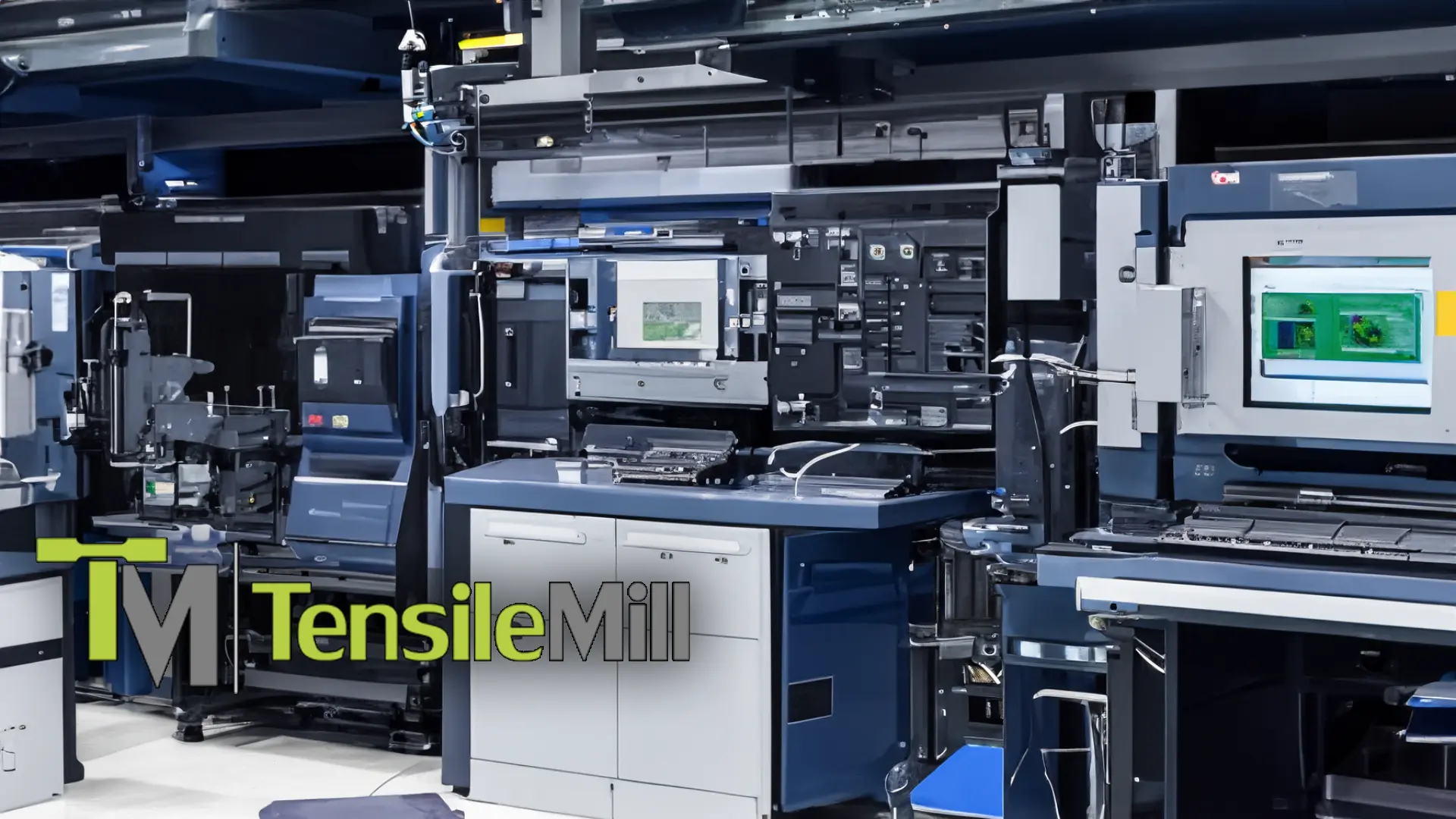
Today, in the ever-changing industrial sector, the CNC (Computer Numerical Control) industry, an integral part of manufacturing, is focusing on sustainable practices. This shift is driven by a growing global consciousness about environmental impacts. Traditional CNC machining, while efficient, often results in significant waste, consumes considerable energy, and uses materials inefficiently. As a result, pollution, resource depletion, and climate change are caused.
Recent advancements in the CNC sector have revolutionized sustainability. For instance, waste reduction is achieved through optimized material use, minimizing cut-off waste, and employing efficient part nesting methods. Energy efficiency has also become a central focus, with CNC machines becoming more energy-efficient, reducing power consumption during processes. This is complemented by investments in advanced technologies such as regenerative drives and smart energy management systems.
Moreover, water conservation efforts in CNC operations, particularly in cooling and lubrication processes, are gaining traction. Closed-loop cooling systems, filtration techniques, and recycling methods significantly reduce water consumption and mitigate environmental impacts. Even CNC machining tooling is evolving, with the use of sustainable materials and advanced coatings to minimize tool waste and enhance durability.
Understanding CNC Machining and Tensile Testing
Before discussing the main theme of our article, it's essential to familiarize ourselves with two fundamental concepts: CNC Machining and Tensile Testing. These technical domains, though distinct, are interconnected significantly in modern manufacturing and material science. A CNC machine, known for its precision and automation, shapes components to exact specifications. Meanwhile, tensile tests, a cornerstone of material science, evaluates materials' strength and flexibility under stress. Understanding these processes is key to appreciating their impact on sustainable manufacturing practices, which is the focus of our exploration.
Machining with CNC: An Essential Technology in Modern Manufacturing
Computer Numerical Control represents the foundation of modern manufacturing. This technology involves the precise control of machine tools such as lathes, mills, and routers via computer programming. CNC machining's core advantage lies in its ability to produce complex and precise parts with a high degree of repeatability. In industries such as aerospace, automotive, and medical devices, this is of critical importance.
