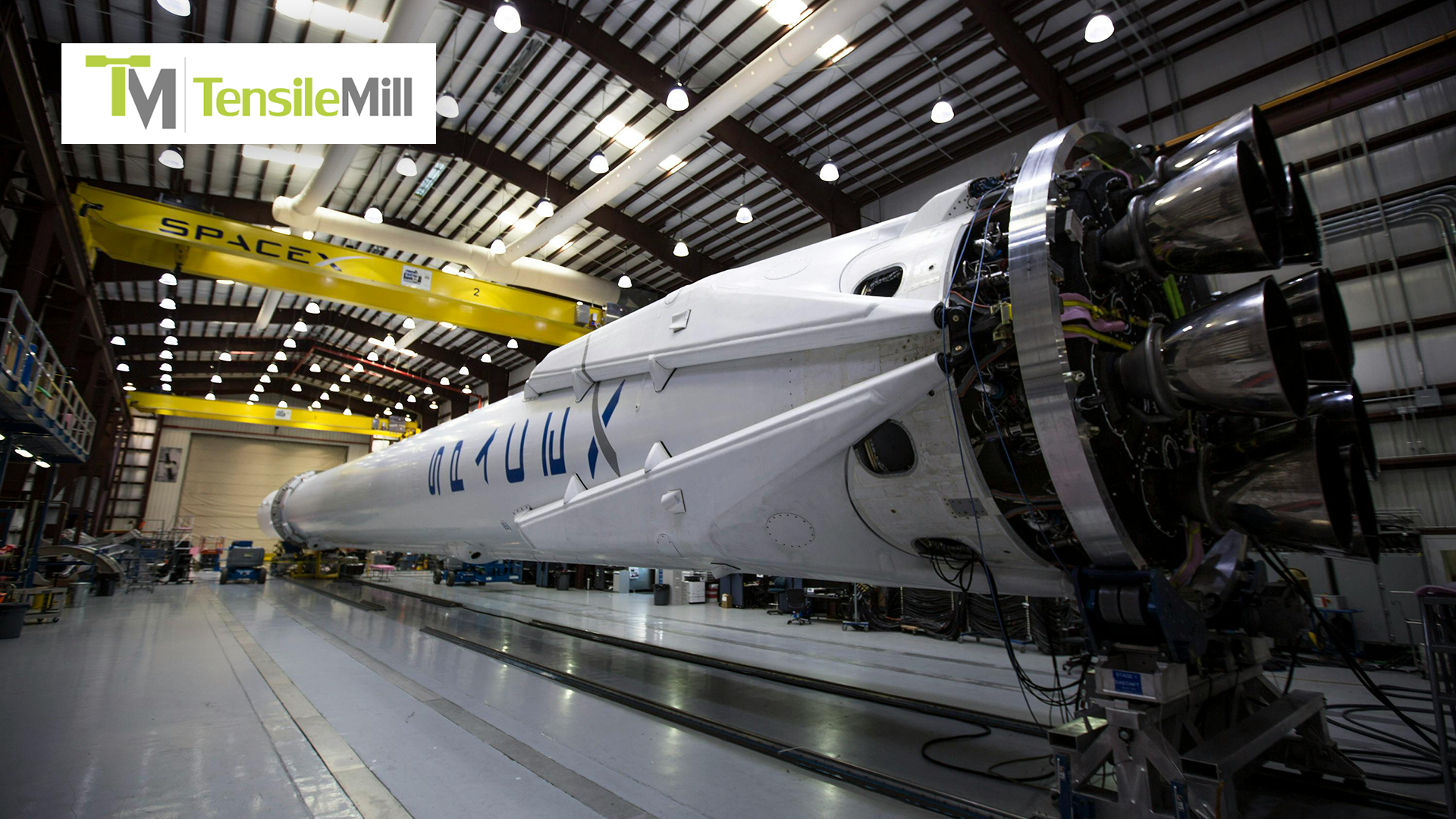
There is a great deal of stress placed on every component of a spacecraft during space travel. From the violent forces of launch to the vacuum of space and the intense heat of reentry, materials must withstand conditions far beyond what we experience on Earth. Failure may result in catastrophic consequences.
