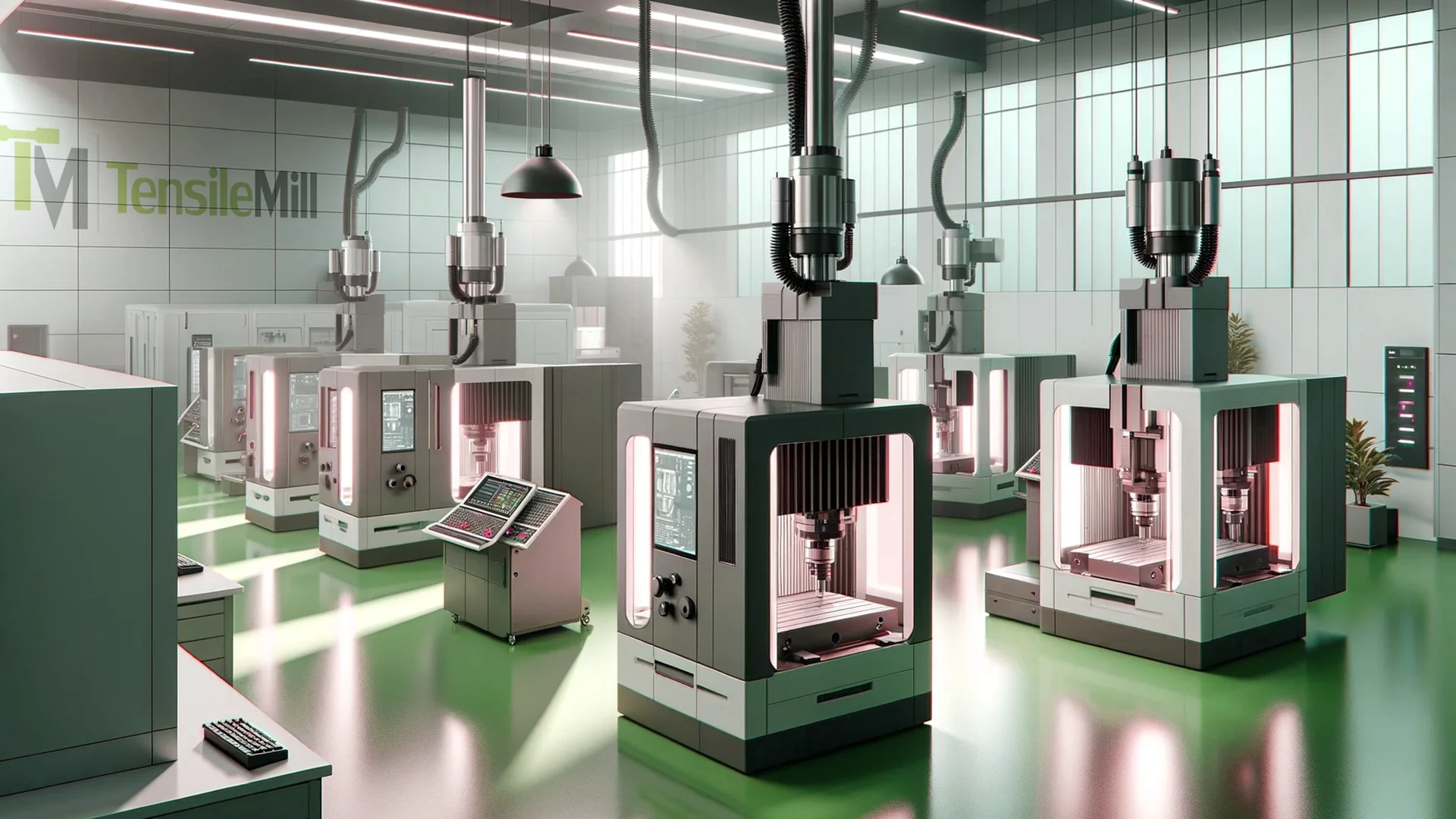
Have you heard of computer numerical control machines? CNC (Computer Numerical Control) machines are advanced tools that use computer programming to control machining operations. Their impact has been felt across a broad range of industries. The introduction and widespread use of these tools have fundamentally altered how materials are processed, shaped, and ultimately products are made. However, many people remain uninformed about CNC machines despite their widespread use in factories and businesses. Having a clear understanding of why CNC machines have become such a turning point in manufacturing, particularly their key advantage of automation, is essential.
