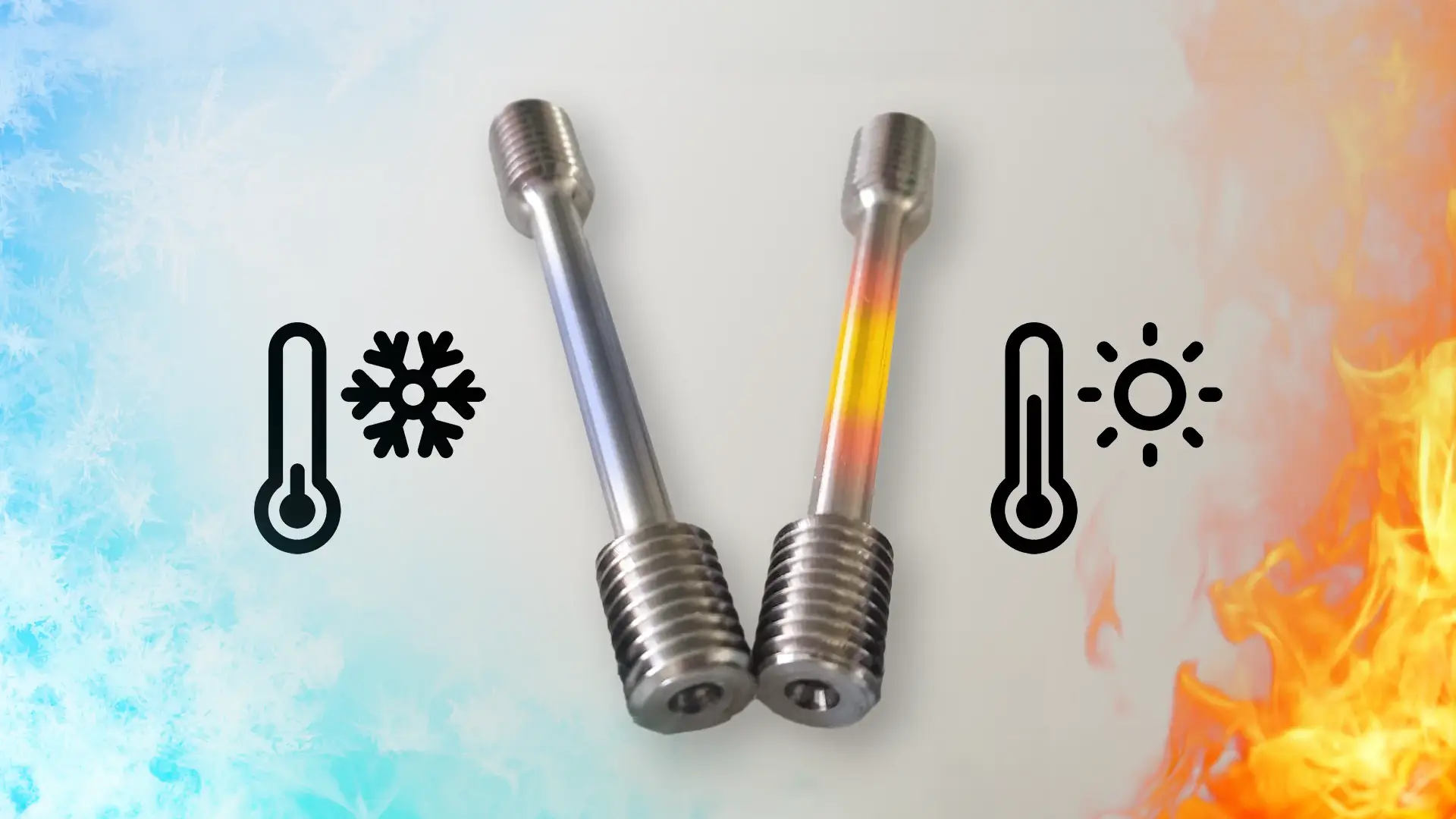
The temperature of specimens affects tensile testing results by altering their mechanical properties, such as tensile strength and ductility. Higher temperatures typically decrease tensile strength and increase ductility due to increased atomic mobility and weaker intermolecular bonds. Conversely, lower temperatures increase tensile strength but cause brittleness.
