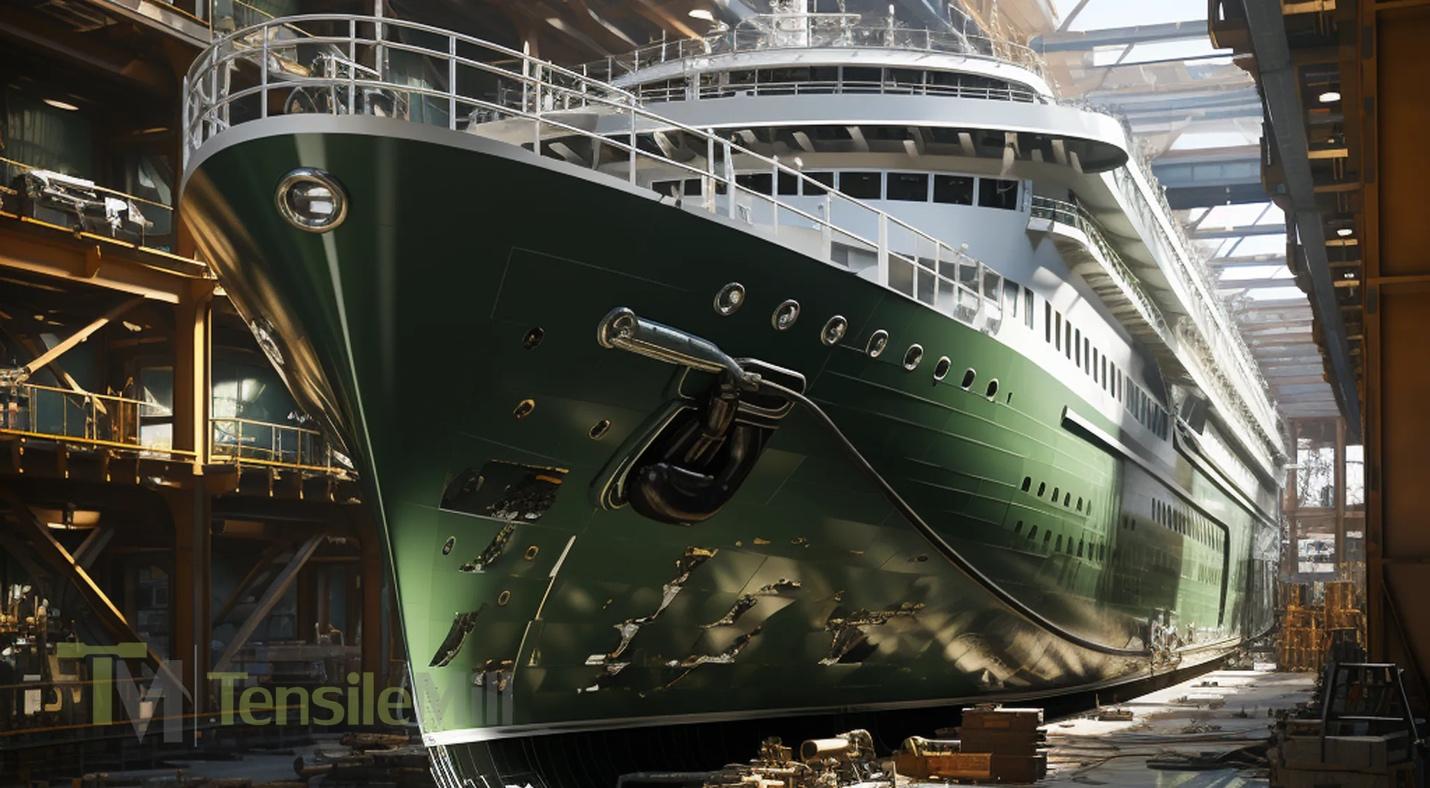
Development of materials in shipbuilding: from wood to composites
Initially, wooden ships were built being lightweight, fairly strong, and made of readily available material. However, they were limited in size and could not compete with steel ships that appeared later in the 19th century. Steel ships were much stronger and could be built larger, allowing them to carry more crew, passengers and cargo. However, steel has its drawbacks, such as vulnerability to corrosion, even when it comes to stainless steel. In the 20th century, new materials for shipbuilding emerged, such as aluminum, fiberglass and rubber.
