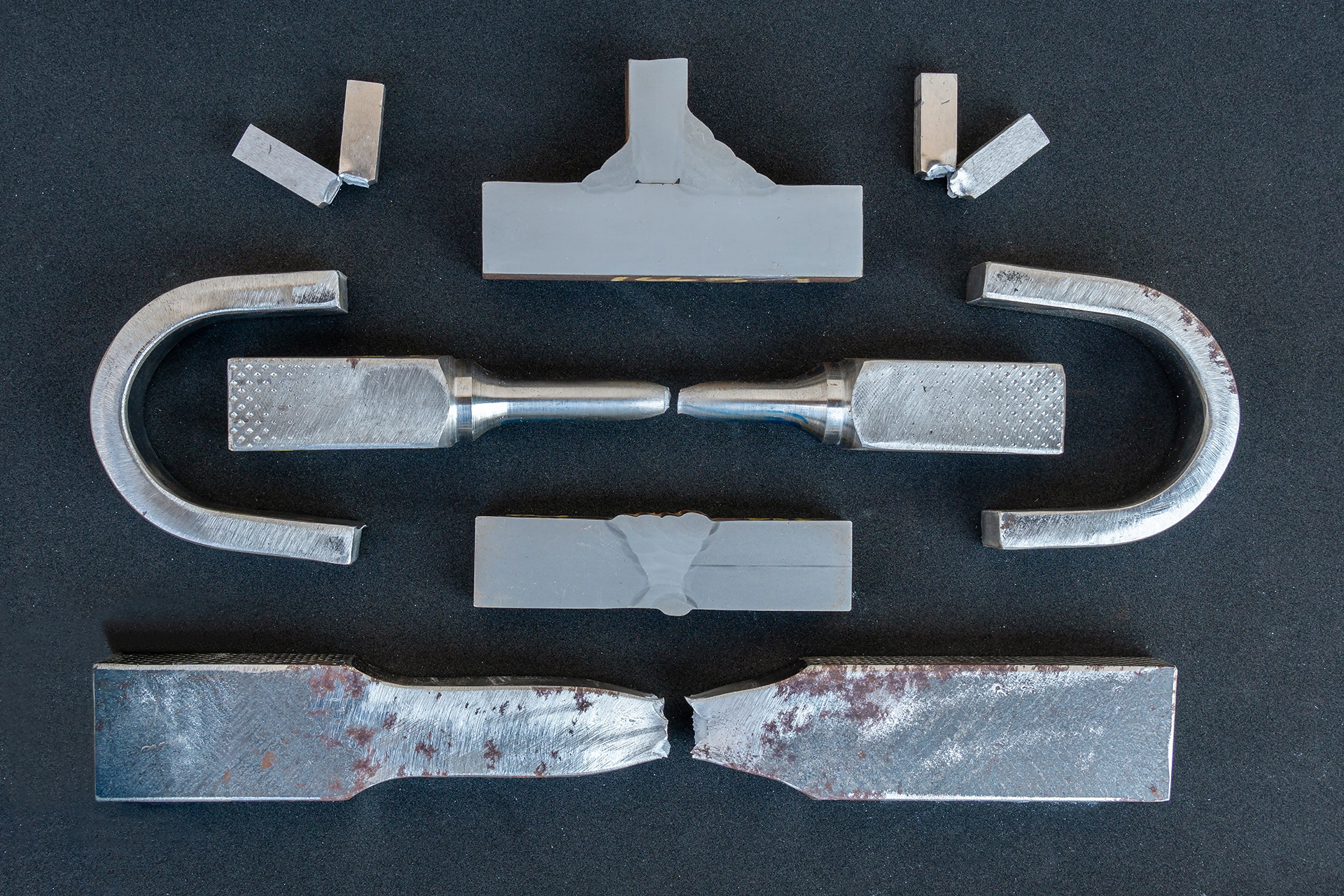
Throughout history, there have been many tragic engineering failures. Some resulted in minimal harm, while others led to significant death and property loss. This illustrates the critical responsibility engineers bear, as their creations directly impact people's safety and lives. In engineering, there is no room for error.
To avoid such errors, engineers must know their calculations and designs. Material testing, which involves a comprehensive array of data and measurements, is an integral part of this process. Among these tests, the tensile strength test is of the greatest importance. Tensile testing, which measures materials' resistance to breaking under tension, has become a necessity for modern engineers. This is especially true for those designing large structures such as bridges and buildings, where failure can have dire consequences.
Even though tensile testing was developed in the 15th century by Leonardo da Vinci and was actively used in the 19th century, many engineers did not fully appreciate its importance. Despite advancements in testing methodologies and equipment, numerous engineering failures have occurred due to neglecting proper material testing protocols. Tensile testing became more standardized and mandatory in the mid-20th century, with organizations like ASTM developing specific standards for testing materials. However, the lack of rigorous application of these tests led to catastrophic failures.
The purpose of this article is to explore tragic events from the 20th century that occurred as a consequence of failure to comply with testing standards and measurements, including tensile tests. We will discuss these incidents in detail and explain the importance of tensile strength testing in these cases. Our objective is to demonstrate the critical role that tensile testing plays in preventing such disasters by examining these events.
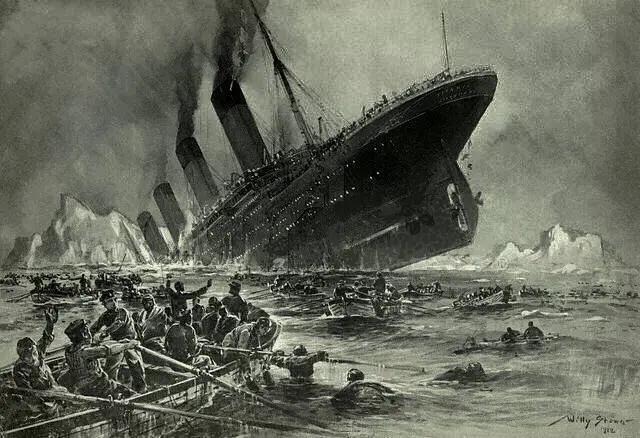
The Sinking of the RMS Titanic
As a starting point, let us consider an accident well-known to everyone - the Titanic's sinking. The RMS Titanic was a marvel of early 20th-century engineering, yet its tragic sinking on April 15, 1912, remains one of the most infamous maritime disasters in history. Despite being deemed "unsinkable," the Titanic's collision with an iceberg led to catastrophic structural failures that caused the ship to sink in less than three hours, resulting in the deaths of over 1,500 passengers and crew members.
