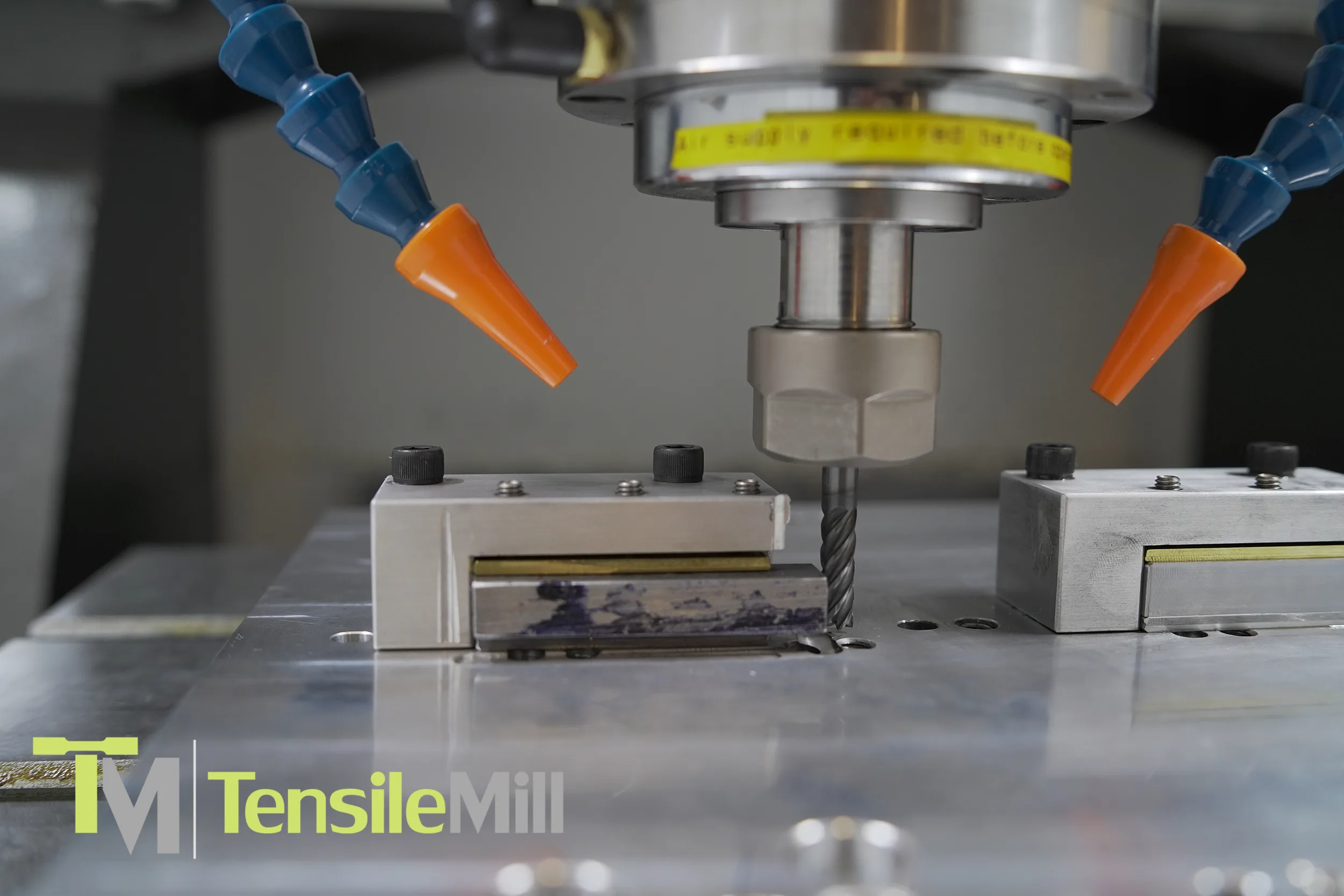
The preparation of samples is a fundamental part of material testing, making certain that specimens meet the specific standards required for accurate testing. Whether preparing tensile samples for testing material elasticity and strength or crafting impact specimens to measure fracture resistance, each sample must be extremely carefully prepared to achieve valid results. Historically, this preparation involved considerable manual effort, which could lead to inconsistencies, variations, and potential human errors. However, advancements in CNC technology have transformed this field, introducing precision and automation that significantly elevate sample preparation quality.