However, the topic of temperature effects on tensile testing results is much more complex than it might seem. The temperature during testing can also influence other parameters such as strain rate, microstructural changes, and phase transformations. Together, these measurements contribute to a comprehensive understanding of tensile testing outcomes.
The purpose of this blog is to analyze how the temperature of tensile specimens affects their testing. We will also discuss why it is necessary to test specimens at different temperatures and where products made from these tested materials are used. This detailed exploration will show how important temperature is in determining material performance.
Why Specimens Are Tested at Different Temperatures
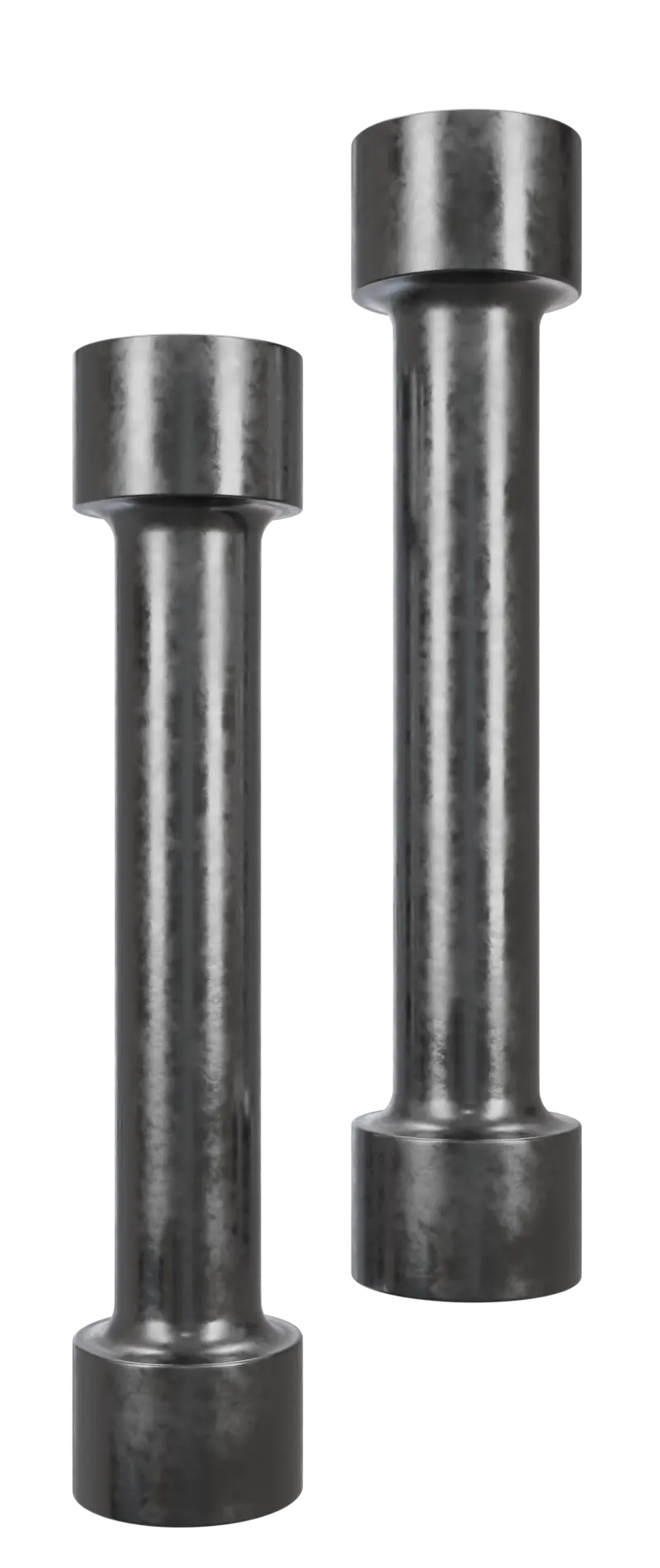
Understanding how temperature influences tensile testing results is key to predicting material performance under real-world conditions. Materials often experience an array of temperatures in practical applications. For example, aerospace components must endure extreme temperatures from high-speed flight or re-entry into the Earth's atmosphere. Testing at different temperatures confirms that materials will perform reliably under these diverse conditions.
