and receive a detailed project timeline and quotation.
How easy is the UTM to operate, and is training provided?
Despite its power, the 2000kN Servo-Hydraulic UTM is designed for intuitive, safe operation.
Its user-friendly interface and fully automated software system allow technicians to conduct complex tests— including tensile, compression, bend, and shear—without manual calibration or control adjustments.
We offer in-depth training options—remote or on-site—depending on your team’s preferences. Training includes system operation, software usage, test standard configuration, and safety procedures.
For technical questions or support, reach out by phone at 877-672-2622 ext. 3 or email support1@tensilemillcnc.com.
Does the UTM comply with international standards?
Yes, our 2000kN Servo-Hydraulic UTM is designed to meet and exceed global testing standards including:
- ASTM E4, ASTM A370, ASTM E8, ISO 6892, ISO 7500-1
- EN, DIN, JIS, and other regional and industry-specific norms
Compliance is ensured through:
- Calibrated high-accuracy load cells
- Rigid machine frame for minimal deflection
- Repeatable fixturing and automation controls
Our software includes preloaded testing templates and exportable results for quality audits and regulatory traceability. Whether you’re running in-house quality control or third-party certifications, this machine delivers consistent, standards-aligned performance.
At TensileMill CNC, we facilitate certification services for both our own products and third-party devices, ensuring full compliance with NADCAP, ISO, ASTM, and other recognized industry standards.
What are the expected maintenance costs for the Testing Machine?
The 2000kN UTM is built with industrial-grade components to withstand high-force applications with minimal wear.
Routine maintenance is primarily limited to periodic inspection of hydraulic lines, actuator seals, software calibration, and control unit servicing.
We offer annual Preventative Maintenance (PM) Packages to reduce unplanned downtime, extend machine life, and maintain industry compliance.
To request a quote for service or maintenance planning, contact our support team at support1@tensilemillcnc.com or call 877-672-2622.
How do you minimize downtime for the Servo-Hydraulic UTM?
At TensileMill CNC, we prioritize uptime for high-capacity testing systems where production and compliance depend on consistent operation.
Should an issue arise, our expert support team provides rapid remote diagnostics and step-by-step solutions— often within 4 hours of your initial contact. For critical components or repair needs, we coordinate next-day shipping and, if required, on-site technician dispatch within 24–48 hours.
Support is available via:
- Phone: 877-672-2622 ext. 3
- Email: support1@tensilemillcnc.com
- Online ticket system for the fastest response
Our service infrastructure is built to keep your UTM productive and lab-ready with minimal disruptions.
What is included in the TensileMill CNC Service Plan?
The TensileMill CNC Service Plan is designed to maximize the longevity and performance of your equipment. It includes:
- Annual Preventative Maintenance (PM) Services to keep your CNC machines operating efficiently.
- ISO 17025-certified Calibration Services for Universal Testing Equipment, Hardness Testers, and Impact Testers to maintain accuracy.
- Training programs for both new and experienced operators to enhance proficiency.
How do I know which TensileMill CNC Service Plan is best for my needs?
Selecting the ideal service plan for your equipment depends on your specific usage and long-term goals. Our representative will work closely with you to assess your needs and recommend a comprehensive service plan. Whether you need annual maintenance, calibration services, or training programs, we'll ensure your TensileMill CNC equipment remains in optimal condition for years to come. Contact a TensileMill representative for a personalized consultation.
Why is ISO 17025-certified calibration important for my testing equipment?
ISO 17025-certified calibration ensures that your Universal Testing Equipment, Hardness Testers, and Impact Testers meet internationally recognized accuracy standards. This helps maintain reliable test results, ensures compliance with industry regulations, and reduces the risk of measurement errors. With the TensileMill CNC Service Plan, you receive professional calibration services to keep your equipment performing at peak precision. Contact us today to learn more.
