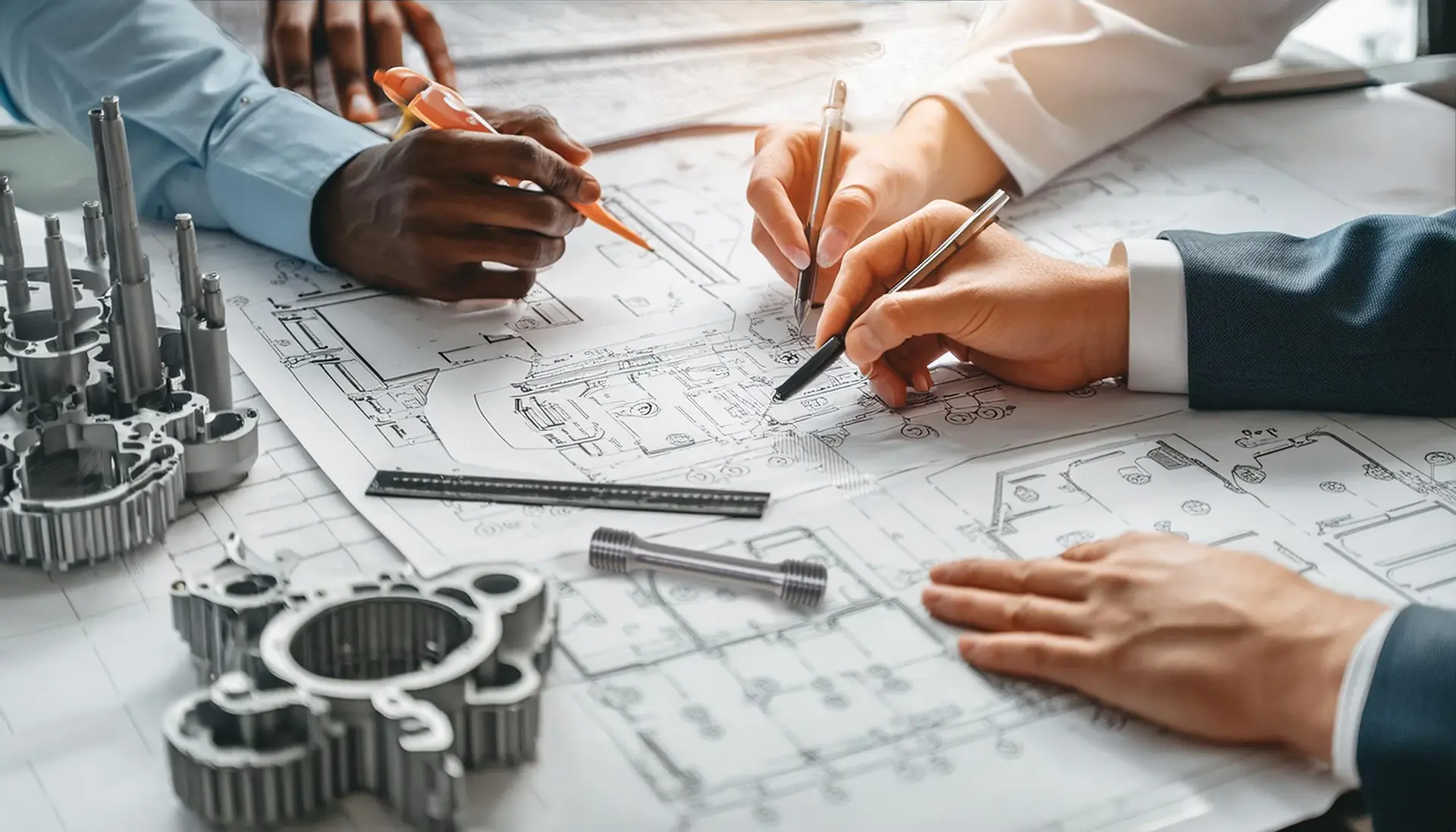
In the quality assurance of everyday items, from the tools we use to the transportation we use, to the buildings we occupy, tensile testing plays a key role. This type of material examination is not confined to these areas alone. It is widely applied to common products that are made from metals, plastics, and composite materials. For instance, even LEGO blocks, which can withstand heavy forces without breaking, are tested for tensile strength.
Despite its widespread application, not all manufacturers conduct tensile testing for materials in their products. Some believe that this type of testing is both time-consuming and costly. However, the tensile test offers numerous advantages that far outweigh its costs.
The purpose of this blog is to discuss the benefits of tension testing and why every manufacturer should consider incorporating it into their quality assurance processes. Our discussion will focus on how tensile testing ensures the reliability of manufactured goods as well as other benefits it offers.