Aluminum is lightweight and corrosion-resistant, which has made it popular in shipbuilding industry. However, its price is 3 times higher than that of stainless steel, and it has certain technical difficulties associated with metalworking, namely welding. Fiberglass and rubber (Rigid Inflatable Boats) are mostly used to create small, very lightweight boats.
An important trend in modern shipbuilding industry is the increasing use of composite materials such as kevlar, carbon fiber and epoxy resins. These materials combine high strength, lightness and corrosion resistance. Shipbuilders also combine different structural materials to achieve optimum performance. For example, stainless steel can be used for the main structural elements, while rubber or composites are used for non-structural parts or internal equipment.
Titanium is a high-strength, relatively lightweight and corrosion-resistant metal. However, its widespread use in the shipbuilding industry is severely limited by its high price. Due to its unique properties, it can be used in special applications where a combination of high strength and corrosion resistance is required: in military and research ships for structural elements such as decks and hulls.
So, in a historical retrospective, materials for shipbuilding industry have evolved from wood to steel and then to aluminum, fiberglass and modern composite materials. However, stainless steel is still the main structural material for building large ships today. It has properties that make it an ideal choice for large ships: it is quite strong at a low cost, and provides high compressive and bending strength. In addition, steel can be easily welded, which contributes to the structural strength of the vessel. The problem of corrosion resistance can be solved by metalworking methods, including heat treatment and the application of protective coatings.
Changing the Shipbuilding Industry
In today's world, with the many materials available for use, shipbuilding engineers are constantly coming up with ideas on how to improve or reduce the cost of products, which leads to changes in the production cycle. Therefore, at the beginning of a new project in shipbuilding industry, the question of how best to organize the production process arises: should we create production facilities ourselves to manufacture the necessary parts and structural elements? Or should we turn to third-party companies specializing in the production from a particular material – metals, rubber and elastomers, composite materials?
What is more cost-effective?
This is not a simple question and requires an assessment of several key factors that can influence the decision:
- Production volumes. If the production of ships is constant and large-scale, then owning your own production facilities may be a more cost-effective option. This allows you to control the quality and timing of production, and reduces dependence on third-party suppliers.
- Specialization. If the production of certain ship components requires specialized expertise or technologies that are not the core business of the shipbuilding company, then engaging third-party suppliers may be a more efficient solution.
- Cost. In-house production facilities may require significant expenditure on equipment, new professional staff and infrastructure support, which increases initial costs but may result in lower costs in the long run. Engaging third-party suppliers can reduce initial costs, but requires contract management, logistic, and may involve the risk of supplier dependency.
- Risks. Involvement of third-party companies may create risks associated with dependence on timely fulfilment of orders by such companies. In such cases, in order to ensure the reliability of your own production, you should always consider a plan B in case of such delays and failures.
- Saving time. Involving third-party suppliers can provide greater flexibility and speed of production, as there is no time spent on setting up your own production facilities and mastering new technologies.
At the initial stage, it is worth planning to create a pilot sample of a new product, or a pilot batch, to assess the quality characteristics and cost, and based on all the results, decide on a further scheme for setting up mass production.
Metals and Metal Fabrication for the Shipbuilding Industry
The choice of metal for shipbuilding is usually based on several criteria, which are taken into account depending on the needs and requirements of a particular project. Professionals in metal fabrication have up-to-date information on the modern metal alloys available to meet the needs of shipbuilders.