People Also Searched For
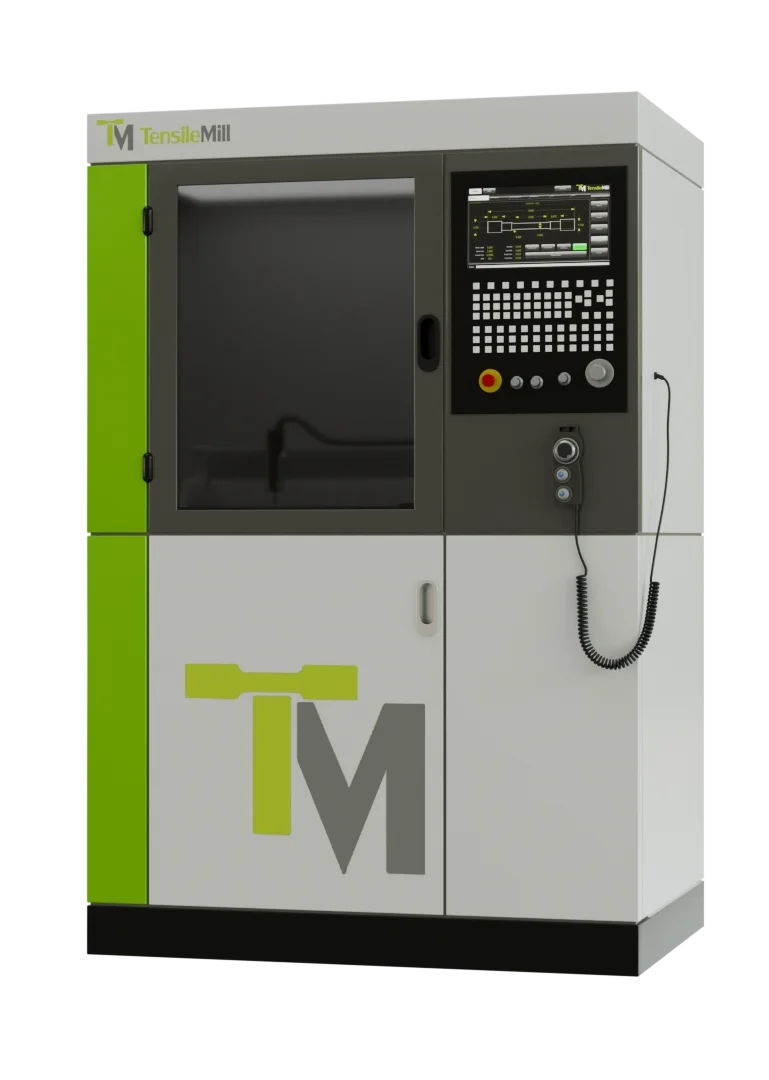
TensileMill CNC - Classic Upgrade
The TensileMill CNC - Classic Upgrade is the ultimate solution for precise and repeatable flat tensile and impact test specimen preparation. Engineered with TensileSoft™ technology and powered by a Fanuc controller, this machine offers an intuitive, user-friendly experience for both seasoned CNC operators and those with minimal training. Its compact footprint and turnkey design make it an ideal addition to any testing facility, ensuring maximum efficiency without compromising on accuracy. With a high-precision 3.2kW servo motor, the TensileMill CNC - Classic Upgrade ensures 0.0003” accuracy, handling specimens up to 14” long, 2” wide, and 0.5” thick. It meets ASTM, ISO, DIN, and JIS standards while efficiently preparing three 1.0” thick stacks at once with its triple clamping fixture. Compatible with an Impact/Pendulum notching machine, it also streamlines U & V-notch specimen preparation, making it a top choice for precise, high-speed testing.