Understanding Tensile Testing
In order to understand how tensile testing can benefit manufacturers, we must first discuss the basics of what it is and why it is so important.
A tensile test is a material science technique used to determine how a material reacts to forces exerted upon it. The purpose is to assess the mechanical properties of various materials to verify that they meet the required standards for strength and durability. It measures properties such as tensile strength, yield strength, elongation, and Young's modulus. Thus, providing critical information regarding the behavior of a material when subjected to tensile stress.
The Process of Tensile Testing
A tensile test involves several key steps:
- Preparation: The material sample, or specimen, is prepared according to specific dimensions and shapes required by the testing standards.
- Mounting: The specimen is mounted on the tensile testing machine using grips or fixtures to hold it securely.
- Loading: A tensile force is applied to the specimen at a constant rate, pulling it apart until it breaks.
- Measurement: During the test, data is collected on the force applied and the specimen elongation.
- Analysis: The data is analyzed to determine key properties.
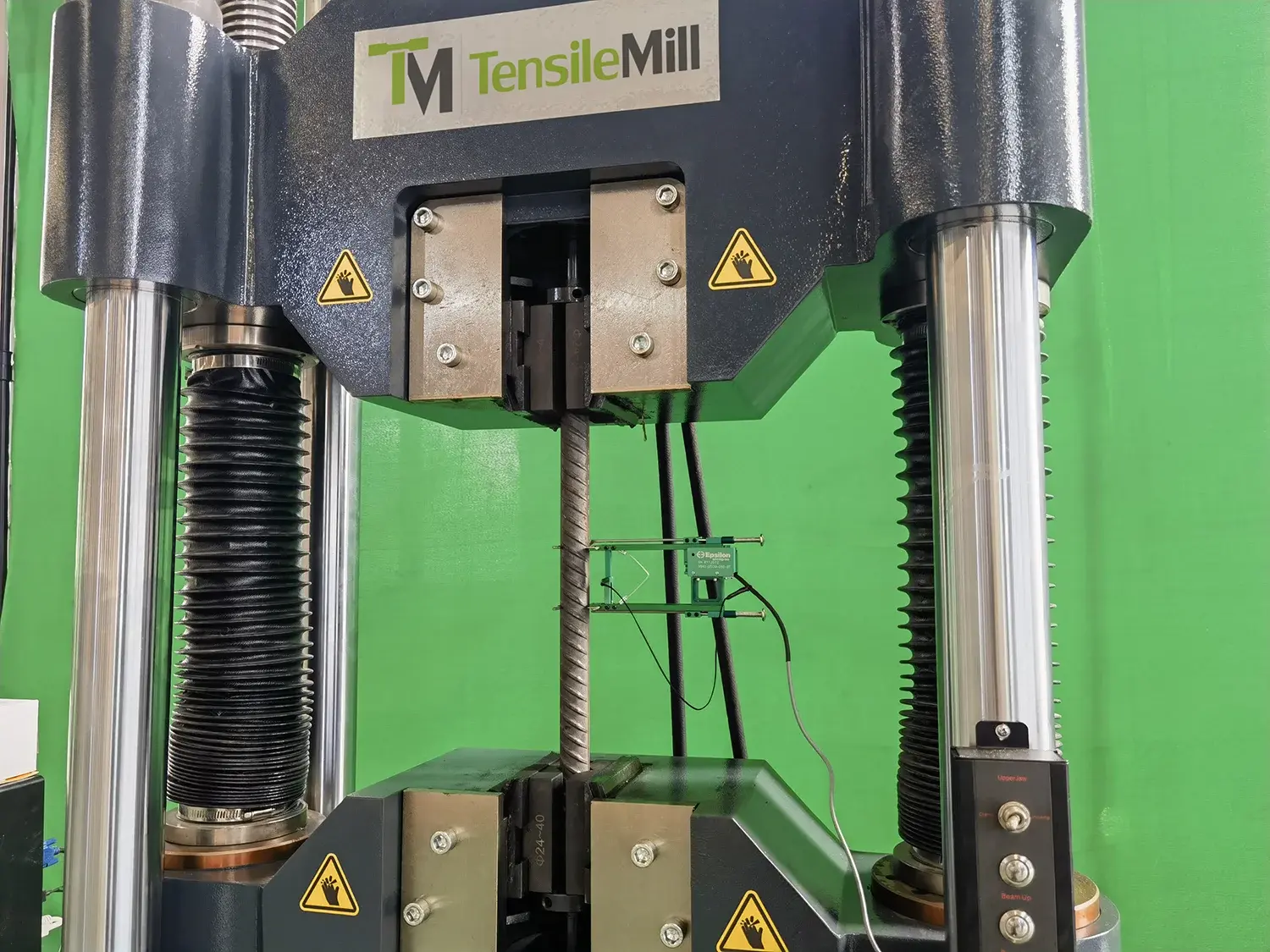
Equipment Used in Tensile Testing
Testing for tensile strength requires specialized equipment to achieve accurate and reliable results. As part of the primary equipment, there are a few types of machines such as:
- Tensile Testing Machines (UTMs): These machines apply tensile force to the specimen and measure its response. Universal Testing Machines are commonly used for their capability to conduct numerous types of tests.