CNC technology for sample preparation refers to the use of automated, computer-controlled machines to accurately shape, polish, and finalize test specimens. In material testing, CNC (Computer Numerical Control) machines enable precise, efficient, and repeatable processes, reducing manual labor and minimizing inconsistencies among samples. Today, this technology is widely used in preparing various types of test specimens, including those for tensile, impact, hardness, fatigue, and flexural testing, as well as for microstructural analysis and corrosion resistance assessments.
CNC Automation's Role and Benefits in Sample Preparation
CNC automation in sample preparation offers unprecedented precision, increasing quality and reliability for various material testing applications. By transitioning from labor-intensive manual processes to automated, computer-controlled systems, CNC technology enables faster, more accurate, and repeatable sample preparation. Let us look at a few of the main benefits of CNC tech in sample preparation:
Precision and Consistency Across Samples
CNC technology shapes and finishes samples with remarkable accuracy, meeting specifications like those required for tensile, impact, and hardness tests. For instance, CNC machines produce uniform cross-sectional areas, achieving tolerances within microns. This precision is a necessity to comply with ASTM E8, where even slight deviations can impact test outcomes.
Reduced Variability and Human Error
Manual preparation often leads to inconsistencies due to human error or technique variations. CNC machines eliminate these issues, creating uniformly prepared samples and delivering more trustworthy results. For impact testing, where an improperly shaped notch can alter test results, CNC systems guarantee accurate, repeatable notches, and comply perfectly with ASTM E23 specifications.
Time Efficiency and Productivity Gains
CNC machines significantly reduce preparation time, completing intricate processes like polishing and notching in minutes. In high-volume facilities, such as aerospace facilities, this efficiency supports the rapid processing of hundreds of samples daily. While manual sample polishing might take half an hour, CNC technology completes the task in under ten minutes, improving productivity by over 60%.
Adaptability to Various Sample Types
CNC technology is highly flexible, handling diverse specimen types from tensile and flexural samples to microstructural analysis specimens. This adaptability enables testing facilities to switch between standards, such as ASTM and ISO, without difficulty. A single CNC machine can transition from preparing tensile samples to compression samples with minimal adjustments, meeting different testing needs easily.
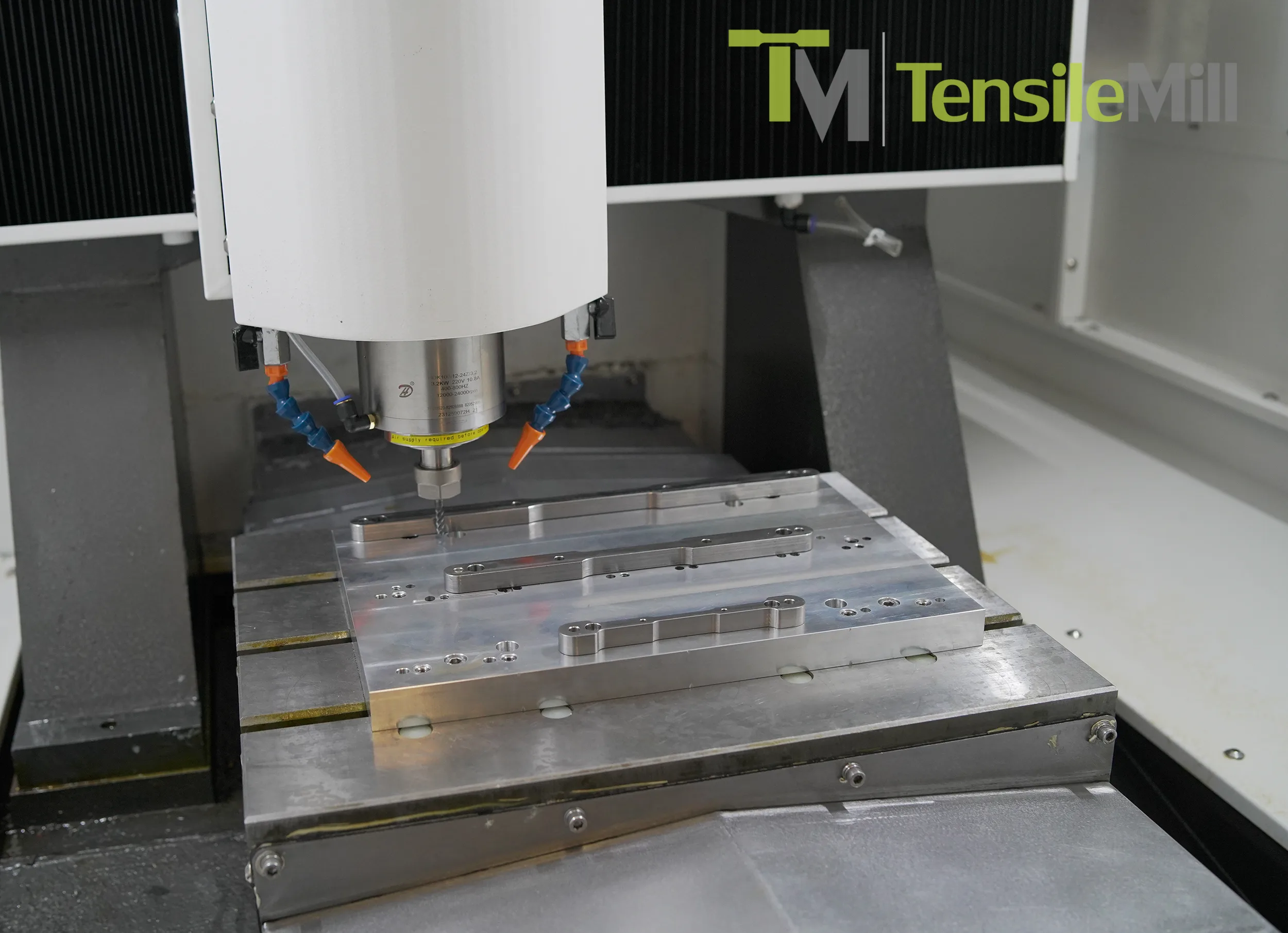
CNC Technology Applications in Diverse Industries