To maintain safety, aerospace engineers use tensile testing. This is a process that measures how much force a material can handle before deforming or breaking. As an integral part of the verification of the integrity of spacecraft, such testing is more than simply theoretical.
From NASA’s Artemis program to SpaceX’s Starship, tensile testing is a key component of designing, manufacturing, and validating spacecraft. Without it, there would be no way to guarantee that materials and structures could survive spaceflight conditions.
Why Spacecraft Face Extreme Structural Challenges
Spacecraft must endure some of the harshest physical conditions imaginable. Each phase of its mission—launch, orbit, and reentry—imposes unique stresses that demand maximum structural integrity. Below is a description of each of them:
Launch: Extreme Acceleration and Vibration
During liftoff, a spacecraft experiences intense G-forces, sometimes exceeding 3 to 5 times Earth's gravity. Every component must withstand this sudden acceleration while being exposed to violent vibrations and acoustic shockwaves from rocket engines. The Saturn V rocket that launched the Apollo missions, for example, produced over 220 decibels of sound pressure, creating vibrations that could shake apart weakly secured components.
The Space Shuttle program also highlighted launch stress risks. In STS-51-L (Challenger), an O-ring seal in the booster joint failed due to cold-induced brittleness, leading to vehicle loss. This disaster proved the need for tensile testing at operational temperature extremes to make sure all materials remain flexible and strong under real conditions.
Orbit: Continuous Stress and Temperature Extremes