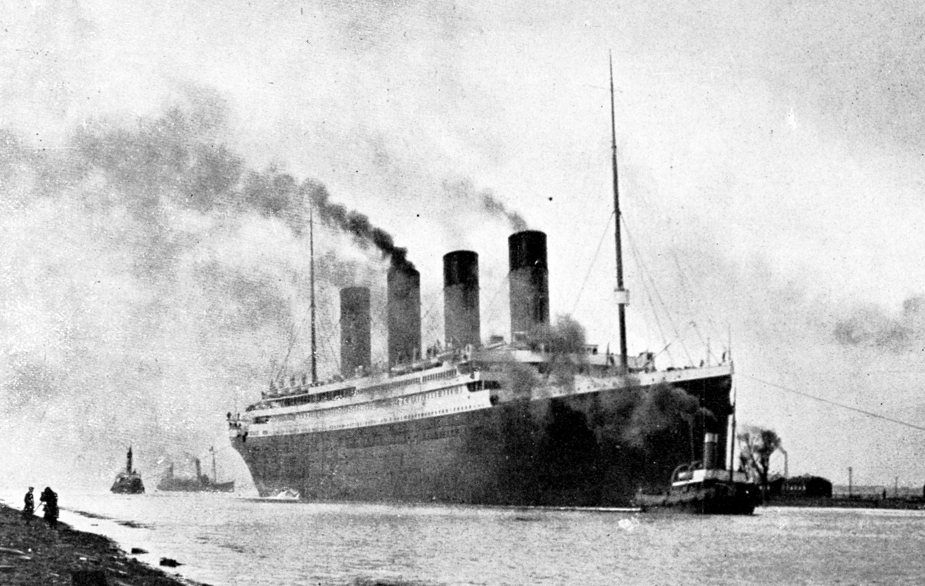
The Titanic's design included 16 major watertight compartments intended to keep the ship afloat even if several were breached. However, the collision with the iceberg caused critical damage to the hull. The iceberg impact compromised six of these compartments, which rapidly flooded, leading to the ship's bow dipping and water spilling over into additional compartments, exacerbating the flooding.
The primary material failure involved the ship's hull steel and the wrought iron rivets that held the hull plates together. Analyses of the steel and rivets recovered from the wreck revealed high levels of sulfur and slag impurities, making them brittle in the cold North Atlantic waters. Upon impact with the iceberg, the brittle steel hull plates fractured rather than deformed, and the rivets failed, either by shearing off or popping out, leading to the separation of the hull plates.
Additionally, design flaws in the Titanic's watertight compartments contributed to the disaster. While the compartments were designed to be watertight, the bulkheads did not extend high enough, allowing water to spill from one compartment to the next as the ship's bow sank deeper. This flaw significantly accelerated the sinking process.
Had the Titanic's materials been subjected to rigorous tensile strength testing, the deficiencies in the steel and rivets might have been identified and addressed. Proper tensile testing would have revealed the brittleness of the steel at low temperatures and the high slag content in the rivets, prompting the use of higher quality, more ductile materials. This could have prevented the catastrophic failure of the hull and rivets, potentially averting the disaster or at least mitigating its severity.

The Tacoma Narrows Bridge Collapse
The Tacoma Narrows Bridge, nicknamed "Galloping Gertie," was a suspension bridge in Washington State that opened on July 1, 1940. It was designed by Leon Moisseiff, a renowned bridge engineer, and was the third-longest suspension bridge in the world at the time. The bridge was intended to be a marvel of modern engineering, but it tragically collapsed just four months after its opening on November 7, 1940.
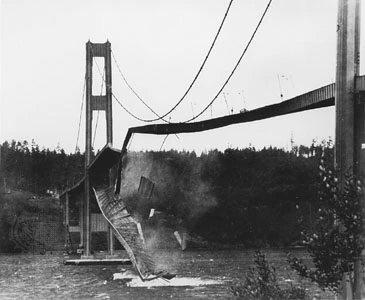
The Tacoma Narrows Bridge collapse was due to its design, which did not adequately account for aerodynamic forces. The bridge's slender and narrow design, coupled with shallow plate girders instead of deeper trusses, made it highly susceptible to wind-induced oscillations. From its inception, the bridge exhibited significant vertical movements in even moderate winds, a phenomenon that led to its nickname, "Galloping Gertie".
The bridge's design flaws were exacerbated by its insufficient stiffness. The solid plate girders acted like sails, catching the wind rather than allowing it to pass through, which would have been possible with perforated girders. Despite various attempts to stabilize the bridge, including the addition of tie-down cables and hydraulic buffers, these measures proved ineffective. On the day of its collapse, the bridge experienced torsional oscillations—twisting movements that increased in amplitude until the structure ultimately failed.
If tensile strength testing had been rigorously applied to the Tacoma Narrows Bridge materials and design, it is possible that structural deficiencies could have been identified and corrected. For instance, understanding the tensile limits of the materials might have prompted the use of more robust stiffening trusses instead of shallow plate girders, providing the necessary rigidity to withstand the aerodynamic forces that ultimately caused the collapse.
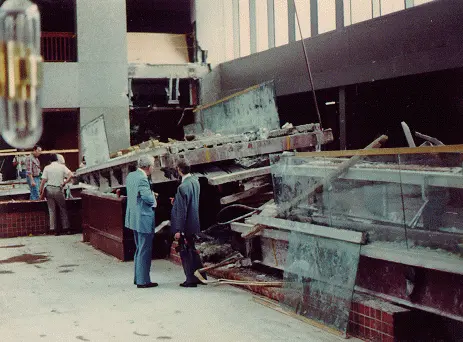
The Collapse of the Hyatt Regency Walkway
The Hyatt Regency walkway collapsed on July 17, 1981, in Kansas City, Missouri. This tragic event resulted in the deaths of 114 people and injuries to over 200 others when two suspended walkways collapsed into a crowded lobby during a tea dance.
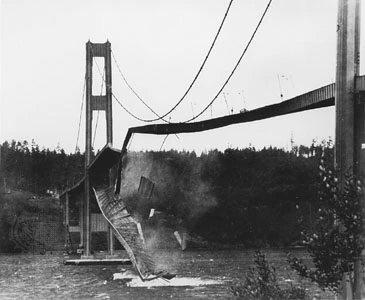
The accident was primarily caused by a critical design change during the walkway construction. The original design involved a single set of steel hanger rods running from the ceiling through the fourth-floor walkway to the second-floor walkway. However, to simplify construction, the design was altered so that two sets of rods were used: one set from the ceiling to the fourth-floor walkway and another set from the fourth-floor walkway to the second-floor walkway. This change effectively doubled the load on the connection between the fourth-floor walkway and its support beams.
