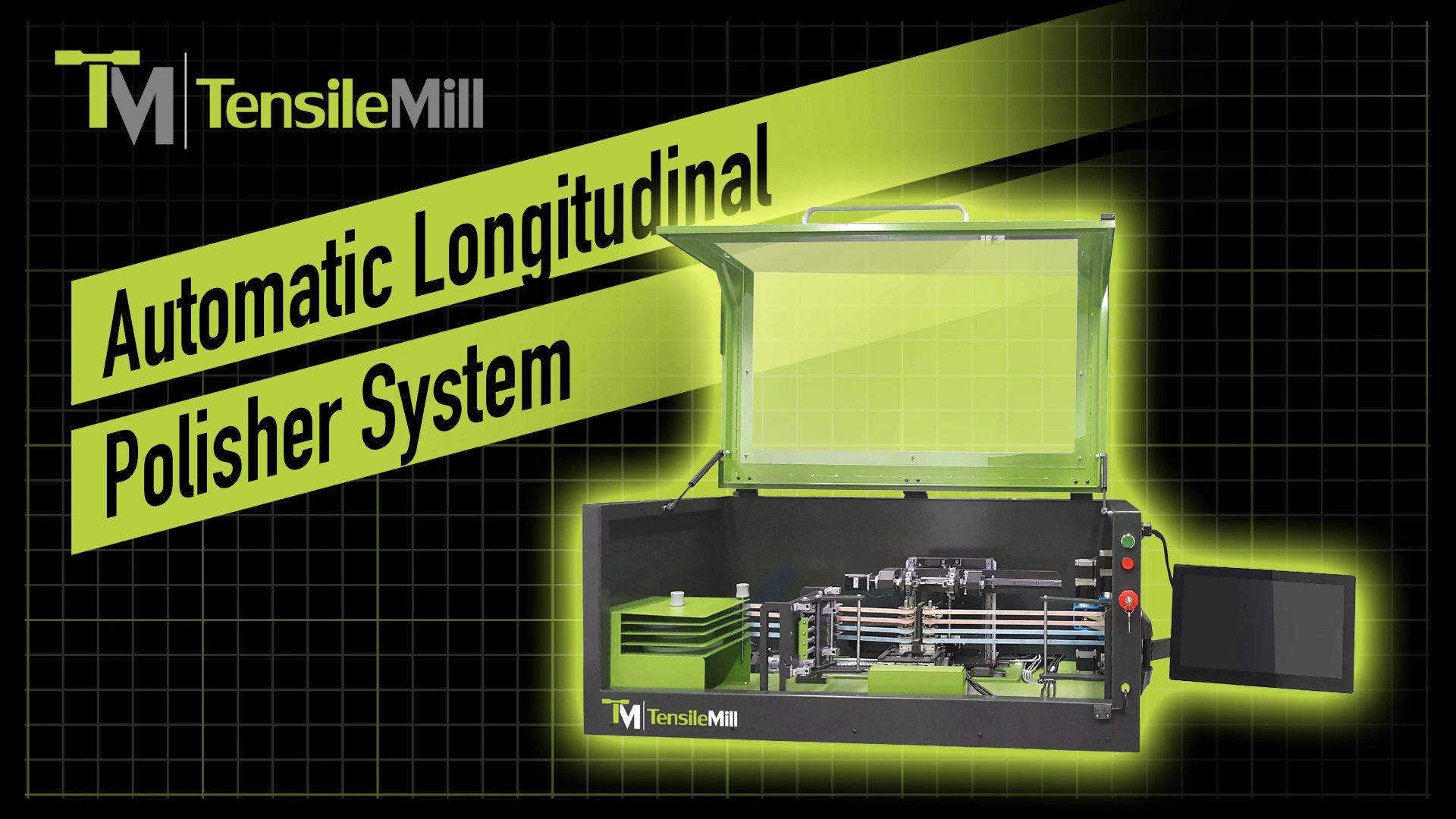
Automatic Longitudinal Polisher System: A Review by TensileMill
In material testing, specimen machining is not the final step in achieving a fully prepared specimen for accurate testing results. Machining processes like turning, milling and grinding, often leave residual stresses and surface finish imperfections that affect test outcomes. Often, imperfections in specimens, whether for tensile testing specimens or other types of samples, need to be corrected.
Surface finishes require a good deal of polishing to achieve the necessary quality. The purpose of this blog is to provide a review of the Automatic Longitudinal Polisher System - TensilePolish GR04, a new tool that automates the polishing process for cylindrical and flat tensile specimens. We will discuss the features, capabilities, industry standards it complies with, and how it can benefit a variety of fields requiring the most meticulous specimen preparation.
General Overview of the Automatic Longitudinal Polisher System
The Automatic Longitudinal Polisher System - TensilePolish GR04 is a cutting-edge solution designed to address surface preparation challenges in material testing. After machining processes such as turning, milling, or grinding, materials often exhibit residual stresses or surface imperfections that can affect test results' accuracy and reliability. The TensilePolish GR04 effectively minimizes these issues by offering automated, precise polishing for both cylindrical and flat specimens, making certain that materials are prepared to exact standards for further testing.
