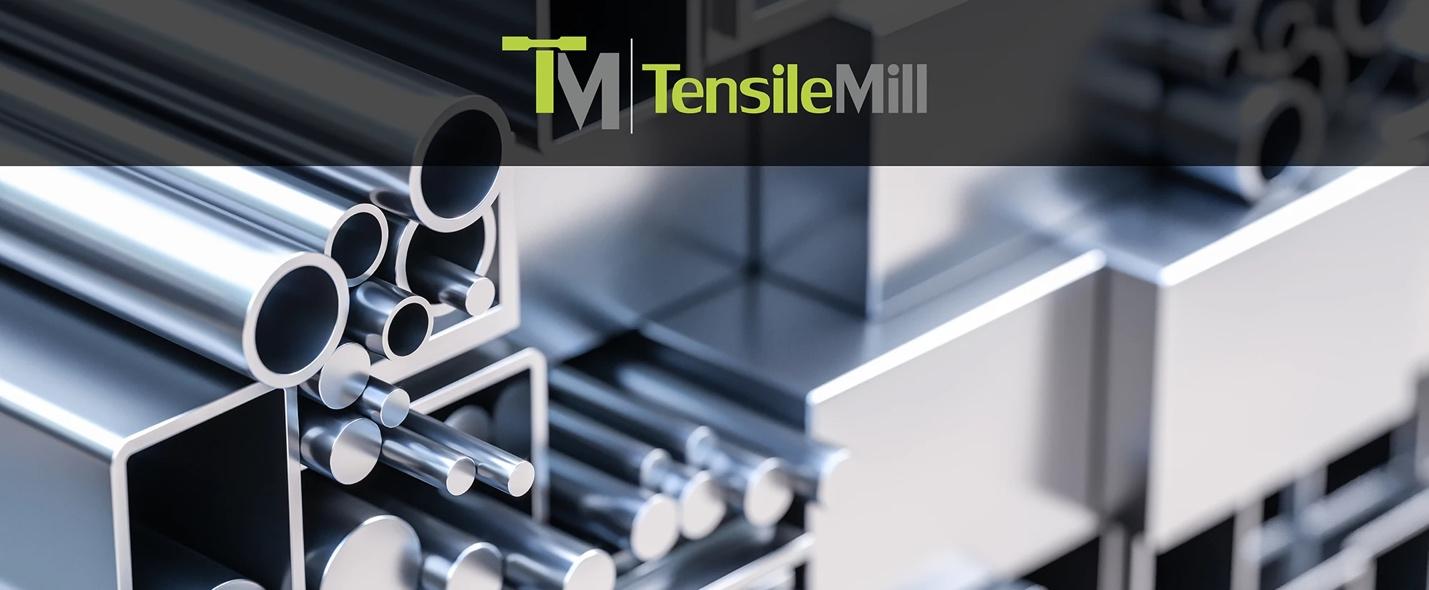
This article is dedicated to the multifaceted field of aluminum extrusion, where together with the reader we will learn how aluminum has become a part of our everyday life, why it is the most abundant metal in the air, and how consumer products are made from it. But first, let's talk about extrusion.
The Essence of The Extrusion Process
The essence of the extrusion process is to shape a plastic mass of material by forcing it through a molding hole (die opening) that corresponds to the profile of the final product. Machines for this process are called extruders. Each of us has used this principle when squeezing toothpaste out of a tube. Interestingly, the tube itself, regardless of whether it is aluminum or plastic, was also made using the extrusion process. So what is this process and why has it become commonly used in various industries? Let's find out!
Historical Note
Extrusion as a process for making pipes was patented by the English inventor Joseph Bramah in 1797. It involved preheating a sufficiently soft metal, lead, and then pushing it through a die using a manually operated plunger. Interestingly, the hydraulic press had been invented two years earlier by the same inventor, but the combination of these solutions, the use of a hydraulic press to advance the plunger, was only proposed in 1820 by Thomas Burr. Much later, in 1894, this process was extended to copper and brass alloys. Extrusion of steel, nickel, aluminum, and titanium alloys, as well as refractory alloys, appeared in the mid-20th century.
Basic Principles of Extrusion and How To Stay In Shape For Materials
Of course, in order to produce products and their components, it is necessary not only to create a mold but also to fix it. Therefore, the simple example of a toothpaste tube does not exactly correlate with the extrusion processes used in industry.
