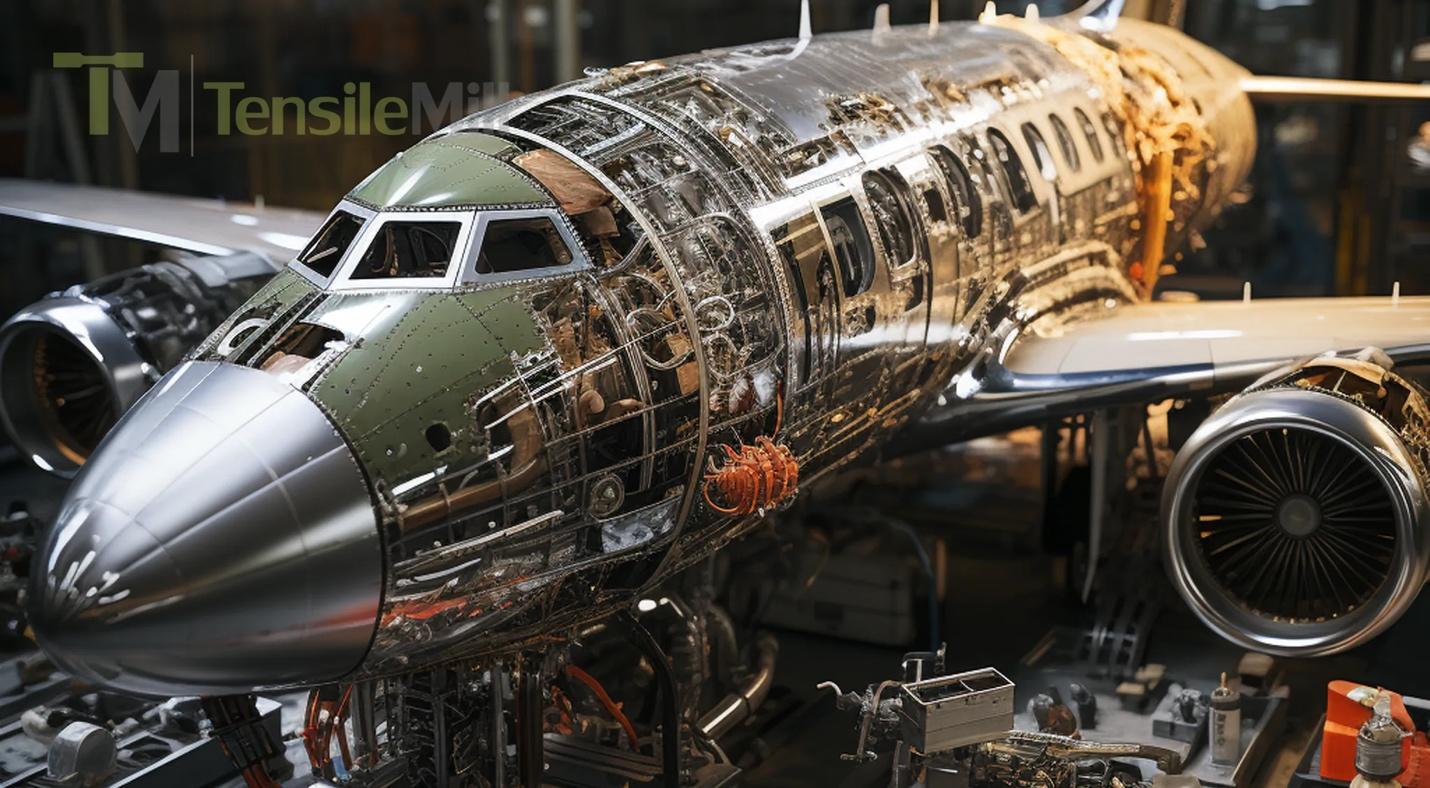
When choosing a product or service, we are guided by the desire to get high quality at the best price. The production of any parts must also be profitable and reliable, and when manufacturers need individual parts, they have to look for good partners with whom they can cooperate for a long time and receive high-quality parts. This also applies to the production of metal parts for the aerospace industry. Let's take a look at the specifics of this area - metal processing. What criteria should be considered when looking for partners for the production of metal parts and structures in the aerospace industry?