Once in space, a spacecraft is exposed to constant mechanical stress from internal pressure differentials. The International Space Station (ISS), for example, is pressurized to 14.7 psi inside, while the vacuum outside exerts zero pressure. Without structural reinforcement, its aluminum alloy walls would rupture outward.
Another major challenge is thermal cycling. Spacecraft in low Earth orbit (LEO) move from sunlight to darkness every 90 minutes, facing temperature swings between -150°C and +120°C. These extreme shifts cause metals and composites to expand and contract repeatedly, leading to fatigue cracks.
Reentry: Aerodynamic Forces and Intense Heat
When a spacecraft returns to Earth, it slams into the atmosphere at speeds over 27,000 km/h. This generates intense aerodynamic pressure and temperatures exceeding 1,600°C—enough to melt most metals.
A tragic example of structural failure during reentry was Space Shuttle Columbia (2003). A damaged carbon panel on the left wing allowed superheated plasma to enter, causing the orbiter to break apart. Had these panels been impact-tested under simulated conditions, engineers might have detected the weakness before flight.
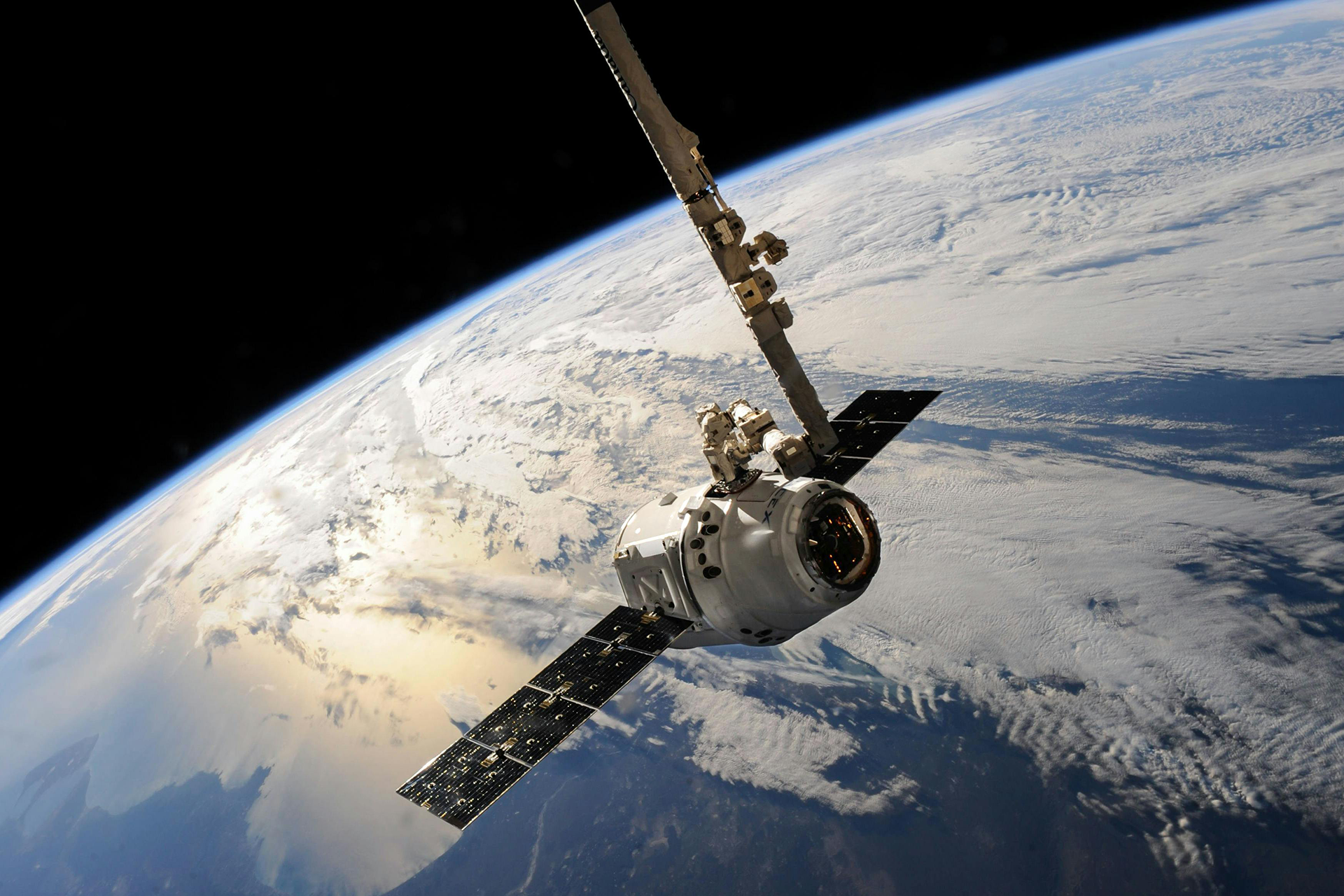
How Tensile Testing is Used in Modern Spacecraft Engineering
As previously mentioned, tension testing is a key component of aerospace engineering as it provides crucial information about material behavior under stress. By applying a uniaxial force to a material specimen, engineers can assess a number of properties, including:
- Yield Strength: The stress at which a material deforms plastically.
- Ultimate Tensile Strength: The maximum stress a material can withstand before breaking.
- Elongation: The extent to which a material stretches before failure.