- CNC Machines for Specimen Preparation: Computer Numerical Control (CNC) machines are used to prepare specimens with high precision.
Compliance with International Standards
All tensile testing procedures must comply with international standards in order to guarantee consistency and accuracy. Key organizations that establish these standards include ASTM International, the International Organization for Standardization (ISO), and the Deutsches Institut für Normung (DIN). Among the most notable standards are:
- ASTM E8/E8M: This standard specifies the methods for tension testing metallic materials.
- ISO 6892-1: This standard covers the tensile testing of metallic materials at room temperature.
Benefits of Tensile Testing for Manufacturers
As mentioned earlier, the tensile test offers numerous advantages. The following are some of the key advantages of tensile testing:
Quality Assurance and Reliability
First and foremost, tensile testing confirms that materials meet specific strength and durability requirements. Manufacturers are able to verify that their products will perform reliably under expected conditions.
Affordability
Even though testing for tensile strength incurs upfront costs, it can save money in the long run by preventing product failures and reducing the need for product recalls. When material quality is ensured upfront, the risk of costly defects and warranty claims is minimized.
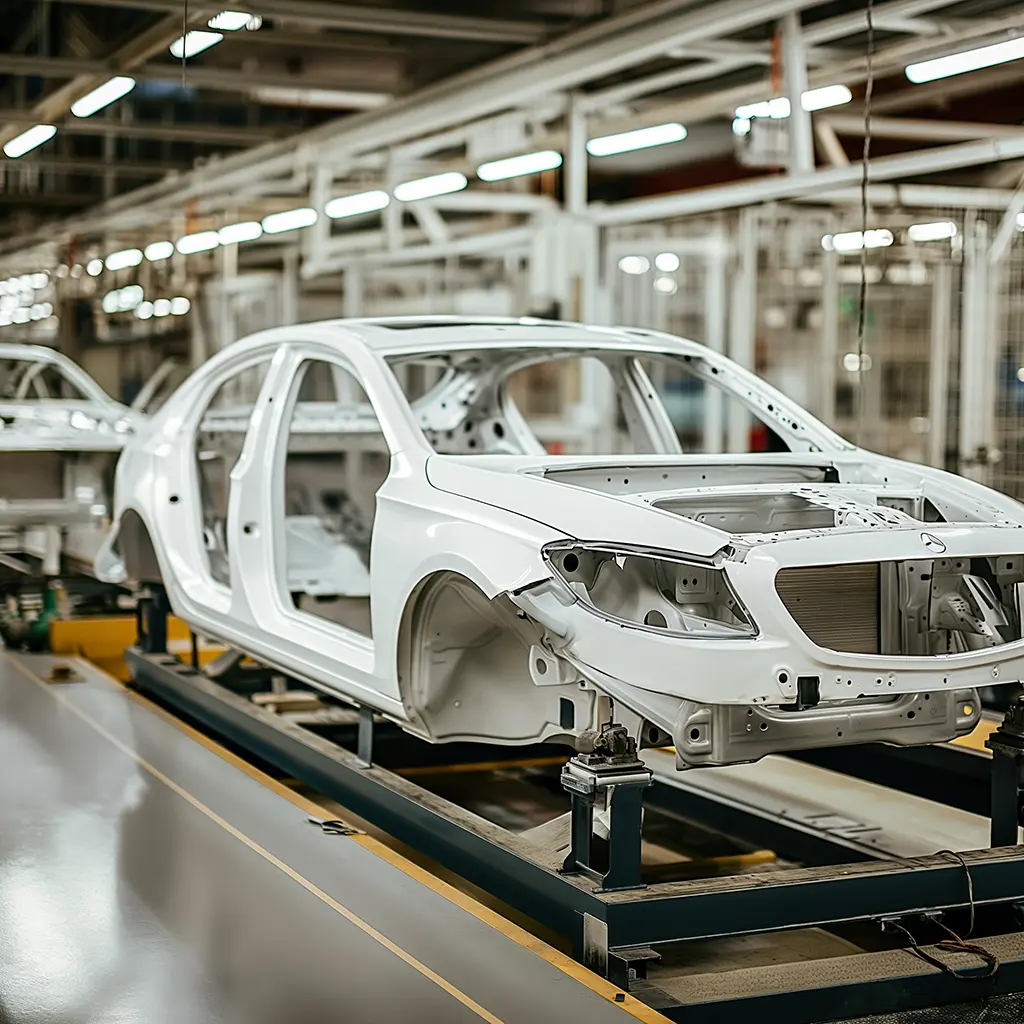
Improving Safety
By testing materials for their tensile properties, potential weaknesses that may lead to product failure can be identified. In industries where material failure can have severe safety implications, this is of particular importance.