Temperature variations can cause significant microstructural changes in materials. Elevated temperatures may lead to grain growth or phase transformations, altering mechanical properties. Testing helps scientists understand these changes and predict material behavior in service. Additionally, the rate at which a material is strained may also be temperature-dependent. High temperatures accelerate deformation processes, while low temperatures slow them down. Accurate testing at different temperatures provides comprehensive data on how strain rates affect material properties.
Certain materials undergo phase transformations at specific temperatures, altering their mechanical properties. For example, steel experiences changes in its crystalline structure at different temperatures, impacting its strength and ductility.
Industry standards often require testing at different temperatures to verify that materials meet specific criteria for safety and performance. Standards like ASTM E8/E8M mandate testing at varying temperatures to provide a complete profile of material capabilities. By understanding the effects of temperature on tensile properties, engineers and scientists can design materials optimized for their intended applications.
Research on high-purity nickel, for instance, has shown distinct changes in tensile properties at temperatures between 500°F and 700°F. Testing tensile specimens at various temperatures is necessary for gaining a comprehensive understanding of material behavior, assuring reliable performance in diverse applications, and complying with industry standards. Through this process, it is possible to develop materials that can withstand the environmental conditions in which they will be used.
Measurements Affected by Temperature in Tensile Testing
At the beginning of our article, we mentioned a few measurements that can vary due to the temperature of tensile specimens during the test. Here are the key measurements that vary most in tensile testing at different temperatures and their brief descriptions:
Tensile Strength
Tensile strength, the maximum stress a material can withstand while stretched, changes with temperature. At higher temperatures, tensile strength typically decreases due to increased atomic mobility and intermolecular bond weakening. For example, high-purity nickel's tensile strength decreases from about 550 MPa at room temperature to approximately 350 MPa at 500°C. Conversely, at lower temperatures, the tensile strength can increase, but this often comes with greater brittleness. For instance, aluminum alloys can see an increase in tensile strength at cryogenic temperatures due to reduced atomic mobility and enhanced dislocation movement resistance.
Ductility
Ductility, the ability of a material to undergo significant plastic deformation before rupture, also varies with temperature. Higher temperatures generally increase ductility, allowing materials to stretch more before breaking. This is due to increased atomic movement and ease of dislocation motion at elevated temperatures. For example, the ductility of certain steel alloys can rise from about 10% elongation at room temperature to over 20% elongation at temperatures above 300°C. In contrast, lower temperatures decrease ductility, leading to higher fracture likelihood. An example is the reduced ductility of titanium alloys at temperatures below -100°C, which can drop to less than 5% elongation.
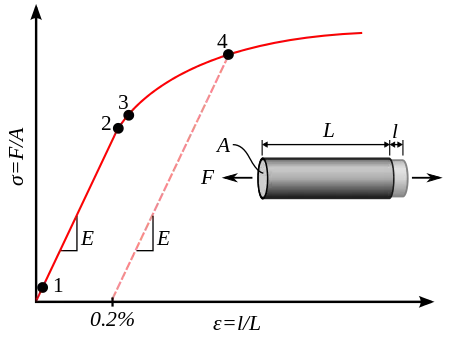
Strain Rate
Strain rate, the speed at which a material deforms, is significantly affected by temperature. At higher temperatures, materials may deform faster due to increased atomic mobility. For instance, aluminum and steel exhibit different strain rates when tested at elevated temperatures by UTM than at room temperature. Higher temperatures can decrease yield strength and increase ductility, making the material more malleable. Contrary, at lower temperatures, the strain rate is reduced, leading to greater yield strength but increased brittleness.