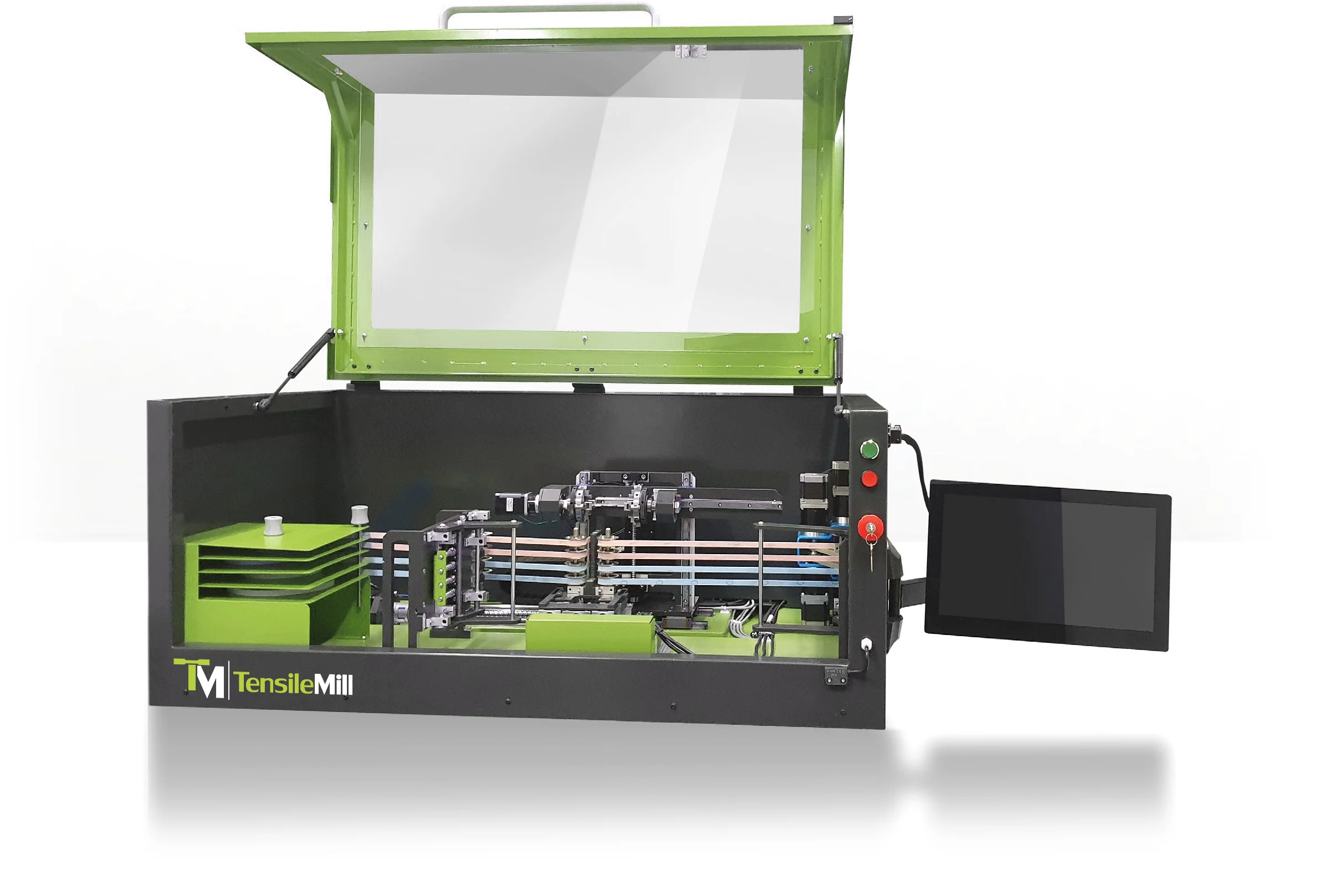
This system is specifically engineered to handle a variety of specimen geometries and sizes, making it highly versatile for industries that require flawless surface preparation. By automating the longitudinal polishing process, the TensilePolish GR04 not only reduces manual workload but also provides consistency in results.
One of the key advantages of the TensilePolish GR04 is its user-friendly design. Equipped with an intuitive touchscreen interface, it allows operators to easily adjust parameters such as force, speed, and polishing length, giving them the flexibility needed for different material types and testing standards. The system's compact, space-saving footprint also makes it an ideal choice for laboratories and facilities with limited space.
Moreover, our longitudinal polisher system supports automatic switching between multiple types of sandpaper during the polishing process, allowing for smooth transitions and reducing manual intervention. This feature, combined with the ability to customize polishing parameters, provides greater control over the final surface quality.
Features and Main Advantages of the TensilePolish GR04
The TensilePolish GR04 comes equipped with a number of advanced features designed to streamline specimen preparation and achieve optimal surface quality. As a result of these features, the system is not only more versatile, but it is also more efficient.
Here are some of its main features and advantages:
Key Features
- Automatic Longitudinal Polishing: The system provides automatic longitudinal polishing, resulting in consistent outcomes by preventing repeated contact between the specimen and the sandpaper. This method reduces surface imperfections, offering a precise and uniform finish across different specimens.
- Customizable Polishing Parameters: The TensilePolish GR04 allows full customization of key polishing parameters, including rotation speed, applied force, and active polishing length. This flexibility enables users to customize the process to suit different specimen types and materials.