Manufacturing and production have undergone a major shift due to industrial automation. Using a control system, such as a computer or robot, and information technologies, in an industry replaces a human worker in handling different processes and machinery. Many production processes use it in a range of industries. Increasing the efficiency of manufacturing production, improving product quality, reducing manufacturing times, and ensuring workplace safety are just a few advantages of industrial automation. The use of automated systems can minimize human errors and increase productivity by automating repetitive tasks.
In this blog, we will explore the impact of CNC machining on industrial automation. We will discuss how CNC technology has revolutionized manufacturing processes, resulting in greater precision, efficiency, and flexibility. Understanding the role of CNC in contemporary manufacturing will provide insight to anyone curious about technological advancements shaping our modern lives.
Understanding Basics of a CNC Machine
We must first establish a foundational understanding of what CNC machining is and why it's so revolutionary in the field of industrial automation before we proceed. First, let's explore the basics of CNC machining, followed by a look at the recent advancements that have enhanced its efficiency and precision. Additionally, we need to understand what CNC machines are and why CNC technology is so important to understand why this kind of equipment is so beneficial.
Definition and Working Principle
CNC machining is a manufacturing process in which computers control machine tools. Lathes, mills, routers, and grinders can all be controlled in this way. CNC stands for Computer Numerical Control, a technology that uses computerized controls and machine tools to remove layers of materials from a stock piece, known as a blank or workpiece, to create a custom-designed part.
The process begins with the design of a 3D model in a CAD (Computer-Aided Design) software. Afterwards, the model is converted into a CNC program (G-code and M-code) that instructs the machine on how to produce the desired part. After checking the model for errors, advanced software plans the path the tool will follow. To produce the part, the machine executes these commands.
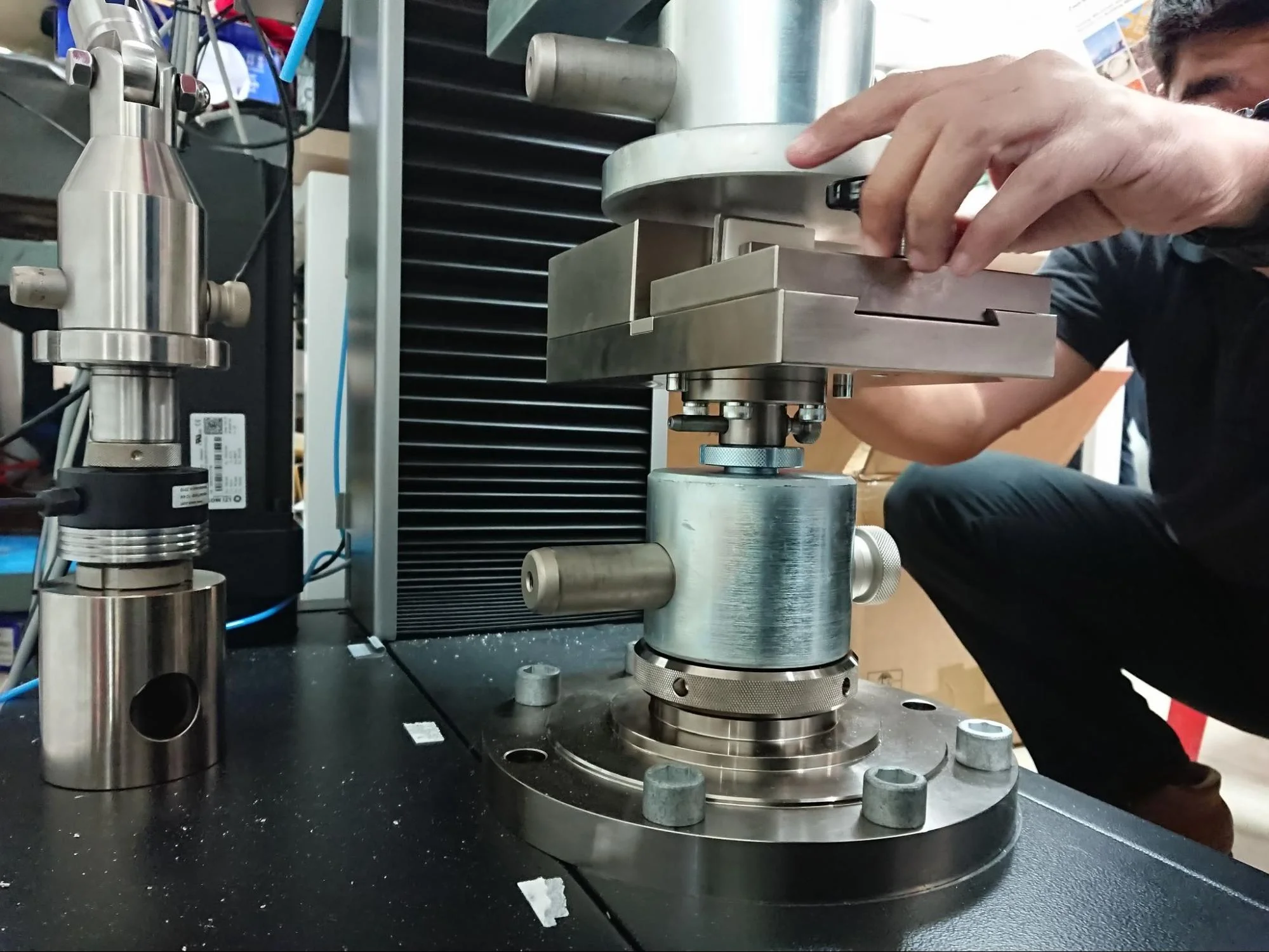
Types of CNC Machines
A CNC machine can be classified into several types, each designed for a specific manufacturing purpose. These include:
- CNC Lathes and Turning Machines: These machines are primarily used to produce round or cylindrical parts. In addition to being highly efficient when machining symmetrical shapes around an axis, they are also very accurate. CNC lathes are commonly used to make shafts, hubs, and bushings.
- CNC Milling Machines: CNC milling machines are versatile machines used for machining complex shapes and features. Their capabilities include drilling, cutting, and shaping. Manufacturing industries such as aerospace, automotive, and electronics rely on CNC milling machines for creating detailed components and even samples for material testing.