Most materials are extruded in the extruder chamber under conditions where the material becomes plastic and can therefore be pushed into the die opening. In most cases, an elevated temperature is used in the extruder chamber. As a result, the material becomes sufficiently pliable to be forced through the molding hole, whereafter it cools as it exits the chamber and thus retains its shape. Such processes are called hot or warm extrusion.
An interesting exception, in which it is the increased temperature after extrusion helps to maintain the shape of the product, is baking. Dough extruders are widely used in this industry, and dough is a very plastic material. In this case, the shape is retained during the baking process due to chemical transformations of the confectionery components. While the shape of most structural materials is maintained by cooling, where the general principle of increasing the hardness of materials with decreasing temperature works.
There are also methods of cold extrusion. In this case, sufficient plasticity of the materials is achieved by mechanical force, i.e., by creating increased pressure in the extruder chamber. The process takes place without significant heating the material. This process can be used to create high-quality metal parts that can be used in a variety of industries. The metal, usually in the form of a cylinder, is inserted into the extruder chamber and then mechanical force is applied to it. This causes the metal to be pushed out through the opening of the die, forming a product of the desired shape. The process is carried out using presses or special mechanical devices that provide the necessary mechanical force.
Cold extrusion is well suited for metals that have high ductility, such as aluminum, copper, brass, and stainless steel, although the specific alloy composition can significantly affect the applicability of the metal to this process. The main advantages of cold extrusion are the high precision and quality of the products obtained and the cost-effectiveness of the process.
The pressure to be used for metal extrusion depends not only on the properties of the metal itself, but also on the diameter and thickness of the material, as well as on the profile of the product to be manufactured. Typical pressures for cold extrusion range from 200 to 1500 bar. However, for larger output blocks or thinner profiles, significantly higher pressures may be required. In addition to pressure, other parameters such as extrusion speed, material temperature, product length, and die design must also be considered for successful cold extrusion. All of these parameters have an impact on the quality and accuracy of the resulting product.
In addition to metals, cold extrusion is also used for other materials such as plastics, ceramics, even glass and some types of food, such as sausages, candies, and more.
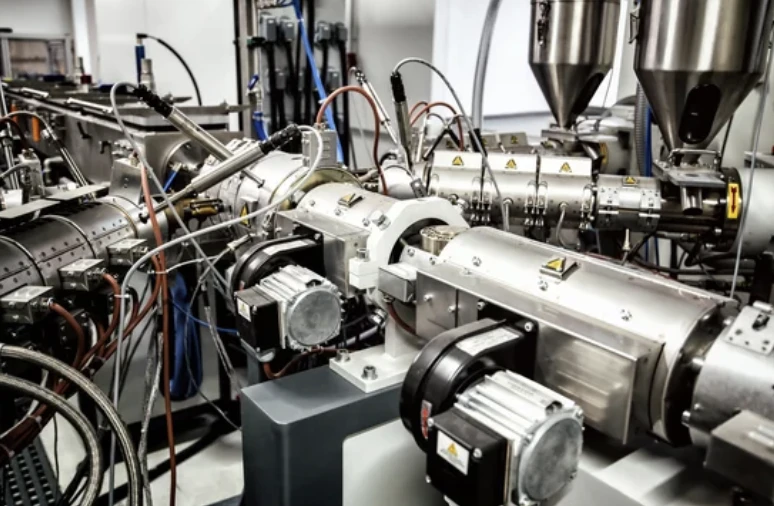
What Industries Use Extrusion?
The scope of the process is so vast that it is impossible to answer this question in detail in a single article. However, you can get an idea by realizing that this process is used in the following production areas.
-
Cooking
In addition to the cases mentioned above, pasta, corn sticks and other crispy snacks, and many types of packaging materials are produced by extrusion. -
Agriculture
For the production of seed materials for sowing, such as corn, soybeans, rice and others, as well as for the briquetting of animal feed. -
Medicine and pharmacy
Production of various polymeric tubes and hoses, catheters, filters for liquids and gases, packaging materials, surgical sutures, tablets, capsules, and films for coating tablets. -
Construction
A wide range of metal and plastic profiles, fasteners and connections, plastic pipes and much more. -
Electronics
Cases for electronic devices (phones, tablets, laptops), aluminum cooling radiators, wire insulation. -
Military
Kevlar and metal plates for body armor, knife and other weapon handles, metal rails for armored vehicles, metal housings for protected devices, and much more. -
Mechanical engineering
A huge range of products. For example:
- aluminum profiles for the manufacture of frames and frames, doors, windows and other structures,
- various metal and plastic pipes for transporting liquids and gases,
- composite materials for aircraft wings and fuselages, car bodies, watercraft and other vehicles.