Metal Processing and Its Purpose In the Aerospace Industry
Metal fabrication includes many different technological operations, but they are all aimed at creating a given size, shape, structure and properties of metal products. Metalworking processes include bending, cutting, punching, drilling, stamping, casting, welding, and others.
Read more in our blog: 10 Ways that Metal Fabricators benefit the shipbuilding industry.
Metalworking has a wide range of applications. It is required for the production of various products and structures in many fields, including aerospace industry. This sector places high demands on the materials used in the construction of airplanes, rockets, satellites and other aerospace vehicles. Metal fabrication involves a variety of processes, including the following.
- Creation of parts and products with specified shapes and dimensions: manufacturing of sheet parts, pipes, profiles, shafts, housings and other shapes and complex parts.
- Changes in the structure and properties of a material to increase its strength and durability. That is, heat treatment – hardening, hardening and other methods that improve the hardness and strength of the metal.
- Improving the appearance, resistance to corrosion or wear – this requires the treatment of a metal surface. It may include painting, polishing, electroplating, and other methods. Additionally, the aerospace industry includes processes that improve chemical resistance.
- Connecting various structural components and producing complex structures and mechanisms. For this purpose, methods such as welding, bolting, soldering, riveting, and others are used.
- Achieving high precision is especially important in aerospace metal fabrication, where precision components are widely used and where the health and lives of many people depend on the accuracy of their manufacture and the reliability of structural materials.
- The development of new and improved alloys with new properties, reduced cost, and more simple processing.
The aerospace industry operates in extremely demanding conditions, where units and machines are exposed to extreme temperatures, aggressive environments and other factors that can lead to metal damage. Therefore, it is important to use special processing methods and protective coatings.
Additionally, the aerospace industry requires precision metal fabrication in production of complex shapes and components, such as turbines, wings, skins, and landing gear, etc. These processes usually require high accuracy and quality to ensure the safety and reliability of aircrafts.