- Plasma and Laser Cutters: These machines are specialized for cutting materials with high precision, such as sheet metal fabrication. With their precision and speed, they can cut through a wide range of materials, including metal, plastic, and composites.
- CNC Routers: Usually used to cut softer materials like wood, plastic, and foam. It is very common for CNC routers to be used in woodworking, sign making, as well as in the production of decorative panels and doors.
- EDM Machines (Electrical Discharge Machining): These machines cut conductive materials using electrical discharges. In mold-making, tool-making, and die-making, they're known for producing complex geometries with high precision.
Advancements in CNC Technology
Over the years, CNC technology has significantly enhanced machining processes, making them more efficient, precise, and adaptable. Manufacturing and product development have been revolutionized by these innovations, ranging from rapid prototyping to environmental sustainability. Here are a few of the most important advancements:
- Rapid Prototyping: Rapid prototyping enables the rapid creation of physical models from digital designs, crucial for validating designs before mass production. CNC machines ensure accurate replicas of products, aid in the early detection of design flaws and impove efficiency and cost.
- Advanced Software Integration: By combining computer-aided design (CAD) and computer-aided manufacturing (CAM) software with CNC machines, complex designs can be created and simulated. Boosting overall production efficiency, this integration minimizes errors, enhances design accuracy, and automates machine operations.
- High-Precision Tooling Innovations: Using advanced materials such as polycrystalline diamond (PCD) and cubic boron nitride (CBN), advanced tooling has brought unprecedented accuracy and quality to machining. Implementing these innovations allows CNC to create intricate parts and handle tough materials more effectively.
- Enhanced Machine Learning and AI Integration: AI and machine learning are integrated into CNC systems to optimize operations, reduce tool wear, and increase efficiency. In large-scale production settings, AI's predictive maintenance capabilities are particularly useful.
- Internet of Things (IoT) Connectivity: CNC machines with IoT connectivity enable smart factories, where interconnected devices facilitate data sharing, real-time monitoring, and rapid response to production changes. Connectivity also facilitates predictive maintenance.
- Environmental Sustainability: CNC advances promote recycling and reuse of materials, reducing energy consumption and waste. This aligns with sustainable manufacturing practices.
- Customization and Flexibility: CNC machines are highly adaptable, capable of handling diverse materials and catering to both small-scale custom projects and large production runs, opening doors to a broad range of industries.
Economic Transformation through CNC Automation in Manufacturing
The automation of CNC machines has a significant and multifaceted economic impact in the manufacturing industry. Numerous industries have been transformed by CNC technology, resulting in enhanced efficiency, productivity, and quality.