Microstructural Changes
Temperature differences can induce significant microstructural changes in materials. At elevated temperatures, phenomena such as grain growth, crystallization, and phase transformations can occur. For example, in steel, high temperatures can lead to the formation of larger grains, which generally reduce the material's strength but increase its ductility. On the other hand, low temperatures can preserve fine grain structures, increasing material strength but reducing ductility.
Phase Transformations
Certain materials undergo phase transformations at specific temperatures, significantly altering their mechanical properties. For example, steel transforms from austenite to martensite or bainite at different temperatures, impacting its hardness, strength, and ductility. Material behavior in different thermal environments is influenced by these transformations. Testing tensile specimens at different temperatures helps identify these phase changes and their effects, making certain that materials can be used reliably in applications like automotive components, especially those that are exposed to extreme temperatures.
Elastic Modulus
Temperature also influences the elastic modulus, which measures material stiffness. Generally, the elastic modulus decreases with increasing temperature, indicating a reduction in stiffness due to atomic bond softening. For example, metals such as titanium and nickel alloys show a significant decrease in elastic modulus at elevated temperatures. On the other hand, at lower temperatures, the modulus increases, leading to stiffer and more brittle behavior. When designing materials that must maintain stiffness under changing temperatures, this characteristic is a necessity.
Why Test Tensile Specimens at Different Temperatures?
Performing tensile tests at different temperatures is necessary as materials often experience various temperatures in real-world applications. Evaluating material performance at different temperatures allows engineers to predict material behavior.
Temperature variations can significantly impact a material's microstructure, altering its mechanical properties. High temperatures can cause grain growth or phase transformations in metals, which affect strength and ductility. Testing at different temperatures allows scientists to observe these changes and adjust material compositions or treatments to improve performance. For instance, high-temperature tests can reveal how alloys develop larger grains, reducing strength but increasing ductility, while low temperatures can maintain fine grain structures, increasing strength but reducing ductility.
Materials can also undergo phase transformations at specific temperatures, significantly changing their properties. Steel, for example, transforms from austenite to martensite or bainite at a range of temperatures, affecting hardness and strength. Testing at these temperatures helps engineers understand and control these transformations so that materials retain their desired properties under thermal stress. By identifying these transformations during tensile testing, potential issues with material performance can be predicted and mitigated.
Furthermore, tensile testing at varying temperatures guarantees that materials meet stringent performance requirements and perform reliably under different thermal conditions. Having this understanding is important for designing safer, more efficient products, especially for critical applications like jet engines and space shuttles. These materials must maintain integrity at extremely high temperatures to provide safety.
Compliance with industry standards, such as ASTM E21 and ISO 6892-2, allows for the quality and reliability of materials to be assured at all times. These standards specify testing conditions, including temperature ranges, so that materials perform as expected in different environments. Compliance with these standards reduces failure risk in critical applications, guaranteeing reliability and regulatory compliance.
Common Materials Tested in Tensile Testing at Different Temperatures
Testing materials by tensile under various temperature conditions is possible for a wide selection of materials. However, some materials might disintegrate, melt, or become so brittle that a slight impact on a metal table could shatter the specimen. Therefore, certain materials are commonly used for tensile testing at different temperatures. Here are some of the most common materials that have been tested:
Steel
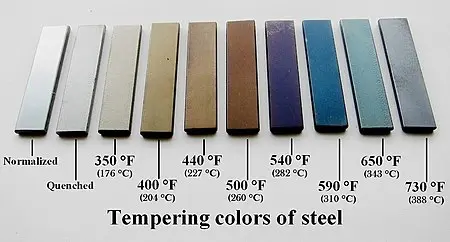
Steel is one of the most widely tested materials due to its extensive use in construction, automotive, and industrial applications. Tensile testing of steel is conducted over a broad temperature range to understand its performance under different conditions. For instance, mild steel typically shows tensile strengths between 400-500 MPa, while high-strength, low-alloy steels can reach 800 MPa. Steel testing temperatures vary from cryogenic levels (-196°C) to high temperatures exceeding 600°C. This extensive testing helps in evaluating how steel structures will behave under extreme cold or heat.