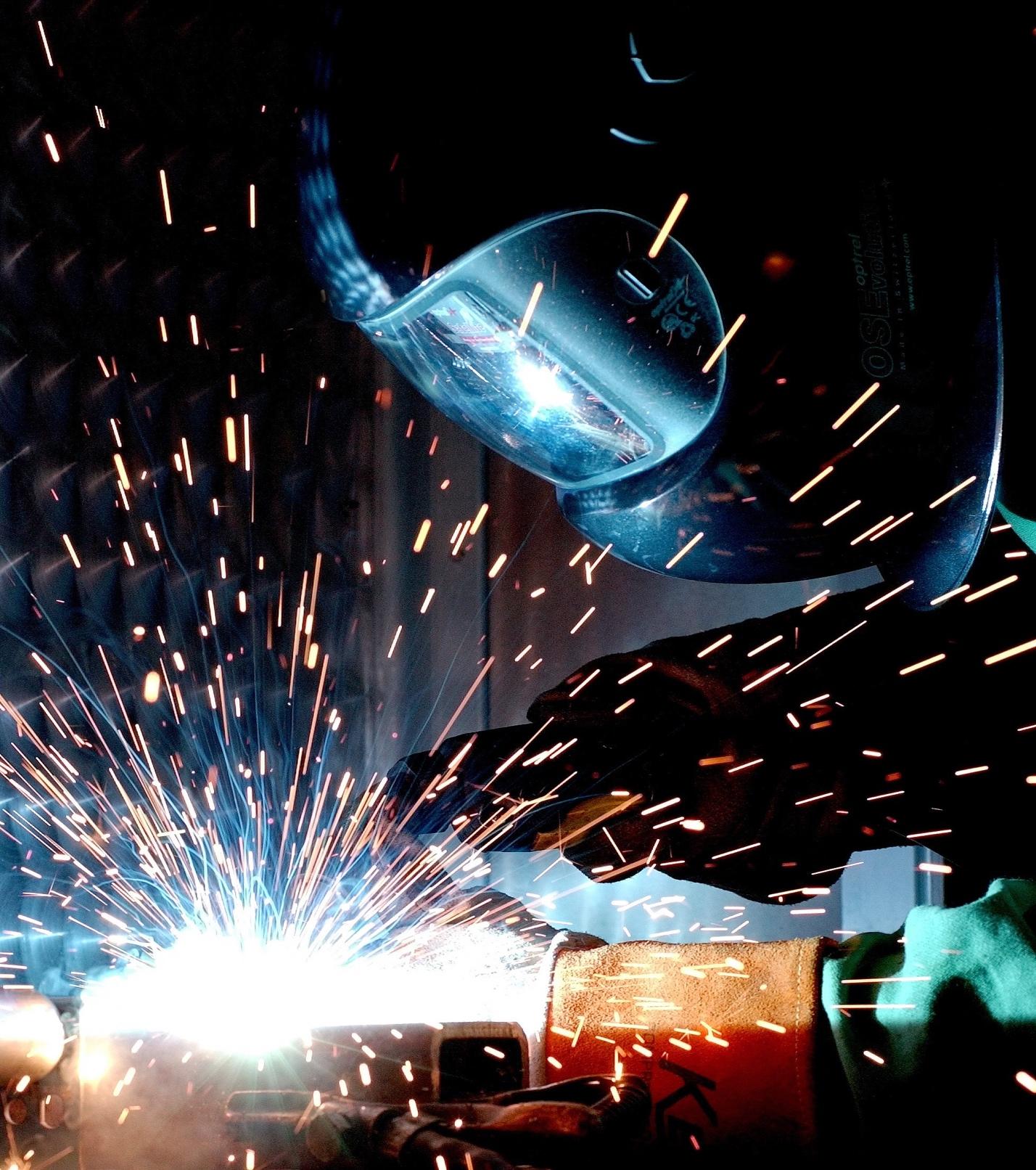
Ships must have sufficient strength to withstand the stresses of navigation and interaction with water. The construction material must have sufficient compressive strength to avoid deformation and structural failure under water pressure. In extreme temperature conditions, at low temperatures, the metal should not change its mechanical properties from ductile to brittle and become vulnerable to fracture. Also, warm water should not significantly reduce the corrosion and wear resistance of the metal. Lightweight materials, such as aluminum alloys, offer advantages in reducing the weight of the vessel. This can contribute to reduced fuel consumption, improved maneuverability and increased cargo capacity. However, structural strength of aluminum may be lost compared to steel. The loss of strength can be compensated for by increasing the thickness of the aluminum walls, but this will certainly increase the price. The use of titanium alloys can increase strength, corrosion resistance and reduce the weight of the vessel, but its cost will increase significantly.
In shipbuilding industry, steel grades such as AH36, DH36, and EH36 are used, which have increased strength and corrosion resistance in both hull and superstructure construction. In the case of aluminum, alloys of the 5000 or 6000 series can be used, which combine lightness and strength. In the case of titanium, alloys such as Ti-6Al-4V and others are used by the US Navy to build warships. This significantly increases the mobility and stability of ships and reduces hull weight while maintaining its high strength.
In general, the choice of a particular metal and its grade in shipbuilding depends on a comprehensive analysis of project requirements, technical capabilities, economic and many other factors considered by project engineers and specialists in the field of metal fabrication and shipbuilding industry.
The metalworking methods used in shipbuilding industry include almost all metal forming methods for steel fabrication. Among them are the following.
- Sheet metal production: the process involves the use of a rolling mill to produce sheet metal of various thicknesses.