- Versatile Sandpaper Options: The machine supports automatic switching between four different types of sandpaper during polishing. This feature allows smooth transitions between polishing stages, reducing manual intervention and assuring that the optimal surface finish is achieved with minimal effort.
Main Advantages
- Low-Stress Grinding and Polishing: Our longitudinal polisher system - TensilePolish GR04 minimizes surface stress by making use of controlled and precise polishing methods. This is critical for maintaining material integrity, especially in specimens intended for high-stress testing environments like fatigue or tensile testing.
- Ability to Handle Various Specimen Geometries: The system polishes specimens of assorted geometries, including both cylindrical and flat tensile specimens.
- Automatic Sandpaper Management: The GR04 has automatic sandpaper changes and cleaning during polishing. This not only saves time but also improves results consistency, as each specimen is polished under identical conditions, regardless of material type or size.
Available Models, System Configuration, and Technical Specifications
The following is a detailed description of the models, the system configuration, and the technical specifications of the Longitudinal Polisher version TensilePolish GR04 for an understanding of its capabilities and characteristics:
Available Models
There are several models of Automatic Longitudinal Polisher System - TensilePolish GR04 that can suit various types of specimen sizes and geometries:
- SCS – Standard Cylindrical Specimen: Suitable for polishing standard cylindrical specimens of varying diameters and lengths, compliant with EN 6072.
- ESCS – Extremely Small Cylindrical Specimen: Specifically designed for very small cylindrical specimens, providing the same precision as for larger specimens.
- ELCS – Extremely Large Cylindrical Specimen: Handles extremely large cylindrical specimens, offering flexibility for large-scale projects that demand high-quality surface finishes.
- FS – Flat Specimen: This model is specifically designed for polishing flat specimens of different sizes, resulting in uniform polishing.
- C – Customized Longitudinal Polisher: Offers customizable options to meet specific requirements, allowing the machine to be customized to unique specimen types or testing needs.
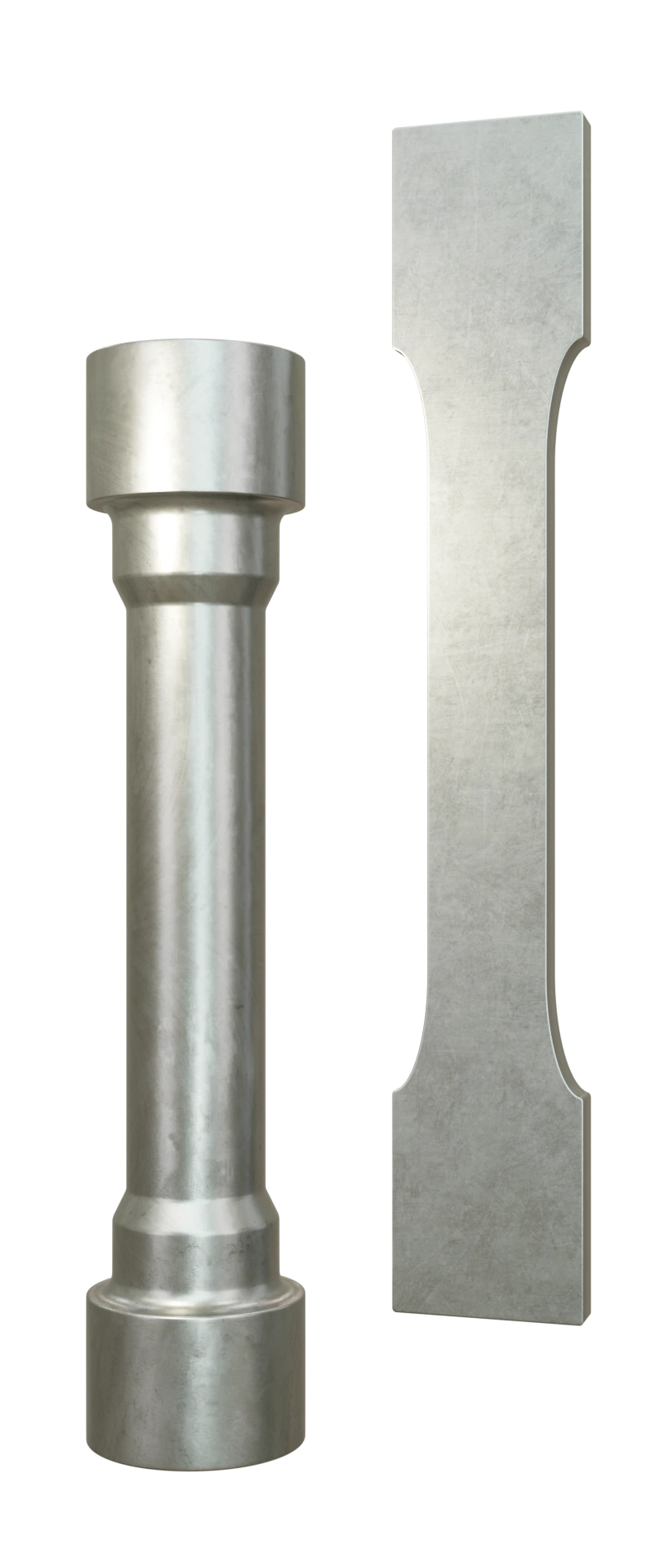
Moreover, all of the standard models of the Automatic Longitudinal Polisher System TensilePolish GR04—including the SCS, ESCS, ELCS, and FS—are fully compliant with the EN 6072 standard. Thus, the system meets the highest industry standards for the mechanical testing of metallic materials, as well as providing consistent and reliable results for every specimen preparation.