The process starts with a digital design, typically created using Computer-Aided Design (CAD) software. This design is then converted into a program written in a language understood by CNC machines, usually G-code. The CNC machine interprets this program to execute precise movements, ensuring the cutting tool shapes the material into the specified design.
CNC machining has a wide range of applications. It can work with an array of materials, including metals, plastics, and composites, enabling manufacturers to produce diverse components. CNC's versatility, precision, and efficiency make CNC an indispensable technology in modern manufacturing.
Moreover, the advent of advanced CNC technology has enabled the production of highly complex geometries that would be challenging or impossible to achieve with manual machining. This capability is particularly important in industries where component performance is directly related to its geometry and precision, for example, aerodynamic parts for aircraft or highly complex components for medical devices.
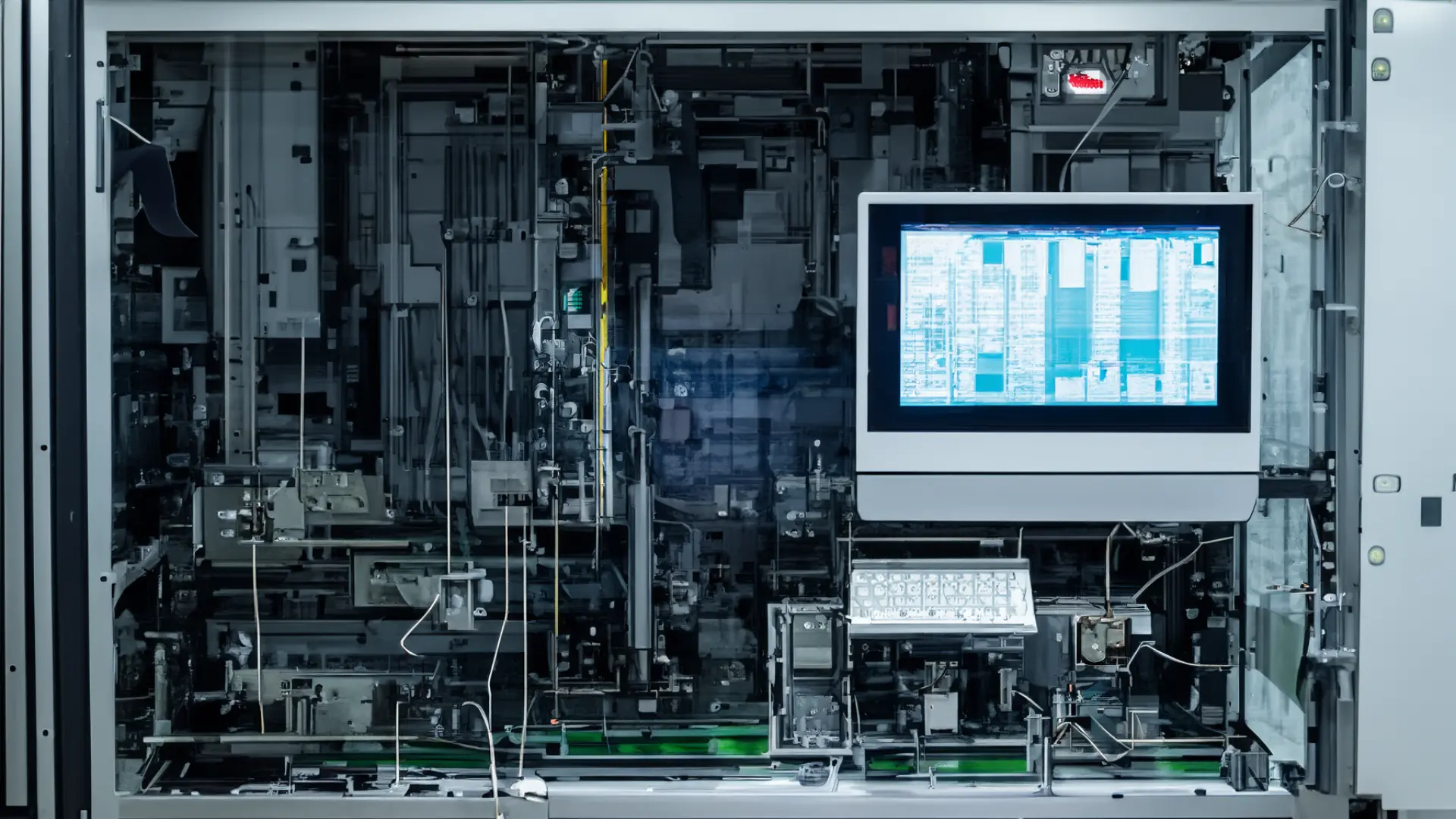
Tensile Testing: A Critical Process in Material Science
A tensile test, performed by a specially designed tensile tester, is a fundamental component of material science that evaluates the ability of a material to resist forces intended to separate it from its surroundings. This process is vital for understanding the mechanical properties of a material, including tensile strength, yield strength, elongation, and modulus of elasticity. These properties are essential in determining how a material will behave under various conditions, especially in applications where the material will be subjected to tensile forces.
In the tensile test, a controlled tension load is applied to the specimen until it fractures. The specimen's response to this load is recorded, and a stress-strain curve is generated, providing valuable data on the material's properties. The peak of the stress-strain curve indicates the material's ultimate tensile strength, while the point at which the material begins to deform permanently marks its yield strength.
In industries like aerospace, automotive, and construction, understanding a material's tensile properties is critical for ensuring final product safety and reliability. For instance, aerospace materials need high tensile strength to withstand flight stresses without adding unnecessary weight. In construction, materials like steel and concrete dictate their suitability for use in structures like bridges and skyscrapers.