- Die casting: molten metal is poured into a mold under high pressure. This method is used to produce complex parts, such as engine and turbine housings.
- Sand casting: this process requires a mold that is filled with molten metal that solidifies after cooling. Sand casting is a simpler and more economical method for producing large parts, such as ship hulls.
- Powder metallurgy: the process requires powder pressing, where metal powder is compressed into a mold under high pressure and then sintered, to produce complex small to medium-sized parts.
- Extrusion is carried out using an extruder, a specialized device for compressing metal through a hole that is shaped under a certain pressure, which allows for profiles with complex geometries.
Read more in our blog: 12 Major Benefits of Aluminum Extrusions
- Bending (forming): This method is used to create curves, roundings and angles in the metal sheets that will be used to create the hull of the ship. Bending can be done using presses or special machines.
- Drawing: this process requires a drawing mill, which is used to produce wire and ropes of various thicknesses from metal.
- Press forming (hot or cold) takes place in a pressing mill using rolling, forging, and stamping. Hot forming allows metal to be shaped by plasticizing at high temperatures. Cold forming requires more force to form the metal, but has greater geometric accuracy and can be used to produce thin sheets.
- Heat treatment is a set of methods for improving the mechanical properties of metal products. This process takes place in a furnace at high temperatures, which allows changing the structure of the alloy and its structure and properties. Heat treatment is used to fix the shape, harden and release stresses in the metal, to strengthen the surface and improve its anti-corrosion properties.
Read more in our blog: The 10 Benefits of Heat Treating In Metalworking
5 Ways the Tool and Die Sector Uses Heat Treating
- Other methods include drilling, welding, milling, grinding, polishing, electroplating, painting, and applying protective anti-corrosion coatings.
Of course, each of these methods has many variants, and the nuances of their application depending on the type of metal and the requirements for the final product. Therefore, when deciding whether to outsource the production of parts, the complexity of these processing methods and the time required to master them should be taken into account.
How Can Metal Fabricators Solve Shipbuilding Challenges?
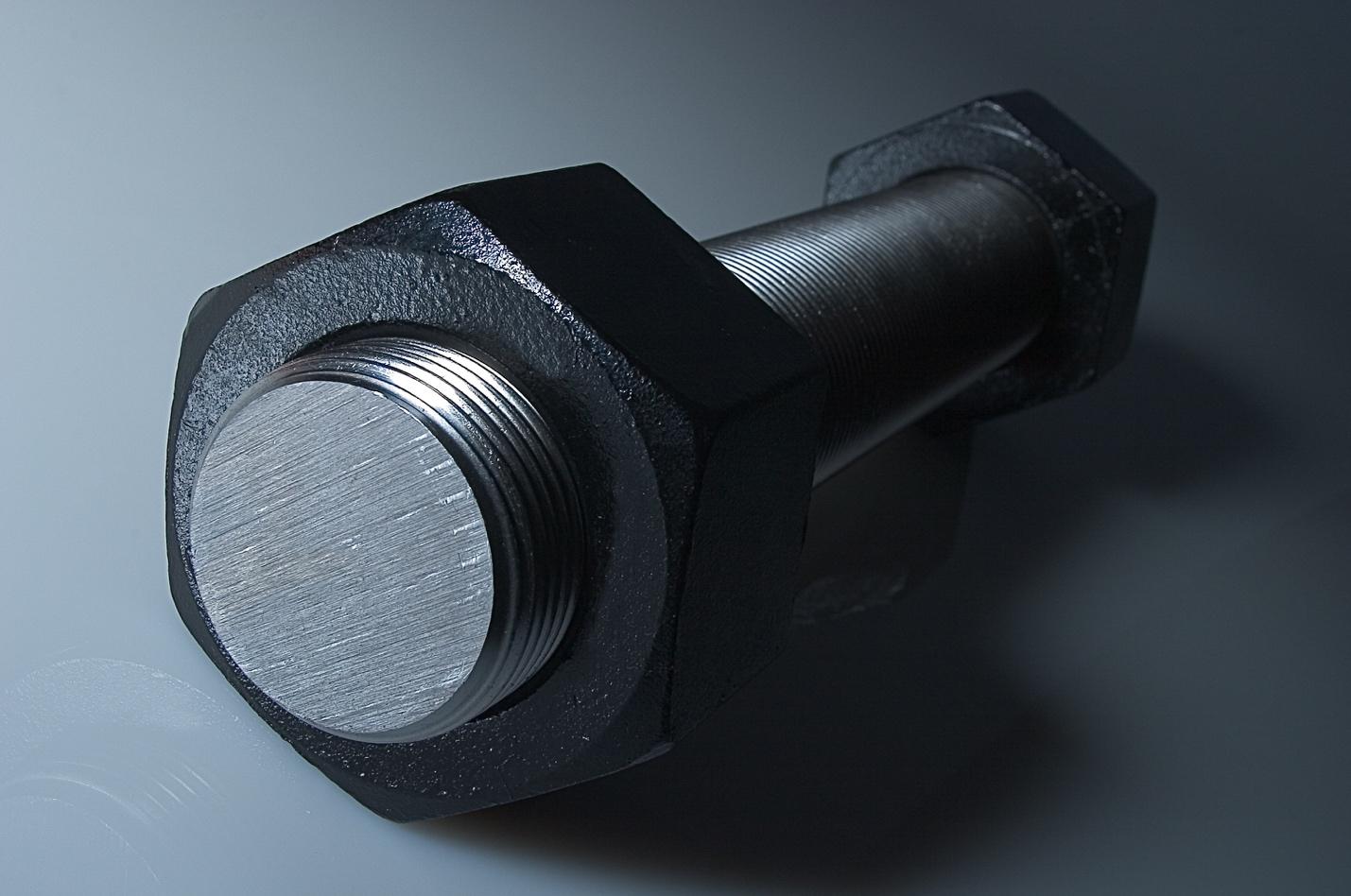
Metal fabrication is the process of shaping steel into the desired shape to meet your needs. Metal fabricators offer many benefits to a variety of industries, a large part of which is shipbuilding in both the commercial and military sectors. Let's take a look at some of the benefits that metal fabrication offers to the shipbuilding industry.
- Competence: metal fabricators have the most extensive experience in the industry, possess the professional knowledge and know-how to solve complex technological problems and keep abreast of new developments.
- Quality: these competencies are used to maintain and improve products, ensuring high strength, corrosion resistance and other necessary properties, and the ability to operate at extreme temperatures.
