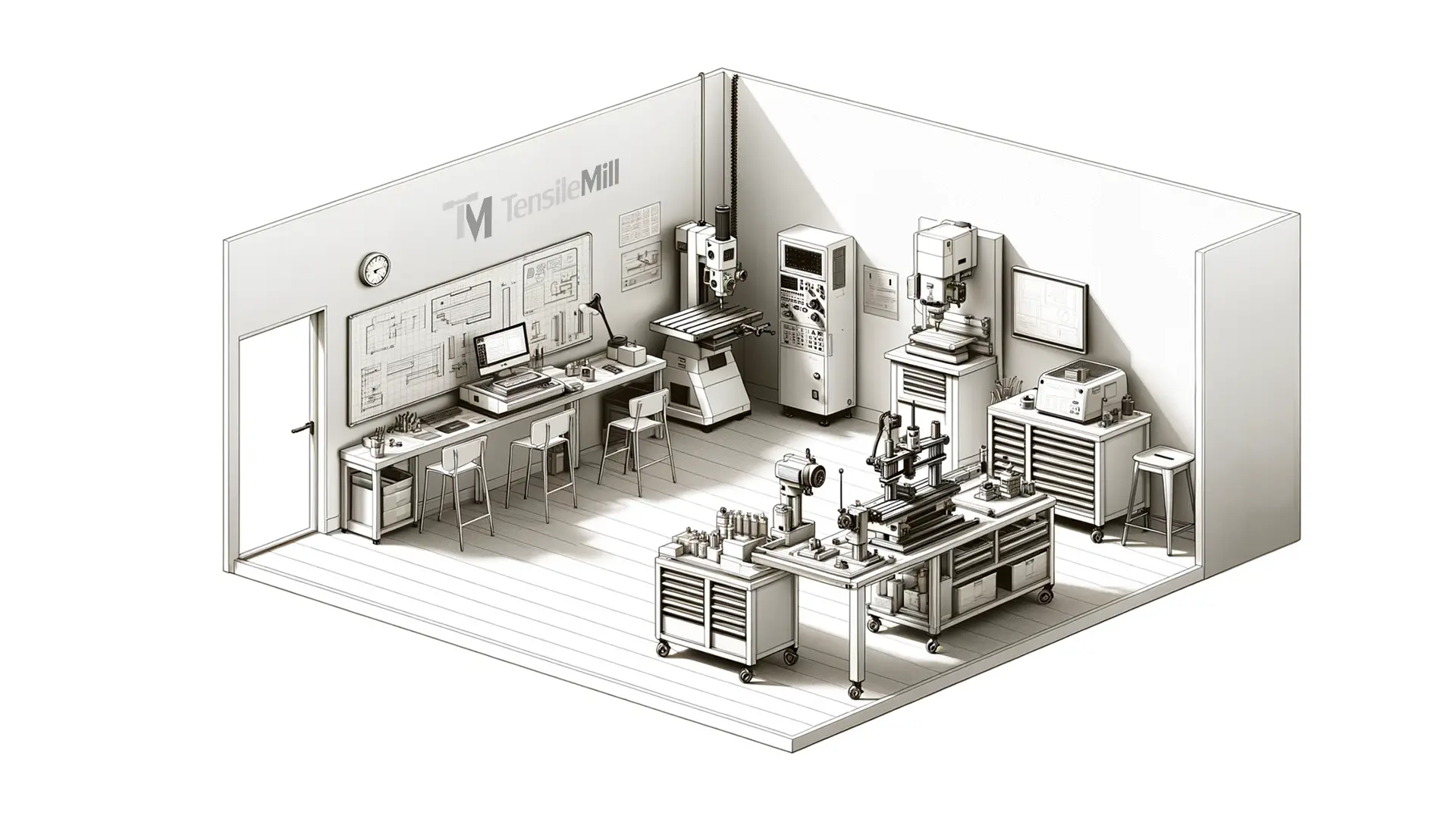
The process of preparing a tensile specimen is key to the testing of reliability and accuracy. Minor imperfections or deviations in specimen preparation can significantly impact test outcomes' validity, leading to potentially misleading conclusions.
Different jobs require different types of end mills, and the choice depends on the specifics. By analyzing the specimen information provided, we can determine the most suitable end mills for your project's unique demands.