In general, the process of metal fabrication in the aerospace industry is crucial for creating safe, durable and efficient flying machines. The high demands on metal structures, as well as the need for corrosion protection and the production of complex components, make metalworking critical to the success of the aerospace industry.
How the Aerospace Industry Said Goodbye to Steel Fabrication
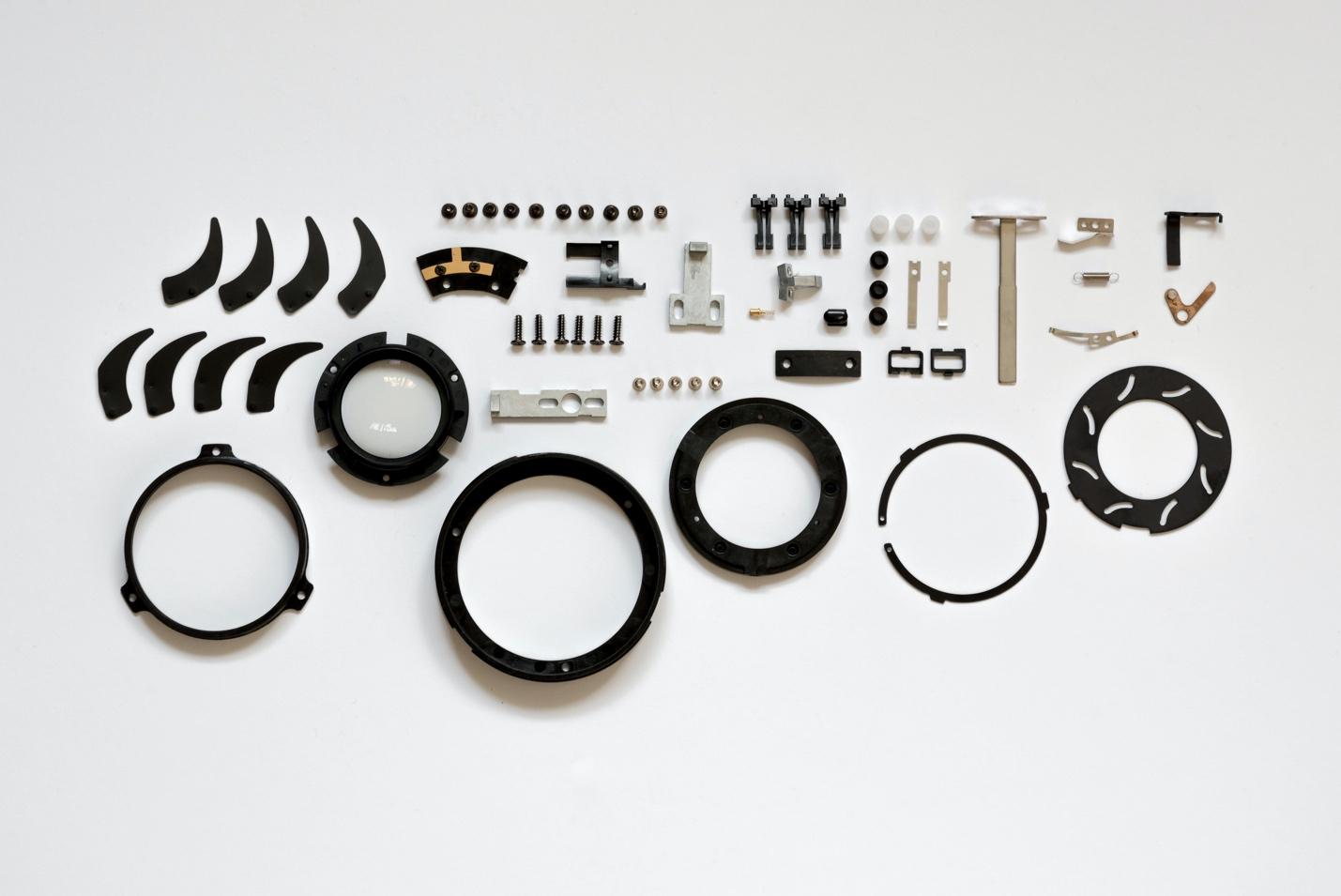
One of the most important aspects of metal fabrication for the aerospace industry is ensuring that structures are highly durable and lightweight. Airplanes and other aerial vehicles need to be very strong to withstand the heavy loads and stresses they face during flight. At the same time, weight is a critical factor, since each additional kilogram increases fuel consumption. That’s why, aircraft must also be lightweight.
Stainless steel was widely used in the early days of aircraft construction. However, during the 20s and 30s of the 20th century, steel was gradually replaced by aluminum alloys as the main structural material for aircraft. This was an important step in the development of aviation. The main reason for this replacement was the reduction in the cost of aluminum due to the establishment of its continuous production. The desire to reduce the weight of aircraft, improve their performance, and increase their range eventually led to the invention of certain aluminum-based alloys, which are still the most common structural material in aerospace metal fabrication today. Instead, steel fabrication remains the overall leader in metallurgy due to the low price of steel compared to aluminum alloys and its suitability for everyday use in other industrial sectors.
Aluminum alloys have a much lower density than steel, which makes products made from them much lighter. This reduces the weight of the aircraft and, consequently, its energy consumption and increase fuel efficiency. The lightness of aluminum alloys also helps to carry more loads and improve the machine maneuverability.
In addition, aluminum alloys are known for their high corrosion resistance. This is especially important in the aerospace industry, where aircraft are exposed to variable weather conditions and high levels of humidity. The use of aluminum alloys reduces the risk of corrosion and ensures long-term operation of aircraft.
Titanium alloys are also characterized by their low density, and they have even greater strength and corrosion resistance, but are much more expensive than aluminum-based alloys. This limits their use, but they are still applied in the aerospace industry in special cases, as well as for the construction of military aircraft.
Magnesium is a very light metal with high strength, but it is highly reactive and can burn in air. It is used as an additive to aluminum and titanium alloys.