System Configuration
The TensilePolish GR04 system comes fully equipped with all the necessary hardware and software for smooth operation, including:
- Main Unit: The core TensilePolish GR04 system is capable of polishing a range of geometries, such as cylindrical and flat specimens.
- Additional Hardware: Tools and attachments for polishing specimens of assorted sizes and shapes, assuring compatibility with different geometries.
- Set of Sandpaper Rolls: A comprehensive set of sandpaper rolls in different grits, allowing users to optimize the surface finish based on material type and requirements.
- User Manual and Instructional Videos: Detailed user guides and videos for setting up and operating the system, making it easy and quick onboarding for new operators.
Technical Specifications
TensilePolish GR04 offers a number of advanced technical capabilities that enhance its performance and adaptability:
- Polishing Force: The sandpaper pushing force is adjustable between 5-50 N, providing flexibility depending on the material and the desired surface finish.
- Speed of Longitudinal Movement: The system allows users to adjust the longitudinal movement of the sandpaper between 10-100 mm/sec, with adjustments available in 10 mm/sec increments for fine control.
- Polishing Length: The active polishing length is adjustable between 5-280 mm, offering compatibility with an array of specimen lengths and geometries.
- Automatic Sandpaper Switching: The machine automatically switches between four different grades of sandpaper (e.g., 200, 400, 600, 800 grit), simplifying the process and making certain that the optimal surface finish is achieved without manual intervention.
- Touchscreen Control: All settings and adjustments are controlled via an intuitive touchscreen interface, making it simple for operators to set parameters, adjust the process, and monitor progress in real time.
Standards Compliance of the TensilePolish GR04
The following is a list of the key standards to which the Automatic Longitudinal Polisher System complies, along with a brief explanation of their significance.
ASTM E466 – Force-Controlled Axial Fatigue Testing Standard
This standard outlines the practice of conducting force-controlled constant amplitude axial fatigue tests on metallic materials. It is commonly used in industries like aerospace, automotive, and manufacturing to determine how materials behave under repeated cyclic loading, simulating real-world conditions. By complying with ASTM E466, the TensilePolish GR04 ensures that specimens prepared using the system are suitable for accurate fatigue testing, contributing to the development of safer, more durable materials.
ASTM E606 – Strain-Controlled Fatigue Testing Standard
ASTM E606 specifies the method for strain-controlled fatigue testing of metallic materials. Unlike force-controlled testing, this method evaluates the material's response to controlled deformation or strain, which is especially important for applications where materials experience significant strain over time. Compliance with ASTM E606 means that the TensilePolish GR04 produces specimens that are precisely polished and prepared for testing in high-strain environments, such as pressure vessels and structural components in the construction and transportation industries.
EN 6072 – Mechanical Testing of Metallic Materials
EN 6072 is the European standard that governs the mechanical testing of metallic materials, particularly the preparation of test specimens for tensile and fatigue testing. It establishes clear guidelines for how specimens should be prepared to provide reliable and comparable results. All models of the TensilePolish GR04 guarantee that cylindrical and flat specimens are polished to meet stringent European testing requirements, which makes them an excellent option for laboratories that must follow international testing protocols.
NADCAP – National Aerospace and Defense Contractors Accreditation Program
NADCAP is an internationally recognized accreditation program that focuses on achieving high-quality standards for aerospace and defense processes. Compliance with NADCAP means that the Automatic Longitudinal Polisher System - TensilePolish GR04 meets the rigorous requirements for material preparation in sectors where safety and performance are paramount. For companies that supply key components to the aerospace industry, even the smallest imperfections in material testing can have significant repercussions.
Bridging Raw Materials and Testing with CNC Machining
Since we are discussing the polishing process for flat and round tensile specimens—which addresses minor surface imperfections—it would be helpful to highlight the significance of their initial preparation. In this process, raw metal bars are formed into standardized shapes suitable for accurate material testing. During this initial phase, the highest level of precision must be achieved using Computer Numerical Control (CNC) equipment.
CNC machines offer exceptional accuracy and consistency, making them ideal for producing specimens that meet strict industry standards like ASTM E8/E8M. They precisely control cutting tools to achieve the exact dimensions and geometries required for both flat and cylindrical tensile specimens. The precision of this procedure provides uniformity between specimens, which is vital for obtaining reliable and reproducible results.
While the Automatic Longitudinal Polisher System aids in removing minor surface imperfections and residual stresses from machined tensile samples, it cannot correct significant machining errors. Therefore, the initial preparation for CNC machines must be flawless. High-quality machining minimizes the risk of defects such as dimensional inaccuracies, tool marks, and micro-cracks, which could compromise the specimen's integrity and affect the accuracy of material testing.