Tensile Testing Procedures
The test of tensile strength process in aerospace applications typically involves:
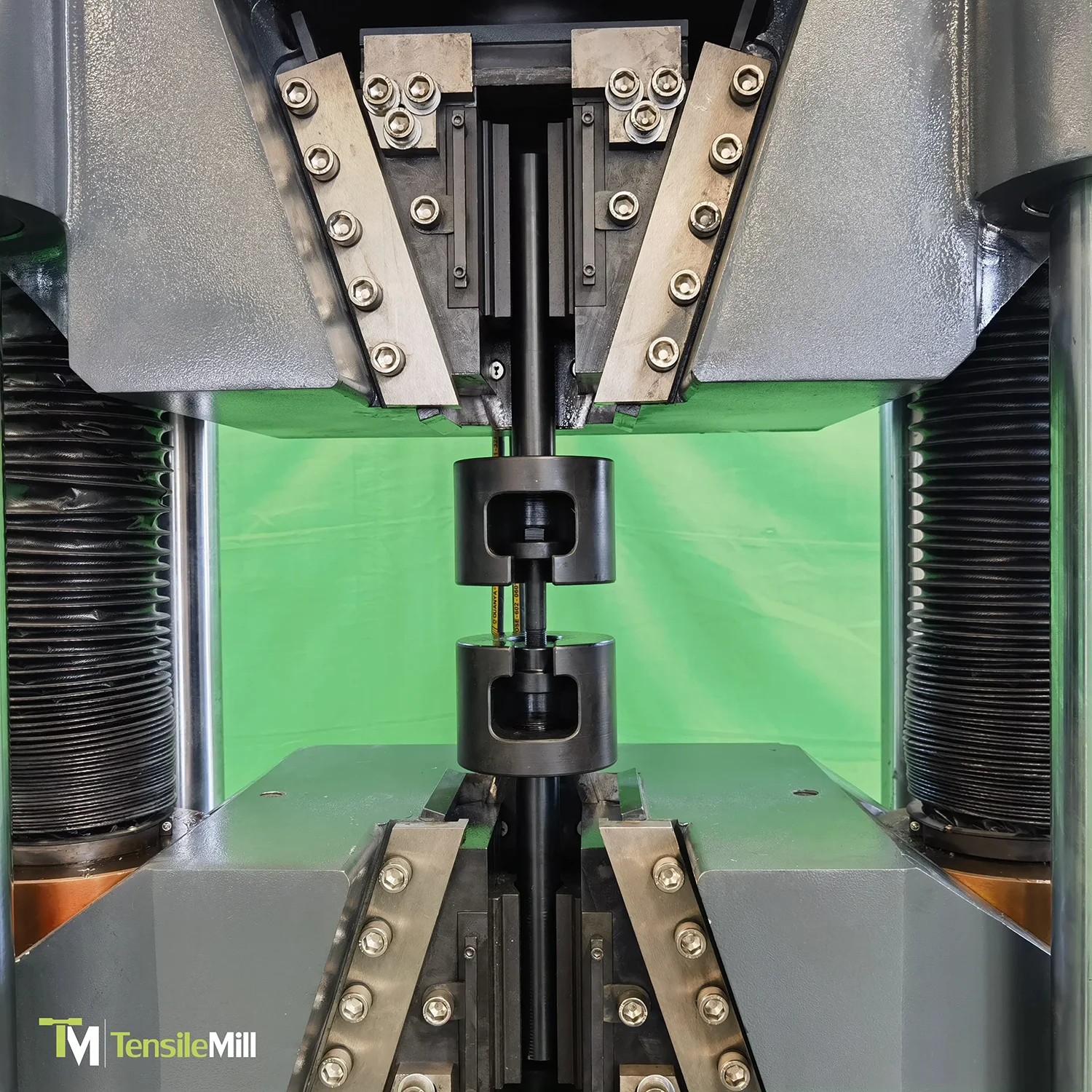
- Specimen Preparation: Creating standardized samples from materials intended for spacecraft components.
- Mounting: Secure the specimen to a tensile testing machine equipped with precise grips to prevent slippage.
- Loading: Applying a controlled, uniaxial tensile force to the specimen at a constant rate.
- Data Collection: Measuring material response, including stress-strain behavior, to determine mechanical properties.
Why is Tensile Testing Critical for Spacecraft Structural Integrity?
In detail, tensile strength testing of spacecraft components is a must for a number of reasons. To better understand its significance, here are 5 key reasons why tension testing is indispensable in spacecraft engineering:
1. Verifying Material Strength in Extreme Conditions
Spacecraft components experience unprecedented mechanical stress, whether from launch acceleration, orbital pressure changes, or reentry heat. Tensile testing proves that every construction material has been physically validated to survive these harsh conditions.
- Rocket and spacecraft fuselages are subjected to millions of pounds of force. Testing guarantees that the metals, composites, and welds remain intact under stress.
- Fuel tanks and pressure vessels must withstand intense internal pressure. If a tank or module ruptures due to weak materials, the consequences could be catastrophic.
- Space station and habitat modules must handle long-term exposure to radiation and thermal expansion cycles without cracking or losing strength.
