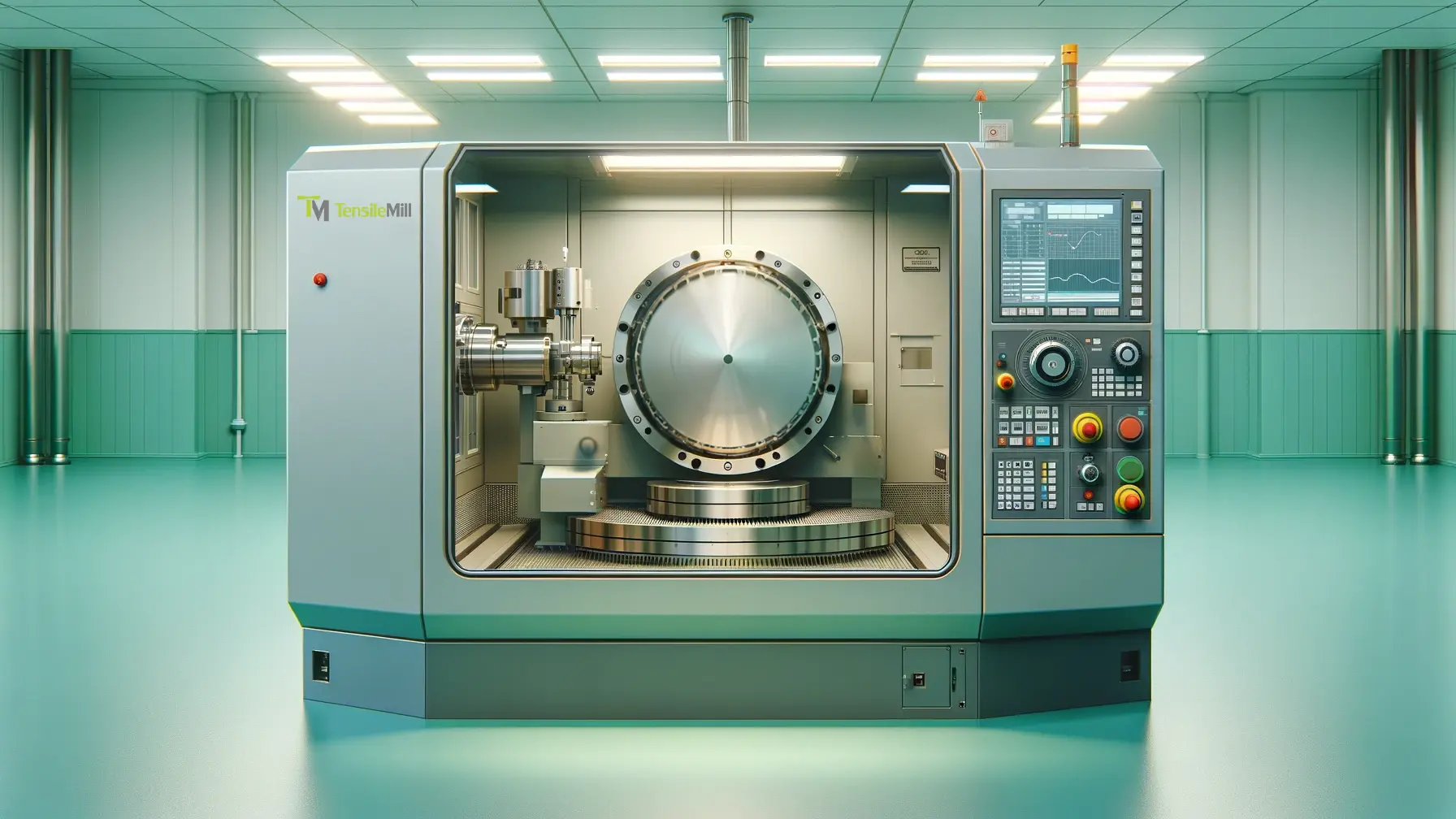
Preparing tensile specimens is known to be a complex process requiring specialized tools and equipment in the material testing industry. CNC (Computer Numerical Control) machines are essential tools in this process, designed to produce commonly prepared cube-shaped pieces of material made of specially treated components. Tensile samples will then be produced from these pieces of material. Most of the materials used for these samples have different hardness levels, from soft to hard substances. While soft materials like plastics or medium metals can be processed using CNC machines, they all require different configurations and instructions.