The combination of precise CNC machining and advanced polishing with the TensilePolish GR04 results in specimens of the highest quality. CNC machining provides the exact dimensions and geometries, while the polisher enhances the surface finish and eliminates residual stresses. Together, they guarantee that both flat and round tensile specimens are optimally prepared for testing, resulting in more accurate and reliable data on material properties.
CNC Machines for Precise Flat and Round Tensile Specimen Preparation
At TensileMill CNC, we are known for our reliable CNC machines created specifically for preparing both flat and round tensile specimens. If you are interested in adding a CNC machine to your laboratory that complements the Automatic Longitudinal Polisher System and offers swift, convenient operation, consider our following products.
TensileMill CNC—Classic Upgrade: Flat Tensile and Impact Specimen Preparation
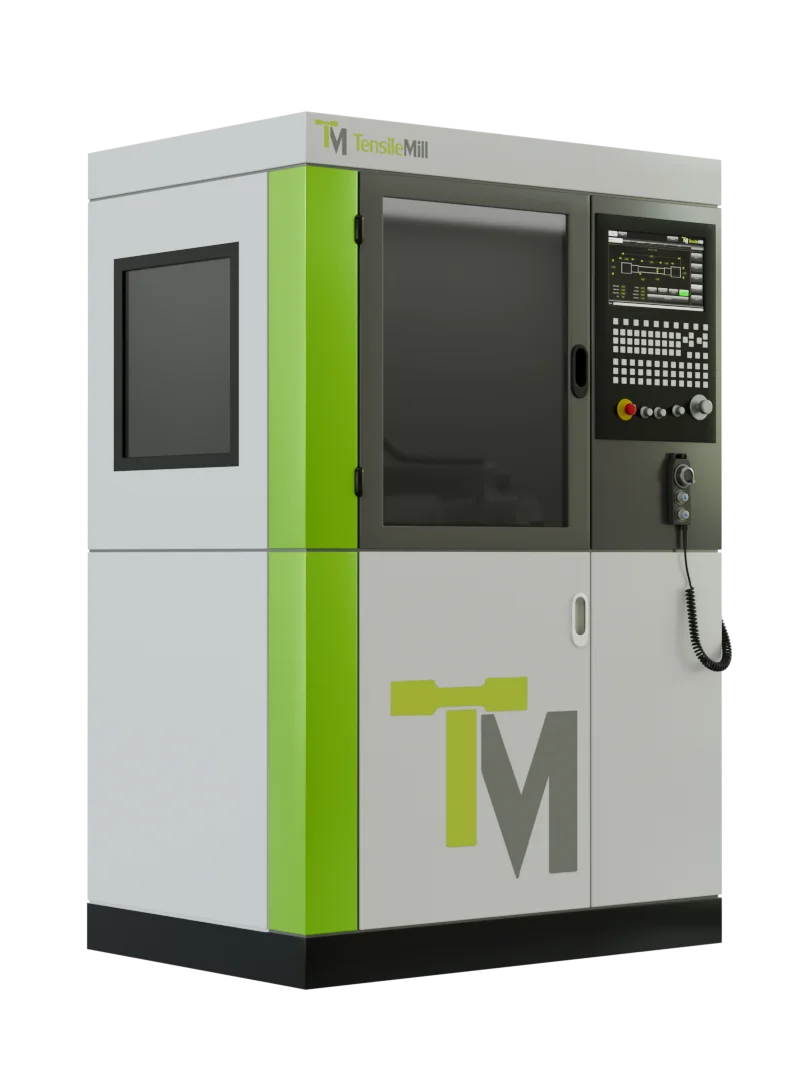
The TensileMill CNC—Classic Upgrade is the world's first machine dedicated to preparing flat tensile and impact test specimens. Featuring our innovative TensileSoft™ interface and Fanuc controller, it is user-friendly for both novice and experienced operators. This machine can process specimens up to 14 inches (350 mm) in length, 2 inches (50 mm) in width, and 0.5 inches (12.5 mm) in thickness, accommodating virtually all ASTM, ISO, DIN, and JIS standards. The system delivers exact specimen dimensions every time, thereby serving as a valuable addition to your material testing equipment.