- New alloys: the creation of special alloys and the improvement of known alloys is constantly being carried out to improve the characteristics that are important for the shipbuilding industry.
- Variability of metalworking: the most professional application of a set of metalworking methods in their modern execution.
- Improved and new metalworking technologies: metal manufacturers are constantly refining well-known and introducing new metalworking technologies, such as laser cutting, bending, drilling and milling, and assembly. These allow for the production of more complex and precise parts for ships.
- Protective coatings such as paints, galvanising or surface treatments to protect metal from corrosion and other negative environmental influences, when applied professionally, can significantly extend the service life of ships.
- Quality control is carried out on an ongoing basis to ensure compliance with shipbuilding standards and requirements. This includes determining the mechanical properties of the metal, such as tensile testing and other important parameters.
Read more in our blog: What is the Leading Tensile Specimen Lathe - TensileMill CNC
- Accessibility: The North American market has a large number of companies in the metalworking sector with a reputation for reliable suppliers and in-house logistics capabilities. This competitive environment allows shipbuilders to receive qualified service at reasonable prices.
- Cost-effectiveness: fruitful cooperation between shipbuilding companies and metal producers can be realized not only at the initial stages of a shipbuilding project. Cooperation with a reliable third-party supplier can become permanent, avoiding the cost of setting up an in-house metalworking division.
- Collaboration and advice: metal producers liaise with shipbuilders to provide advice and support in selecting the right metal for specific projects. They can also develop special solutions and customize production to meet individual customer needs.
These ways show how metal producers are actively contributing to the development of the shipbuilding industry by providing quality metal and innovative solutions for ship production.
The Importance of Tensile Testing for the Shipbuilding Sector
Tensile testing of metals is an important part of the shipbuilding process and quality control. These tests allow us to assess the mechanical properties of a metal, including its strength, ductility and deformation characteristics under stress. This is used in the development of new metal alloys and materials for shipbuilding. It helps to determine the optimal alloy compositions and processing parameters to obtain the required mechanical properties and improve metalworking processes.
These tests also help determine the yield strength, tensile strength and fracture strength of the material. The obtained data is used for determining the maximum load that a metal can withstand without breaking, and for assessing the metal's ability to undergo plastic deformation before fracture. Such knowledge is crucial for construction of structural elements that may be subjected to bending, tension or compression during the operation of boats.