CNC technology has become increasingly important in a broad range of industries. Below, we explore how CNC automation supports material testing requirements unique to different industries.
1. Aerospace Industry
Aerospace materials are subjected to extensive testing to guarantee their safety and durability under extreme conditions. CNC-prepared samples are a necessity for tensile, fatigue, and impact tests on high-strength metals like titanium alloys and aluminum composites. Utilizing CNC technology allows aerospace labs to precisely prepare specimens to FAA and EASA standards. A high degree of precision is necessary to determine factors such as tensile strength and fracture resistance, which have a direct impact on the reliability of aircraft and the safety of passengers.
2. Automotive Industry
Automotive manufacturers rely on material testing to validate the durability and safety of vehicle materials. CNC automation is key to preparing specimens for compression, flexural, and impact testing. By creating samples with exact tolerances and consistent dimensions, CNC machines help engineers evaluate properties like flexibility, impact resistance, and fatigue life.
3. Medical Device Industry
Medical device manufacturing also requires strict testing to guarantee safety and compliance with regulations like ISO 10993. CNC technology is used to prepare tensile and fatigue samples, providing uniform specimens suitable for tests of durability and flexibility.
4. Construction and Civil Engineering
In the construction sector, materials such as steel and composite are subject to high standards of strength and durability. CNC technology allows labs to prepare compression and tensile samples with reliable precision, supporting tests on material properties crucial for structural integrity. This capability is valuable in testing load-bearing components for buildings, bridges, and other infrastructure.
5. Electronics and Semiconductor Industry
Electronics industry requires precise sample preparation for mechanical and microstructural testing. Electronic materials, such as ceramics and advanced polymers, need specific machining techniques that CNC technology provides. For microstructural analysis, CNC machines can prepare samples with mirror-like finishes, so that microscopic evaluations reveal accurate insights into a material composition.
How CNC Technology Transforms Sample Preparation
One of the standout features of modern CNC technology is real-time monitoring and automatic adjustments, allowing the machine to adapt instantly to any variable, such as temperature changes during cutting. For materials sensitive to heat or deformation, CNC systems can automatically adjust cutting speed or feed rate to preserve sample integrity. This dynamic control is particularly advantageous for materials like advanced polymers or aerospace-grade alloys, in which structural stability is a key component.