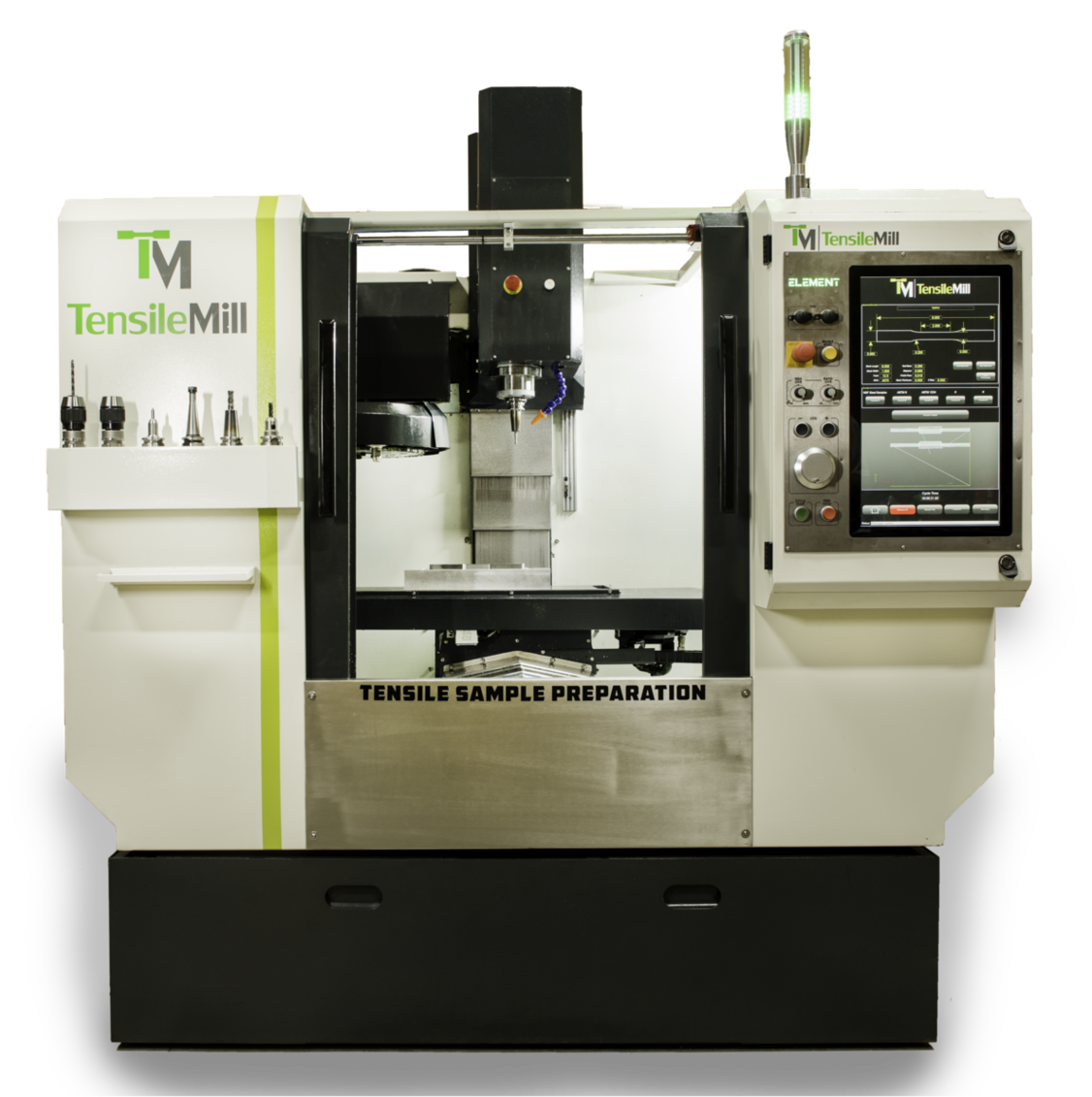
TensileMill CNC XL - Flat Specimen Preparation
The XL model is our larger tensile sample preparation machine that comes standard with an upgrade function of full CNC Carbon package for general purpose CNC requirements. TensileMill CNC XL is equipped with a state-of-the-art auto tool changer for the ultimate milling flexibility and time savings, allowing to prepare various types of tensile specimens and other parts. The advanced software allows to the operator reach milling results in seconds with a push of a few buttons. TensileMill CNC XL is an ideal user-friendly solution for medium to large size laboratories and manufacturing facilities.