Moreover, the approach taken in preparing and handling the specimen is key. Besides selecting the right tools and conditions for machining, this process also involves careful management of consumables used in preparation. Consumables such as cutting fluids, abrasives, and coolants are vital to preventing surface defects, ensuring dimensional accuracy, and preventing material alterations that could affect tensile testing.
Here's a closer look at each component in the tensile specimen preparation process, starting with consumables and their importance in maintaining sample integrity.
Understanding Tensile Sample Preparation Consumables and Edge Quality
Tensile specimen preparation techniques have evolved significantly over the years. Eccentric presses were traditionally used, but they often caused considerable edge damage to specimens. To mitigate the effects of this method, additional processes such as cold working had to be used. This method caused compression, deformation, and an undesirable level of hardening.
While cold working strengthened specimens by applying mechanical stress in a cooler environment, it had drawbacks as well. For most applications, it made the materials brittle and lowered their yield strength significantly.
Today advances in preparation technology have led to more refined methods that minimize damage and preserve the integrity of the material. The mechanical properties of specimens can be maintained through precision and controlled conditions in modern techniques. Cutting tool materials and coatings have improved edge quality and specimen consistency by reducing thermal and mechanical stresses during specimen preparation.
Furthermore, computer-controlled machining processes enable unprecedented precision in specimen shaping, guaranteeing that each sample adheres strictly to the required dimensions and tolerances. Tensile testing results are more reliable when there is this level of control between specimens.
At TensileMill CNC Inc. we take pride in offering specialized consumables for tensile specimen preparation. By perfectly complementing our end mills, we can guarantee a high level of accuracy and reliability for our specimens.
Advantages of CNC End Mills in Precision Sample Preparation
CNC end mills stand out as the preferred solution for tensile sample preparation. Unlike traditional methods such as cold working, laser cutting, or plasma cutting, which often compromise specimen integrity through deformation or excessive heat, CNC end mills like those from TensileMill CNC offer a technologically advanced, non-invasive approach to specimen preparation.
CNC end mills excel at maintaining the original properties of the material by minimizing heat transfer and using advanced cooling techniques. These machines utilize an advanced coolant system that lubricates the cutting surface and regulates temperature. As a result, the sample's physical and mechanical properties remain unchanged. Material that is sensitive to temperature and mechanical stress needs this feature.
CNC end mills are also versatile. These machines can prepare specimens with exceptional precision, handling an array of materials, including metals, plastics, laminates, acrylics, and composites. CNC end mills are indispensable in lab settings, catering to a wide array of tensile testing requirements.
Furthermore, the integration of CNC technology with tensile sample preparation ensures compliance with global standards. CNC end mills comply with ASTM, ISO, JIS, DIN, and other industry standards, helping organizations meet international market demands.
Additionally, advances in CNC end mill technology and consumables have further refined specimen preparation. The development of advanced tool materials and innovative coatings has reduced wear and extended the life of endmills, making them a more cost-effective and reliable choice for laboratories seeking the highest degree of accuracy and efficiency.

The Role of Flute Count and Tool Material
When selecting the right end mills for tensile specimen preparation, understanding the nuances of flute count and the tool material - be it ferrous or non-ferrous - is crucial. Performance, durability, and efficiency of CNC end mills are influenced by these factors, which impact both the quality of the specimen and the efficiency of the operation.
End Mills with a higher flute count, typically between 5 and 8 flutes, are designed with a larger core size. This design choice enhances the tool's strength, making it more capable of cutting tough materials. In contrast, tools with fewer flutes, such as 3-flute designs, offer larger flute valleys. While these may be less strong, they are better suited to certain applications where chip removal is a priority.
The industry has seen a trend towards end mills with higher flute counts, particularly in the 5 to 7 range. However, some specialized applications may use even more. These tools are often constructed from ferrous materials, which contribute to their longevity and robustness. The choice of ferrous material not only extends the life of the tool but also supports a higher material removal rate (MRR).
Modern coating technologies and the development of new ferrous and non-ferrous materials have further increased the capabilities of CNC end mills. Innovations such as titanium coatings and carbide materials have been introduced to improve wear resistance, reduce friction, and increase tool lifespan. These advancements mean that endmills can maintain their performance over time, even under the stress of high-speed machining and in the presence of hard-to-machine materials.
Along with material and coating innovations, the precise engineering of flute geometry has also advanced significantly. Optimizing the flute shape and angle improves chip evacuation, reduces heat buildup, and minimizes tool wear.