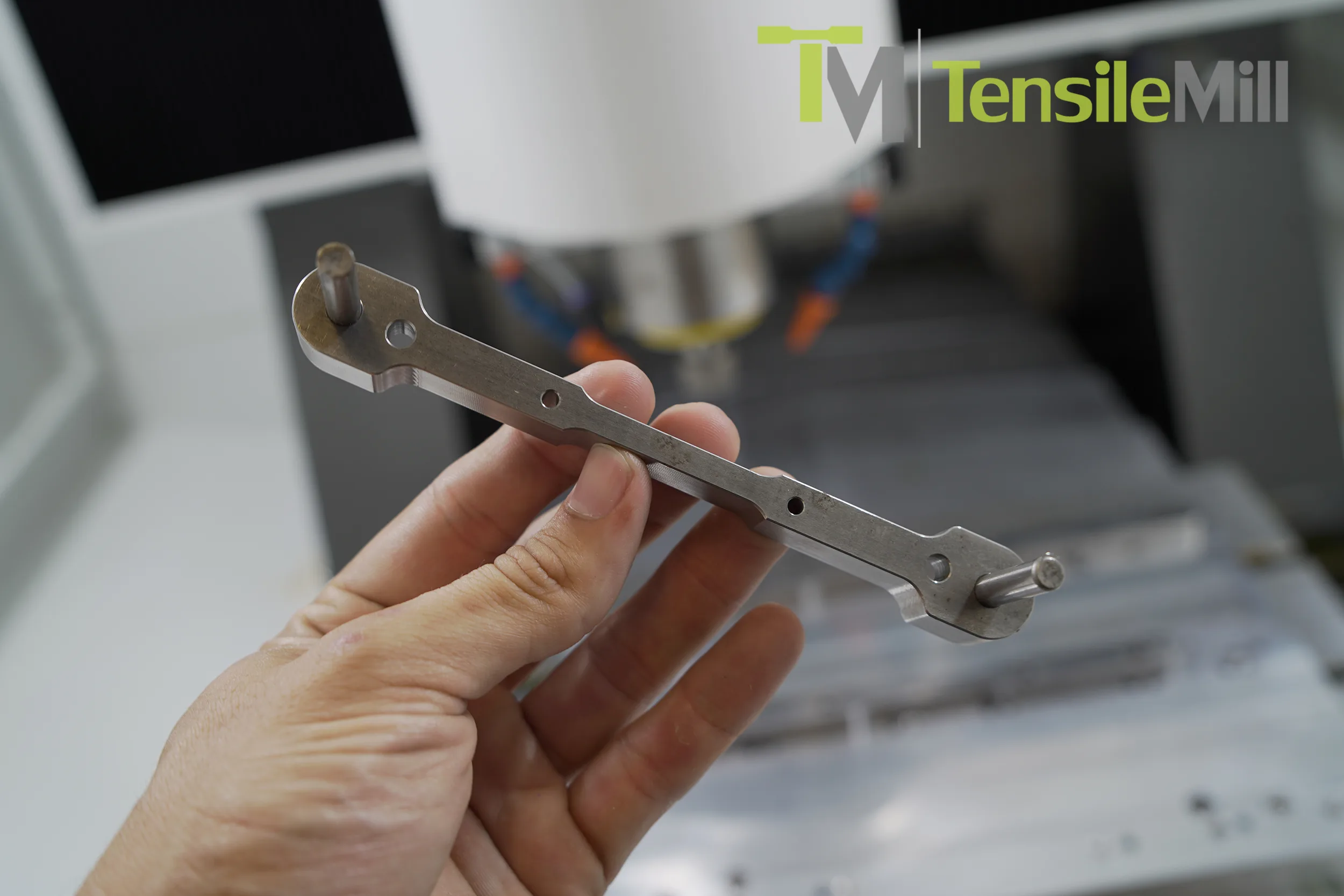
Moreover, CNC technology’s ability to handle multi-step processes in a single setup, from initial cutting to final polishing, significantly boosts laboratory productivity. By eliminating manual intervention between stages, CNC machines streamline workflows, reducing preparation time by up to 70% compared to manual methods. This efficiency allows testing facilities to increase sample throughput without sacrificing quality.
CNC technology brings another critical benefit to material testing. CNC-prepared samples exhibit smooth, uniform surfaces, free of irregularities that could lead to anomalies during testing. For tensile, fatigue, and hardness tests, this uniformity helps prevent issues like stress concentration points, so that test results reflect true material properties.
CNC technology also integrates advanced data collection features, enabling each preparation cycle to be logged with settings such as tool speed, wear, and temperature. Digital recordkeeping supports rigorous quality control and traceability, especially vital in compliance-heavy industries. Laboratories can monitor sample consistency, refine processes, and provide data-backed reports, assuring clients of consistent, standards-compliant sample preparation.