Material Selection and Optimization
Tensile testing provides valuable information that can be used to select and optimize materials for specific applications. By understanding the mechanical properties of different materials, manufacturers can select the most appropriate for their products and optimize them for performance and cost efficiency.
Research and Development
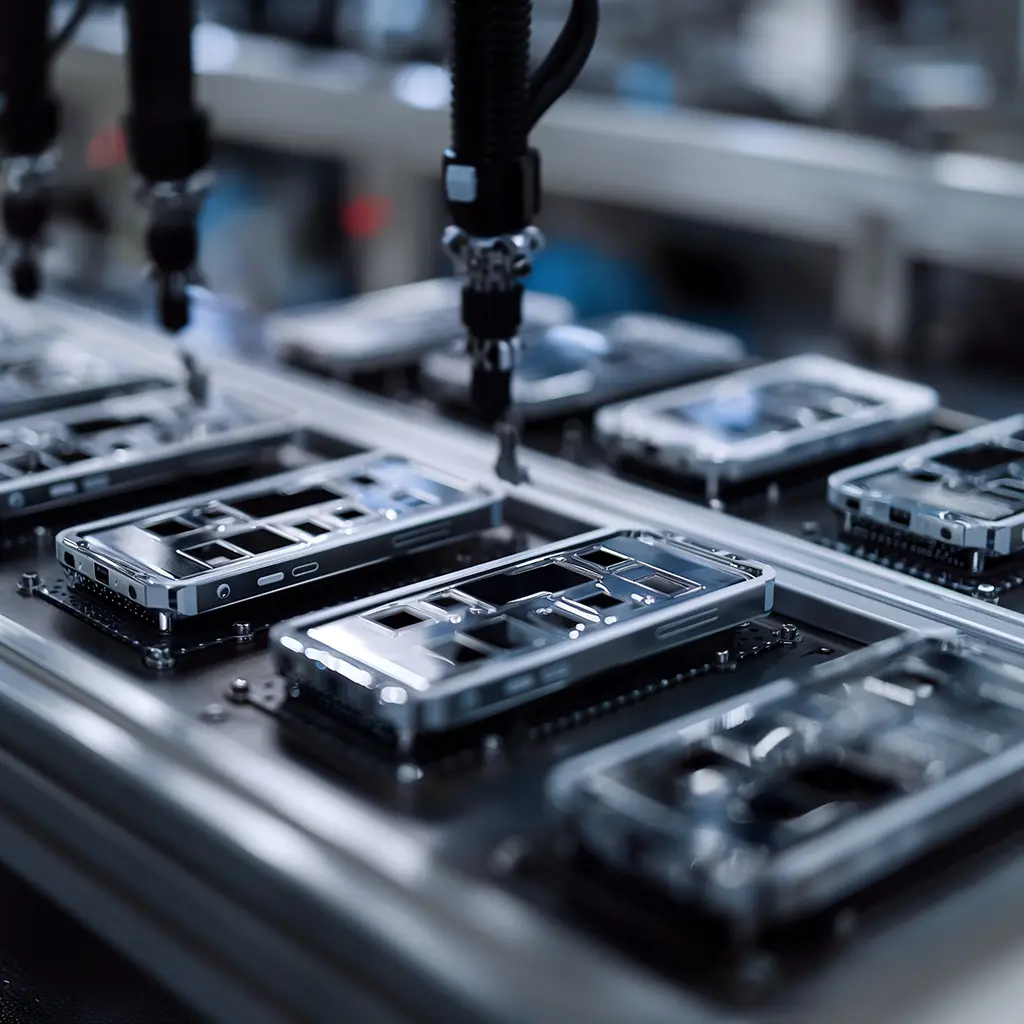
The purpose of tensile testing in R&D is to develop new materials and improve existing ones. As a result, scientists gain a better understanding of how different materials behave under stress. This results in innovations and advancements allowing manufacturers to produce better products.