However, what about extremely hard materials, such as robust metal alloys or titanium? Can these materials be effectively processed by standard CNC machines, which are typically used for less tough materials? The purpose of this blog is to explore this question. We will discuss the preparation of tough titanium materials, the preparation of square and irregular starting blanks, and the creation of small and large threads on tough materials ranging from M12 to M20. We will also highlight the major advantages of full automation when it comes to this process.
The Preparation of Tough Titanium Materials
Titanium is susceptible to mechanical deformation during cutting, grinding, and polishing. To prepare specimens accurately and reliably you need specific techniques and equipment. Using regular aluminum oxide cut-off wheels when machining or cutting titanium, for example, may result in long chips and heat damage. Instead, silicon carbide cut-off wheels are recommended for sectioning titanium.
In laboratories that analyze large samples such as ingots, billets, and slabs, titanium is often processed unmounted. However, mounting is essential for smaller parts, such as wire and fasteners, to simplify preparation and ensure accuracy. Cold mounting with slow-curing epoxy or hot compression mounting with phenolic resin is recommended for smaller parts.
Furthermore, due to titanium's extreme ductility, traditional diamond polishing can cause mechanical deformation to the surface in the form of scratches and smearing, making it difficult to remove. To avoid these problems, hydrogen peroxide and colloidal silica are recommended as a chemical-mechanical polish. This method consistently delivers excellent and reproducible titanium and tough alloy results.
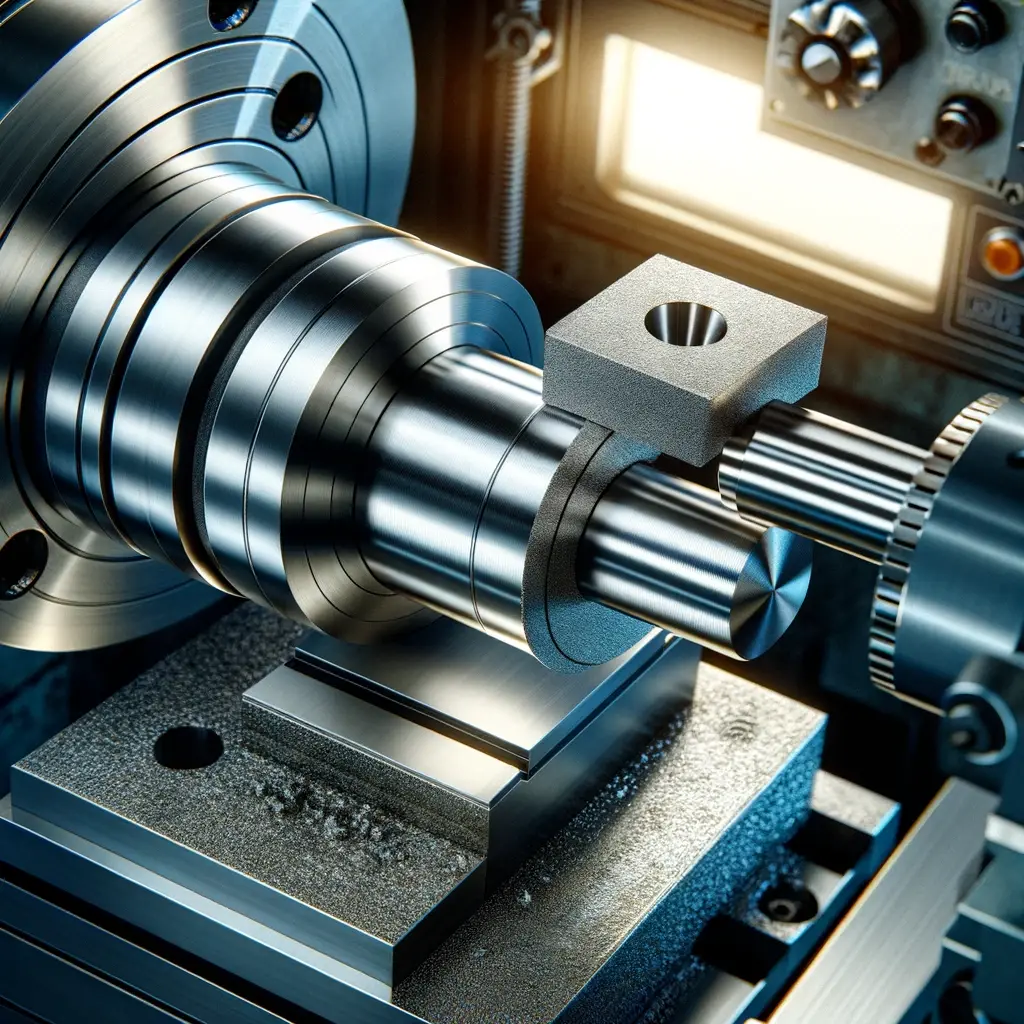
What Type of Equipment Can Handle Titanium Specimens?