Aluminum
Aluminum is another common material tested for its tensile properties over a range of temperatures. Pure aluminum has a tensile strength of about 90-100 MPa, but aluminum alloys range from 200 to 600 MPa. Tensile testing for aluminum typically spans cryogenic temperatures up to about 500°C.
Copper
Copper's excellent electrical conductivity makes it a crucial material for electrical applications. However, it is also tested for its tensile properties to verify mechanical reliability. The tensile strength of copper is around 210-220 MPa, with copper alloys like bronze and brass exceeding 400 MPa. Tensile testing for copper is often performed at temperatures as low as -200°C to about 400°C. Understanding how copper and its alloys behave at different temperatures helps in designing components for electrical wiring, plumbing, and industrial machinery that need to operate reliably under varying thermal conditions.
Titanium
Titanium is known for its high strength-to-weight ratio and corrosion resistance. Commercially pure titanium has a tensile strength of about 240-370 MPa, whereas titanium alloys can exceed 1000 MPa. Tensile testing for titanium typically ranges from cryogenic temperatures to 600°C. Titanium components must undergo this testing to make sure they can maintain their performance in extreme cold as well as extreme heat
Nickel and Nickel Alloys
Nickel and its alloys, particularly nickel-based superalloys, are essential for high-temperature applications due to their exceptional strength and resistance to oxidation and corrosion. Nickel's tensile strength ranges from 460 to 1400 MPa, with superalloys exceeding 1000 MPa. Tensile testing for nickel and its alloys is conducted from -196°C to above 800°C.
Polyethylene (PE)
Polyethylene is a popular polymer with varying tensile strengths depending on its density. Low-Density Polyethylene (LDPE) typically has a tensile strength of 8-17 MPa, while High-Density Polyethylene (HDPE) ranges from 20-33 MPa. Tensile testing for polyethylene is conducted at -100°C to 100°C.
Polypropylene (PP)
Polypropylene is an all-purpose polymer used in hundreds of applications from packaging to automotive components. Its tensile strength typically ranges from 25-35 MPa. Tensile testing for polypropylene spans from -50°C to 150°C. Performing this test assures that polypropylene products will perform as expected under multiple thermal conditions.
Polyvinyl Chloride (PVC)
PVC is a commonly used thermoplastic known for its durability and chemical resistance. The tensile strength of rigid PVC can be up to 55 MPa, while flexible PVC typically has a tensile strength of 10-25 MPa. Tensile testing for PVC is usually performed at -40°C to 60°C
Industries and Products Benefit from Tensile Testing at Different Temperatures
Each industry has its own products which are tested under different temperature conditions in order to make sure they are suitable for tensile testing. It is worth exploring which industries are leading in such testing as well as examples of products in which testing is crucial to delivering a good product.
Aerospace Industry
Various temperatures are used in the aerospace industry to test tensile strength. Aircraft and spacecraft are exposed to extreme temperatures during flight and reentry. Components such as turbine blades, fuselage materials, and landing gear must withstand these conditions without failure. For example, turbine blades made from nickel-based superalloys are tested at high temperatures to verify they can endure jet engines' intense heat and stress. Similarly, the fuselage of an aircraft, often made from aluminum alloys, is tested at both high and low temperatures to remain intact during high-altitude flights.
Automotive Industry
In the automotive industry, tensile testing at different temperatures is used to make sure that vehicles remain safe and functional under varying environmental conditions. Components such as engine parts, body panels, and suspension systems are subject to temperature changes from freezing winters to hot summers. For instance, high-strength steel used in car frames is tested at different temperatures to verify structural integrity in collisions. Additionally, rubber components like tires and seals undergo tensile testing at low temperatures to prevent brittleness and failure during cold weather.