Additionally, tensile testing is vital in research and development, where new materials and composites are constantly being developed. Understanding the tensile properties of these new materials will enable researchers to predict how they will perform in real-world applications and tailor them accordingly.
CNC machines are primarily used in the preparation of specimens for tensile testing. A CNC machine ensures that these specimens are made to the precise dimensions and tolerances specified by standards such as ASTM or ISO. A high degree of precision is critical for ensuring the accuracy and reliability of the results of tensile tests, as even the slightest deviation from the specimen geometry can have a significant impact on the test.
CNC machining and testing for tensile strength are interconnected processes vital to material science. The use of CNC machines provides the precision necessary to create accurate test specimens, while tensile testing offers essential insights into material properties. Both processes are indispensable in ensuring the performance, safety, and reliability of materials used in many different industries.
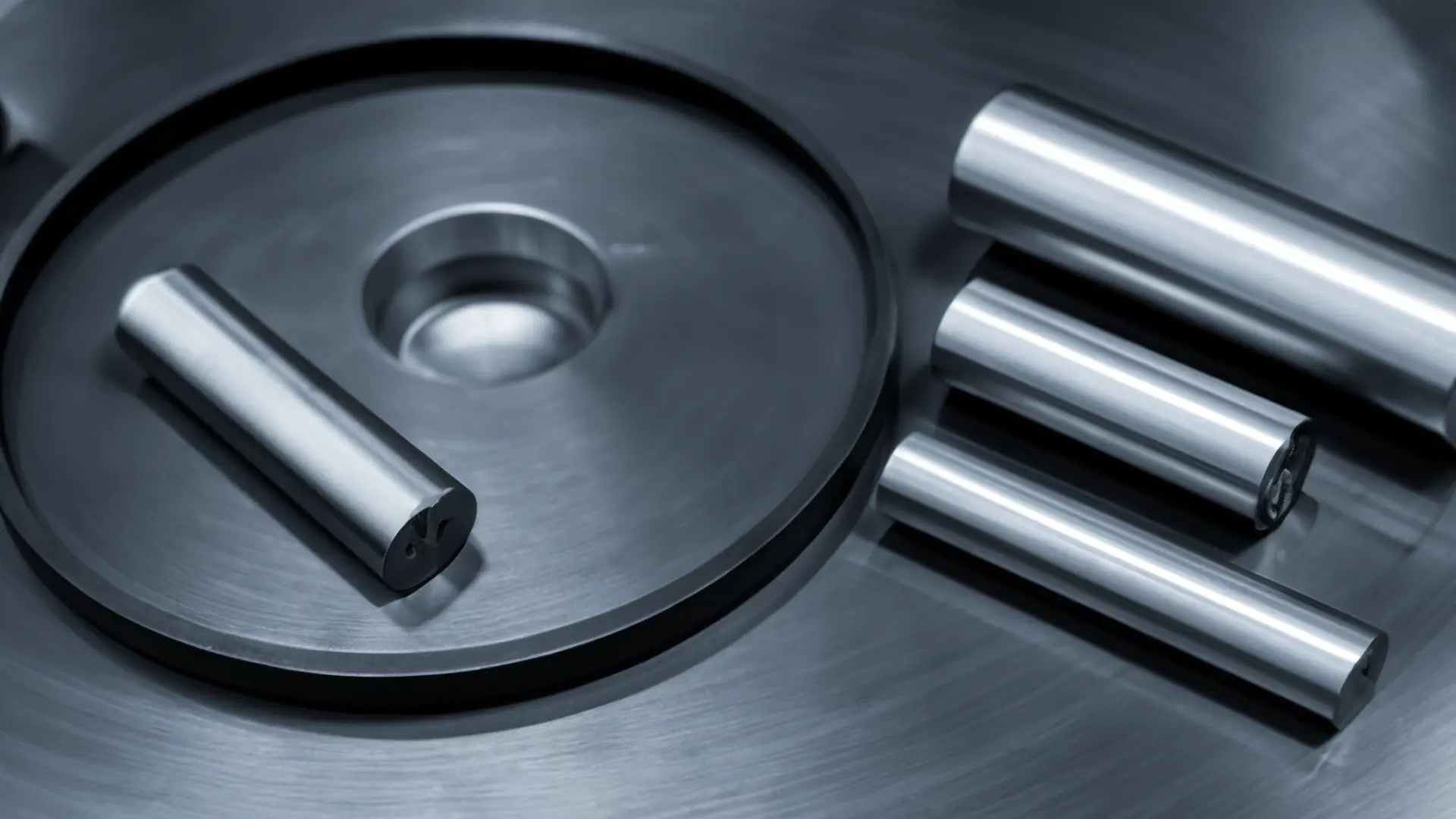
CNC Machining's Role in Tensile Tester Manufacturing
Following the exploration of computer numerical control machining and tensile testing, it becomes apparent how important these processes are to the field of material science. As a matter of fact, the advancements in CNC machining have profoundly influenced the manufacturing of tensile testers, devices that are central to the testing of tensile strength. As a result of this connection, it is possible to manufacture reliable and precise tensile testing equipment, which plays an important role in a variety of industries.
Precision Manufacturing of Tensile Testers: Tensile tester manufacturing demands exceptional precision, which is characteristic of CNC machines. A tensile tester is a complex device consisting of many components, each of which requires exact specifications in order to provide accurate results. CNC machines are ideal for creating intricate parts due to their ability to follow precise programming instructions. In order to ensure accuracy in dimensions, numerical control is critical to the functionality of the tensile tester, ensuring that materials are tested consistently and under controlled conditions.
Material Considerations in Tensile Tester Production: CNC machining plays a significant role in the choice of materials in tensile tester production. The materials used in these testers should possess qualities such as strength, durability, and resistance to wear and tear. The CNC machine process allows manufacturers to choose from a wide range of materials, ranging from metals to advanced composites, for different components of the tensile tester.