While the majority of tensile specimen preparation equipment typically suitable for soft and medium materials can be used for making titanium samples, keep in mind that if a machine was primarily designed for less tough materials, it might damage titanium specimens without precisely adjusted parameters and the right additional equipment, like specific cutters. Therefore, when working with titanium or other extremely tough alloys, you must use machines specifically intended for hard materials.
While talking about titanium or other hard material tensile specimen preparation, we must mention TensileMill CNC's TensileTurn CNC - Industrial Upgrade for round sample preparation. For industrial-grade high-speed machining, this machine has a granite frame and ballscrews, which provide a robust and shock-absorbing foundation. A stainless steel enclosure, a 2 HP (1.5kW) motor running 4000 RPM, and an 8-position turret with 1/2" shank OD tools illustrate its advanced capabilities. Four boring tool holders with 3/4" shanks are included in the machine, and FANUC Bis 0.5 Servos are used to automate center drilling. Using a touchscreen interface, you can easily enter custom dimensions or select common tensile sizes from a library of standards (ASTM, ISO, DIN, etc.). It can handle specimens up to 5 inches in diameter and up to 8 inches in length. Therefore, it is an excellent choice for achieving the highest quality in specimen preparation, even for operators with limited experience.
Preparing Square and Irregular Starting Blank Stock
It takes a meticulous process to prepare square and irregular starting blank stock for tensile testing. The preparation process usually begins with selecting the appropriate blank stock material, which must match the material's properties and testing parameters. Depending on testing standards like ASTM, ISO, or DIN, the blank stock is typically machined into a standardized shape, such as a dog bone or cylinder. To achieve the specific dimensions and geometry needed for tensile testing, this shaping process requires precise machining.
With advanced CNC machining techniques, the blank stock can be precisely and efficiently cut, shaped, and finished into the desired specimen shape. Machines such as CNCs are crucial when dealing with hard materials such as titanium or other alloys since they ensure consistent quality. Tensile testing accuracy depends directly on this preparation. Any deviation from the required dimensions or surface finish can significantly affect the material's behavior under stress and lead to inaccurate testing results.
Creating Small and Large Threads for Tough Material
The threading of tough materials, particularly in sizes M12 to M20, is essential in sectors where threaded components need to be durable and precise. Threaded parts must endure significant stress and wear in industries such as aerospace, automotive, and heavy machinery.
Due to their hardness and resistance to abrasion, hard materials like steel and titanium require advanced threading techniques. It is recommended to use CNC machining for sizes M12 to M20. With CNC technology, these thread sizes can be produced precisely, guaranteeing that each thread maintains its integrity under operational stress while meeting tight standards.
Thread milling and tapping are alternative threading methods. For large or uniquely shaped workpieces, thread milling offers flexibility in thread design and placement. Meanwhile, tapping ensures consistency in thread depth and pitch by creating internal threads within pre-drilled holes.
TensileMill CNC specializes in providing tools for threading tough materials and titanium in the M12 to M20 range. You can request a quote for the threading you need by following the link.