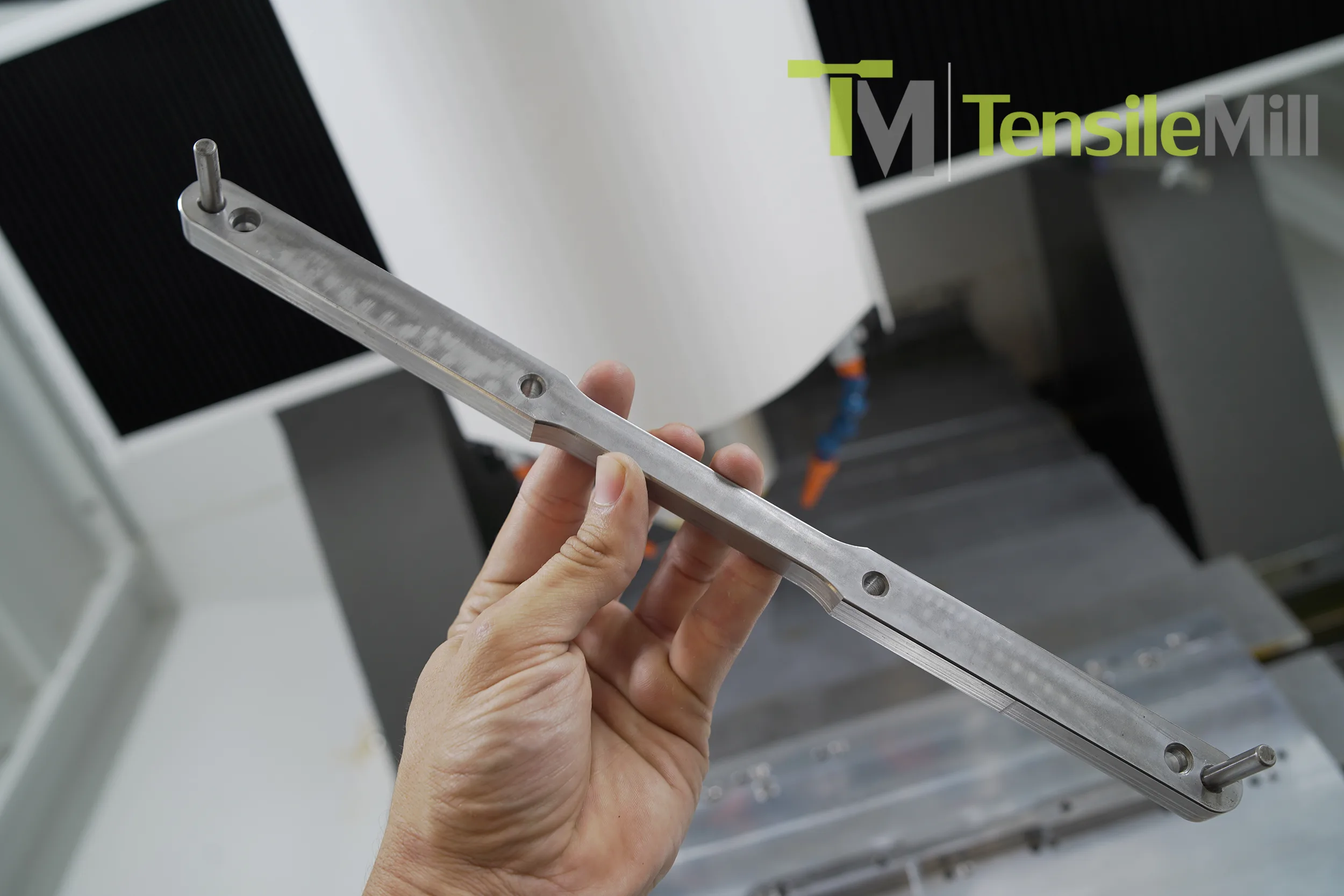
Finally, CNC automation minimizes material waste by executing precise cuts according to programmed specifications. This capability is especially cost-effective when working with high-value materials like titanium or carbon composites, where waste reduction directly impacts overall expenses. CNC systems guarantee that each sample is prepared with minimal excess, a factor that is especially important for industries where material costs account for a significant portion of the test budget. Additionally, CNC-prepared samples can be easily integrated into robotic testing systems, facilitating smooth workflows in high-throughput environments and reducing handling time for improved operational efficiency.
Why CNC Reliability and Regular Maintenance Matter
A reliable CNC system provides precise cuts, consistent dimensions, and flawless surface finishes. Without it, even slight inaccuracies in sample geometry or surface finish can lead to skewed data, compromising the integrity of tests and potentially leading to costly rework or product recalls.