Competitive Advantage
Tensile testing helps manufacturers achieve higher quality and reliability of their products, giving them a competitive advantage in the marketplace. Trust and satisfaction are more likely to be earned by products that consistently meet or exceed standards.
Advancements in Tensile Testing Technology
Another significant benefit of tension testing lies in continuous advancements in testing technology. Modern tensile testing equipment has evolved to offer the highest levels of efficiency, accuracy, and user-friendliness. These advancements include automated testing systems, advanced data analysis software, and high-precision extensometers. All these contribute to making tensile testing more accessible and reliable for manufacturers.
Automated testing systems have transformed the tensile testing process by reducing manual intervention and minimizing human error. These systems can handle multiple specimens at once, resulting in the consistent application of forces and precise measurements. This not only speeds up the testing process but also allows for more reliable and repeatable results.
Advanced data analysis software integrated into tension testing machines provides comprehensive insights into material behavior under stress. These software systems collect and analyze data in real time, generating detailed stress-strain curves and other critical metrics. Additionally, artificial intelligence (AI) improves predictive analysis and automated reporting, simplifying the process for users and enabling more informed decision-making.
Looking ahead, recent trends in tensile testing technology are poised to further advance manufacturing processes. The integration of AI and machine learning will enable predictive maintenance, optimize testing parameters, and provide deeper insights into material behaviors. IoT-enabled test machines will facilitate real-time monitoring and remote operation, allowing manufacturers to oversee testing processes from anywhere and make timely interventions. User-friendly interfaces will make tensile testing equipment accessible to a broad range of users, reducing the learning curve and giving non-experts the ability to perform complex tests easily.
Choosing the Right Tensile Testing Equipment
If you are considering tensile testing for your manufacturing processes, the first step is to select the appropriate testing equipment. At TensileMill CNC, we have been supplying our customers with advanced, modern equipment for years. Here are some of our best-selling products for specimen preparation and tensile testing procedures that may be of interest to you:
TensileMill CNC MINI - Flat Tensile Test Sample Preparation System
The TensileMill CNC MINI is a state-of-the-art machine designed for efficient tensile specimen preparation. Despite its compact size, this mini mill offers extensive capabilities for both tensile specimen preparation and full CNC machining. Recent upgrades have improved its performance, making it superior to previous models in nearly every aspect. The MINI now features a smaller footprint, larger table size, increased power, and improved precision and repeatability, all at a lower cost.
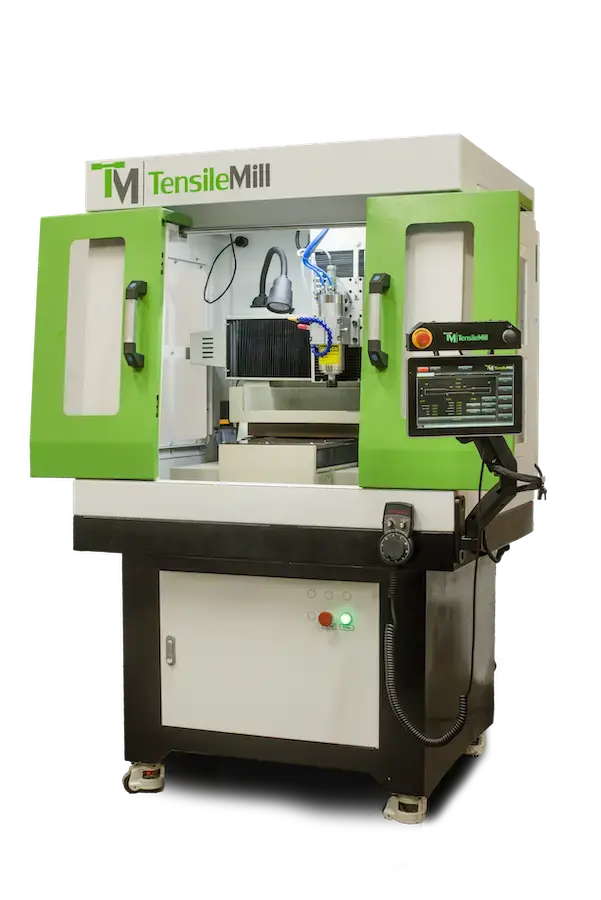
Operating the TensileMill CNC MINI is straightforward, thanks to its 10" LCD touchscreen equipped with intuitive Tensile Software. This interface allows operators to quickly input the desired specimen dimensions according to a number of industry standards, such as ASTM, ISO, DIN, and JIS. Once the parameters are set, the machine is ready to mill in seconds. The 2.2kW (3hp) Water Cooling Spindle and specialized tooling enable the preparation of various materials, including soft, hard, and Inconel, in large volumes.