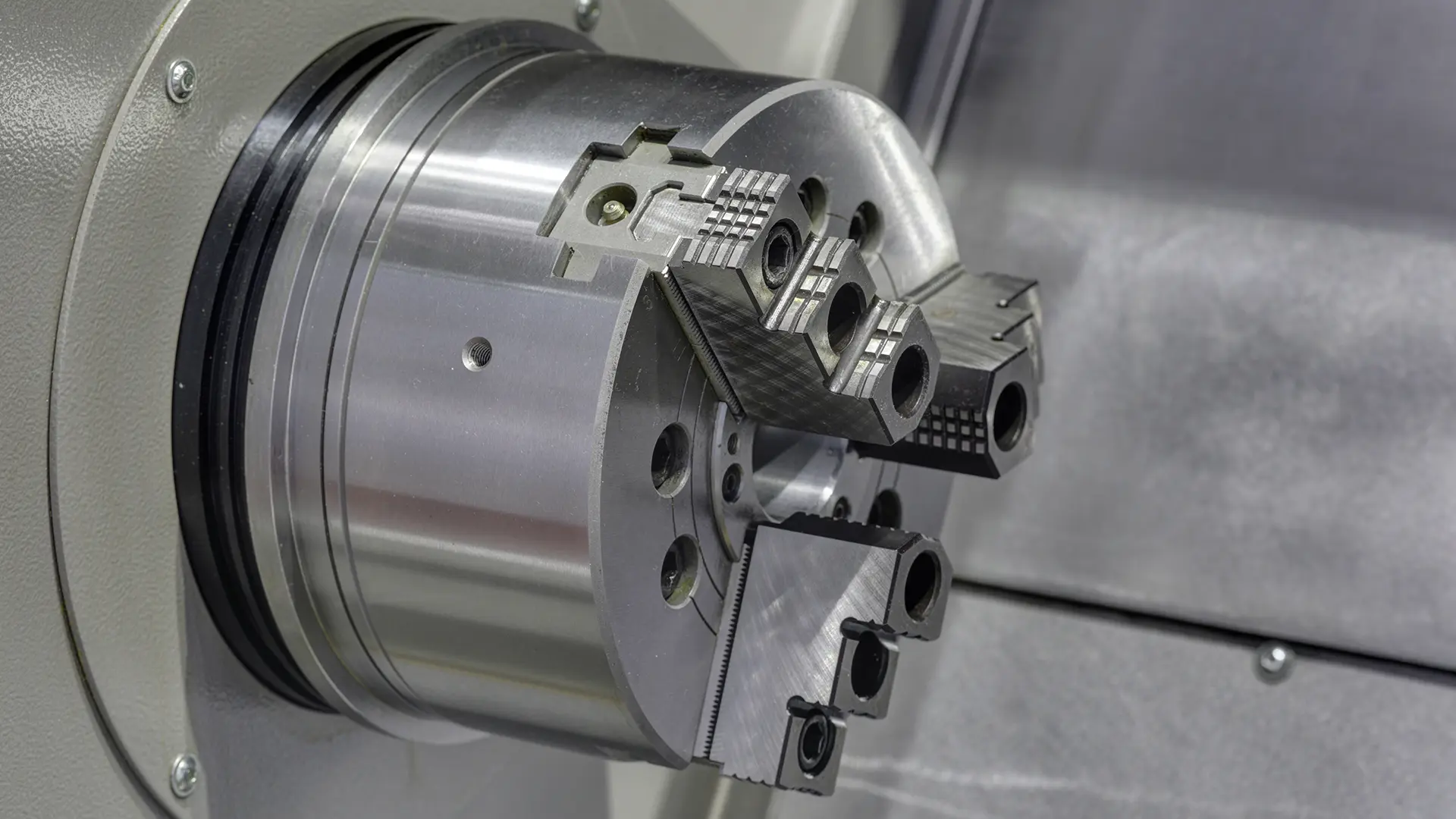
Advantages of Full Automation in CNC Machining
For material testing and sample preparation, CNC machining with full automation, including center drilling, roughing, threading, and parting, offers significant advantages. Manufacturing benefits from this kind of automation on multiple levels, including operational, financial, and business aspects. Let's look at some of them closely:
- Operational Efficiency: Automation dramatically improves manufacturing key performance indicators (KPIs), resulting in better operational performance. Automated CNC machines require less human intervention, even during off-hours, resulting in higher productivity rates. By automating set-up times and standardizing part loading sequences, machines can operate continuously and error-free, reducing scrap and increasing customer satisfaction.
- Increased Capacity: Manufacturing operations can be doubled in size by automating within the same shop floor. As CNC machines get more automated, their production rate shoots up 2-3 times, especially when working on titanium or other tough materials. As a result, the process becomes more reproducible, error reducing and output increasing.
- Faster and More Reliable Lead Times: The automation of processes ensures a more reliable and stable lead time. To maintain consistent output, intelligent automation systems predict capacity for upcoming batches and adjust production accordingly.
- Data-Driven Process Development: Automation allows the collection of production data, crucial for monitoring and improving key performance indicators like Overall Equipment Effectiveness (OEE).