Construction Industry
The construction industry uses tensile testing to guarantee the durability and safety of building materials exposed to diverse environmental conditions. Steel beams, concrete reinforcements, and glass panels are examples of materials that undergo tensile testing at varying temperatures. For instance, steel used in bridges is tested from sub-zero temperatures to high heat to confirm it can handle thermal expansion and contraction without compromising structural integrity. Similarly, glass panels for skyscrapers are tested to withstand both high temperatures from sunlight and cold winter conditions, preventing cracking or shattering.
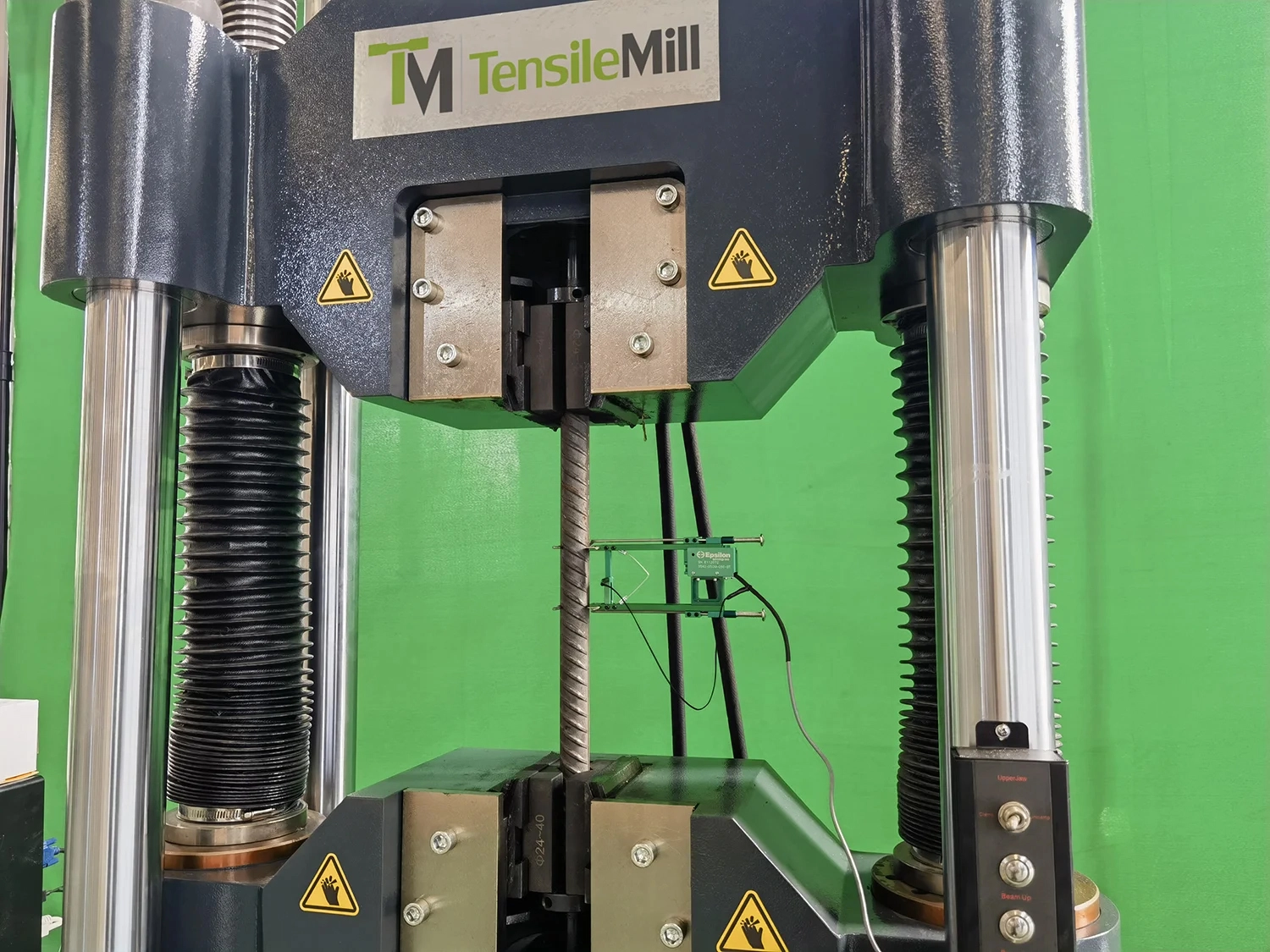
Medical Devices
Medical devices, particularly implants and prosthetics, must maintain their mechanical properties at body temperature and during sterilization processes, which often involve high temperatures. Materials like titanium and certain polymers used in implants undergo tensile testing at different temperatures to verify that they do not fail in the human body or during sterilization. For example, hip and knee implants made from titanium alloys are tested to verify they can withstand the body's constant temperature and autoclaving high temperatures without losing their structural integrity.