2. Preventing Structural Failures Before Launch
A spacecraft failure in orbit or during reentry leaves no room for repairs. Testing for tensile strength prevents such failures by identifying material weaknesses long before a spacecraft leaves the ground.
- Microcracks in metal parts can grow under repeated stress cycles, leading to sudden failure. Tensile testing detects these weaknesses before manufacturing.
- Fasteners, bolts, and welds must be strong enough to withstand vibration and shock loads. Poorly tested joints could lead to detached panels or collapsed structures in space.
- Heat shield components and reentry structures are tested at both high temperatures and high mechanical stress to prevent Columbia-type disasters.
3. Assuring Safety Margins and Redundancy
No material should ever operate at its absolute limits in space. Tensile testing confirms that every spacecraft component has a built-in safety margin—meaning it can withstand far greater forces than expected.
- NASA enforces a 1.4× to 2.0× safety factor on all critical spacecraft structures. If a module is designed for 10,000 psi stress, it must be tested to survive at least 14,000–20,000 psi before approval.
- SpaceX’s Starship fuel tanks are tested at 40% beyond operational pressure to confirm their structural integrity even under worst-case conditions.
- The International Space Station’s aluminum pressure modules were tested at 1.5× their operating load to verify long-term safety in orbit.
4. Improving Manufacturing and Material Selection
Not all materials perform equally well in space. Tensile testing allows engineers to compare different metals, composites, and alloys, selecting the best materials based on actual performance data rather than theoretical estimates.
- Titanium vs. Aluminum: Titanium has higher strength but is heavier. Testing for tensile strength optimizes the balance between weight and durability.
- Carbon Fiber Composites: These are lighter than metals but prone to delamination under stress. Testing determines if they can handle repeated stress cycles without failure.
- Welding and Fastener Quality Control: Even the strongest material is useless if welded or bolted improperly. The tensile test evaluates joint strength to prevent separation or fatigue failure.
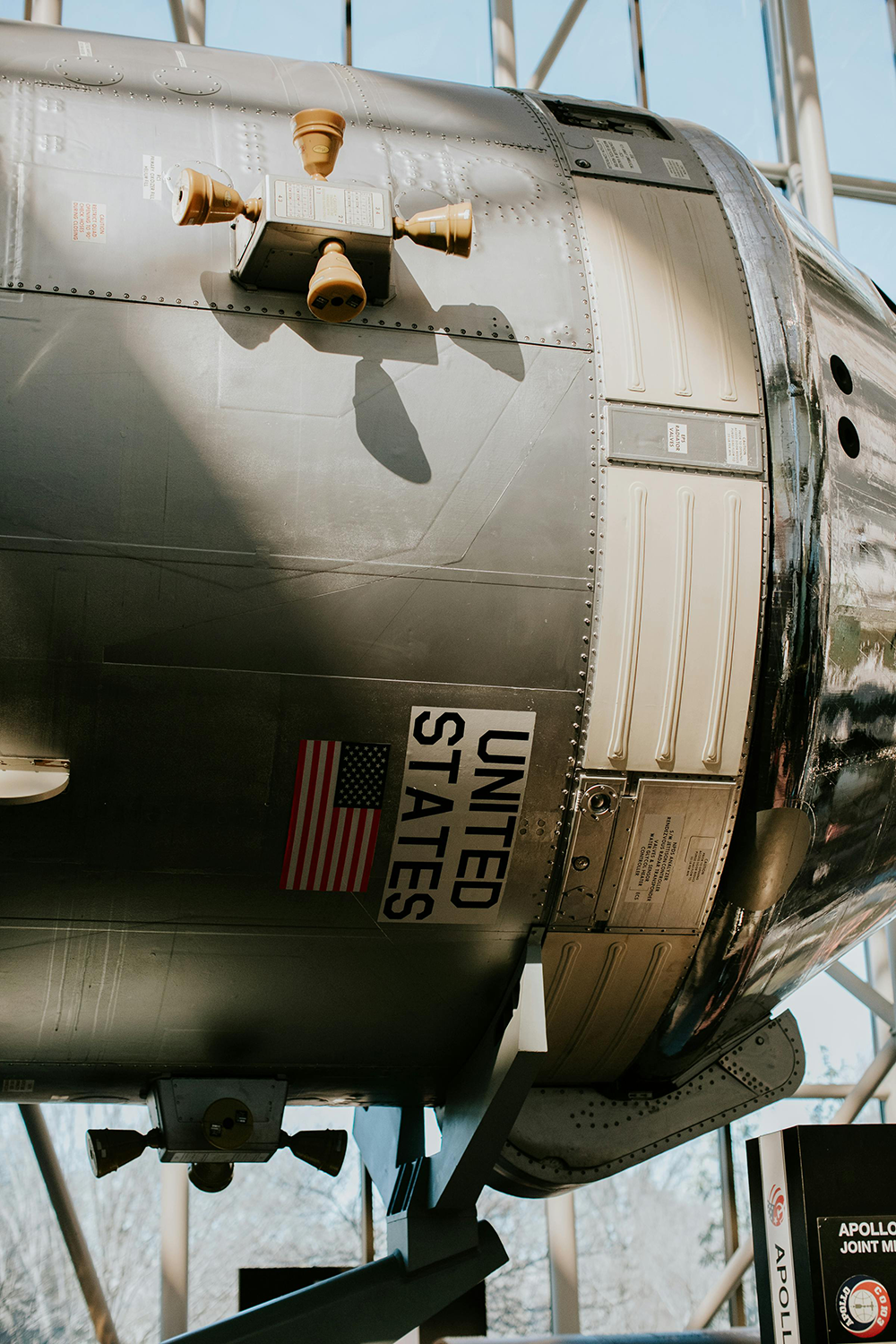
5. Adapting to Future Space Exploration Challenges
Demand for lighter, stronger, and more heat-resistant materials is growing as missions expand to deep space exploration, Moon bases, and Mars habitats. Tensile testing will be even more crucial in the coming decades for:
- Lunar structures: Materials will need to resist lunar dust abrasion, extreme temperature swings, and micrometeorite impacts.
- Mars habitats: Long-term exposure to the Martian atmosphere (CO₂-rich, low pressure) and surface radiation will require completely new materials.
- Reusable spacecraft: Starships and other vehicles built for multiple missions must withstand repeated stress cycles without failure.
Real-World Applications of Tensile Testing in Spacecraft
The following examples showcase how NASA, SpaceX, and other aerospace companies have used tensile and structural testing on Earth to improve spacecraft design and prevent failures during actual missions. Taking a closer look at them will be helpful.
NASA’s Artemis Program: Stress Testing the Space Launch System (SLS)
NASA’s Space Launch System (SLS), the most powerful rocket ever built, underwent extreme structural testing before its first flight. In 2019, NASA engineers subjected a full-scale liquid hydrogen fuel tank to tensile stress beyond its expected flight conditions. The test tank was loaded to 260% of its maximum predicted flight load, applying millions of pounds of force. After hours of increasing pressure, the tank finally ruptured—exactly as expected. This test validated the SLS structure's strength, verifying that it could withstand launch forces with a significant safety margin.
SpaceX Starship: Testing Stainless Steel Tank Durability
SpaceX uses stainless steel (301/304L) for its Starship rocket due to its ability to handle extreme temperatures and stress. During development, SpaceX engineers conducted a series of burst pressure tests to determine the failure limits of the fuel tanks. Early prototypes were pressurized with liquid nitrogen, pushing the tanks to 8.5 bar (125 psi)—about 40% higher than the required operational pressure. Some tanks failed, providing valuable data to refine welding techniques and material thickness for later versions.
International Space Station (ISS) Module Proof Testing
The ISS modules that house astronauts in orbit were all tested under 1.5× their normal operational pressure before launch. This proof testing confirmed that aluminum pressure vessels could endure decades of internal pressurization without failure. If any material weakness was present—such as microcracks in weld seams—tensile testing would have revealed it before the module left Earth.