The design change led to a significant flaw. The steel hanger rods were now bearing much more weight than initially intended. The beams supporting the fourth-floor walkway were not strong enough to handle the combined weight of both walkways and the people on them. On the day of the collapse, the connections failed, causing the fourth-floor walkway to fall onto the second-floor walkway, and both plummeted to the lobby floor.
Even with the redesign done during construction, data from proper tensile testing could have revealed the inadequacy of the rods and beams to bear the doubled load, prompting a necessary redesign or reinforcement of the connections to guarantee that they could handle the expected stresses.
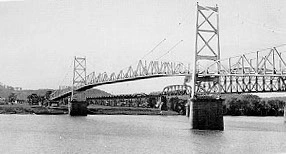
The Silver Bridge Collapse
The Silver Bridge, which connected Point Pleasant, West Virginia, and Gallipolis, Ohio, collapsed on December 15, 1967. This tragic event resulted in the deaths of 46 people and marked a significant moment in bridge engineering history in the United States.
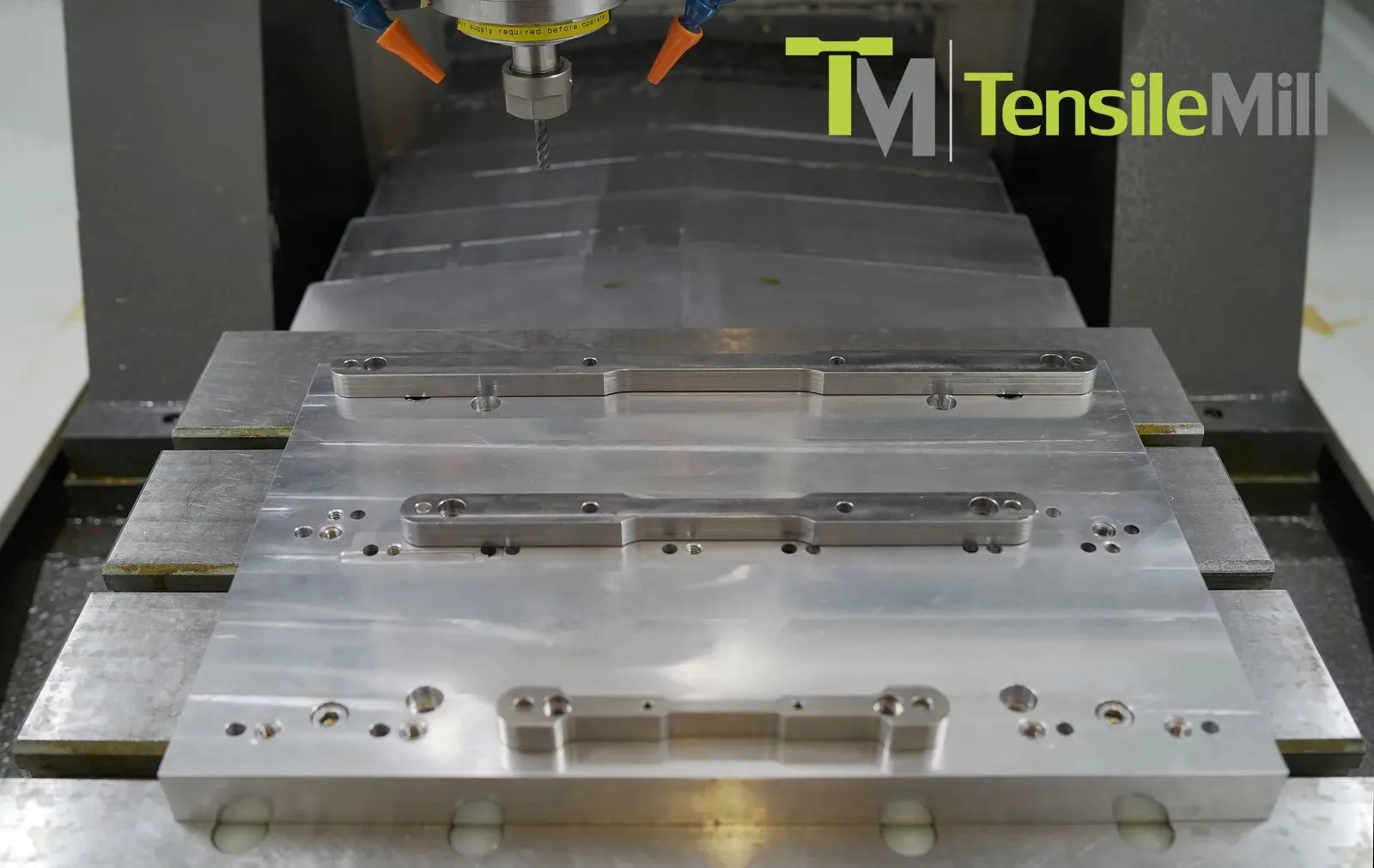
The bridge collapsed mainly due to a critical flaw in one of the bridge's eyebars. The Silver Bridge was one of the first in the nation to use an innovative eyebar-link suspension system rather than traditional wire-cable suspension. One of these eyebars had a small, unseen defect that eventually cracked and corroded. This crack grew over time due to stress corrosion and fatigue, eventually leading to a brittle fracture under the bridge's load stress.
The bridge's design included only two eyebars per link, lacking redundancy. This meant that the failure of a single eyebar could (and did) lead to the collapse of the entire structure. On the day of the collapse, the critical eyebar failed, transferring the load to the remaining eyebars, which could not bear the additional stress, leading to the catastrophic failure of the entire bridge.
Proper tensile testing would have provided information regarding the susceptibility of the eyebars to corrosion and fatigue under stress. By identifying these weaknesses, a more robust design could have been developed, such as providing redundancy by increasing the number of eyebars per link.