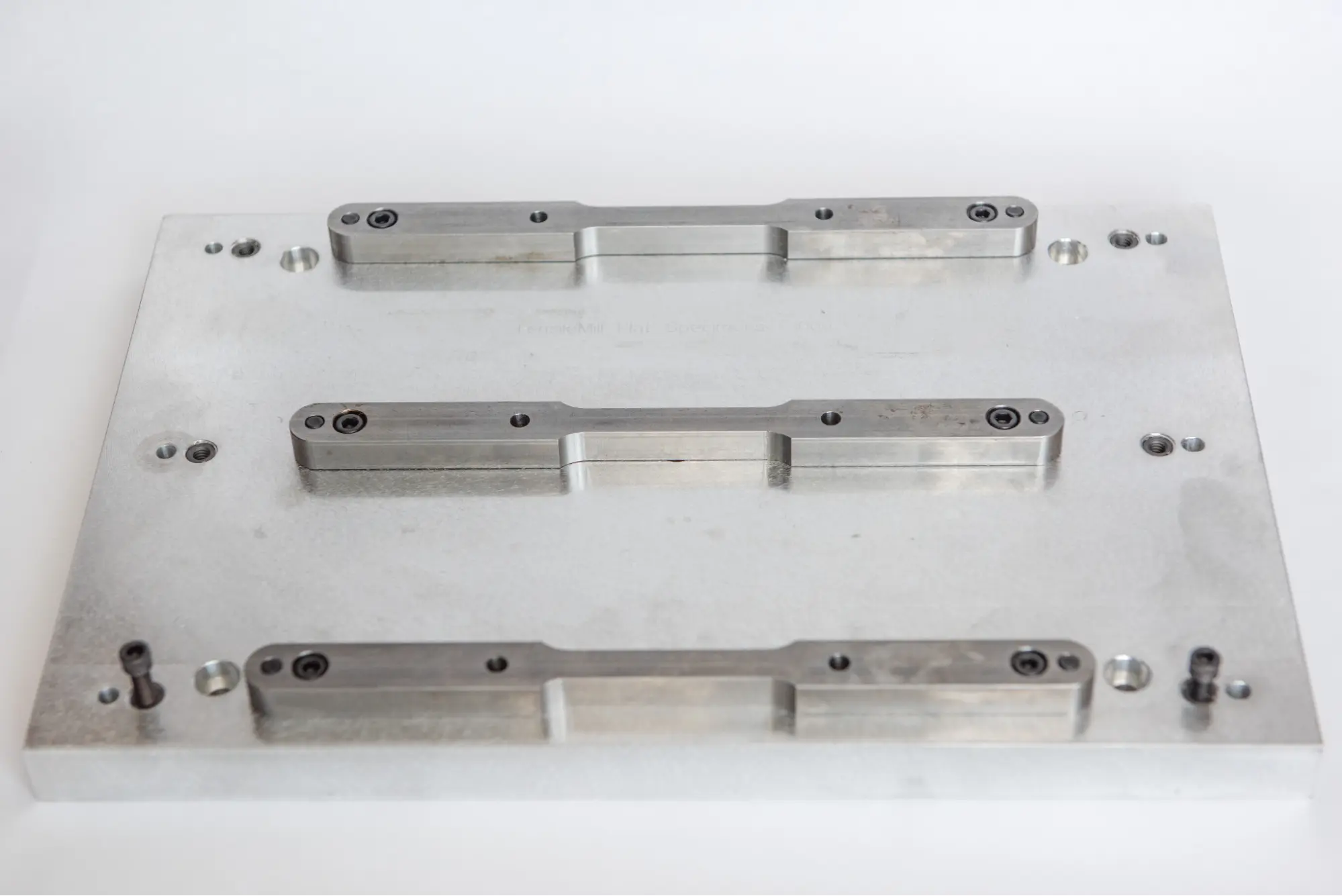
The machine also features a library of preprogrammed tensile specimens, which can be accessed quickly without entering original measurements each time. For advanced operators, the TensileMill CNC MINI can be upgraded with the Carbon software interface, transforming it into a hybrid tensile sample preparation and CNC machining center. This includes upgraded control capabilities, extensive storage, and connectivity options.
Built on a heavy cast iron frame with linear rails, the TensileMill CNC MINI combines durability with high-speed machining capabilities. Its 24,000 RPM ISO20 spindle and high-powered servos provide excellent performance, making it an ideal choice for the testing industry.
SHM Class A Series - Servo-Hydraulic Universal Testing Machine
One of our most popular products for tensile testing is the SHM Class A Series - Servo-Hydraulic Universal Testing System. The system is characterized by its high performance and high precision.