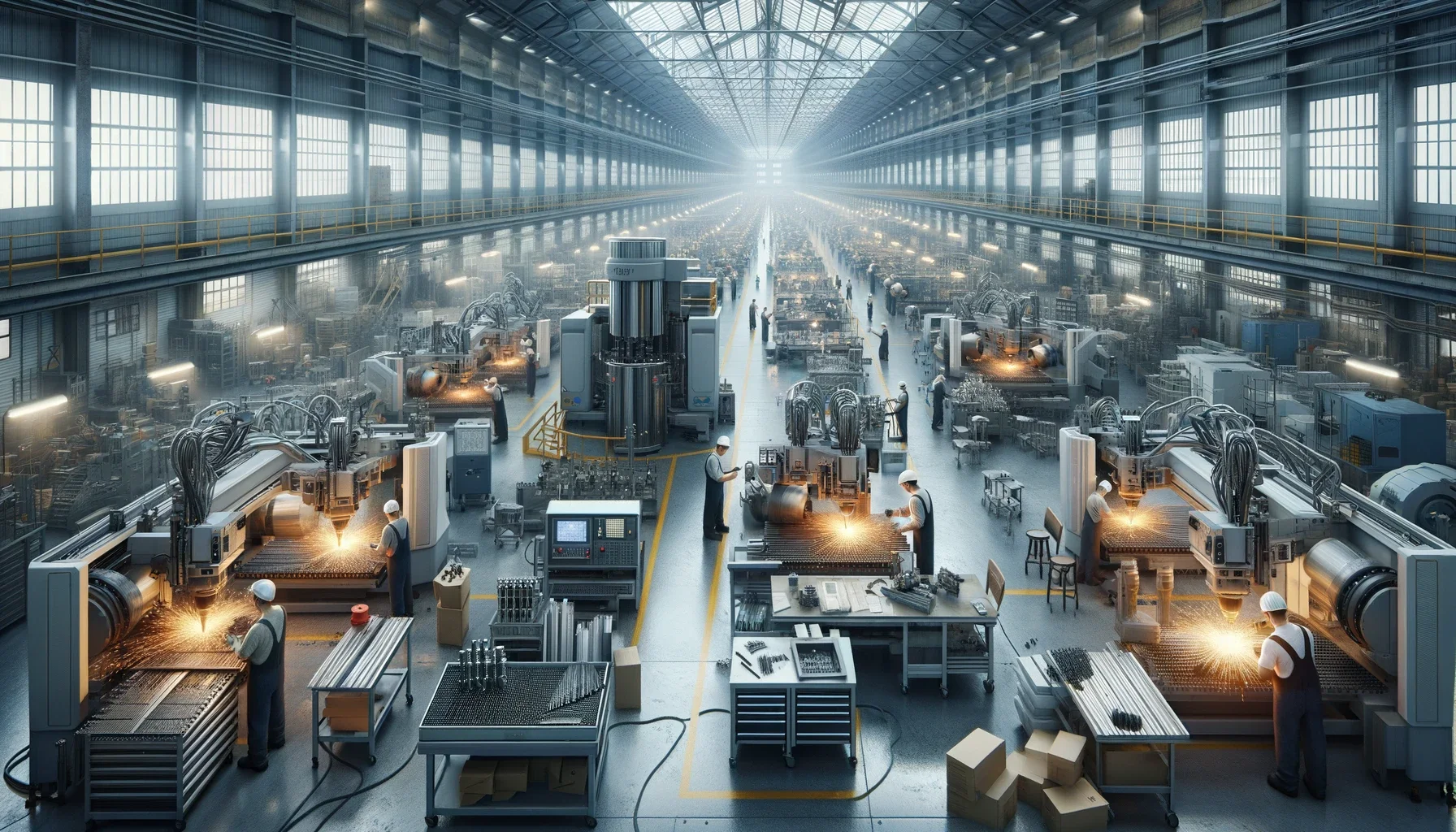
First of all, the CNC machine market has been experiencing substantial growth. The market value was approximately USD 86.83 billion in 2022, and is expected to reach about USD 140.78 billion by 2029, reflecting a compound annual growth rate (CAGR) of approximately 7.1%. The growth can be attributed to the increasing demand for precision products across a number of industries, including automotive, aerospace, and healthcare. By automating manufacturing processes, CNC technology reduces operating costs, maximizes manpower efficiency, and minimizes errors.
As for labor market effects, this technological shift has altered the labor market by increasing the demand for highly skilled workers to operate a CNC machine. As a result of this shift in labor demand, capital expenditures, value added, and labor productivity have increased significantly. Changing manufacturing conditions necessitates new skills and competencies for the workforce. CNC technology has driven economic growth, improved production efficiency, and reshaped workforce dynamics, reflecting a transformative era in industrial manufacturing as a result of this evolution.