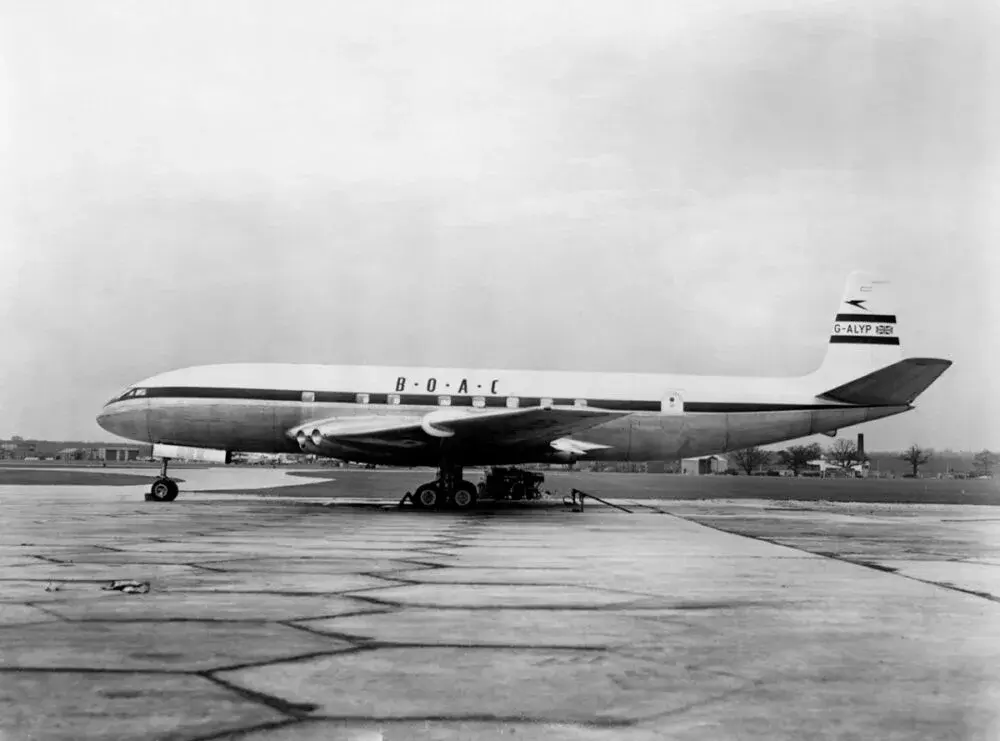
The De Havilland Comet Disasters
The De Havilland Comet was the world's first commercial jet airliner, entering service in 1952. It was a pioneering aircraft, offering faster travel times and higher altitudes than its predecessors. However, a series of catastrophic failures in the early 1950s revealed serious flaws in its design, leading to multiple fatal crashes.
The first major disaster occurred in January 1954, when BOAC Flight 781 broke up in mid-air over the Mediterranean Sea shortly after taking off from Rome. All 35 people on board were killed. This was followed by another crash in April 1954 involving a South African Airways Comet, which also disintegrated mid-flight, killing all 21 people on board.
Investigations revealed that the primary cause of these crashes was metal fatigue in the aircraft's fuselage. The repeated pressurization and depressurization cycles experienced during flight caused stress fractures in the aircraft's skin. These cracks originated from areas of high-stress concentration, such as the corners of the aircraft's square windows and the riveted joints in the fuselage. The combination of these design flaws led to catastrophic failures under normal flight operations.
By performing careful tensile tests, it would have been possible to determine whether the fuselage materials were susceptible to fatigue under cyclic loading conditions. Using tensile testing to simulate repeated pressurization cycles would have identified the possibility of cracks forming and propagating in the aircraft's skin, prompting design modifications to avoid catastrophic failures.
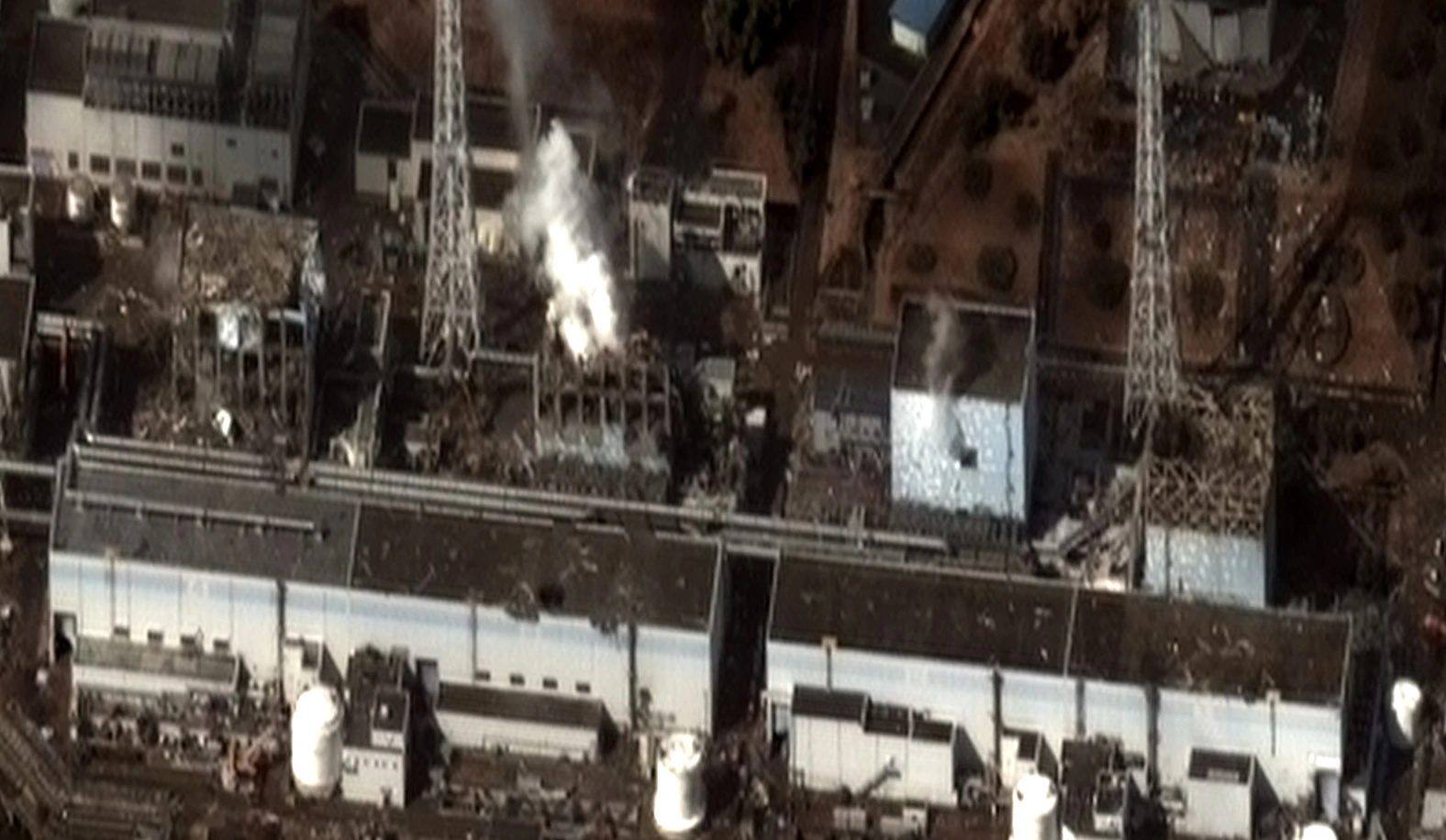
Fukushima Daiichi Nuclear Disaster
The Fukushima Daiichi nuclear disaster occurred on March 11, 2011, following a massive earthquake and tsunami that struck Japan's northeastern coast. This incident is considered the second-worst nuclear accident in history, surpassed only by the Chornobyl disaster. The tsunami disabled the power supply and cooling of three Fukushima Daiichi reactors, leading to a severe nuclear meltdown and the release of radioactive materials into the environment.