The examples are chosen to demonstrate the widespread use of the extrusion process in various industries, from culinary to heavy engineering. We're getting close to discussing the main topic of the blog, aluminum extrusion, but first we need to answer the question: why aluminum?
Aluminum Fever, Or Why This Metal Was More Expensive Than Gold
Out of about a hundred metal elements in the periodic table, iron, aluminum, and zinc (Fe, Al, and Zn) are the most commonly used in modern industry. As a rule, the properties of pure metals do not meet the necessary requirements for structural materials, so in almost all areas of human activity, alloys are most often used rather than pure metals.
Iron alloys, steel, and cast iron have been known to mankind for more than 2500 years, so compared to this, aluminum has only recently entered the metal industry. Now we're going to find out how this happened.
When we throw a foil wrapper of a chocolate bar in the trash, we don't even realize that aluminum used to be more expensive than gold. In fact, it is the most abundant metal in the Earth's crust. But aluminum does not exist in nature in a metallic state and is found only in the form of compounds with other elements, most often with oxygen. Some jewels, such as rubies and sapphires, are mainly composed of aluminum oxides. Aluminum was discovered as a chemical element in 1825, but at that time it was very expensive to use in industry due to the difficulty of its extraction, which is caused by the stability of compounds of this metal with other elements. Thus, despite the fact that aluminum was literally under our feet, it remained a very rare precious metal, so it was especially valued. That's why Napoleon III honored his guests by setting the tables with aluminum appliances. The six-foot aluminum pyramid of the Washington Monument was an expensive extravagant decoration. At that time, gold, for which many people died, briefly faded into the background.
The situation was changed by the emergence and spread of electricity. In 1886, two inventors, the French engineer Paul Héroult and the American engineer Charles Martin Hall, independently invented a process that allowed them to produce aluminum from molten bauxite, a mineral, using an electric current (electrolysis). This process reduced the cost of aluminum and made it more affordable for industrial use. The price of aluminum slipped from $12 per pound in 1880 to 20 cents per pound in the 1930s.
Since then, aluminum has become the second most used metal in industry, but still far behind iron, steel, and cast iron alloys. Its price is usually higher than most steel grades because of the large amount of electricity required to produce it. However, it is what allowed people to fly easily.
So What Makes Aluminum a Unique Structural Material?
To lift something into the air, you have to overcome the force of gravity. This makes the weight of an airplane one of the most critical factors in its efficiency. But its reliability is also a necessary factor, which is ensured by the efficiency of its design and the strength of the materials used to make it. Aluminum is almost three times lighter than its most fierce competitor, iron, which is the main component of steels. At the same time, some aluminum alloys are not much inferior to steel in terms of strength.
Aluminum is a very reactive metal by its chemical nature. However, it is a great fortune for mankind that it reacts very quickly with air oxygen, which creates a thin but dense protective oxide film on the metal surface that protects it from further oxidation and deterioration. In fact, this is a sapphire film. That’s why int is very hard. Therefore, aluminum is a corrosion-resistant material. It is not surprising that when its price dropped significantly, it was used to create aircraft and quickly won the championship in the competition of flying metals. Add to this the ductility of aluminum, which allows the use of the extrusion process to process it. But this is the topic of the next part of the article.
Aluminum Extrusion Process
Aluminum extrusion is an industrial process for forming this metal, most suitable for the production of long aluminum profiles with a constant cross section. This includes unalloyed aluminum and aluminum alloys. Due to the ductility of aluminum, this material is suitable for extrusion, which is why this process is widely used in industry.
12 Pros Of Aluminum Extrusion
There are 12 main advantages of aluminum extrusion for molding.
1. Suitability of aluminum for hot extrusion
Hot extrusion of aluminum takes place at very high temperatures of up to 500 °C (~930 °F), at which the aluminum becomes soft and easy to form. The hot-extrusion process is used to create large workpieces such as airplane landing gear, facade profiles, bicycle frames, and more. The process is fast, but the surface condition of the product may require further processing.
2. Energy saving
Hot extrusion of aluminum requires significantly lower temperatures compared to the temperatures at which the steel hot extrusion process takes place (approximately 1600 °C, i.e. 2900 °F). Also, the pressure required for cold aluminum extrusion is much lower than for cold steel extrusion. Both of these factors make a significant contribution to the energy savings of extruding aluminum parts.