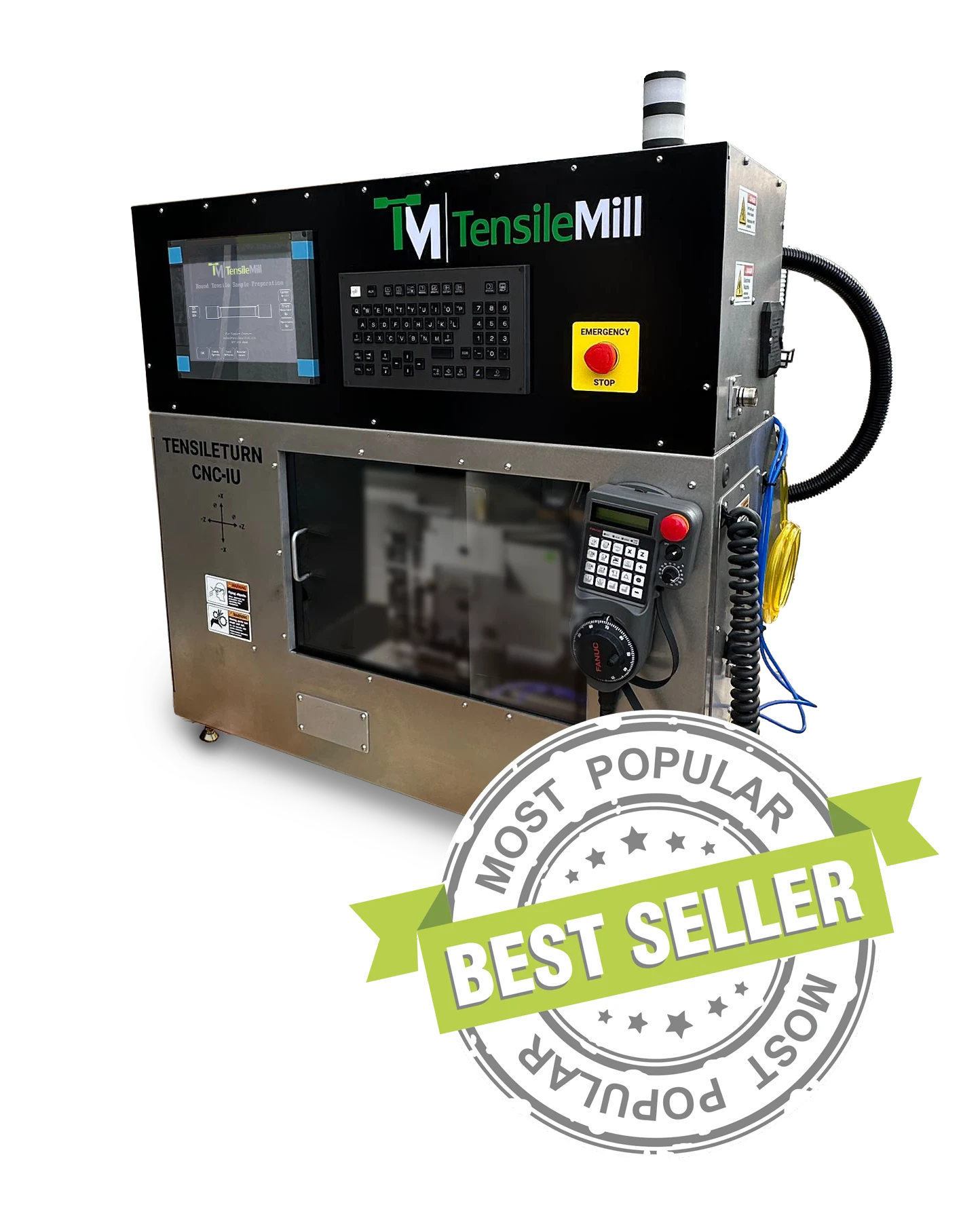
TensileTurn CNC - Industrial Upgrade - Round Tensile Sample Preparation Machine
The Industrial Upgrade model is a substantial step up from our Classic system. It offers the ability to accommodate larger starting blank sizes, tougher materials, irregular shapes, higher specimen preparation volumes, automatic center drilling and other unique functions required for the simplest and most accurate round tensile sample preparation. This system comes standard with a granite frame for added stability and the shock absorption for maximum sample preparation accuracy and longer system life-span. Though the Industrial Upgrade system is extraordinary for tensile specimen preparation needs, it is also capable of full range of CNC machining capabilities.