The primary cause of the Fukushima disaster was the loss of power and subsequent failure of cooling systems. The earthquake triggered an automatic shutdown of the reactors, but the tsunami that followed inundated the site, knocking out both the primary power supply and the backup diesel generators. Without power, the reactors' cooling systems failed, causing reactor cores to overheat and partially melt. Hydrogen gas, generated by the reaction of overheating fuel rods, accumulated and eventually caused explosions in three reactor buildings, releasing radioactive materials into the atmosphere.
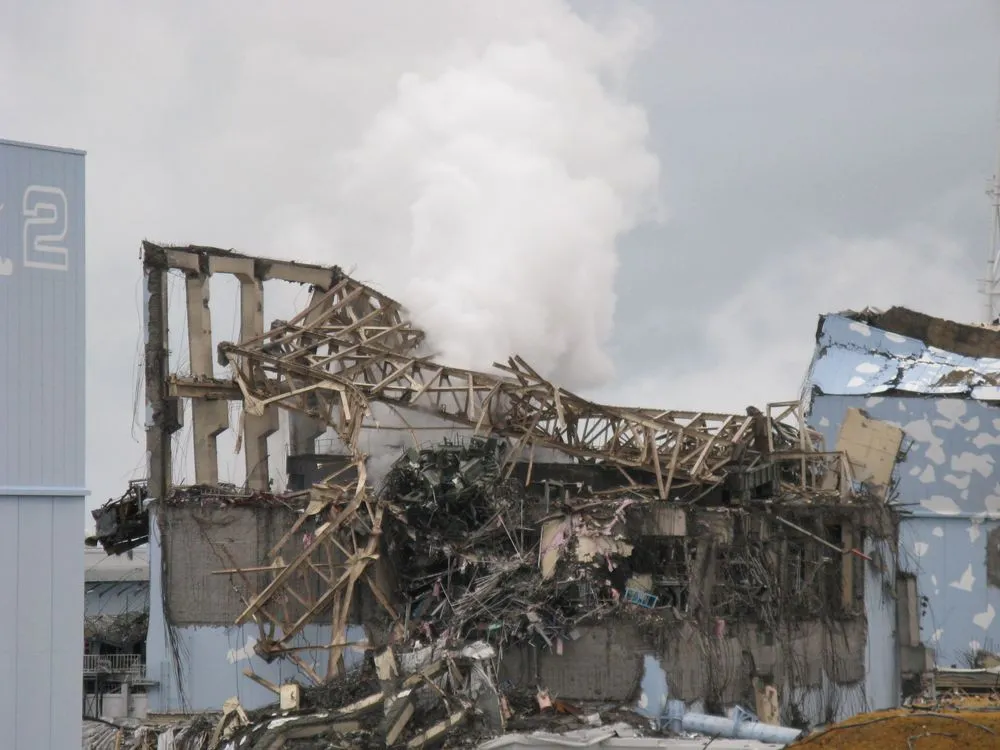
The reactors at Fukushima Daiichi were boiling water reactors (BWRs) with a Mark I containment design, including a steel reactor pressure vessel and a primary containment vessel. These systems were supposed to act as barriers to prevent radioactive materials release. However, the prolonged cooling loss led to fuel rod melting, which breached these containment barriers. The explosions caused by hydrogen buildup further compromised the reactor buildings' structural integrity, exacerbating radioactive materials release.
Tensile testing could have identified weaknesses in reactor pressure vessels and containment structures. By simulating extreme conditions and testing the materials' resistance to stress, tensile testing might have revealed vulnerabilities in the steel used for the containment systems. Identifying these weaknesses could have led to design improvements or reinforcements, potentially mitigating the extent of the disaster by making sure the structures could better withstand the conditions experienced during the meltdown.
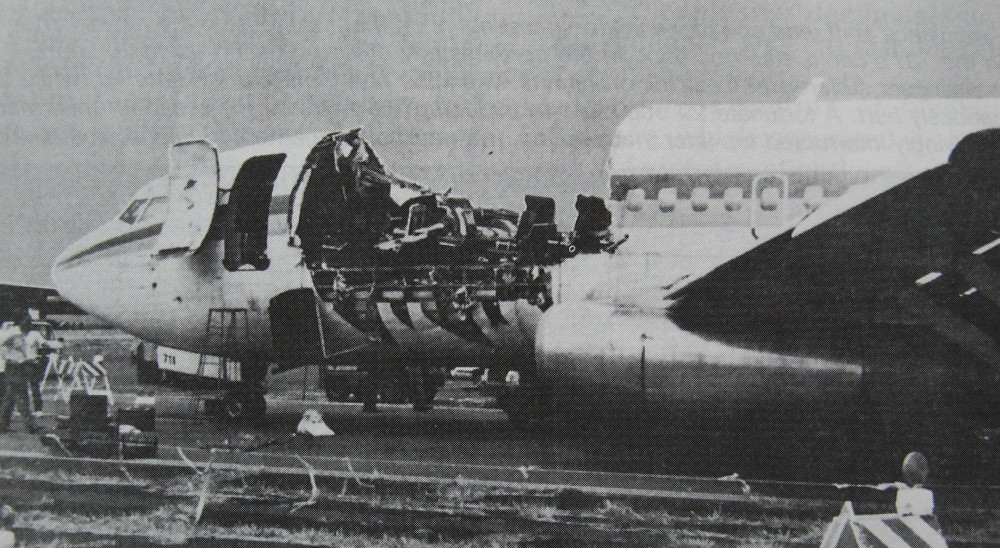
The Aloha Airlines Flight 243 Incident
On April 28, 1988, a routine flight from Hilo to Honolulu turned into a nightmare. Aloha Airlines Flight 243, a Boeing 737-200, experienced explosive decompression at 24,000 feet. A significant section of the fuselage roof was ripped away, exposing passengers to the open sky. Despite the severe damage, the pilots managed a miraculous landing at Kahului Airport in Maui, Hawaii. Tragically, one flight attendant was lost, and 65 passengers and crew members were injured.