3. Suitability of aluminum for cold extrusion
Cold extrusion takes place at lower temperatures (less than 150 °C, about 300 °F), at which the aluminum remains solid but is forced through the molding hole under high pressure. This process is used to create thin walls of aluminum alloys, such as radiators or profiles for windows and doors. Cold extrusion typically takes longer, but the surface quality and accuracy of the shape can save time because there is no need for post-processing.
4. The possibility of optimum: Warm aluminum extrusion
The process takes place at an intermediate temperature, which can be the answer to finding a compromise between fast hot extrusion and a slower but more accurate cold process. The choice of temperature depends on the specific needs of the manufacturer and the properties of the final product.
5. Variety of shapes and sizes
Aluminum extrusion makes it possible to create a variety of products such as tubes, profiles, wires, sheets, plates, and others. The shapes can be round, square, rectangular, hexagonal and much more complex. By varying the size and shape of the outlet, and thus the pressure of the plunger, different product sizes can be achieved, from very thin to very thick. The process is suitable for manufacturing long lengths of product: it is possible to set up production of metal parts up to 100 meters long and even longer, which allows for the production of large metal structures. When combined with other metalworking methods, the availability of possible product shapes increases many times over.
6. Combination with other mechanical metal processing methods
Metal extrusion can be combined with various methods of further metal processing to help bring the product to the required shape, improve the quality and properties of the resulting products. Both mechanical and non-mechanical processing methods can be used here. The most commonly used method is cutting, which can be compared to how we cut a stick of sausage into convenient pieces for consumption.
Drilling allows you to make the necessary holes and grooves in the product. Bending, stamping and pressing can also be used to further modify the shapes created by extrusion. Surface polishing can be used to improve its smoothness. However, do not expect to maintain the bright shine of a newly polished aluminum surface. Over time, it will become dull again, as an oxide film quickly forms in the air on the surface of this metal.
The process of extruding aluminum and then machining the workpieces on digitally controlled milling and turning machines allows for significant shape changes with high dimensional accuracy.
7. Combination with non-mechanical metal processing methods
After extrusion and further machining, aluminum products can be processed using non-mechanical methods.
- Artificial aging: heating aluminum billets to relatively low temperatures (usually in the range of 100-200 °C, 210-390 °F) and holding them at these temperatures for dozens of hours. In this process, aluminum atoms and alloying additives are evenly distributed throughout the material, which results in its hardening and increased wear resistance.
- Aluminum anodizing is an electrochemical process that strengthens the naturally formed surface film of aluminum oxide that always forms on this metal in the air. Anodizing can be used to turn the surface into a decorative one, strengthening the oxide film to increase the product's resistance to corrosion.
- Galvanic treatment of an aluminum surface is also an electrochemical process by which thin layers of other metals, such as zinc, copper, nickel, or chromium, are applied to the surface of an aluminum product. This allows for additional corrosion protection, decorative properties, or specific structural capabilities, such as solderability, improved electrical performance, reduced friction, increased wear resistance, and improved adhesion to rubber.
- Laser processing - laser hardening can be used to improve the strength and stiffness of aluminum parts.
8. High precision and surface quality of products
This factor is also considered an advantage of the aluminum extrusion process, although the accuracy of the extrusion shape reproduction is high enough for most applications, it is usually inferior to the accuracy of machining parts on CNC machines. However, due to the ability to improve accuracy using other metalworking methods and in combination with the following advantages of the aluminum extrusion process, this process is preferred for mass production.
9. Increased strength
Products made by aluminum extrusion typically have increased strength and therefore wear resistance. This is because the material is formed under pressure to produce a homogeneous structure with no cavities, chips, or pores.
10. Low material loss
The nature of the process is such that it does not leave any excess material, such as chips and dust, which not only contributes to the economics of production, but also improves safety and reduces environmental impact. Combined with the low reject rate of a well-tuned production, this factor makes a significant contribution to its cost-effectiveness, which should be mentioned separately.
11. Efficiency and cost-effectiveness
Compared to other methods of aluminum processing, extrusion is superior to all other methods of processing this metal because extrusion can be easily adapted to assembly line production. The combination of these advantages makes the aluminum extrusion process very popular in production, as it allows for the production of a large number of parts with high precision in a short time. The high quality of the products is also guaranteed by the use of modern high technologies.