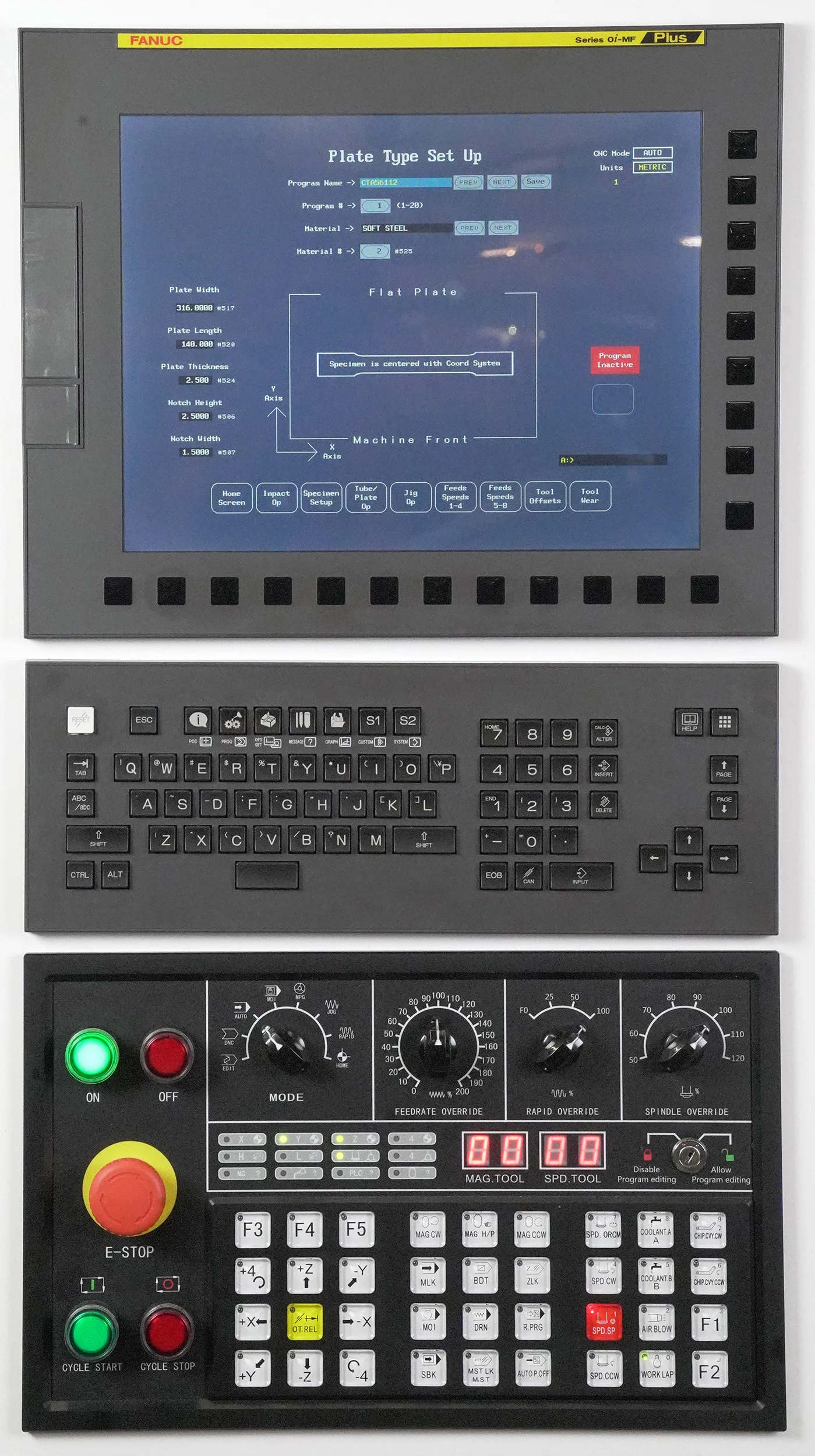
Regular maintenance of CNC machines is equally significant. Routine checks help prevent unexpected breakdowns so that the machine operates at peak efficiency. Maintenance routines typically involve inspecting and cleaning the machine, monitoring tool wear, and checking for proper lubrication, all of which help extend the life of the CNC system. For high-stake industries an unexpected machine failure can disrupt testing schedules, causing delays and increasing operational costs.
Proper calibration is another influential factor. Calibration makes certain that the CNC machine consistently meets precision tolerances, delivering samples that adhere to exact specifications every time. Over time, machine components can experience wear or drift from initial settings, which can lead to deviations in sample preparation if not corrected. Regular calibration keeps machine accuracy in line with required standards, supporting reliable testing outcomes.
For facilities focused on high-throughput testing, regular maintenance and calibration of CNC machines reduce downtime, guaranteeing that the equipment is always ready to meet testing needs. By investing in a reliable CNC machine and committing to consistent upkeep and calibration, testing facilities not only protect their equipment investment but also uphold the accuracy and dependability of their material testing processes.