TensileTurn CNC—Industrial Upgrade: Round Tensile Specimen Preparation
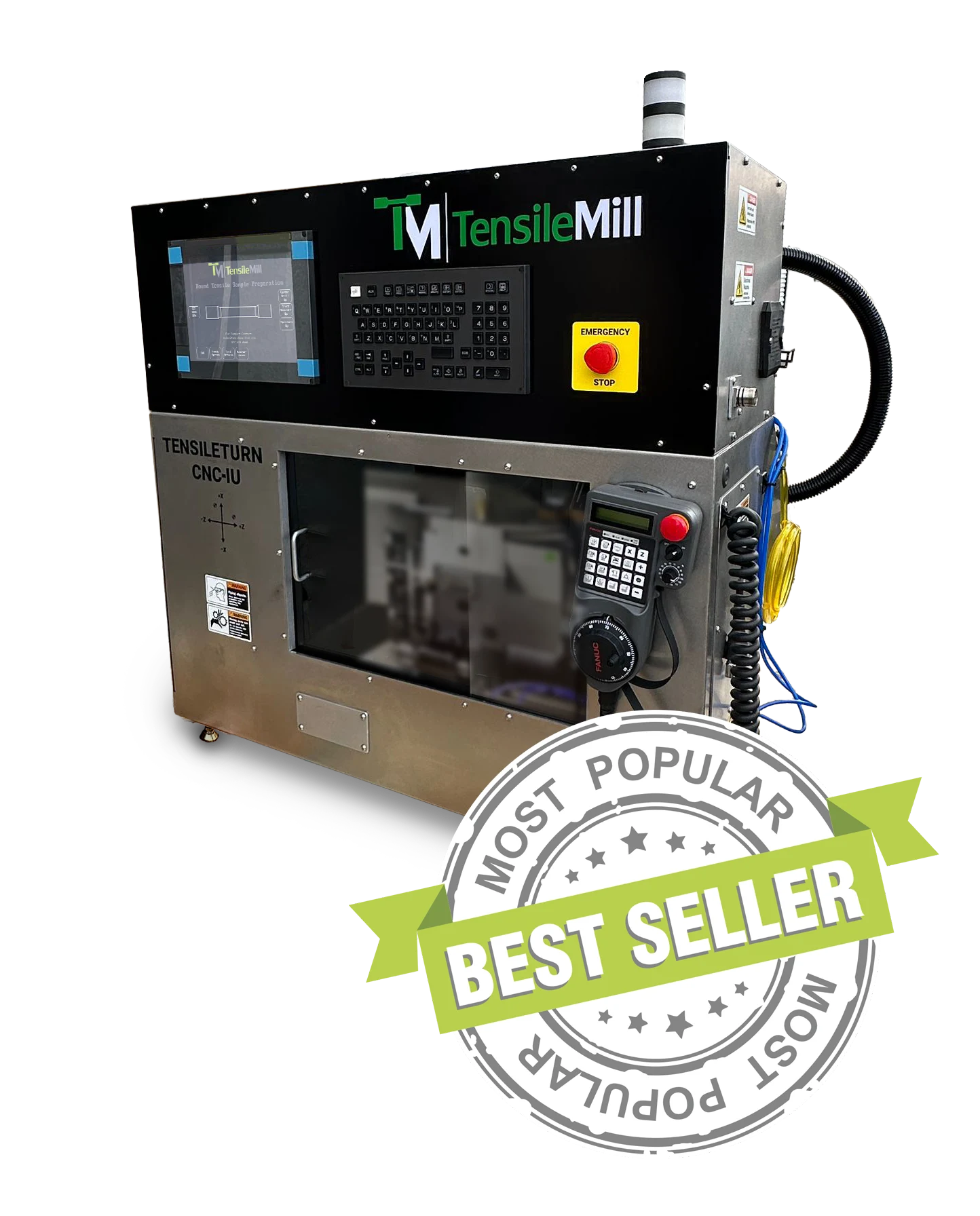
The TensileTurn CNC—Industrial Upgrade is a compact, automatic CNC lathe designed for the precise preparation of round tensile specimens. Equipped with a touch-screen interface and our advanced TensileSoft™ software, it allows operators—with or without machining experience—to quickly prepare specimens to desired specifications. Capable of handling standard round, sub-size, threaded, button-head, and fatigue specimens, this machine simplifies the preparation process, reduces wait times, and increases testing efficiency. A number of features, such as automated center drilling and an 8-position turret, make this machine an excellent asset for any laboratory.
Industries That Can Benefit from the TensilePolish GR04
The TensilePolish GR04 offers tremendous value within a number of high-demand industries, particularly those requiring precise specimen preparation in material testing in order to verify its reliability and safety. The following section breaks down the few industries that can greatly benefit from this advanced polishing system.
Aviation and Aerospace Industry
In both the aviation and aerospace sectors, material performance under extreme conditions has a significant impact on safety and operational success. Aircraft components such as jet engine blades, structural airframe materials, and fuel system components must meet rigorous standards to withstand high levels of stress, pressure, and temperature encountered during flight. In the aerospace industry, materials used in satellite construction, spacecraft shields, and rocket propulsion systems must be tested for their ability to endure space environments, including thermal cycling and radiation exposure.
The TensilePolish GR04 is an essential tool in ensuring testing samples are prepared with precision. By automating the polishing process, the system minimizes human error and results in uniform specimen surfaces, a requirement for high-fidelity test results. This is particularly important in fatigue testing and tensile testing, where surface imperfections could significantly skew results. With the GR04, aerospace manufacturers can polish specimens made from advanced composites, titanium alloys, and superalloys—materials commonly used for their high strength-to-weight ratios and corrosion resistance.
In a sector where even microscopic defects in testing specimens can lead to catastrophic failures, the TensilePolish GR04 is indispensable for validating the structural integrity of components like aircraft wings, fuselage panels, and propulsion system parts. This tool supports stringent testing protocols, helping companies ensure compliance with international safety standards, such as those outlined by the Federal Aviation Administration (FAA) and the European Union Aviation Safety Agency (EASA).