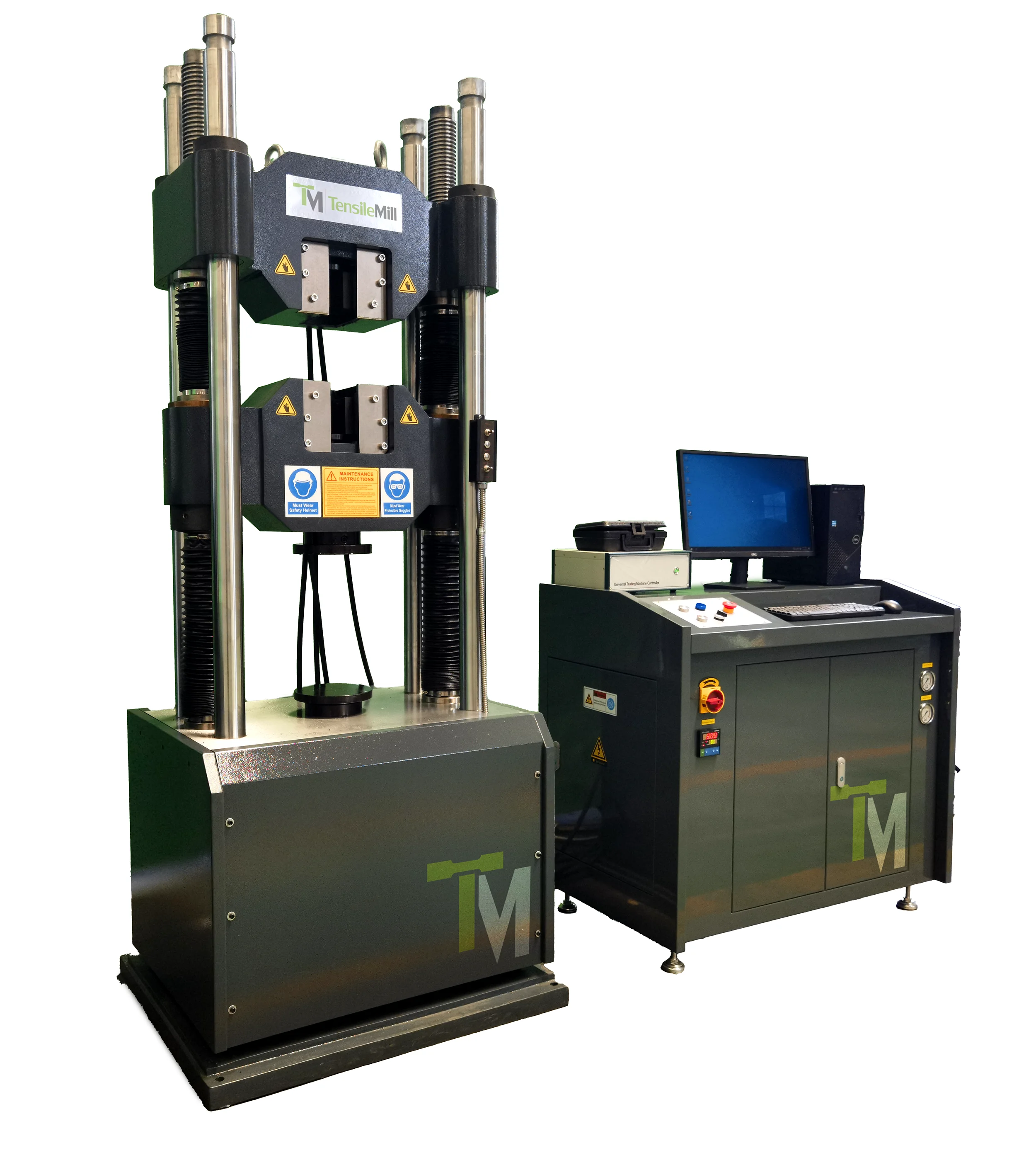
Tensile Testing Equipment
When selecting a tensile testing machine, there are a number of factors that must be considered. Whether you're upgrading in quality or functionality, or have the decision to move your materials testing in-house, you want to avoid buying a machine that doesn't meet the range of testing or materials for your needs. Of course you will be guided by the type of testing - tensile, compression, fatigue, etc. - and the ASTM or ISO standards for the market your product will enter. Other factors to consider when selecting the perfect tensile tester include…