The replacement of steel fabrication with aluminum alloys has also opened the way to new manufacturing and processing methods. Aluminum alloys are more suitable for forming complex geometric shapes, which allows for more efficient and optimized aircraft parts. Modern technologies have eliminated the problem of aluminum welding, which previously limited the use of this material, the manufacturing of aluminum structures and their repair. The most widespread aluminum alloys in the aircraft industry are 7075, 6061 and 7475-02, which possess superior resistance to damage and fatigue.
In general, aluminum alloys in aircraft construction has allowed the aerospace industry to develop significantly. As a result, according to the latest estimations, approximately 100,000 flights are operated daily in air around the world. This number includes all types of flights: passenger, cargo and military aircraft. Passenger flights alone account for more than 90,000 flights per day, transporting millions of passengers to destinations around the world. Traveling by air today is 2,200 times safer than traveling by car – it is also the result of the efforts of many specialists who care about the quality and reliability of every element of the aircraft's construction.
Manufacturing of Metal Structures In the Aerospace Industry
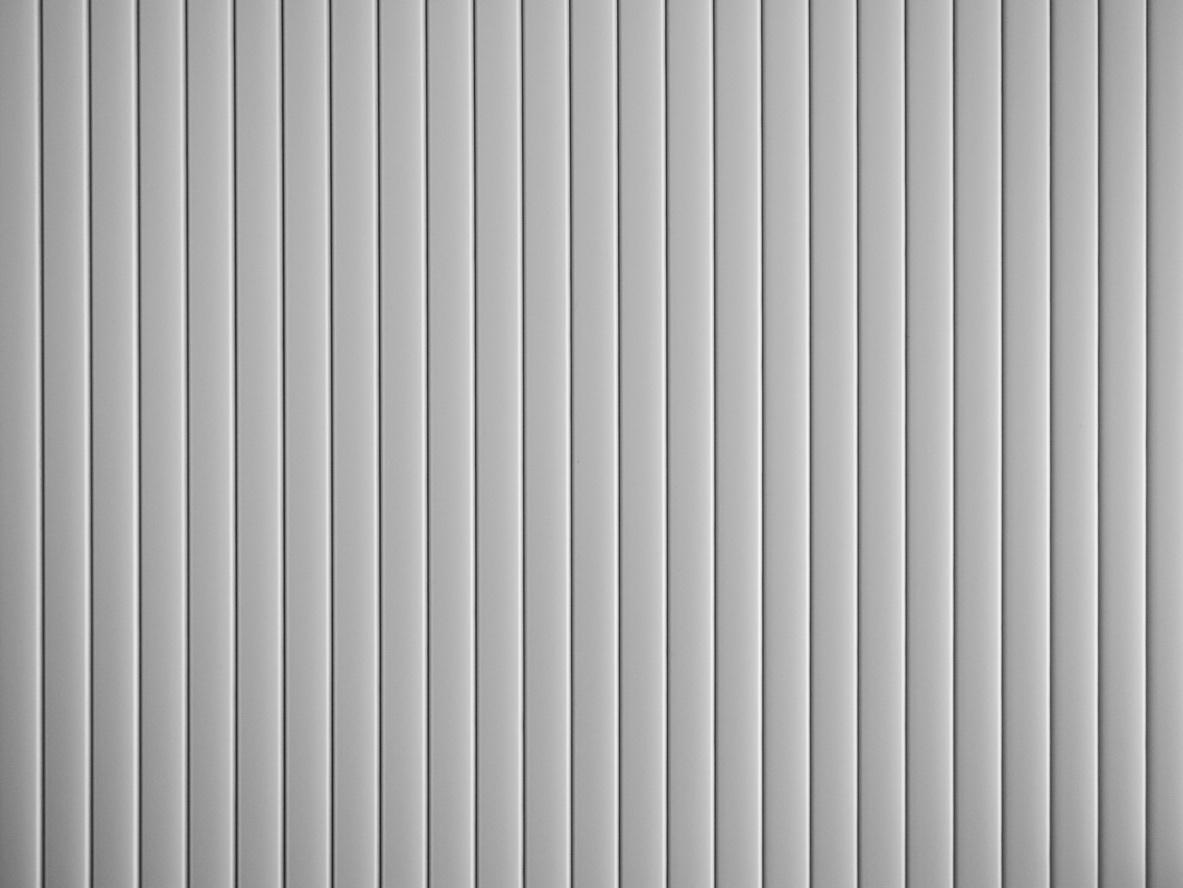
Aerospace components require precision metal fabrication that must meet stringent quality, reliability and safety standards. Metal fabrication processes – especially when performed by a first-class manufacturer – provide the complexity, repeatability, tight tolerances, and durability needed for using these products in exceptionally harsh environments.