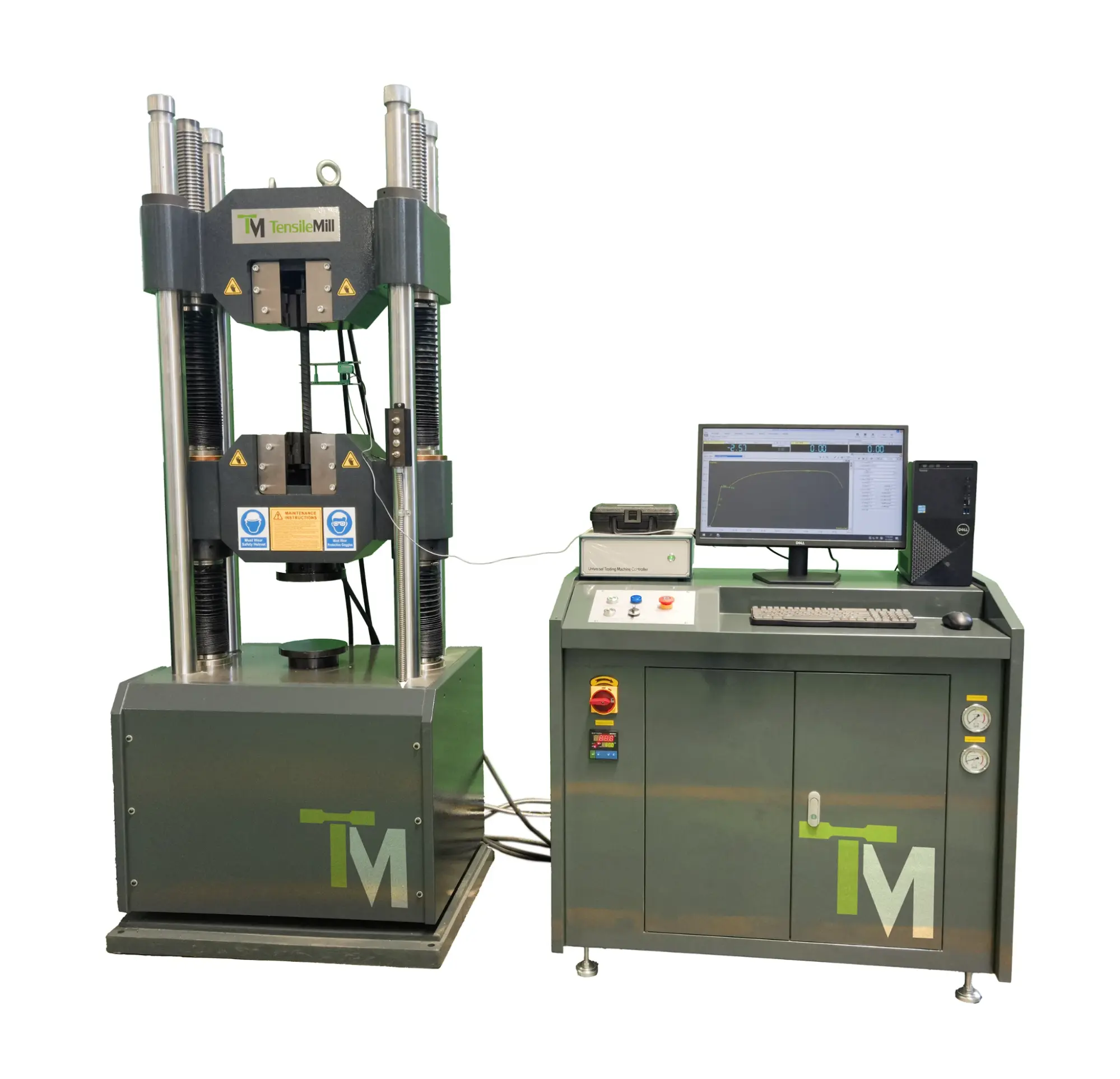
The SHM Class A Series is a high-performance 600kN / 1000kN multi-column testing system designed to handle different types of testing applications, including tension, compression, shearing, and bending. This system is known for its high accuracy, with measurement precision down to ±0.5% of the reading value.
The tester design features a sturdy 4-column and 2-lead screw structure. It is equipped with a hydraulic-operated tensile grip for ease of operation and a dual testing space configuration. The upper test space is dedicated to tensile tests, while the lower space is used for compression and bending tests. This configuration allows smooth transitions between different types of tests without reconfiguration.