Sierra Space’s Inflatable Space Habitat: Extreme Pressure Testing
For future space habitats, the testing of tensile strength goes beyond metals. The LIFE module, an inflatable space station habitat developed by Sierra Space, was subjected to burst pressure tests in 2024. The goal was to reach at least 4× the normal operating pressure (60 psi), but the module exceeded expectations, holding up to 77 psi before rupturing. This result confirmed that inflatable spacecraft can withstand extreme conditions, thereby providing an alternative to rigid spacecraft.
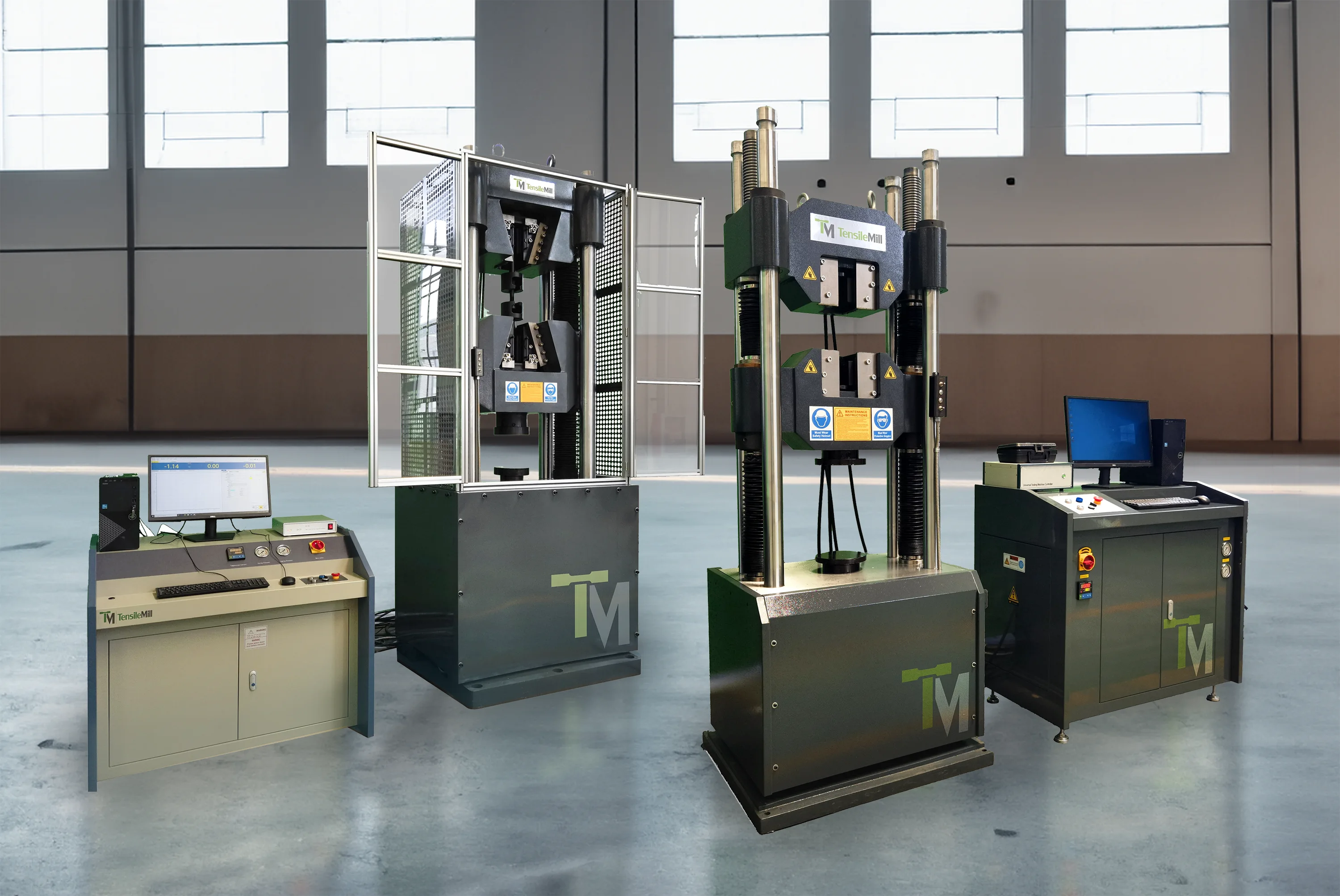
Equipment Required for Tensile Testing in Spacecraft Engineering
A tensile test provides reliable material data only if it is conducted in a precise manner. In order to obtain accurate results, proper specimen preparation, high-performance testing machines, and specialized tools are required.