12. Processability
The use of automated production lines with pressure and temperature control by sensors ensures high efficiency of the extrusion process and a high degree of reproducibility of results. The use of modern computer control on conveyor lines, where robotic units perform monotonous heavy tasks, ensures the accuracy and efficiency of production. By calculating the required conditions using the processing of previously obtained data, it is possible to quickly find the optimal conditions for the introduction of new production lines.
Timely elimination of negative factors that may affect the quality of the extrusion product is possible only with the use of periodic quality control. Such control should take place at key stages of production, which is precisely what extrusion molding of aluminum parts is. It includes testing the mechanical properties of the product by tensile, bending, or compression testing.
Tensile Testing of Aluminum Extrusions for Quality Control
Perhaps the most common type of mechanical testing of aluminum is tensile testing. It is performed on standard specimens of a certain shapes, that can be round or flat. During the test, samples are stretched using special tensile machines with an axial force until they break. This allows us to obtain such indicators as maximum elongation, tensile strength, and maximum cross-sectional area narrowing. The quality assessment of aluminum profiles involves comparing the data obtained with certain standards.
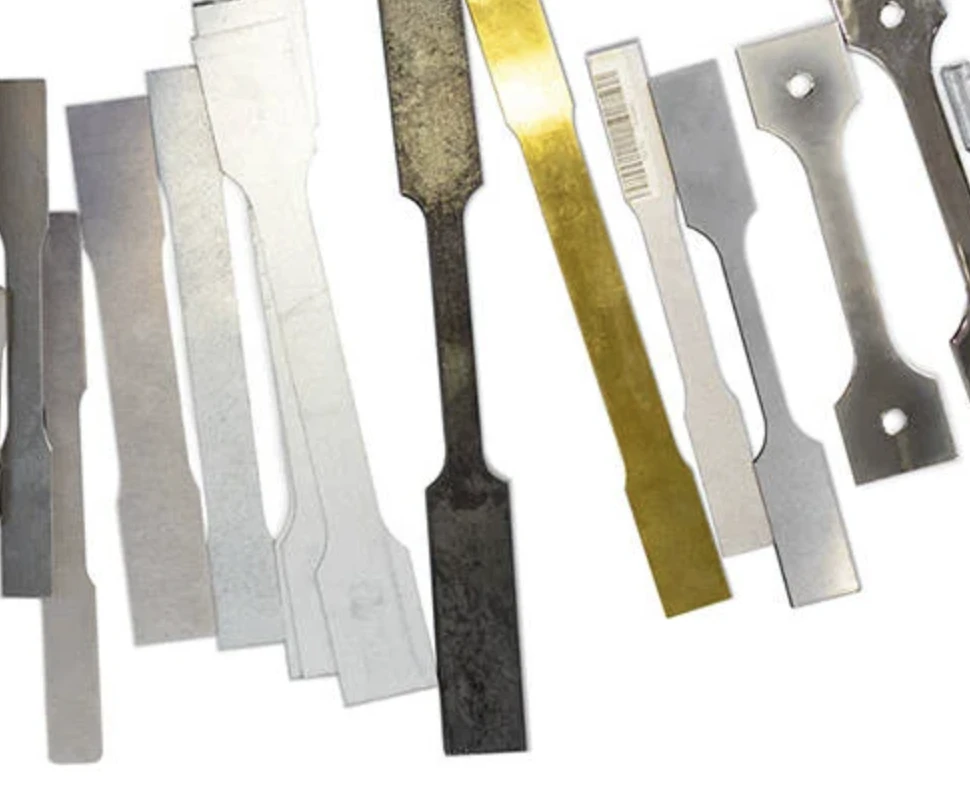
The walls of aluminum profiles are convenient for making flat specimens for tensile testing. These specimens are shaped like a dog bone, and are often called that. They are mounted in the clamps of the testing machine with wide ends, and the part inside is slightly narrowed, which is where the tear is observed. The quality of the specimen shape reproduction determines the test result. High-quality tensile specimens are produced on milling machines with software control. TensileMill CNC Inc. manufactures and sells such flat sample preparation machinesWe supply the market with several types of equipment directly for the preparation of flat tensile dog bone specimens.
The machines offered are very convenient and easy to use, requiring no special training or additional knowledge of the operators. Using tensile testing equipment allows you to work quickly and reliably, ensuring absolute data accuracy.
Flat tensile specimens have never been easier or more convenient to create. Go to the TensileMill CNC Flat Smaple Preparation Machine product page for a detailed description of the TensileMill CNC line and purchase details.