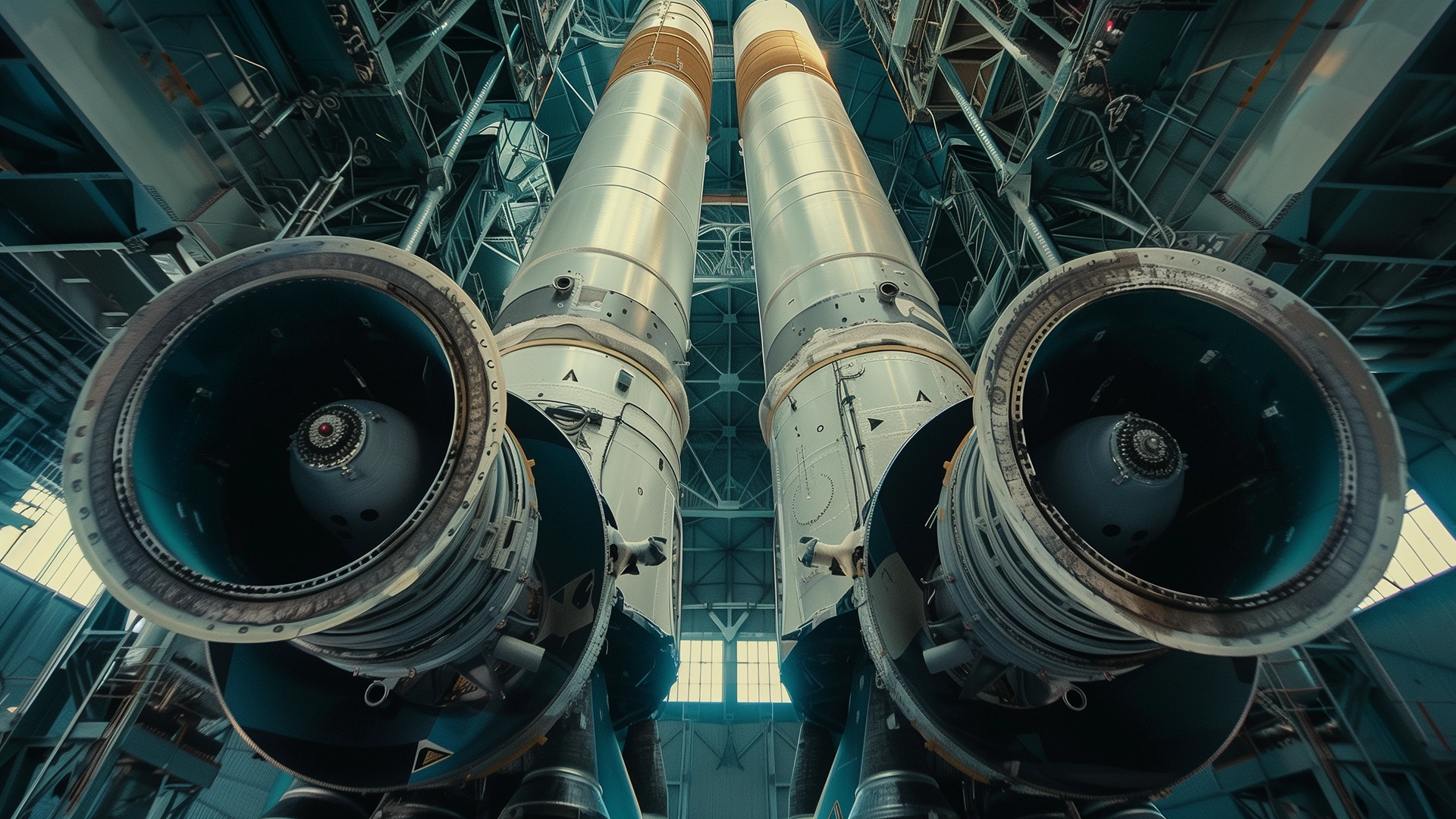
Defense Industry
The defense sector requires materials and components that perform reliably in the most extreme and hostile environments. From ballistic armor plates to missile casings and tank armor, military materials must undergo exhaustive testing to verify that they can withstand high-impact forces, intense heat, and mechanical stress.
The TensilePolish GR04 optimizes the testing process by providing precisely polished specimens free of surface imperfections, thus resulting in accurate and reliable test outcomes. This is especially relevant when preparing high-strength alloys, composites, and ceramics for impact testing or fatigue analysis. The system makes sure that defense contractors can meet the stringent requirements set by military standards such as MIL-STD-810 for environmental and durability testing.
Moreover, components like aircraft carrier parts, helicopter rotor blades, and military vehicle armor are tested for performance under stress using specimens prepared by the TensilePolish GR04. By confirming the integrity of test specimens, the system supports the development of materials that offer both high strength and lightweight properties, critical for modern military applications where mobility and protection are key.
Academic Research Institutions
Universities and research institutions conducting studies in material science, mechanical engineering, and metallurgy rely heavily on precise specimen preparation for experimental work. Research into advanced materials like nanocomposites, smart materials, and high-performance polymers requires accurate testing to validate hypotheses and drive innovation.
The Automatic Longitudinal Polisher System - TensilePolish GR04 allows researchers to prepare specimens with high accuracy, facilitating consistent and repeatable testing. The system's ability to automate polishing reduces manual workload and helps academic labs meet strict research standards. This tool is particularly beneficial for researchers working on projects funded by government grants or industry partnerships, where precision and reproducibility are paramount.