A major cause of the catastrophic failure was metal fatigue in the fuselage. Over its operational life, the Boeing 737 completed more than 89,000 flight cycles. Each cycle of pressurization and depressurization contributed to the gradual weakening of the fuselage skin. Environmental conditions, including exposure to salt and humidity, further accelerate metal corrosion and fatigue, ultimately leading to failure.
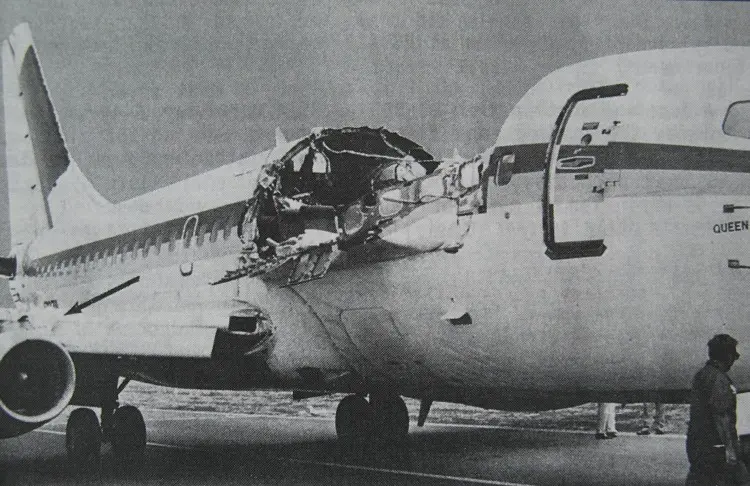
The failure occurred at a lap joint in the fuselage skin, where multiple cracks formed around the rivet holes. This area was a significant stress point, and fatigue cracks severely compromised structural integrity. The lap joint design relied on rivets to hold the materials together, which, over time, allowed cracks to develop and propagate. This culminated in the explosive decompression and loss of a large fuselage section.
Tensile testing could have detected the material's susceptibility to fatigue and cracking under cyclic loading conditions. By subjecting the fuselage materials to in-depth tensile testing, the tendency for crack formation around rivet holes could have been identified. This would have highlighted the need for design changes, such as reinforcing lap joints or using more fatigue-resistant materials, potentially preventing catastrophic failure.
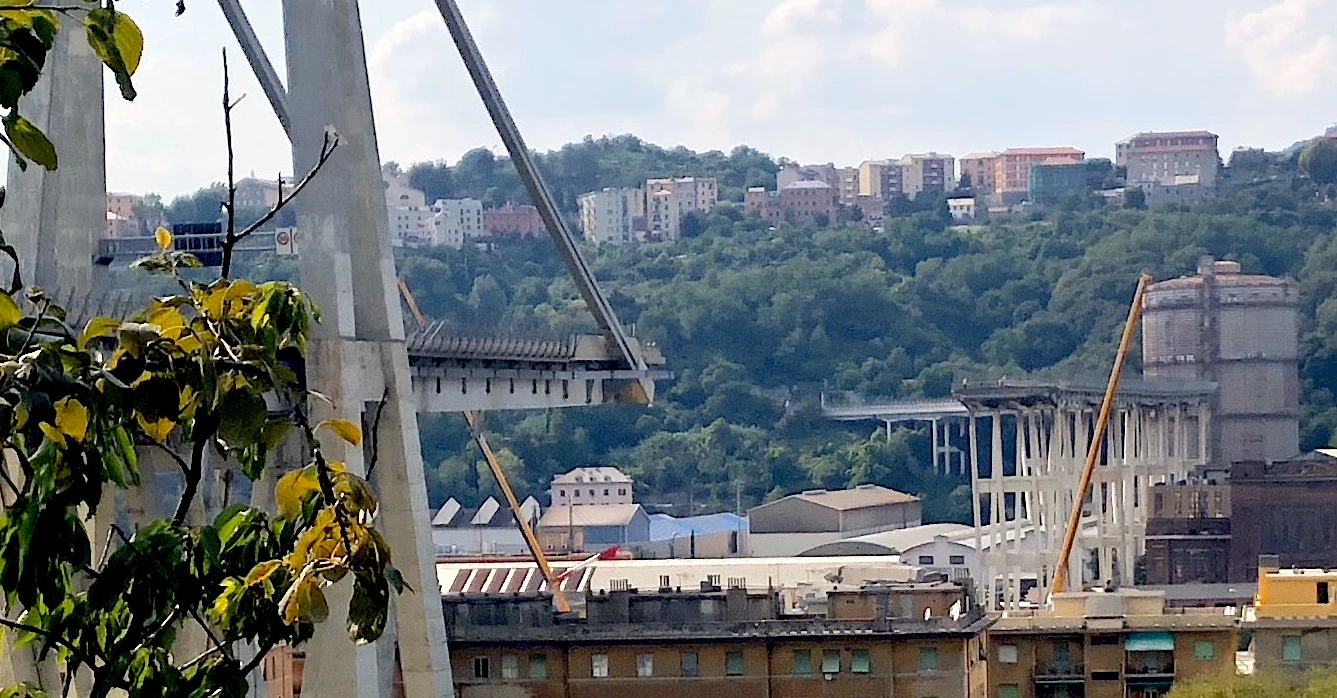
The Collapse of the Morandi Bridge
The collapse of the Morandi Bridge on August 14, 2018, in Genoa, Italy, was a tragic event that killed 43 people. The bridge, part of the Polcevera Viaduct, had been in service since 1967 and was a critical infrastructure component of the region.
In this case, the main cause of the disaster was the failure of one of the bridge's cable stays, which broke during a severe storm. The cable stay, which was part of the support system, failed due to corrosion and structural deficiencies. The bridge's concrete encasements made it difficult to inspect and maintain internal steel cables. In the course of time, environmental conditions, including high salinity from the nearby sea and pollution from industrial activities, led to significant corrosion of steel cables and other structural elements.