CNC automation affects more than just the manufacturing processes. Technology has enabled manufacturers to explore new markets and innovation. Furthermore, the shift towards automation is driving investments in education and training programs to train CNC-savvy workers. Adapting to changing technological landscapes reflects the need for future-proof industries. As a catalyst for industrial evolution and economic growth, CNC automation has become increasingly important in global manufacturing trends.
From Simple Machines to CNC Mastery
We cannot imagine our lives without automation, which has become a fundamental aspect of our daily lives. Its roots date back centuries, evolving from simple mechanical devices to today's complex, interconnected systems. At first, the process was more about automating repetitive tasks, such as looms for textile manufacturing in the 18th century. A significant leap was made during the Industrial Revolution when machinery introduced significant changes in manufacturing and labor. The 20th century, however, saw the true emergence of automation with the advent of electronic and digital technologies.
In the latter half of the 20th century, computers and robotics marked a turning point. As a result of these technologies, industrial processes have become more automated, more consistent, and safer. The development of CNC machining, the crowning achievement of industrial automation, was a significant landmark.
CNC Automation: Reducing Human Error and Expanding Accessibility
In the past, industries relied on highly skilled craftsmen to create parts and components. The process was labor-intensive, time-consuming, and highly dependent on human expertise and precision. Even skilled workers faced challenges maintaining consistency. Often, newcomers and less experienced workers struggle to achieve the required precision, thus limiting their ability to contribute effectively to manufacturing.
CNC machining has changed the face of manufacturing forever. By automating cutting and shaping processes, CNC technology significantly reduces the risk of human error. To create parts with exceptional accuracy, these machines follow precise digital instructions.
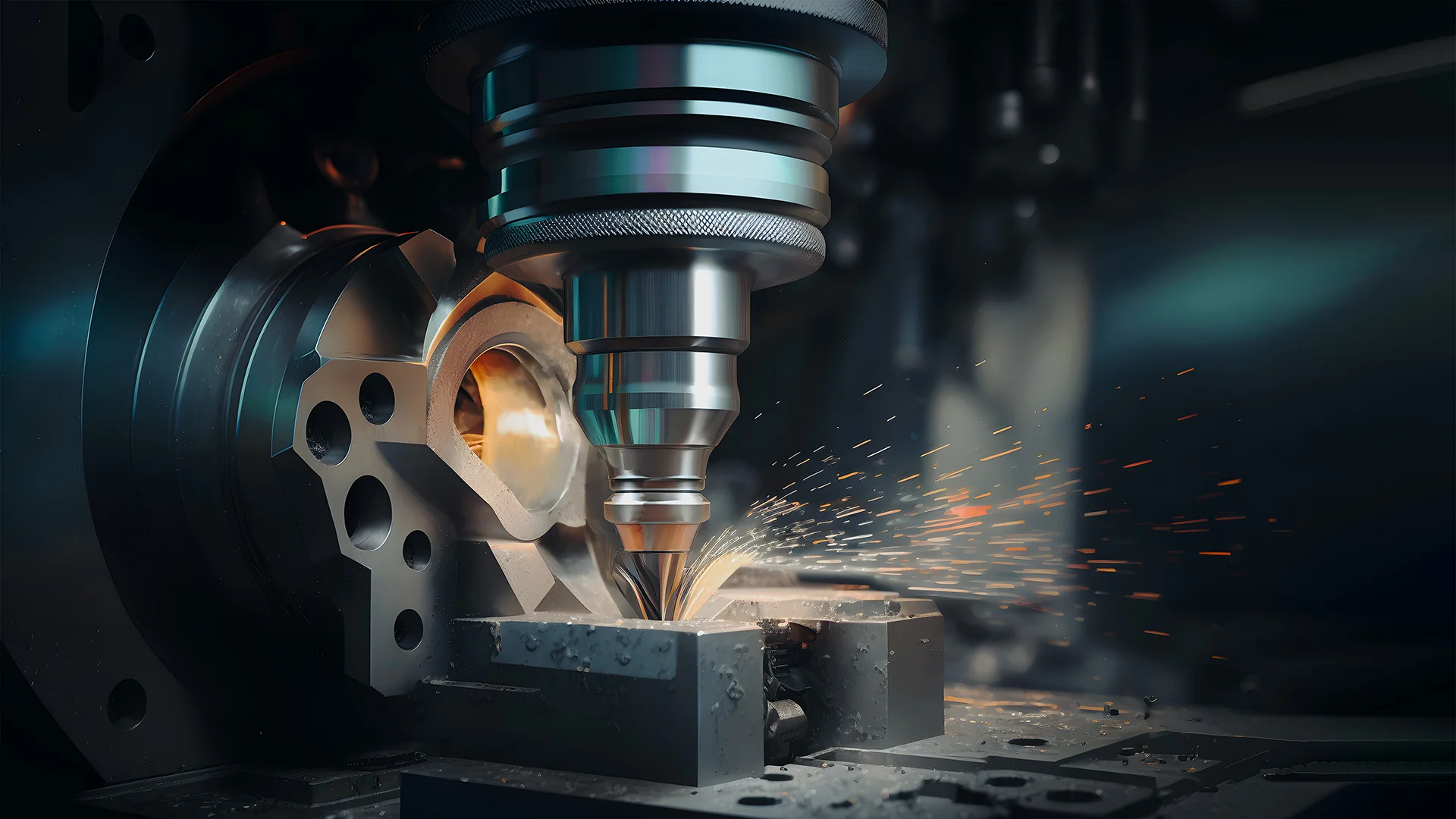
A CNC machine also simplifies the manufacturing process. Unlike traditional machinists, they do not require operators to be skilled or experienced. Basic training is enough for new CNC operators to handle the operations of a CNC machine since a CNC machine can automatically cut complex shapes. The precision, efficiency, and accessibility of CNC technology have made it a cornerstone of modern industrial automation!
CNC Machine Automation Benefits in Examples
To better understand the impact of CNC machines on industrial automation, consider the case of a businessman who runs a small company specializing in chair production, especially metal frames and legs for chairs. Crafting these frames manually with traditional techniques is a labor-intensive and time-consuming task, requiring continuous hands-on involvement and presenting potential safety risks. The quality of the final product heavily relies on the expertise and precision of the craftsmen or the operators of conventional machinery used for cutting and shaping metal. This scenario highlights the challenges faced in traditional manufacturing, especially in small-scale businesses.