Electronics Industry
In the electronics industry, components such as circuit boards, connectors, and casings must withstand thermal cycling during operation. Tensile testing at different temperatures ensures these components can handle thermal expansion and contraction due to power fluctuations and environmental changes. For instance, solder joints on circuit boards are tested to ensure they do not crack under heat stress, maintaining electrical connectivity. Similarly, plastic casings for electronic devices are tested to guarantee they do not warp or break under different temperature conditions.
Quality Tensile Sample Preparation for Reliable Testing
Whether performing standard tensile testing or tensile testing of specimens at high or low temperatures, tensile specimen quality plays a key role. Poorly prepared specimens can lead to inaccurate test results, potentially compromising the reliability and safety of the materials being tested. As a company specializing in tensile testing and specimen preparation, and as one of the largest suppliers of equipment for tensile testing needs, we want to introduce you to our state-of-the-art solution: the TensileTurn CNC - Industrial Upgrade Model.
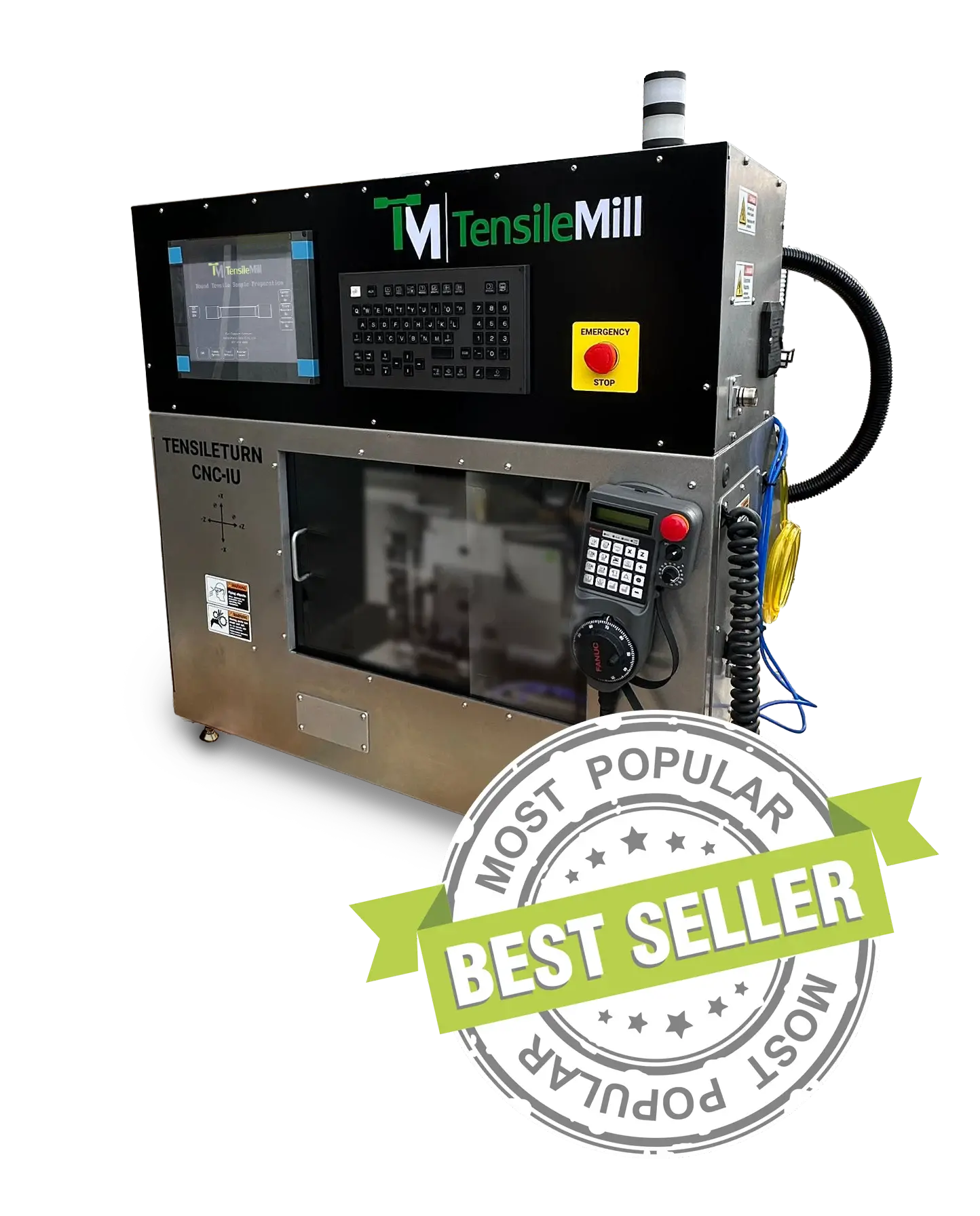
The TensileTurn CNC - Industrial Upgrade Model is a compact, automatic CNC lathe designed for industrial use, specifically for making accurate round tensile specimens. This machine guarantees the highest tensile test accuracy by providing precisely prepared specimens. With its touchscreen interface, even operators without machining experience can quickly and efficiently prepare tensile specimens to the desired size. Users can select from a library of common standards such as ASTM, ISO, and DIN, or input their own dimensions via the touchscreen numerical keypad.