The main structural elements of aircraft made from aluminum alloys:
- fuselage
- wings
- chassis
- floors
- door
- turbines
- exhaust pipes
- seat
- instruments
Along with aluminum, other metals: titanium, stainless steel, carbon steel, copper and brass, as well as special metals and alloys, are commonly used in aerospace steel construction to make components such as following.
- switches and relays
- wires and ropes
- Instruments and instrument housings
- oxygen generation and supercharging systems
- air conditioning
- coolers
- engine controls
- sensors
- actuaries
- antennas
- fuel systems
These are just some of the examples of the wide range of components that can be produced using precision metal fabrication processes.
Given the importance of precise execution of every detail in the aerospace industry, the reliability of partners is a critical factor in ensuring the quality and safety of the entire production process, and thus the safety of aircraft use.
Strict Quality Control In the Aerospace Industry
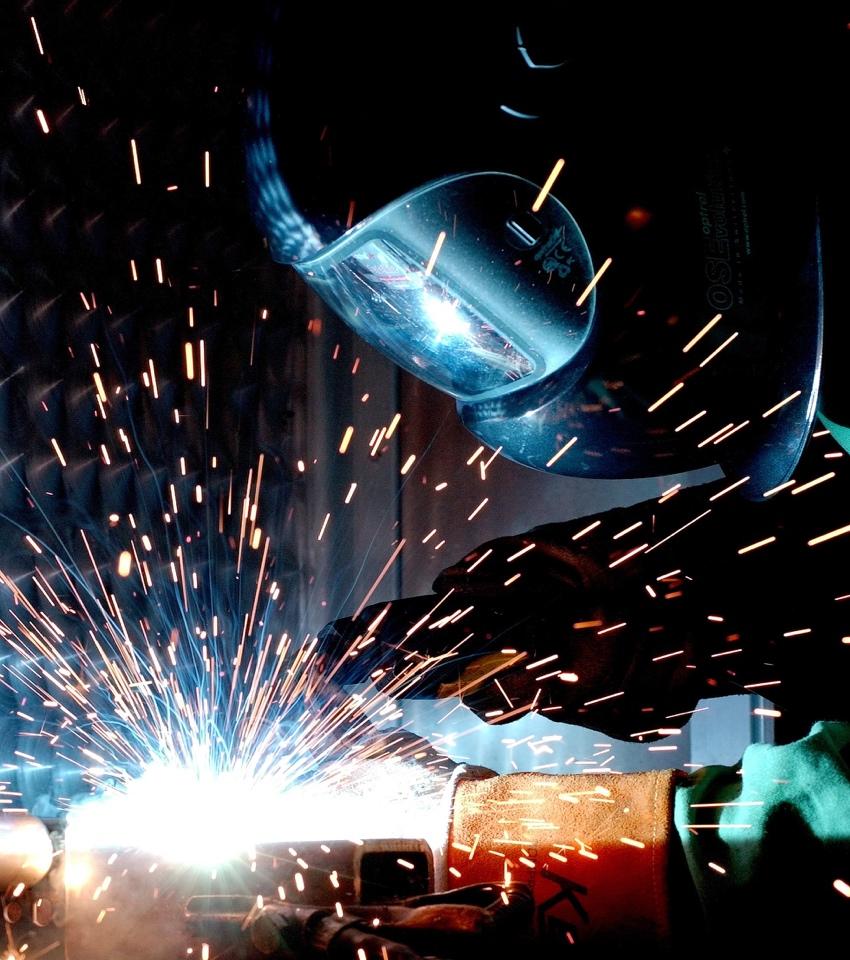
One of the main factors in aircraft safety is the strict regulatory requirements and standards set by the relevant international organizations, such as the Ministry of Civil Aviation (MoCA) and the Federal Aviation Administration (FAA) in the United States. The International Civil Aviation Organization (ICAO) is a specialized agency of the United Nations that works in civil aviation at the international level.