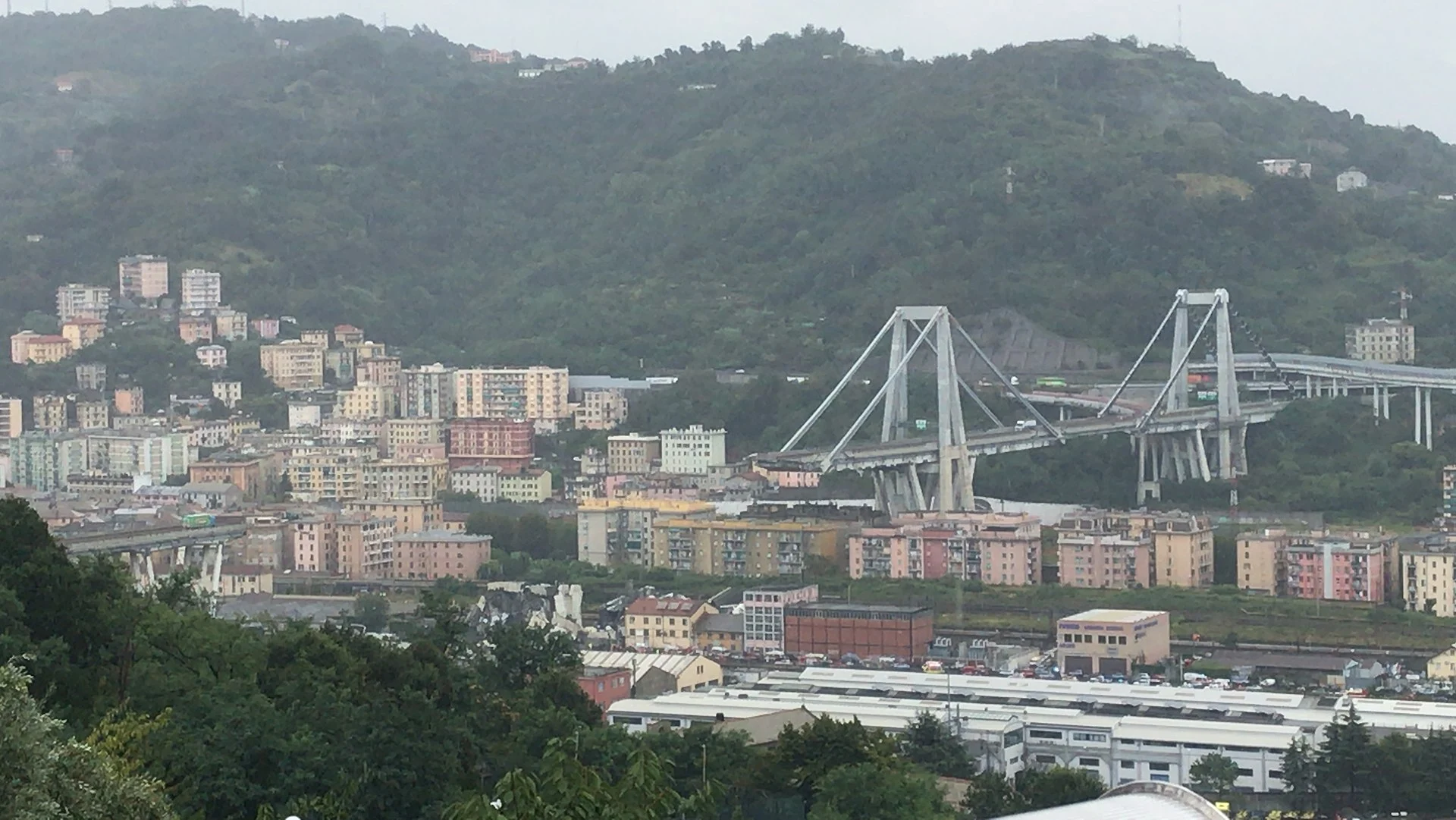
The bridge's design, which included concrete-encased steel cables, proved problematic as it was challenging to monitor and maintain. Reports indicated that from as early as the 1970s, signs of corrosion and structural deterioration were evident, yet comprehensive maintenance and necessary reinforcements were not effectively implemented. The combination of increased traffic load over the decades and environmental impact exacerbated bridge vulnerabilities.
While tensile testing alone cannot guarantee the detection of material corrosion, it can still provide valuable information regarding weaknesses and fatigue in materials. By regularly testing the materials under stress conditions, engineers could have detected early signs of deterioration and weakness in the steel cables. This data would have prompted more timely and effective maintenance strategies, such as replacing corroded cables or strengthening the structure to withstand environmental stressors.
Innovations in the Field of Tensile Testing
Tensile testing has advanced significantly due to new materials, updated standards, and changes in sample shapes. However, the most substantial improvements in tensile testing procedures are attributed to advancements in testing equipment. Two primary categories of equipment crucial for tensile strength testing are Universal Testing Machines (UTMs) and tensile sample preparation tools, commonly known as CNC machines.
Universal testing machines measure the mechanical properties of different materials by applying controlled tension until the specimens break. Recent advancements integrate automation and digitalization, making UTMs more efficient and precise. Automated systems now use robotic arms for sample preparation and testing, reducing human error and variability.
Tensile sample preparation tools, particularly CNC machines, produce high-quality test specimens with precise dimensions. Modern CNC machines feature AI and full automation, allowing users to produce specimens without specialized skills. With simple touchscreen inputs, the machine can prepare the sample, highlighting the ease and efficiency brought by these advancements.
AI and other advanced technologies are rapidly progressing in tensile testing. AI-driven software analyzes extensive test data to identify patterns and correlations, providing real-time feedback and optimizing testing procedures. Digitalization has improved data management, with advanced sensors and data acquisition systems collecting high-resolution data throughout the testing process. Cloud-based storage solutions enable secure and accessible repositories for test data, facilitating collaborative analysis across different locations.
TensileSoft™ 2.0 - World Leading Round Tensile Sample Preparation Software - Training Video
Sustainability is a key focus in developing tensile testing equipment. Modern UTMs and CNC machines are designed with eco-friendly materials and energy-efficient components, reducing their environmental impact. Green testing protocols, using environmentally friendly materials and procedures, are becoming more common, aligning with global sustainability goals. With such advancements, engineers can eliminate technical errors that have historically caused significant deaths.
Advanced Tensile Testing Equipment from TensileMill CNC
If you are looking for high-quality equipment for tensile testing procedures in your lab, you have come to the right place. At TensileMill CNC, we offer a full range of state-of-the-art equipment, including CNC machines for tensile specimen preparation and universal testing machines for precise and reliable testing procedures. Please allow us to demonstrate one of our bestseller products, which may be exactly what you are looking for.
TensileMill CNC MINI - Compact Flat Tensile Specimen Preparation Machine
The TensileMill CNC MINI - Compact Flat Tensile Specimen Preparation Machine is a machine that produces flat tensile specimens that are necessary for accurate tensile testing. This advanced unit integrates CNC technology, assuring that each specimen adheres to the exact dimensions required for consistent and repeatable test results.

The machine features an intuitive touchscreen interface, making it user-friendly and reducing operator training. Its compact design fits easily into most laboratory environments without taking up excessive space. Despite its small footprint, the TensileMill CNC MINI is built with robust construction and high-quality components.