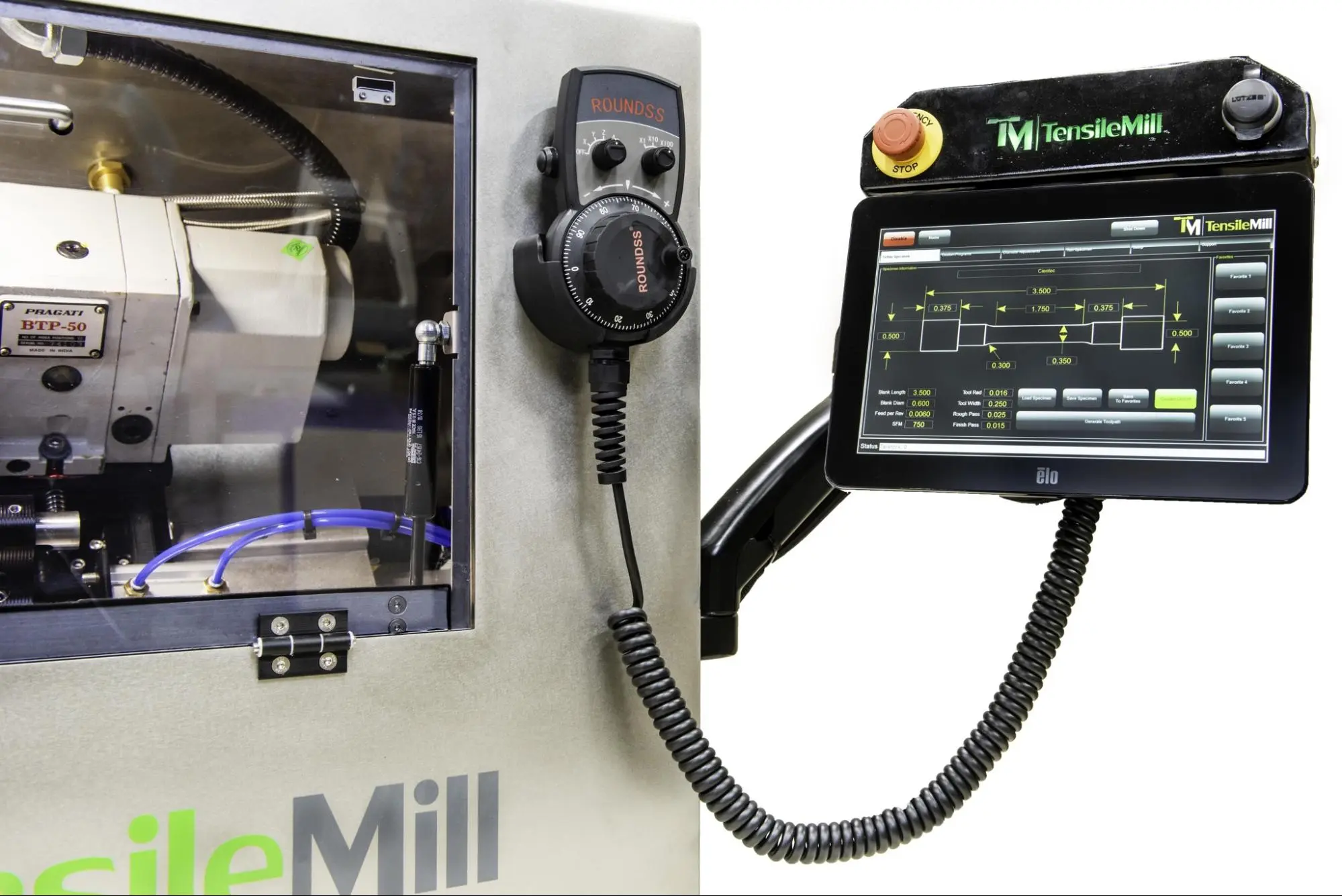
Taking these advantages into account, the TensileTurn CNC - Industrial Upgrade is a model of such exemplary automation. A tough material and complex task like center drilling automation can be handled easily with its precision, repeatability, and efficiency. With this machine, you can prepare tensile specimens from a large variety of materials. This includes those with challenging thread sizes from 12 to 20 mm, which we discussed earlier.
Revolutionizing Tensile Testing with CNC Technology
Technology advancements have revolutionized material science and mechanical testing, especially tensile testing sample preparation. Efficiency and precision increase significantly when switching from manual to CNC machining. Traditionally, tensile specimens were prepared by hand by cutting, shaping, and finishing to achieve precise dimensions.