Using an automated CNC machine will change this dynamic. A metal block can be processed perfectly by the machine once it has been set up by the operator. Using this setup reduces physical labor and the requirement for highly skilled operators, as well as safety risks. Also, CNC automation significantly increases productivity. Thanks to automation, a CNC machine can make 10 components in the time it takes to make 1 manually.
Besides time efficiency, CNC automation provides high precision and consistency. A near-exact replica of every part produced is critical for products that require uniformity, such as chair frames and legs.
A CNC machine can also work with an array of materials and designs, offering flexibility that traditional methods cannot match. Companies that produce different types of products or bespoke items benefit from this versatility.
Lastly, a CNC machine can provide substantial long-term cost savings. Despite higher initial investment costs, efficiency, reduced labor costs, and lower error rates result in significant savings over time. Business owners looking to scale up operations without proportionally increasing their workforce will find CNC machining an attractive option.
The Role of CNC Machines in Choosing the Right Material
Let's take our businessman, in the chair manufacturing industry, as another example to help better understand. In the end, he constructs a chair. But even a modest weight of 30 kg is too much for the chair - the frame gives way, and the legs begin to diverge. Here, the challenge isn't just about design. It's about choosing the right material. Frames made from metal should be capable of supporting significant loads without being bulky. Increasing the diameter of chair legs that are less than 1 inch might not be feasible. This is where material testing, especially tensile testing in this case, becomes invaluable.
Now let's discuss how a CNC machine can help not only in the manufacturing of a product but also in the selection of the right material for that product. We will show from start to finish how these tools can help a businessman in the chair manufacturing industry choose the correct material for his products, making sure they are durable and capable of withstanding greater weights than expected.
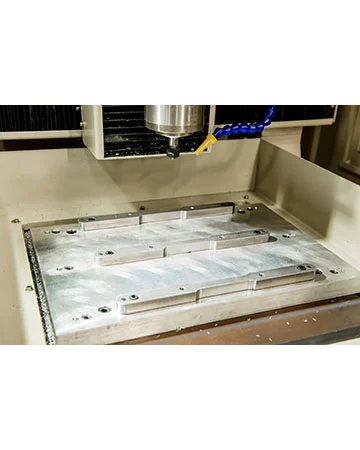
Beginning of the Material Selection Procedure
In our case, the chair material must be tested for tensile strength to guarantee parts like the chair legs can withstand loads. Creating a tensile sample is the first step in this testing process.
The CNC machine which suits best to prepare tensile samples is an automated tensile sample preparation machine. Such a machine can produce flat (also known as dogbones) and round specimens of specific shapes.