One of the key benefits of this machine is its ability to automate the preparation process, significantly minimizing human error and leading to more reliable and reproducible test outcomes. The precision engineering of this unit ensures that each specimen is prepared to meet stringent standards, which is critical for labs dedicated to material testing. This machine is indispensable for any lab aiming to maintain high accuracy standards in tensile testing.
The SHM Class A Series - Servo-Hydraulic Universal Testing System
The SHM Class A Series - Servo-Hydraulic Universal Testing System is a flexible and powerful unit designed for comprehensive material testing. This system can perform a number of tests, including tension, compression, and flexural tests, which makes it ideal for a broad range of material science and engineering applications.
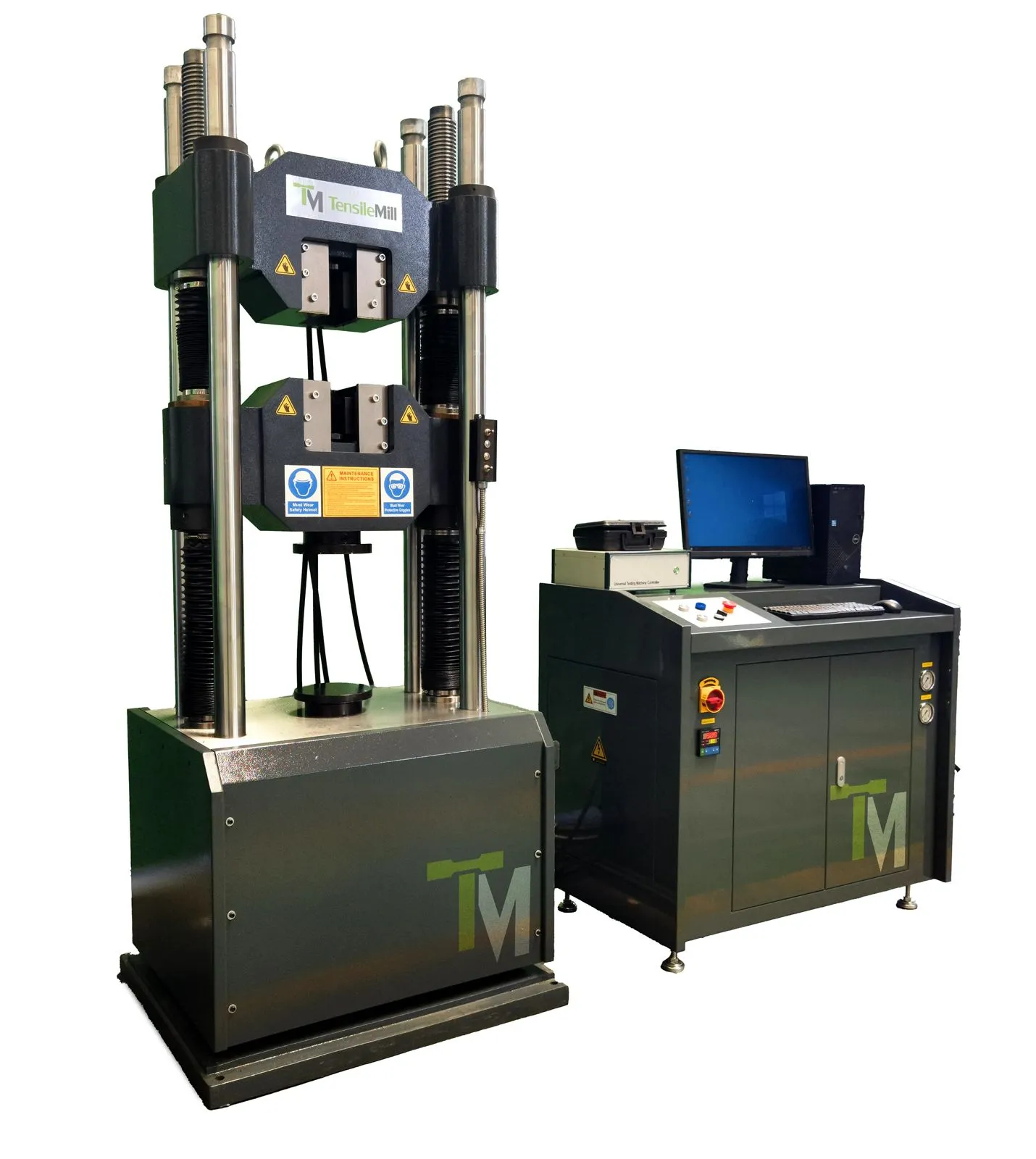
A standout feature of the SHM Class A Series is its servo-hydraulic control system, which ensures precise and repeatable testing conditions. The integrated precision load cell provides accurate force measurements. The system's high load capacity, ranging from 600kN to 1000kN, makes it suitable for testing a broad spectrum of materials, from metals to composites.
The user-friendly software that accompanies this testing system simplifies the setup and execution of tests, as well as the analysis of results. Its intuitive interface allows users to easily configure test parameters and monitor real-time data, improving testing efficiency. Additionally, the robust construction and high-quality components of the SHM Class A Series ensure longevity and dependable performance in demanding lab environments.
A laboratory that requires robust and precise testing capabilities will benefit greatly from the SHM Class A Series. With its advanced features and high load capacity, it is an important tool for ensuring the quality of material testing as well as supporting the development and validation of new materials and products.
The Evolution and Impact of Tensile Testing Technology
Throughout history, numerous tragic engineering failures have highlighted the critical importance of rigorous material testing, particularly tensile strength testing. The Titanic's sinking, the Tacoma Narrows Bridge collapse, the Hyatt Regency walkway failure, the Silver Bridge collapse, the De Havilland Comet disasters, the Fukushima Daiichi nuclear disaster, the Aloha Airlines Flight 243 incident, and the Morandi Bridge collapse are stark reminders of the consequences of neglecting proper testing protocols. Each of these events underscores how vital it is for engineers to make sure that their designs and materials can withstand stress.
In modern times, advancements in tensile testing equipment have significantly improved material testing accuracy and reliability. Universal testing machines and CNC machines for specimen preparation have revolutionized the field, integrating automation, AI, and advanced data management. This has helped reduce human error and increase precision. These innovations have enabled engineers to detect potential material weaknesses and design flaws more effectively, preventing catastrophic failures.
Today, a lot of calculations, test preparations, and executions are performed with advanced machinery. If you need the latest modern tensile testing equipment, please explore our selection of machines from TensileMill CNC. We are here to help you handle your tensile testing needs. If you have questions or want to learn more from us, please do not hesitate to contact us directly or request an online quote.