The TensileTurn CNC - Industrial Upgrade is an upgraded version of our Classic system, featuring advanced TensileSoft and Carbon software. This allows more experienced operators to program the system for numerous applications including cutting, sanding, knurling, drilling, facing, or turning. It can prepare standard round tensile specimens, sub-size specimens, threaded tensile specimens, button-head tensile bars, fatigue specimens, and other round testing specimens. Operators simply load the machine with round, square, or irregular stock.
By choosing our products and services, you can be confident that your tensile specimens will be prepared to the highest standards, resulting in reliable and accurate testing outcomes. You can achieve outstanding results with our assistance.
The Importance of Specimen Temperature in Tensile Testing
Identifying the effect of specimen temperature on tensile test results is crucial for predicting material performance under different real-world conditions. By evaluating how materials behave at different temperatures, engineers and scientists can ensure that components are designed to withstand thermal stresses. This comprehensive understanding helps optimize material compositions and treatment processes, providing reliability and safety in high-risk applications.
Testing at different temperatures provides insights into key mechanical properties such as tensile strength, ductility, strain rate, and elastic modulus. These properties can significantly vary with temperature, affecting materials' performance under extreme conditions.
TensileMill CNC is here to help you with all your tensile testing needs. From providing advanced equipment to preparing your own tensile specimens, we offer comprehensive solutions to help you achieve accurate and reliable testing results. You can request an online quote or contact us directly for assistance. Let us support you in achieving remarkable results in your tensile testing endeavors.