Innovations Enhancing Tensile Testing: By integrating advanced technologies such as multi-axis machining and automated quality control procedures into CNC operations, tensile tester quality has been significantly improved. It is possible to produce parts with complex geometries and high precision using these technologies, which are often required by advanced tensile testers. In addition, manufacturing parts with minimal waste is aligned with the goals of sustainability.
Customization and Adaptability: CNC machining enables flexibility in manufacturing, which is essential for producing tensile testers that are customized to specific testing needs. As different materials and testing conditions require different tester designs, CNC technology provides the flexibility to meet these requirements. Due to this flexibility, tensile testers are not only accurate, but also versatile in their application across a wide range of materials and industries.
Ensuring Compliance with Standards: Tensile testers must comply with strict industry standards, such as those set by ASTM and ISO. In order to achieve this compliance, CNC machining ensures that all parts of the tensile tester meet the required standards. In industries such as aerospace, automotive, and construction, that require stringent safety and quality standards, CNC technology ensures that testers are reliable and consistent in their performance.
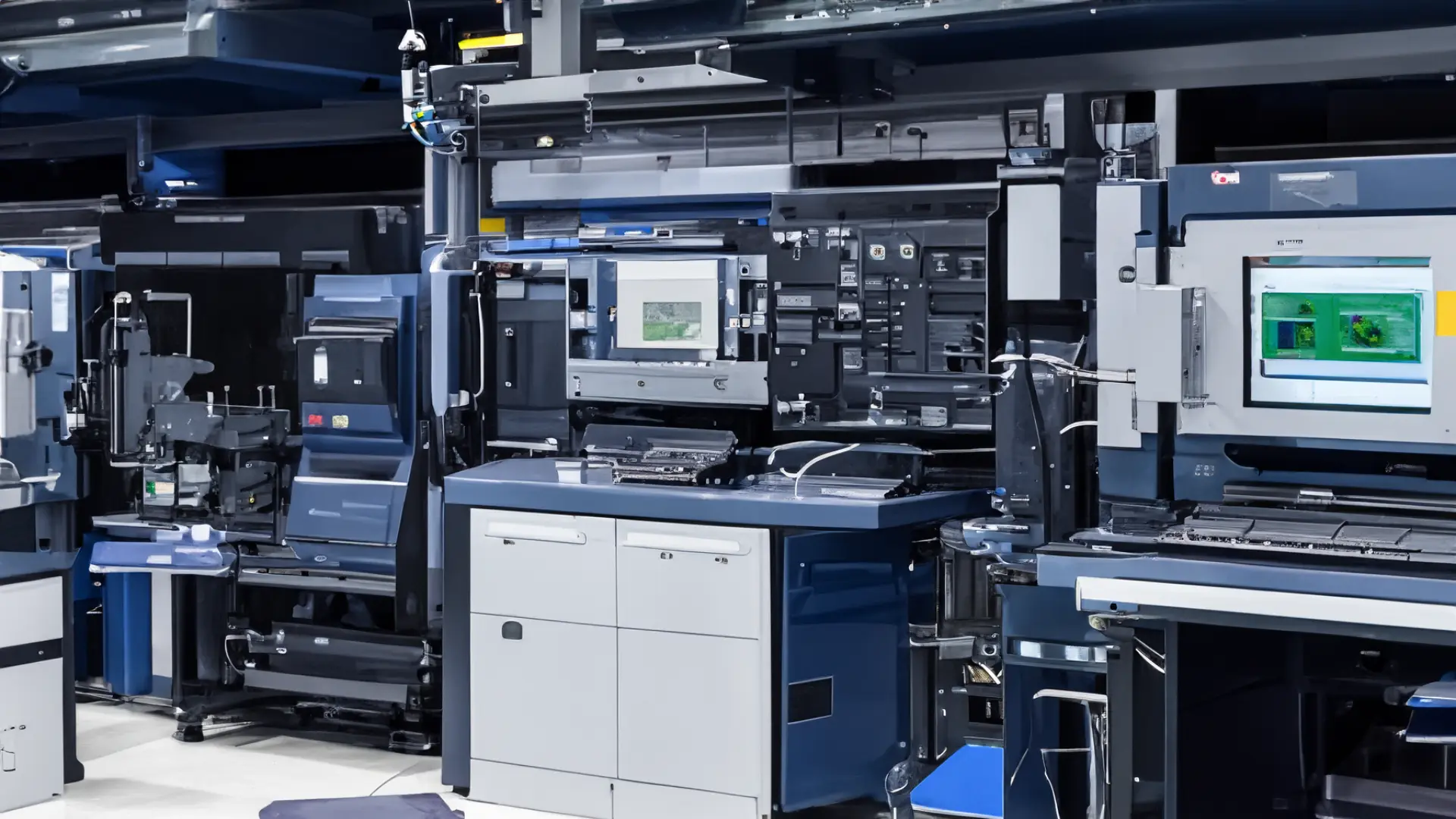
Growth and Innovation in the CNC Machining and Tensile Testing Industries
The CNC industry, an integral part of modern manufacturing, is witnessing significant growth and transformation, fueled by advancements in technology and an increasing demand for precision and efficiency. As of 2023, the CNC market is valued at approximately USD 93.50 billion and is projected to reach USD 136.05 billion by 2028, with a CAGR of 7.79% during the forecast period. This growth is driven by the escalating demand for production efficiency. CNC machines streamline operations, reduce production times, and minimize human error.
CNC industry evolution reflects a broader manufacturing trend toward automation and efficiency. For example, 3D printing integration with CNC machines offers enhanced multi-material capability with minimal resource waste. The automotive sector, in particular, adopts automated manufacturing techniques, contributing significantly to CNC market growth. Moreover, the push towards sustainable energy sources, such as solar and water power, is influencing the market, with CNC machines playing a key role in automating power generation processes.