TensileMill CNC - Classic Upgrade for Specimen Preparation
At TensileMill CNC, we specialize in high-precision equipment for specimen preparation and material testing. If you’re looking for an all-purpose CNC machine, the TensileMill CNC - Classic Upgrade is a great choice, designed to work with both flat tensile and impact specimens with speed and accuracy.
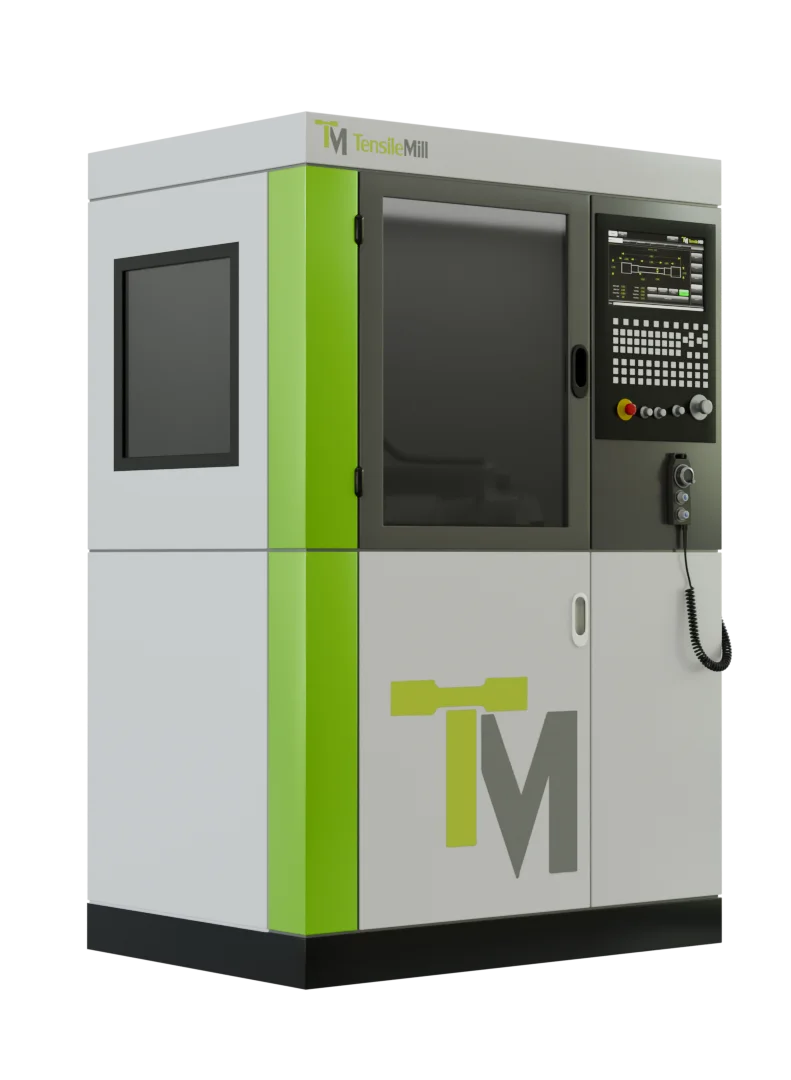
Equipped with TensileSoft™ software and a Fanuc controller, this machine supports both trained and untrained operators in achieving exacting standards for diverse testing requirements. The system supports specimens up to 14” (350mm) in length, 2” (50mm) in width, and 0.5” (12.5mm) in thickness, with an accuracy of 0.0003”. Its 3.2kW servo motor offers consistent results for materials up to 60 HRC, thus making it suitable for a variety of materials.
With triple clamping fixtures, up to three sets of samples can be prepared at once, supporting high efficiency and productivity. Additionally, the Classic Upgrade model prepares both U-notch and V-notch impact specimens, fully compliant with ASTM E23 standards. For greater ease of use, the machine includes automatic oil lubrication and a preprogrammed library of standard specimen sizes.
This all-in-one solution simplifies specimen preparation, offering an advanced, time-saving option for labs aiming to meet high testing standards with a high level of repeatability and accuracy.