The quality control process begins with the supply of high-quality materials and components for the production of aerospace systems. Manufacturers must comply with international regulations, such as ISO (International Organization for Standardization) and AS (Aerospace Standard) standards.
One of the key steps in quality control is to check materials for compliance with requirements. This may include physical, chemical, and mechanical tests to identify defects, inconsistencies, or contamination. For example, parts may be subjected to tests for strength, hardness, tensile strength, and other mechanical characteristics. They are also examined using X-ray analysis, ultrasound, and other methods.
The next step is quality control at various stages of production. This includes checking the accuracy of machining, measuring geometric parameters, and identifying deviations from design specifications. Special equipment, such as coordinate measuring machines, is used to ensure high measurement accuracy.
The manufactured components are then subjected to endurance tests, stress tests and simulations of various operating conditions. For example, the performance of aircraft engines is assessed after many hours of operation at high temperatures and loads.
The final stage of quality control involves testing aircraft before they are released for operation. This includes testing of stability, maneuverability and safety in various flight modes.
Another important role is played by flight safety and regular inspections of aircraft that have already been authorized for use. Before each flight, the aircraft is thoroughly inspected and maintained to ensure its reliability and airworthiness.
All of these quality control processes in the aerospace industry are designed to ensure high reliability and safety of aircraft.
The value of Tensile Testing for Quality Control
In the aerospace industry, tensile testing is one of the key tests of mechanical properties of materials. These tests allow you to determine the mechanical properties of materials, such as strength, ductility, and toughness, which affect the material's behavior under load. But there are other tests that are also important for ensuring the safety and quality of structures. These include compression, bending, impact, and wear tests.
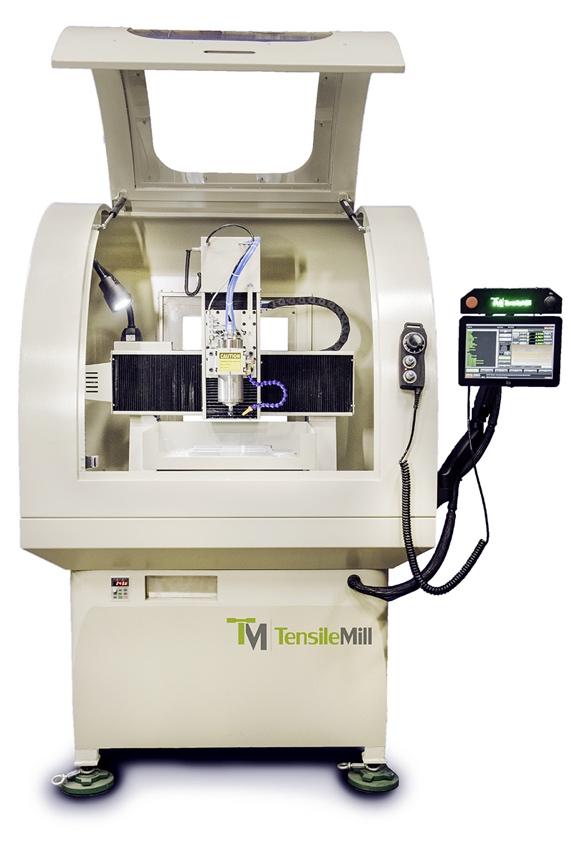
TensileMill CNC Specimen Preparation Machine
Each of these tests has its own significance in determining the mechanical properties of materials and controlling the quality of structures in the aerospace industry. They complement each other, providing a comprehensive assessment of a material's ability to withstand various types of loads and ensure safety and reliability.