In terms of employment opportunities, an estimated 56,000 jobs in CNC machining are expected to open by the end of the following year, highlighting the sector's expanding influence and the need for skilled labor. The use of CNC machines has also found critical applications in the medical field, particularly in the manufacturing of medical screws, which demand high precision. Approximately 900 million such screws are needed annually, underscoring CNC technology's significance in this domain. Furthermore, CNC machining's precision is vital in high-risk sectors such as aeronautical engineering, automotive engineering, and military equipment, where consistency in size and function is an essential factor.
On the tensile testing front, the market size for machines for testing tensile strength and tensile testers is forecast to reach $9.421 Billion in 2027, growing at a CAGR of 3.9% from 2020 to 2027. Tensile testing machines, crucial for determining tensile strength and other mechanical properties of materials, are extensively used in a wide range of manufacturing sectors, including metals, paper, pulp, textile, and automotive industries, which we have already mentioned. The rising demand for these machines is driven by the growing need for robust quality control in the manufacturing sectors.
The global market for tensile test machines and tensile testers is influenced by several factors, including rapid industrial growth in various manufacturing sectors and the growing market trend towards automated tensile testing. Strict government policies and quality standards for tensile strength, along with the increasing demand for durability, reliability, and stability of products, are anticipated to further boost the market. North America, particularly the United States and Canada, leads in revenue generation in this market, with the Asia Pacific region, contributing significantly as well.
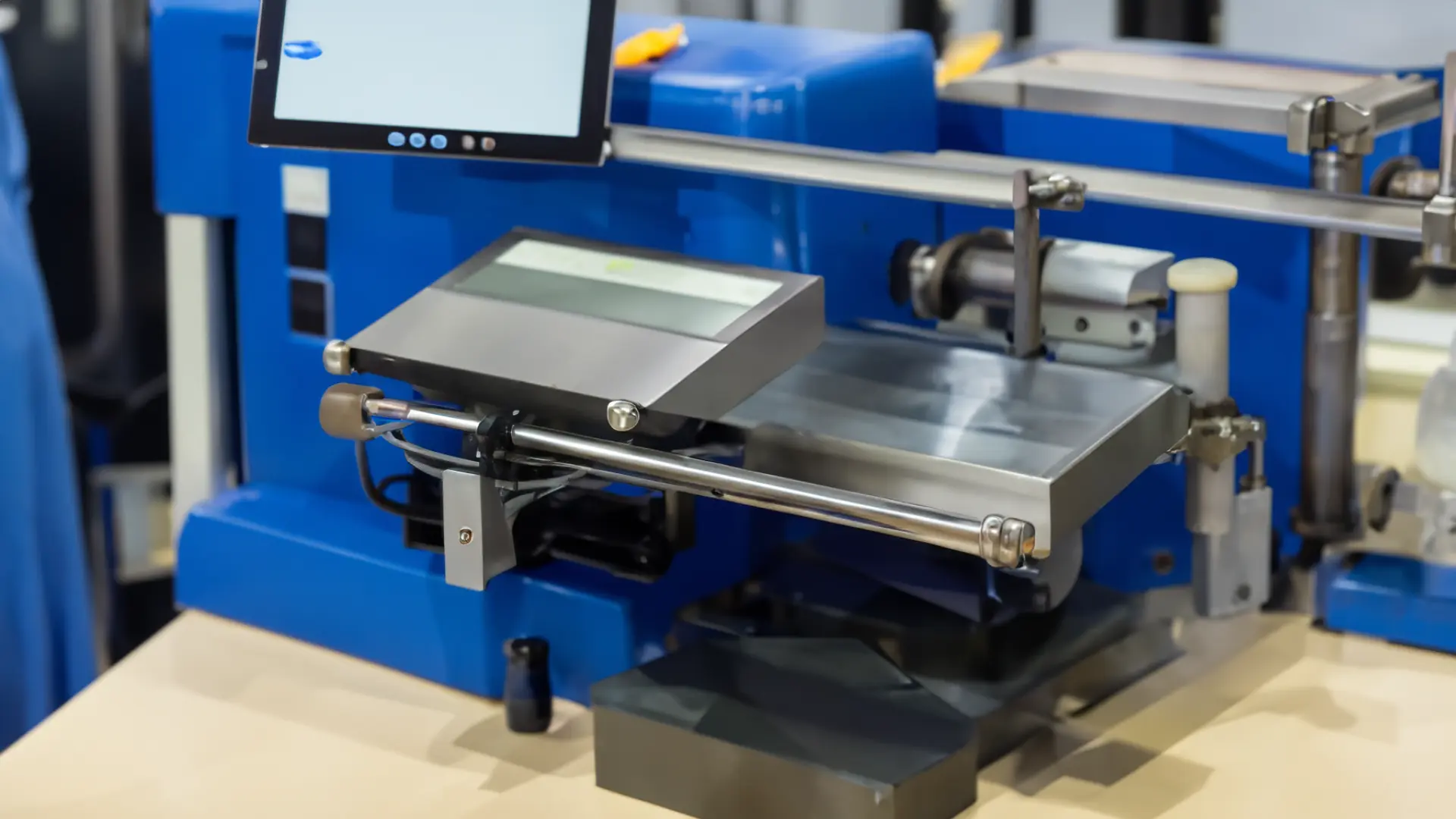
The Importance of Sustainability in Machining with CNC
The environmental impact of traditional CNC machining is multifaceted and substantial. It involves significant energy consumption, extensive water usage, air pollution, and waste production. Specifically, CNC machines require considerable energy, contributing to greenhouse gas emissions. Water, used extensively for cooling and lubrication, strains local resources. Additionally, the CNC process generates waste materials like chips, shavings, and metalworking fluids, which can be environmentally hazardous.