Our Solution for Tensile Sample Preparation with CNC Technology
As a company that specializes in this technology, we offer tensile sample preparation CNC machines. In order to prepare flat tensile specimens efficiently and precisely, we offer a Compact Flat Tensile Test Sample Preparation Machine that features several key features. A small footprint makes it ideal for a range of workshop spaces, and its exceptional user-friendliness makes it suitable for operators of any skill level. High-quality tensile tests require accurate and repeatable results, which the machine provides. The device has a 10" LCD screen and intuitive Tensile Software for easy operation and quick setup based on various industry standards.
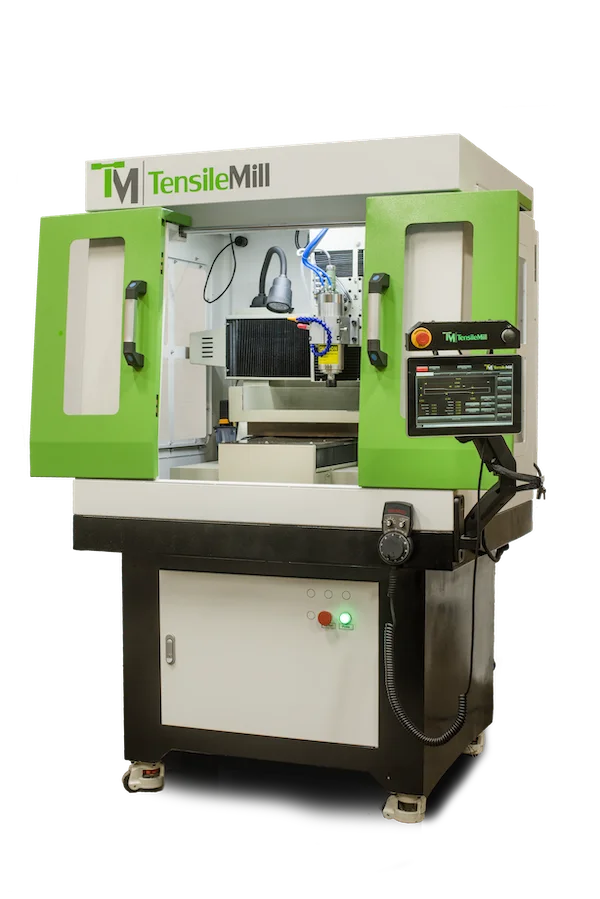
As an alternative, our Round Tensile Test Sample Preparation Machine is designed specifically to prepare round specimens. One of the many features are precision and user-friendliness. The machine is capable of handling a variety of round specimen sizes and types, it also has an interface that facilitates easy testing processes for operators of all levels of experience.

Manufacturers can determine the right materials for products like chair legs easier with our advanced CNC machines for sample preparation. Our machines produce precise and consistent tensile test samples,ensuring that the selected materials will meet quality and longevity standards.
Finishing the Material Selection Procedure
Typically, Universal Testing Machines (UTM) are used to test the tensile samples after they are prepared using a CNC machine. UTMs are essential in measuring tensile strength, elasticity, and durability of materials. By applying force to the sample and measuring its response, they determine how the material will behave under different conditions. It is the final step of the tensile testing procedure when our chair manufacturing businessman selects materials that are aesthetically pleasing but also durable and safe. Material testing, facilitated by UTMs, is a common practice in many industries.
In addition to our CNC machines, we also offer UTMs that are suitable for testing tensile samples. The combination of these technologies offers a comprehensive approach to manufacturing, from material selection to final product testing.