As a result, there has been a major change in the field due to CNC machining. With remarkable speed and precision, operators can insert a blank stock into a machine and produce a tough, threaded specimen ready for testing. As a result, preparation time is greatly reduced, human error is minimized, and specimens are uniformly prepared for testing. Construction, aerospace, and automotive industries require high-precision material properties evaluation, so such consistency is crucial. The development of technology has led to significant time and cost savings in laboratories and manufacturing facilities. Compared to manual methods, CNC machining can reduce sample preparation time by up to 60%.
It is our goal at TensileMill CNC Inc. to lead the way in tensile testing technology. Our product line extends beyond the acclaimed TensileTurn CNC model and includes a wide array of precision equipment designed for many industries. With force capacities ranging from 1kN to a formidable 3000kN, our tensile testing machines are renowned for their precision and user-friendliness.
Every machine we offer is designed with meticulous attention to detail, ensuring that it not only meets but exceeds the expectations of accuracy and reliability. A comfortable and efficient testing experience is provided by the advanced controls and automation of our equipment. Visit our page about tensile testing equipment to learn more about our full range of tensile testing solutions.
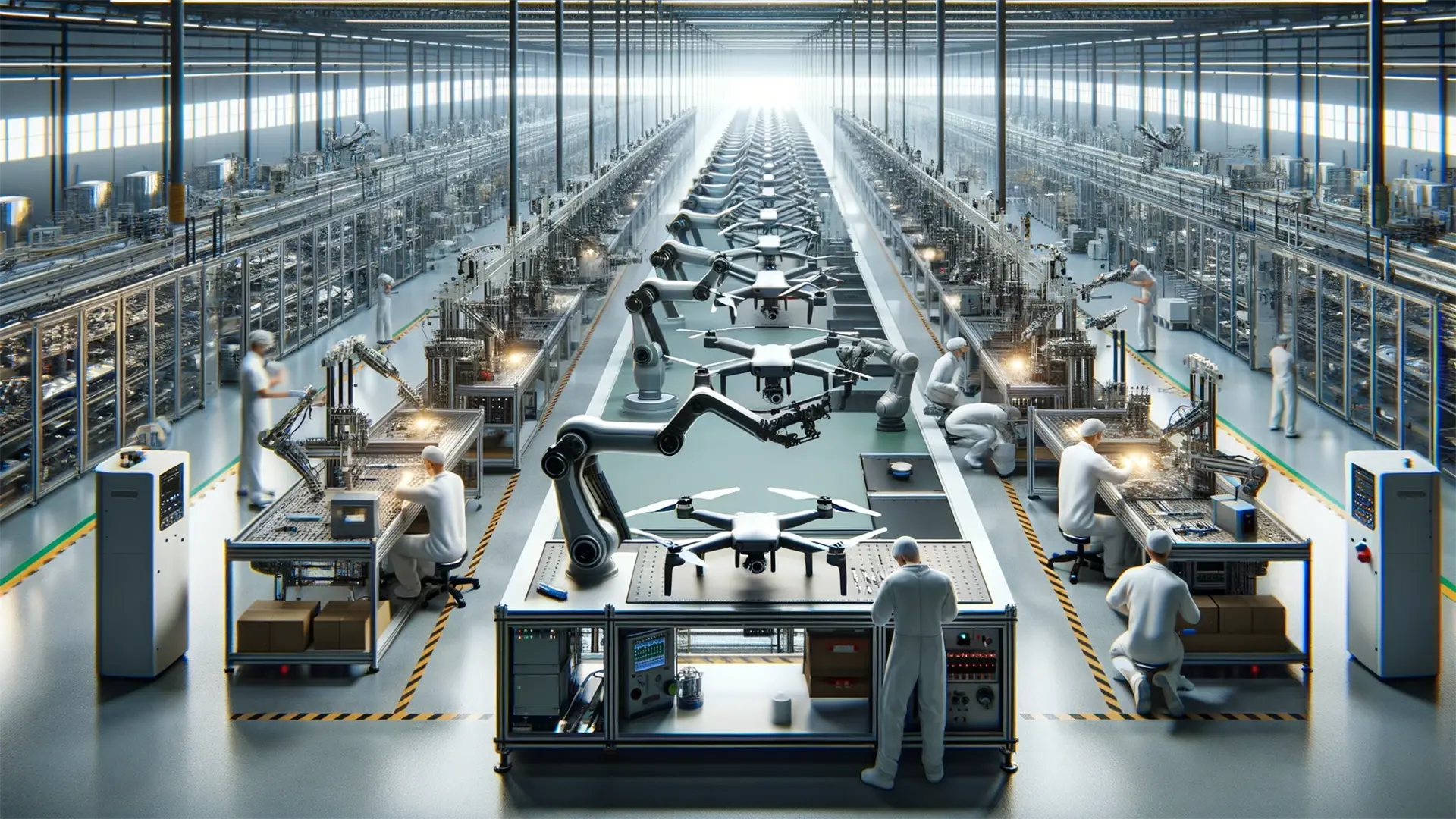
Who Can Benefit from CNC Specimen Preparation Equipment?