Automotive Industry
In the automotive sector, the durability and safety of vehicle components must be tested rigorously to guarantee optimal performance on the road. With growing trends in electric vehicles (EVs), lightweight materials such as carbon fiber composites and aluminum alloys are increasingly used to improve fuel efficiency and extend battery life. These materials must undergo extensive testing for fatigue resistance, impact tolerance, and mechanical strength.
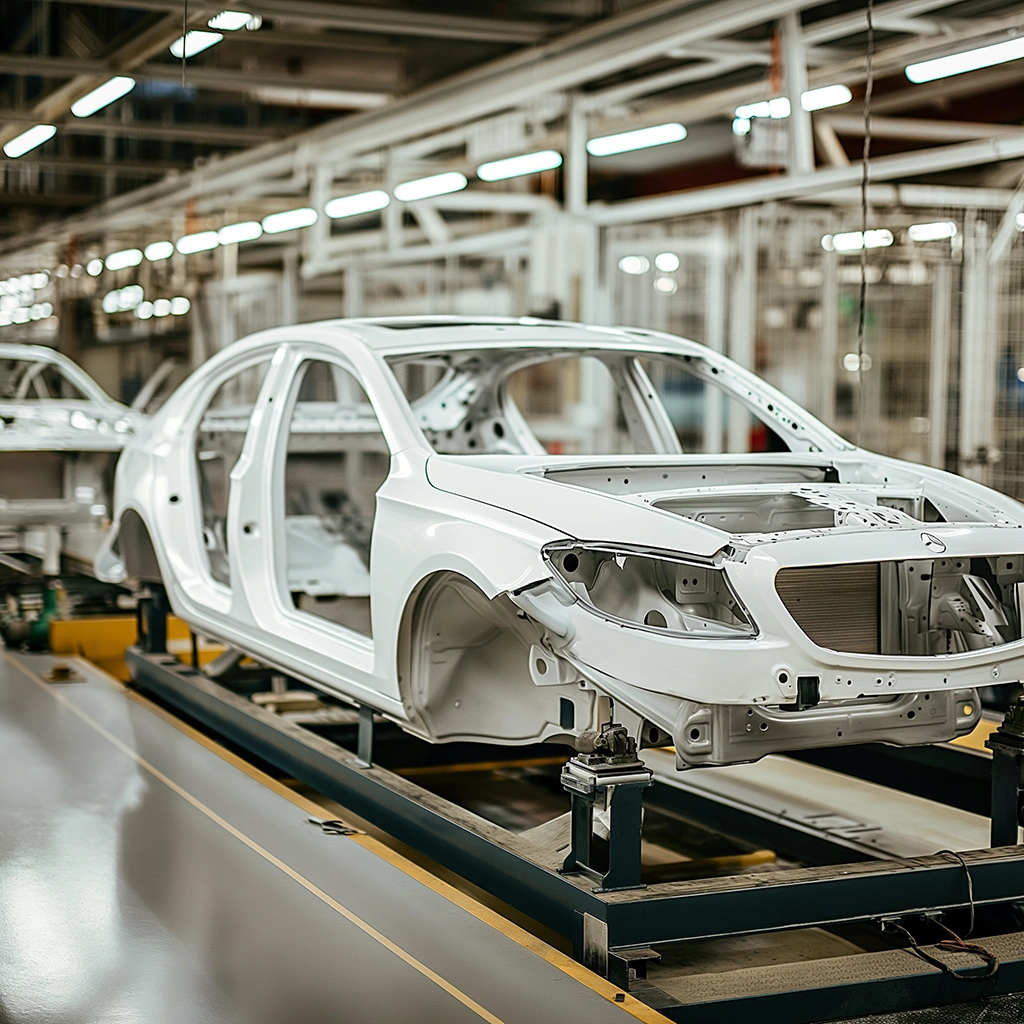
The TensilePolish GR04 is necessary for preparing specimens that will undergo these critical tests, making certain that the surfaces are polished to perfection and free from any micro-defects that could influence the test results. Key automotive components, such as engine pistons, suspension systems, and structural body panels, rely on accurate material testing to meet safety and performance standards mandated by regulatory bodies like the National Highway Traffic Safety Administration (NHTSA) and the European New Car Assessment Programme (Euro NCAP).
Why the TensilePolish GR04 is the Best Solution for Specimen Preparation
The TensilePolish GR04 offers unmatched precision and automation in specimen preparation, which makes it a valuable tool in industries requiring material integrity and accurate test results. By automating the polishing process for both cylindrical and flat tensile specimens, this system guarantees consistent, high-quality finishes that result in reliable testing outcomes for an array of demanding applications.
With its advanced features, including customizable polishing parameters, automatic sandpaper switching, and compliance with the highest industry standards, the Automatic Longitudinal Polisher System - TensilePolish GR04 stands out as a highly reliable and cost-effective solution. Whether used in aerospace, defense, automotive, or academic research, this tool allows laboratories and industries to achieve optimal results in material testing with minimal manual intervention.
If you are interested in learning more about the TensilePolish GR04 or would like to see the full product specifications, please visit its product page. Additionally, if you have any further questions or would like more details, feel free to contact us directly or through our online quote system. We are here to help you achieve excellence in material testing and support you in meeting your precision testing needs.