To address these concerns, the industry is adopting sustainable practices. These include using energy-efficient machine tools, opting for green materials and environmentally friendly designs, and implementing recycling programs for waste materials. Moreover, minimizing coolant usage and ensuring proper disposal of used coolants are crucial to preventing environmental contamination. Renewable energy sources, such as solar or wind power, further reduce greenhouse gas emissions and support a more sustainable production cycle.
CNC machining also offers indirect environmental benefits. The ability to send electronic files to factories reduces travel, cutting down on carbon emissions associated with transportation. This aspect of CNC machines contributes to a greener manufacturing process by minimizing material waste and shortening machining time, thereby reducing the carbon footprint of the manufacturing process.
The industry is further evolving with the integration of the Internet of Things (IoT), which automates and enhances communication between machines, leading to higher-quality products and more efficient operations. This technological advancement enables companies to offer services online, such as transmitting CAD files electronically for computer numerical control machining, injection molding services, and rapid machining.
Additionally, computer-aided design services are becoming more affordable, with prototyping companies able to purchase machines at a fraction of the cost in the past. This lower barrier to entry into the CNC machining industry enables outsourcing companies to offer a wide range of services, including prototype manufacturing, which contributes to a more diversified and sustainable manufacturing environment.
While the environmental impact of traditional machining via CNC is significant, the adoption of sustainable practices and technological advancements presents a path toward a greener, more efficient, and cost-effective manufacturing industry. These efforts are vital not only for reducing the ecological footprint but also for meeting the growing demand for environmentally responsible manufacturing processes.

Innovative Technologies and Solutions in Eco-Friendly Sustainable CNC Machining
With technological advancements and an increasing emphasis on environmental responsibility, sustainable innovations in CNC machining are reshaping manufacturing's future towards eco-friendliness:
- Impact of Industry 4.0: Using Industry 4.0 technologies, CNC machines integrate smart technologies and integrated software, leading to more efficient, less energy-intensive operations. This integration with Computer-Aided Manufacturing (CAM) software optimizes manufacturing times and enhances component production quality, all while minimizing environmental impact.
- AI and Machine Learning: The adoption of AI and machine learning in CNC machining facilitates predictive and preventative maintenance methods. This reduces downtime and boosts productivity, ensuring precise machine performance with reduced energy consumption over time.
- Multi-Axis Computational Machining: The rise of multi-axis CNC technology allows complex parts to be machined efficiently and precisely. This approach reduces material waste and energy usage, contributing to eco-friendly manufacturing processes.
- New Materials in CNC Machining: The use of advanced materials such as composite materials (e.g., carbon fiber reinforced polymers), high-temperature alloys, and ceramics enhances the machine's capabilities. These materials, known for their lightweight, strength, and corrosion resistance, are ideal for sustainable applications in industries like aerospace and automotive.
- Sustainability Focus: CNC machining is evolving with a focus on sustainability. This includes the utilization of recycled or biodegradable materials, energy-efficient motors, and systems to recycle coolant and reuse cutting tools, significantly reducing CNC operations' environmental footprint.
- Role of VR and AR: VR and AR technologies in CNC machines contribute to sustainability by providing immersive training simulations and efficient design and prototyping stages. This minimizes resource usage and waste, furthering eco-friendly manufacturing practices.
As a result of these innovations, the CNC manufacturing industry is demonstrating its commitment to staying at the forefront of technology while also prioritizing sustainability and efficiency in the manufacturing process.
Regulatory Frameworks and Industry Standards for Sustainability
Also, it is important to emphasize the importance of regulatory frameworks and industry standards in ensuring sustainability within the fields of tensile testing, tensile testers, and CNC machines. Material and product performance and integrity are maintained by these frameworks and standards. When considering the impact on environmental sustainability and safety, their role is even more important.
Regarding tensile testing, a key standard is ISO 6892-1:2016, part of the broader ISO 6892 suite. This standard unifies European and international methods for testing metallic materials under ambient conditions. It encompasses various metallic forms, such as sheets, plates, wires, bars, sections, rebars, and tubes. The standard guarantees the proper axial alignment of specimens during testing, which is critical to minimize bending and accurately measure the material's tensile strength until its failure point.