Before testing, raw materials must be shaped into standardized tensile specimens. This is done using tensile specimen preparation systems, commonly CNC machines, which cut and machine materials into precise geometries, such as dog-bone-shaped specimens, to guarantee consistency across tests. Surface finish is key to resulting accuracy, as machining imperfections introduce stress concentrations. To prevent this, polisher systems for tensile specimens refine the surface, removing irregularities and allowing failure analysis based solely on material properties.
Once specimens are prepared, they are tested using Universal Testing Machines (UTMs), which apply controlled tensile loads while measuring parameters like yield strength, ultimate tensile strength, and elongation. Aerospace-grade UTMs integrate digital strain gauges, precision load cells, and high-resolution extensometers, allowing reliable measurements of material performance under stress.
For spacecraft applications, testing conditions must replicate real operational environments. This often requires cryogenic chambers, high-temperature fixtures, and vacuum-compatible grips, which simulate extreme space conditions such as thermal fluctuations and pressure differentials. Material performance data would be incomplete without these specialized systems, potentially compromising the reliability of spacecraft.
TensilePolish GR04 – Advanced Longitudinal Polishing System for Reliable Tensile Tests
As mentioned above, polishing is an integral part of the preparation of tensile specimens, guaranteeing uniform surface quality and minimizing residual stress that may affect the results of the test. At TensileMill CNC, we specialize in high-precision tensile testing equipment, and a key part of this process is accurate and repeatable specimen polishing. Hence, we offer the TensilePolish GR04 – an Automatic Longitudinal Polishing System designed to enhance tensile test reliability in a broad range of industries.

The TensilePolish GR04 is engineered to polish both cylindrical and flat specimens, complying with industry standards such as ASTM E466, ASTM E606, EN 6072, and NADCAP. It automates the longitudinal polishing process, leading to consistent results by eliminating repeated contact between the specimen and the same section of sandpaper. This prevents localized wear and maintains a uniform finish, which is crucial for accurate tension testing outcomes.
With adjustable polishing parameters, including rotation speed, applied force (5–50 N), and active polishing length (5–280 mm), the system accommodates different specimen geometries. It also features an automated sandpaper switching mechanism, allowing smooth transitions between four different grit levels during the polishing cycle.
For laboratories handling a wide range of specimen sizes, the TensilePolish GR04 is available in multiple configurations, including models for standard, small, and large cylindrical specimens, as well as flat specimens. Additionally, customized solutions are available to meet specific application needs.
Featuring a touchscreen interface, precise controls, and an automated workflow, the TensilePolish GR04 simplifies specimen preparation, thus proving to be an invaluable tool for laboratories performing high-accuracy tensile tests.
Overview of the Automatic Longitudinal Polisher System
Achieving Spacecraft Reliability Through Tensile Testing
The tensile test has become an integral part of aerospace engineering, providing assurance that every spacecraft component is strong enough to withstand extreme space travel conditions. From launch vibrations and orbital stress to reentry heat, spacecraft materials must perform flawlessly under immense pressure. Without rigorous testing, even minor weaknesses could lead to catastrophic failures, endangering missions and crew safety.
By verifying material strength, preventing failures before launch, maintaining safety margins, and guiding material selection, tension testing remains a necessity for modern and future space exploration. As technology advances and missions extend beyond Earth's orbit, the demand for high-precision testing methods and equipment will only increase.
If you are looking for tensile testing equipment to meet your specific requirements, explore our range of universal testing machines, specimen preparation systems, and polishing tools. We would be happy to answer any questions you may have via an online quote or by direct contact. We are here to help you find the right testing solution for your requirements.