Tensile specimen preparation, especially for tough materials like titanium and robust alloys, as mentioned above, requires advanced equipment. For tensile specimens, soft and medium materials require different machining configurations than harder materials. Due to its high ductility and narrow machinability band, titanium demands specific cutting speeds and feed rates to prevent work hardening and tool damage.
Titanium has a poor thermal conductivity, which traps heat during machining. Consequently, it is necessary to use machines with high-performance capabilities, able to handle extreme cutting forces, and equipped with features such as coolant-fed cutting tools and filtration systems. It is therefore necessary to use CNC machines specifically designed for hard materials to ensure precise and efficient specimen preparation.
Titanium alloy producers and processors, such as NIPPON STEEL CORPORATION, and TIMET (part of Precision Castparts Corp.) would greatly benefit from integrating machines such as TensileTurn CNC - Industrial Upgrade into their processes. When working with titanium alloys, the TensileTurn CNC, is designed specifically to handle such tough materials. Compared with more generalized equipment, this targeted design approach ensures superior outcomes.
The Impact of Tensile Testing Among Key Industries
Many industries rely on tensile testing, each with its own set of requirements and needs. Using this testing method is vital for determining material properties under tension. The following are 5 key industries that heavily rely on tensile testing and must have advanced equipment to perform the test effectively:
Aerospace Industry
Due to the extreme conditions encountered during flight, the aerospace industry is one of the most demanding sectors for material testing. Materials used in critical components like aircraft wings, bolts, and engine parts must be tested for tensile strength. The A380, for example, contains millions of parts from numerous countries, illustrating the immense scale of this problem. To ensure aircraft safety and integrity, all parts must withstand varied pressures, temperature gradients, and mechanical stresses.
Medical Devices Industry
Throughout this industry, tensile testing is fundamental to the process of confirming the safety and efficacy of equipment, implants, and prosthetics used in clinical settings. Due to their use in critical medical procedures, these devices need to be highly precise and durable. The tensile testing guarantees patient safety and the effectiveness of medical treatments by checking that these medical products can withstand the forces encountered during their use.
Construction Industry
Construction industries also rely heavily on tensile testing to verify that materials like beams, columns, and reinforcing bars maintain structural stability. Glass, stainless steel, and structural steel are among the materials used in the Burj Khalifa, for example. Tests of tensile strength are critical for ensuring that these materials can withstand both heavy loads and environmental factors, ensuring their safety and longevity.
Electronics Industry
In this sector, tensile testing is crucial for assessing wires, circuit boards, and connectors' durability and resilience. Despite mechanical stresses like bending and stretching, these elements are essential to the functionality of electronic devices. Tests of tensile strength make sure that electronics materials can withstand physical demands, contributing to their reliability and longevity.
Automotive Industry
The automotive industry relies on tensile testing to verify the strength and resilience of materials like alloys or even titanium used in axles, drive shafts, and structural frames. As used in the Tesla Model S chassis, high-strength aluminum alloys are tested to ensure that they can withstand extreme conditions like torques and collisions. Therefore, tensile testing is necessary for confirming material durability, ultimately ensuring passenger safety and vehicle integrity under different driving conditions.