Key features include a high-precision load cell that directly measures the testing force, ensuring high accuracy. The chain-type transmission system simplifies maintenance, and the clearance seal of the oil cylinder avoids aging and wear issues typically associated with O-seal rings. The half-open tensile jaw seat design prevents deformation and guarantees no slippage during tensile tests. The system complies with numerous international standards, including ASTM E8, ISO 6892, BS 4449, and others.
Additionally, a comprehensive set of standard accessories is included. These are Dell control PC, ATOS hydraulic servo valve, high-precision load cell, photoelectric encoder, and other tensile and compression test accessories.
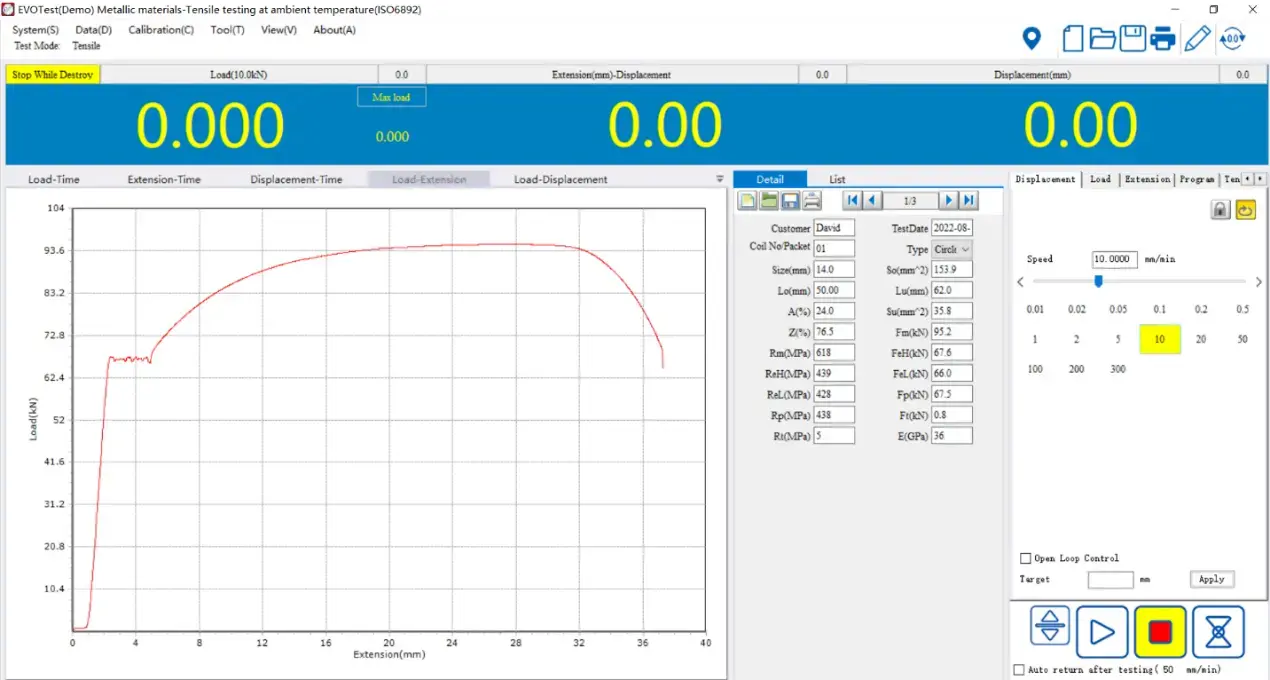
Maximizing Manufacturing Excellence with Tensile Testing
The tensile testing process offers a multitude of benefits to manufacturers that guarantee the quality, reliability, and safety of their products. Manufacturers can verify that their products meet stringent industry standards and perform reliably under various conditions by testing the mechanical properties of materials such as tensile strength, yield strength, and elongation. As a result, not only are high-quality standards maintained, but also costly product failures and recalls are prevented.
In addition, advances in tension testing technology have made the process more efficient and accessible. Testing systems that are equipped with automated features and advanced data analysis software enable more accurate and repeatable results to be obtained with a minimum amount of manual intervention. This makes tensile testing an integral part of quality assurance in many industries.
Choosing the right equipment is a necessity if you intend to conduct tensile tests. At TensileMill CNC, we offer top-of-the-line products such as the TensileMill CNC MINI for compact and efficient specimen preparation and the SHM Class A Series - Servo-Hydraulic Universal Testing System for high-precision testing applications. Our machines are designed to comply with international standards and provide accurate, reliable results.
Our goal at TensileMill CNC is to help you achieve excellence in testing tensile strength. Contact us directly or request a quote to learn more about our products and services. Our team is here to assist you with any questions and provide the support you need to implement effective tensile testing procedures. Looking forward to partnering with you on your path to success in manufacturing!