The Value of Precision in Tensile Specimen Preparation
The integrity of tensile testing is equally important in material testing. Industries rely on these tests for assessing product durability and safety for end-users. Accuracy, precision, and repeatability in tensile testing are not just goals but necessities to guarantee product reliability and user safety.
Improper preparation or handling of specimens is a primary cause of compromised tensile test results. A specimen that fails a test can cause catastrophic outcomes. Poor sample preparation can also incur unnecessary costs by failing tests it should have passed, requiring additional specimens to be tested.
Thus, precision in the preparation process is indispensable. The quality of the specimen's cut - free of nicks, indentations, or rough edges - is critical for maintaining tensile strength and achieving consistent test outcomes. Employing quality specimen preparation consumables and precision CNC milling equipment is key to mitigating these issues.
Beyond machinery, operator expertise can make a significant difference in specimen integrity. Proper training in specimen handling is essential. A specimen compromised by mishandling can skew test results, leading to unreliable data.
To achieve a precise and accurate cut, it is critical to use the appropriate end mill along with meticulous handling practices. Each end mill type is suited to a specific material and application, optimizing the cutting process and improving the quality of the specimen.
Learn More About Preparing Tensile Specimens Properly
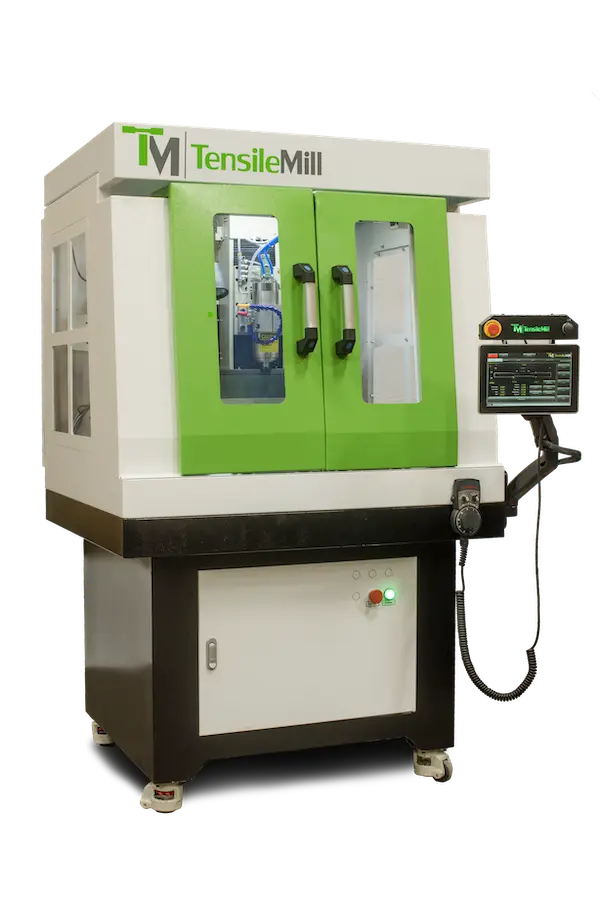
At TensileMill CNC, we lead the way in terms of providing innovative solutions that simplify specimen preparation. Our flagship TensileMill CNC MINI is an example of efficiency and accuracy in the compact tensile test sample preparation market. This machine is not just an asset but a transformative tool designed to meet the exacting demands of modern testing laboratories and manufacturing facilities.
Despite its compact size, the TensileMill CNC MINI delivers performance that belies its size. Its small footprint is a major advantage, offering the high-level efficiency required for precise specimen preparation without occupying significant space. This makes the MINI an ideal choice in any setting, optimizing workspace efficiency while delivering top-tier results.
The machine's design focuses on user accessibility, making it a perfect match for both seasoned and novice CNC machinists. As a turnkey solution, the TensileMill CNC MINI offers simplicity and ease of use without compromising the quality of specimen preparation. This balance between user-friendliness and high performance provides accurate and repeatable results, a critical factor in reliable tensile testing.
Moreover, the option to upgrade to our Carbon software interface expands the MINI's functionality, blending tensile sample preparation with full CNC machining capabilities. This hybrid approach offers new possibilities, allowing more complex and diverse testing scenarios to be addressed with a single piece of equipment.
TensileMill CNC is committed to helping you improve tensile testing processes through innovative and reliable specimen preparation solutions. We encourage you to contact us directly or request an online quote. You will be able to see how the TensileMill CNC MINI can raise your testing capabilities to new heights, ensuring that precision and accuracy are always within reach.