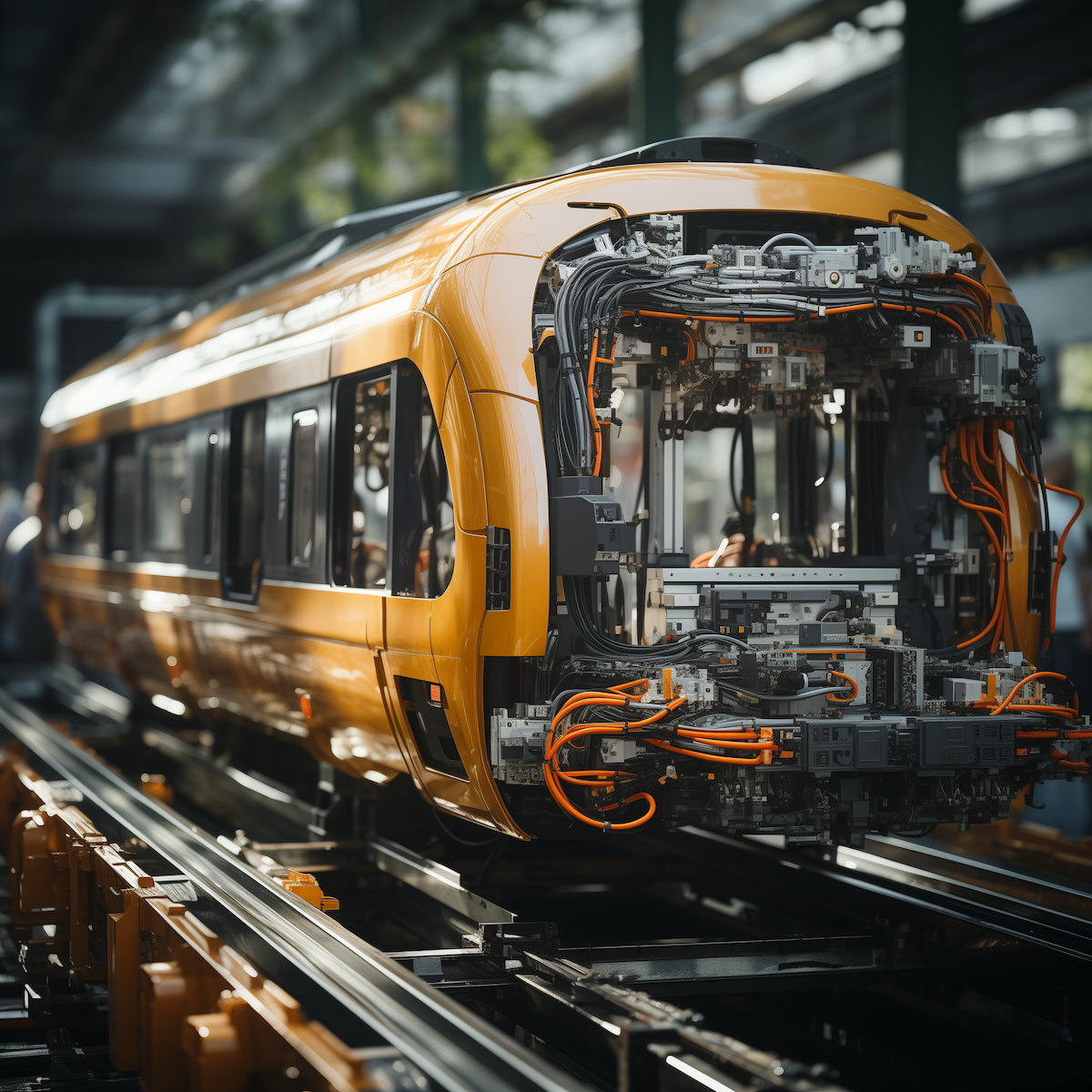
The High-Tech Equipment and Quality Services of TensileMill CNC
The need for top-notch testing equipment is inescapable in a world based on precision and reliability. The right tools are key, whether they are CNC machines for specimen preparation or advanced tensile testing machines. From softer to harder materials like titanium and other tough alloys, this is true for processing a broad range of materials. It is directly related to superior results to choose superior equipment.
Within our range of tools at TensileMill, the CNC MINI for flat specimen preparation and the TensileTurn CNC Sample Preparation Machine for round specimens show our commitment to helping our customers achieve their goals. Precision and ease of use make the CNC MINI machine a popular specimen preparation machine, while the robust and high-speed TensileTurn CNC machine makes it ideal for many types of specimen preparation applications.
Additionally, we offer tensile testing equipment to complement these preparation machines. For instance, our Servo Hydraulic Universal Testing Systems (600kN / 1000kN) are equipped to handle a variety of tests with exceptional accuracy. By combining these systems with our specimen preparation machines like the CNC MINI and the TensileTurn CNC model, we can ensure a smooth, efficient testing process, meeting the rigorous demands of the different industries. Together, they form an ideal combination for testing laboratories, providing the highest quality results in every test conducted.
Let us know if you're interested in enhancing your business with our equipment or services by contacting us directly or requesting an online quote.