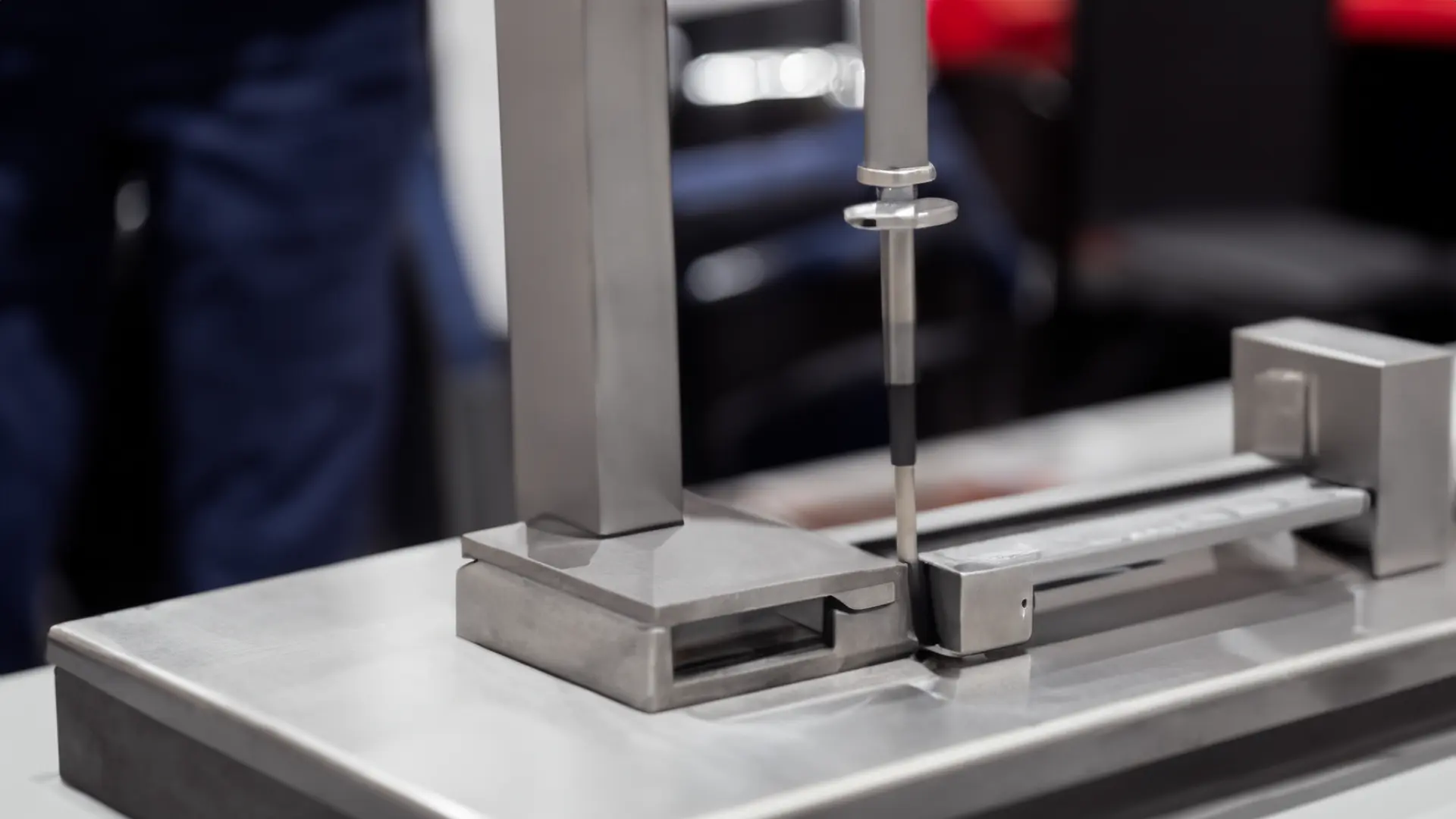
ISO 6892-1:2016 was updated to include distinct methods such as Method A1 (Closed-Loop Strain Control) and Method A2 (Constant Crosshead Separation Rate). This addition provides more precise control and clearer guidance for test laboratories transitioning from traditional methods. This standard offers reduced variation and measurement uncertainty in test rates, ensures more repeatable and comparable results, and facilitates considerable time savings. This standard is indispensable for professionals across numerous industries, including structural engineering and aerospace, as it helps define the mechanical properties of metallic materials at room temperature.
CNC machining has a multifaceted environmental impact. CNC machines, essential for creating tensile test specimens, demand substantial energy and water resources, particularly for cooling and lubrication. Additionally, the process generates waste materials, including chips, shavings, and potentially hazardous metalworking fluids. To deal with these environmental challenges, manufacturers can adopt several sustainable practices. These include employing energy-efficient machine tools, opting for eco-friendly materials, implementing recycling and waste reduction programs, minimizing coolant usage, and using renewable energy sources. Moreover, integrating additive manufacturing techniques with traditional machining can further enhance sustainability. These practices lead to reduced environmental impacts, lower operational costs, and improved public perception. It also ensures compliance with governmental regulations and supports a circular economy by promoting the reuse and recycling of materials.
In the industrial manufacturing sector, tensile testing is a cornerstone of product quality and safety. Recent statistics from the International Organization for Standardization (ISO) highlight its importance: over 70% of manufacturing metals have been subjected to tensile tests to verify compliance with ISO standards. This widespread application underscores the reliability of products made from these metals and reflects the industry's ongoing demand for tensile strength testing.
The Integral Role of Tensile Testers in Sustainable Manufacturing
Following our discussion of regulatory frameworks and industry standards, it's important to look more closely at the specific role of the tensile tester in sustainable manufacturing practices. This instrument, vital in the material testing process, is not only an example of precision and reliability but also sustainable innovation.
Eco-Efficiency of Tensile Testers
The efficiency of a tensile tester in the age of sustainable manufacturing goes beyond its technical capabilities to encompass its environmental impacts. The manufacturers of these devices are increasingly focused on reducing energy consumption and waste. Modern tensile testers are designed with energy-efficient motors and systems that consume less power. The advancement not only reduces operational costs but also reduces materials testing carbon footprint.
Materials and Design Sustainability
Furthermore, the construction materials used in tensile testers are undergoing a green transformation. In their design, manufacturers are using recycled or recyclable materials, which ensures that the testers are not only tools for quality assurance but also products that adhere to environmental guidelines. Efforts are being made to refine the design of these testers in order to maximize longevity and reduce the need for frequent replacements, which contributes to the sustainability of these devices.
The Future of Tensile Testers
In the future, the importance of tensile testers in sustainable manufacturing is expected to increase. As industries continue to emphasize environmentally friendly practices, the demand for tensile testers aligned with these principles will increase. As these devices progress, they will likely include advancements in renewable energy integration, waste reduction techniques, and enhanced recyclability, ensuring that they remain at the forefront of sustainable manufacturing practices.