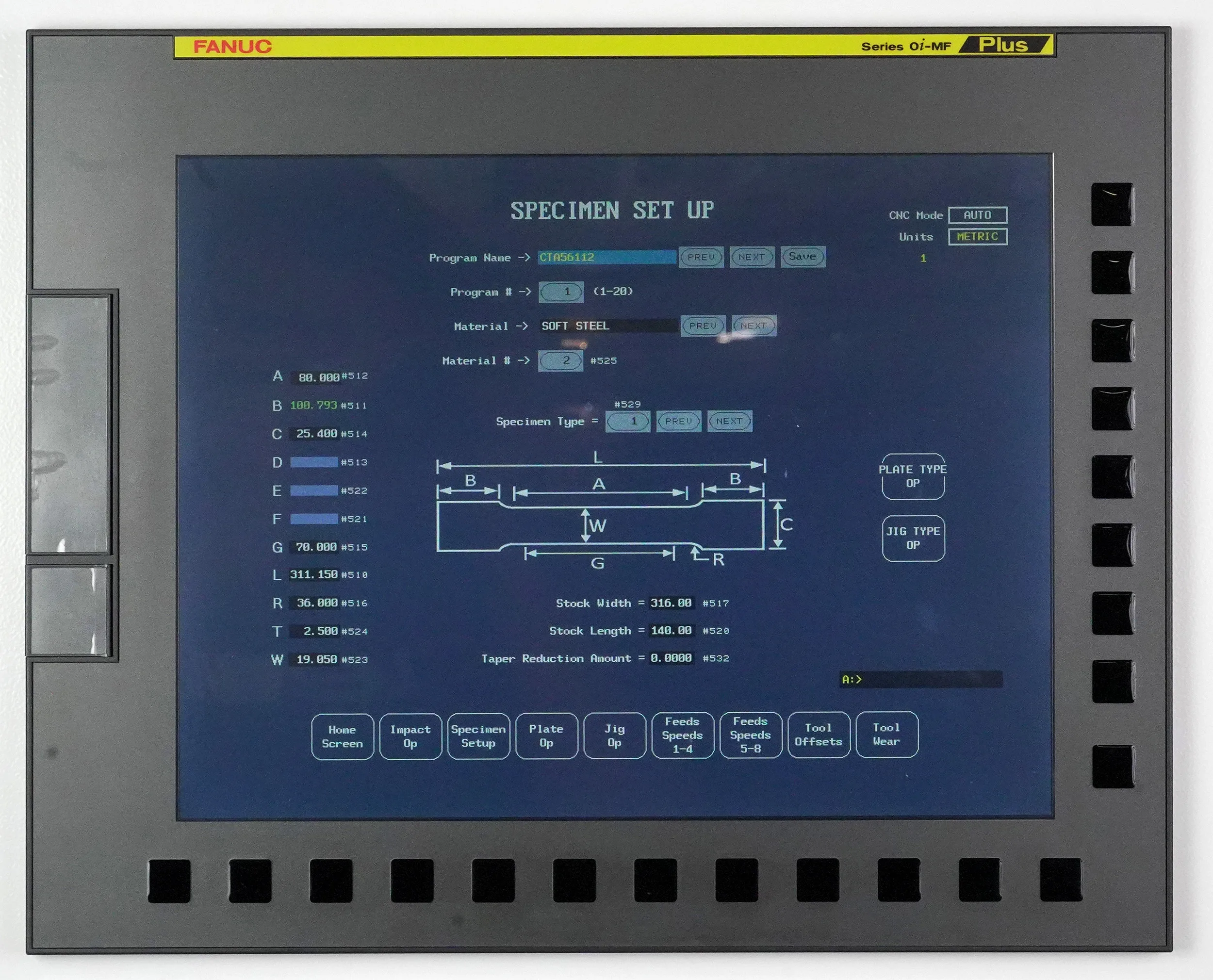
The Future of Material Testing with CNC Sample Preparation
CNC technology has redefined sample preparation in material testing, enabling unprecedented precision, efficiency, and consistency in a number of industries. By automating the complex processes of cutting, shaping, and polishing, CNC machines eliminate variations and potential errors often associated with manual preparation, providing laboratories with reliable results that comply with ASTM and ISO standards. This transition to automation supports a broad array of testing needs, from tensile and impact testing to microstructural analysis and fatigue testing, guaranteeing that each sample meets exact accuracy specifications.
Modern CNC systems offer advantages beyond precision alone. Through features like real-time monitoring, automatic calibration, and multi-stage processing, CNC technology optimizes both sample quality and laboratory productivity. Automated adjustments in response to variables, such as temperature or material behavior, provide consistent results across all sample types, including metals, polymers, and composites. The capability to handle different specimens with minimal manual intervention also allows labs to meet high testing demands without adversely affecting quality.
The implementation of CNC technology is imperative for laboratories committed to efficient, reliable material testing. If you are seeking advanced sample preparation solutions, consider exploring our Classic Upgrade model. For further assistance, feel free to reach out with any questions, or request an online quote. We’re here to support your testing needs with expertise and innovation.