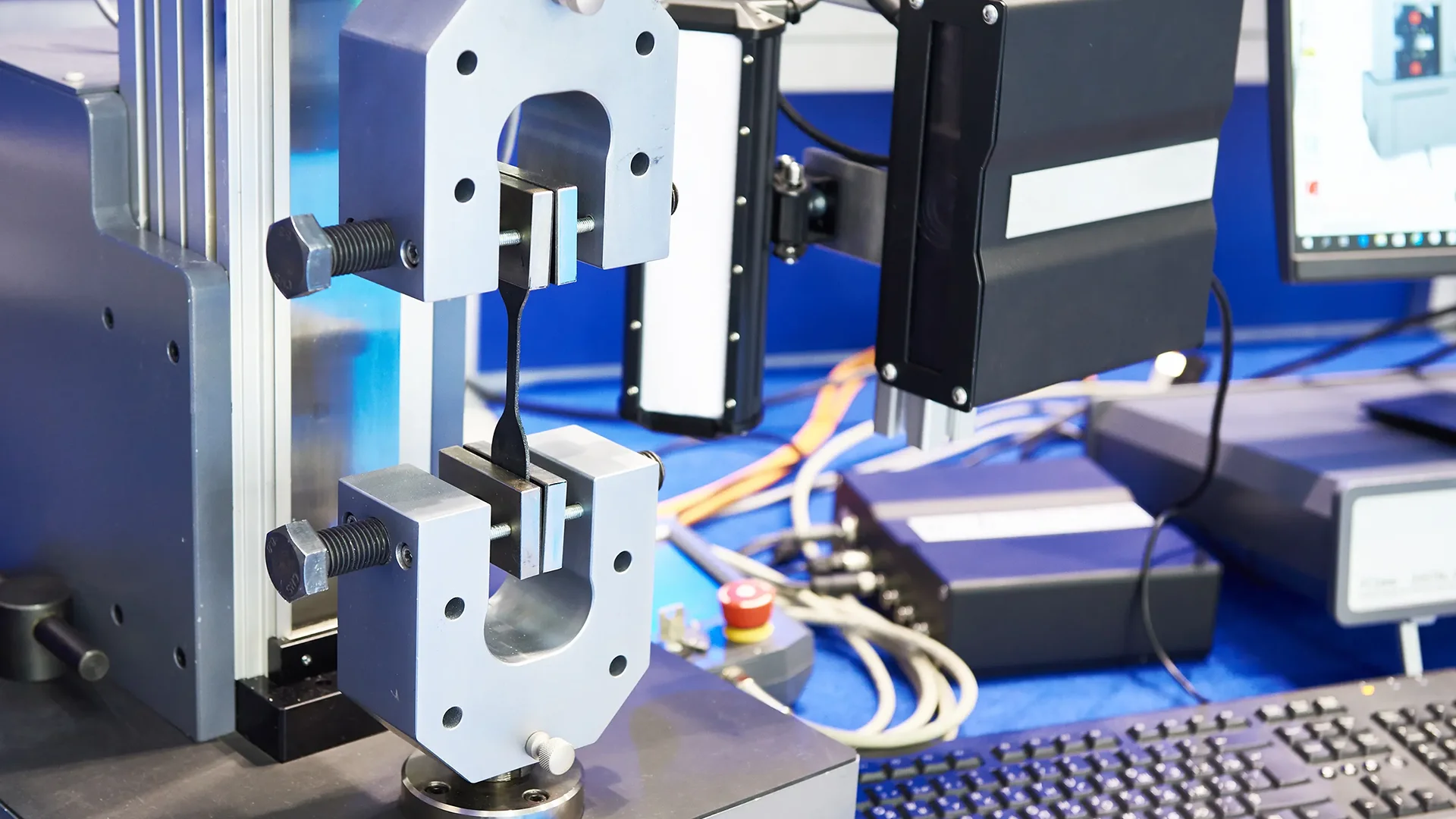
The Transformative Power of CNC Machining in Industrial Automation
As we can see from this blog, CNC machining is a key advancement in industrial automation that is revolutionizing manufacturing across a broad spectrum of industries. Computer-controlled processes have improved precision, efficiency, and flexibility in production. Machines such as lathes, milling machines, plasma cutters, and EDM machines cater to a broad range of materials and design requirements.
In addition to technical improvements, CNC machining drives substantial economic growth. By 2029, the CNC machine market is projected to substantially grow from its 2022 value, driven by rising demand in the aerospace, automotive, and healthcare industries. CNC technology facilitates this growth by automating complex processes, reducing labor costs, and minimizing errors.
The automation of CNC machines also reshapes the labor market, shifting the demand for skilled workers capable of operating advanced machinery. There is no doubt that CNC technology has revolutionized manufacturing, while reshaping production dynamics, fostering innovation, and propelling economic growth.
Automated systems have evolved from simple machines to advanced CNC systems. Automation replaces labor-intensive processes, reducing human error and expanding manufacturing capabilities. CNC machines facilitate all the necessary processes, such as materials selection, testing, and manufacturing.
For anyone interested in the technological advancements shaping modern manufacturing, understanding CNC machining is essential. From soil and concrete testing to sophisticated material analysis in laboratories, these machines ensure quality and safety. We provide durable, precise, and easy-to-use tensile testing equipment, including specimen preparation machines and universal testing systems. To learn more about TensileMill CNC's innovative CNC solutions and their impact on material testing, please contact us.