Tensile tests are performed on tensile machines. The procedure involves loading a metal sample, usually in the form of an elongated flat or round billet with flared ends, along an axis with a certain force until the sample breaks. During the test, the load and strain values are measured, which allows you to determine the mechanical properties of the material. The results of a tensile test provide important information such as tensile strength, yield strength, relative elongation, and elastic modulus. These parameters indicate the strength of the material, its ability to withstand loads, and its ability to ductility and tensile deformation.
In the aerospace industry, tensile tests are performed on samples of materials used in the manufacture of aircraft structures. These can be lightweight aluminum or titanium alloys, or even composite materials. The tests help to determine whether the material meets the strength and safety requirements for specific applications in airplanes, spacecraft, and other aircraft.
Mechanical property tests, in particular tensile tests, are an important step in the quality control of materials in the aerospace industry. They help ensure high reliability and safety of aircraft by evaluating the mechanical properties of materials before they are used in structures.
TensileMill CNC Inc. provides the North American market with reliable tensile testing equipment. It meets the most current industry standards and is designed to meet customer needs for ease of use and accurate results. The tensile testing equipment operates in a wide range of forces, from 1 to 3000 kN. We draw on our customers' extensive experience in the development of this equipment and provide a full range of consulting and technical support to ensure the smooth progress of your aerospace projects.
To ensure accurate results, we recommend that you use tensile test equipment in conjunction with tensile test equipment from TensileMill CNC Inc. We offer two lines of such devices:
We guarantee the accurate reproduction of the tensile specimen geometry, which is a key to obtaining accurate results and thus understanding the mechanical properties of your products.
The company's representatives are always happy to hear from you and are ready to answer all your questions about this equipment.
Finding a Partner For the Manufacture of Metal Products
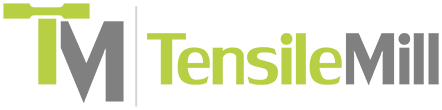
With projects as complex as airplanes or spacecraft, it is impossible to concentrate all production facilities at one enterprise and manufacture products in its own closed cycle: from the screw to the engine, fuselage, and navigation equipment. Therefore, finding partner companies that can perform precision metal fabrication to order becomes crucial to ensure high quality products.
Regardless of the specific part you want to introduce into production, it is important to choose a metal manufacturer that meets the following criteria.
- Pay attention to the partner's experience and reputation.
- Review previous projects and orders to assess their experience in manufacturing metal products for the aerospace industry.
- Conduct a detailed research of the partner's reputation, including reviews, recommendations, and feedback from other clients.
- Demand transparency and accountability.
- Ensure that the partner is willing to provide transparency in the production process, including constant communication about the status of the project and the progress of the work.
- Ask for regular reports and updates on production that demonstrate progress and schedule.
- Arrange for immediate notification in case of changes in delivery times due to force majeure.
- Providing design and engineering support.
- Ensure that the partner can provide advice and guidance on metal product design and engineering.
- It is important to be able to communicate with the partner's specialists to resolve any issues and production challenges.
- Quality control and certification.
- Require certificates confirming that products meet aerospace requirements.
- Learn about the quality control process and what standards they adhere to.
- Does the company have on-site testing capabilities and certified equipment?
- Make sure that the partner has its own quality assurance department that controls various stages of production.
- Logistics capabilities.
- Assess whether the partner has the resources to deliver products and materials efficiently.
- Find out how the partner manages logistics and whether the company can ensure on-time delivery and safety.
Visit the partner's company, if possible. Evaluate your own impression from meeting with the company's management, employees, and possibly customers. Look at the production environment, technology, and overall approach to production. This will help you to take into account additional factors when choosing a partner that cannot be predicted, as they may be at the level of intuition.
All of these criteria should be considered when choosing a partner for the production of metal products in the aerospace industry. Thorough research and cooperation with the best partner will help ensure the successful implementation of your projects.
TensileMill CNC Inc. is a reliable supplier of tensile testing equipment for companies in the metalworking and aerospace industries. You can always count on us for this aspect of product quality control!