Tensile testing is an important step in the certification and quality control process for metal materials in the shipbuilding industry. It confirms that the material meets the established standards and can be used in ship structures in accordance with safety requirements.
In general, tensile testing of metals is a necessary step in the manufacture of metal structures for ships, as it provides information on the strength, ductility and quality of the material, which are crucial factors for the safety and reliability of ship structures.
TensileMill CNC Inc. supplies the most reliable tensile testing equipment that meets all the latest international industry standards. The tensile testing system is designed to provide accurate results with ease of use in the force range from 1 to 3000 kN. The development of our equipment is based on the extensive experience of our customers to ensure convenient and efficient operation. We also provide comprehensive after-sales consulting and technical support to ensure that your projects progress smoothly.
At the same time, we offer many years of field experience combined with practical knowledge of industry best practices in sample preparation and material testing. All of this serves as the basis for providing our customers with the best possible testing equipment.
TensileMill CNC Tensile Tester
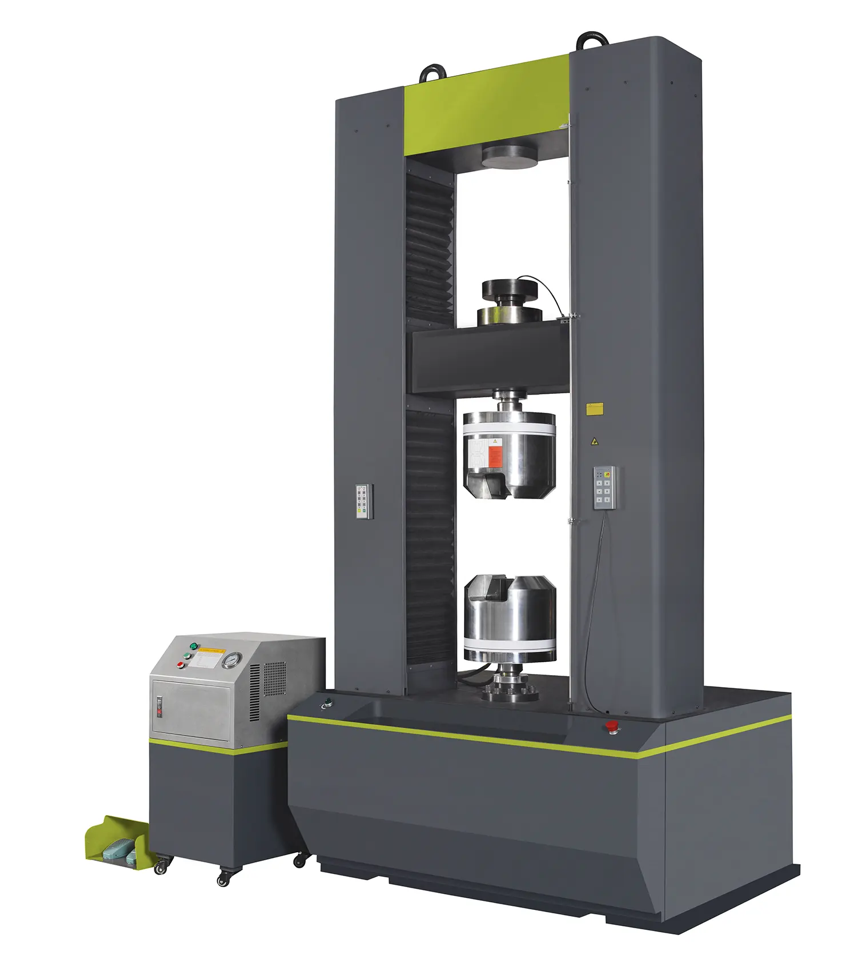
The accuracy of the tensile test specimen shape has a significant impact on the results. Even minor deviations in specimen dimensions can affect test results. For example, if the specimen has the wrong width or thickness, it can change the effect of the applied load, the location of the failure zone, or even cause the specimen to break in an unexpected place. The shape and geometry of the specimens are also important. That is, if the specimen has an uneven cross-section or sharp corners, this can lead to stress concentrations and therefore affect the test results. Surface defects, such as scratches, cracks, or rejects, can affect the stress distribution in the specimen and cause incorrect test results.
In order to obtain accurate tensile test results, it is important to maintain the precision requirements for specimen manufacturing. This is accomplished with high quality tensile testing equipment also supplied by TensileMill CNC Inc.:
Request the quote for testing equipment from TensileMill CNC Inc. today for safe travels on your ships in future!