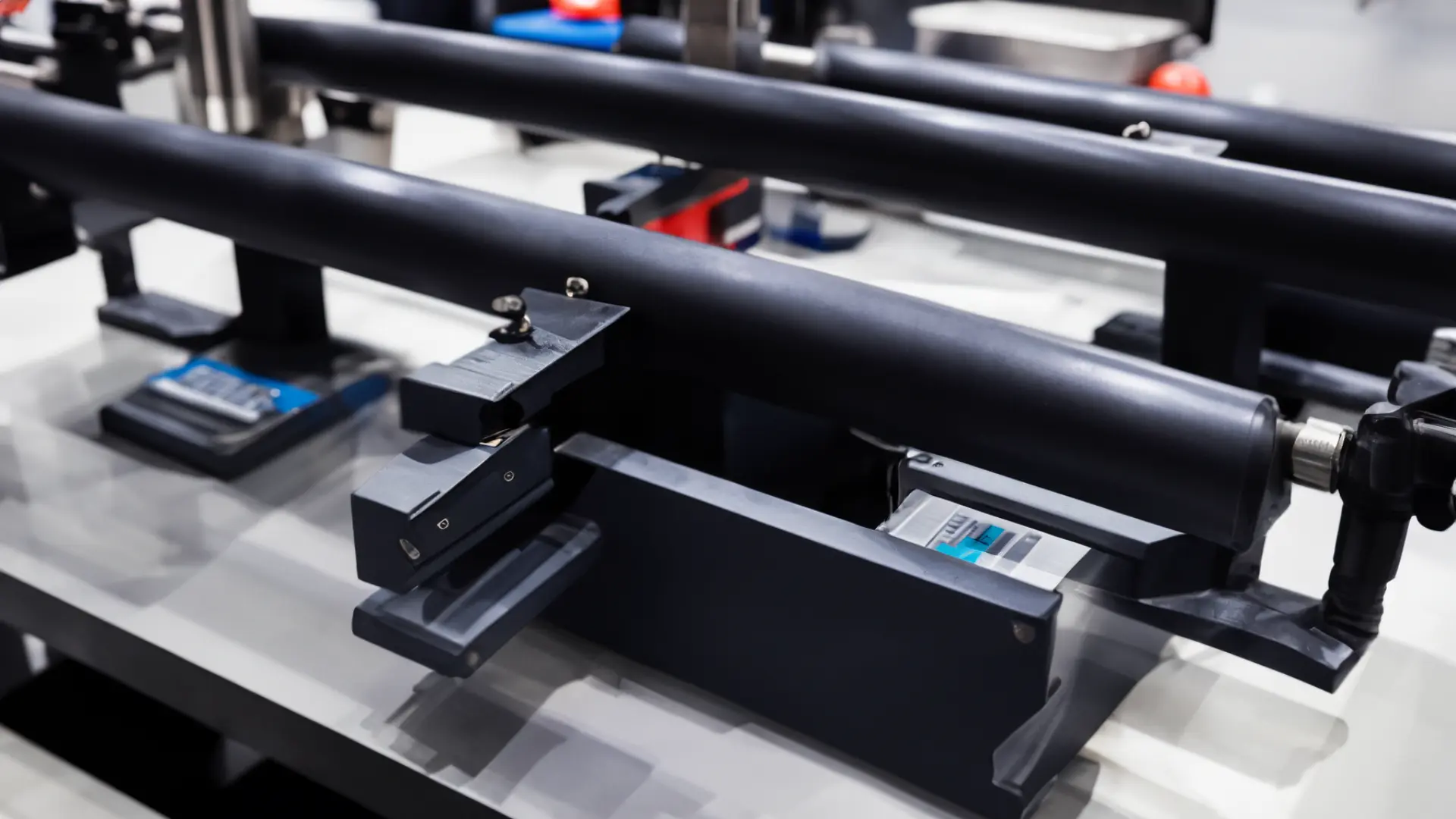
Sustainability in Tensile Tester Manufacturing Through CNC Innovation
To conclude, the progress toward sustainability in the manufacturing sector, particularly in the production of tensile testers, represents a significant step forward for modern manufacturing methods. A CNC machine's role in this transition cannot be overstated. As we have seen, computer numerical control machining is not only about precision and efficiency but also about adapting to a world that increasingly demands environmentally conscious manufacturing processes.
Advancements in CNC technology, particularly those driven by Industry 4.0, AI, and machine learning, have redefined how a tensile tester is manufactured. These innovations have made it possible to produce tensile testing equipment that is not only of the highest quality but also manufactured in a way that minimizes environmental impact. By reducing material waste, optimizing energy usage, and using sustainable materials, CNC manufacturing sets a high standard for eco-friendly manufacturing in the tensile testing industry.
Furthermore, stringent regulatory frameworks and industry standards, such as ISO 6892-1:2016, ensure that the tensile tester meets and exceeds the required performance and safety benchmarks. This commitment to quality, coupled with a focus on sustainability, makes the modern tensile tester an example of responsible manufacturing.
The integration of sustainable practices in the production of a tensile tester through the use of CNC machines reflects a broader shift in the manufacturing sector. It is a shift that acknowledges the need for a balance between industrial advancement and environmental stewardship. This balance is crucial in a world where manufacturing implications extend far beyond the factory floor, impacting global ecosystems and our planet's future.
Tensile tester demand continues to grow, driven by the need for reliable and precise material testing in numerous industries. It will remain important to consider how they are manufactured. The industry's ongoing efforts to enhance tensile tester production sustainability serve as a model for other sectors. It demonstrates that it is possible to embrace technological advancements while maintaining environmental sustainability.
Overall, the sustainable manufacturing of a tensile tester through advanced computer numerical control is an indication as to the potential for balancing industrial progress with ecological responsibility. As we continue to navigate the challenges of a changing industrial setting, the strides made in the eco-friendly production of tensile testers will certainly inspire and inform future efforts across the manufacturing sector. The path towards a more sustainable future in tensile tester manufacturing is not just a goal—it is a necessity, one that will shape the industry for years to come.