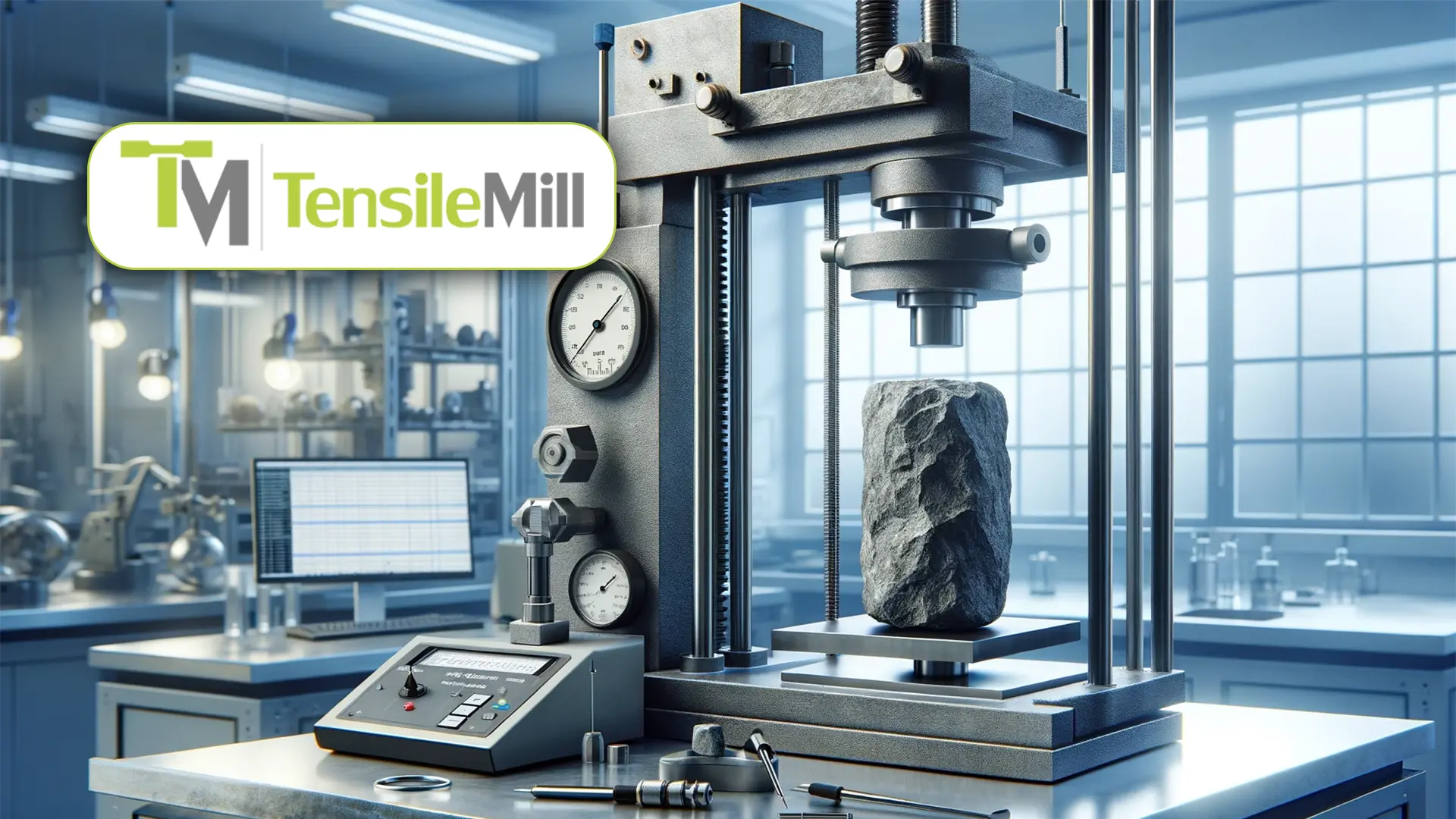
Chances are, you've heard the term "material testing" at least once in your life. It's pretty clear what it involves, but is it that straightforward? How are these materials tested? Where? And most importantly, why? Surprisingly, many of you might not realize that you encounter objects created through metal testing everywhere in your daily life. Regardless of whether you stumbled upon this article seeking answers to specific questions or simply to satiate your curiosity, we're here to provide the information you need.
In this blog, let's explore 11 answers to the most frequently asked questions about materials testing. We'll begin with the fundamentals, discussing what materials testing is, its applications, and its objectives. Then, we'll get into specifics such as the preparation of specialized specimens and the machines employed for materials testing.
1. What is Material Testing?
Material testing is a process that systematically determines the physical and mechanical characteristics of different types of materials. Many industries depend on this process as it determines how a material behaves under different loads and forces like tension, compression, bending, torsion, and shearing.
Historically rooted in early civilizations' use of materials, modern material testing has evolved over centuries, shaping industries from construction to aerospace. The evolution of material testing has been marked by the integration of digital technologies and automation into testing procedures, greatly enhancing the precision and efficiency of material testing in contemporary applications.
2. Why is Material Testing Important?
It might be difficult for someone who is not familiar with materials testing to grasp its importance. As we mentioned earlier, a lot of everyday items undergo thorough testing primarily to comply with international standards such as ISO/ASTM. This ensures that materials match the necessary characteristics and can be used in a range of applications.
Material testing provides engineers, designers, and production managers with information about tested materials, prototypes, and product samples. Compliance with regulatory agencies, selecting appropriate materials and treatments, evaluating product designs, and verifying the reliability of production processes all fall under this category.
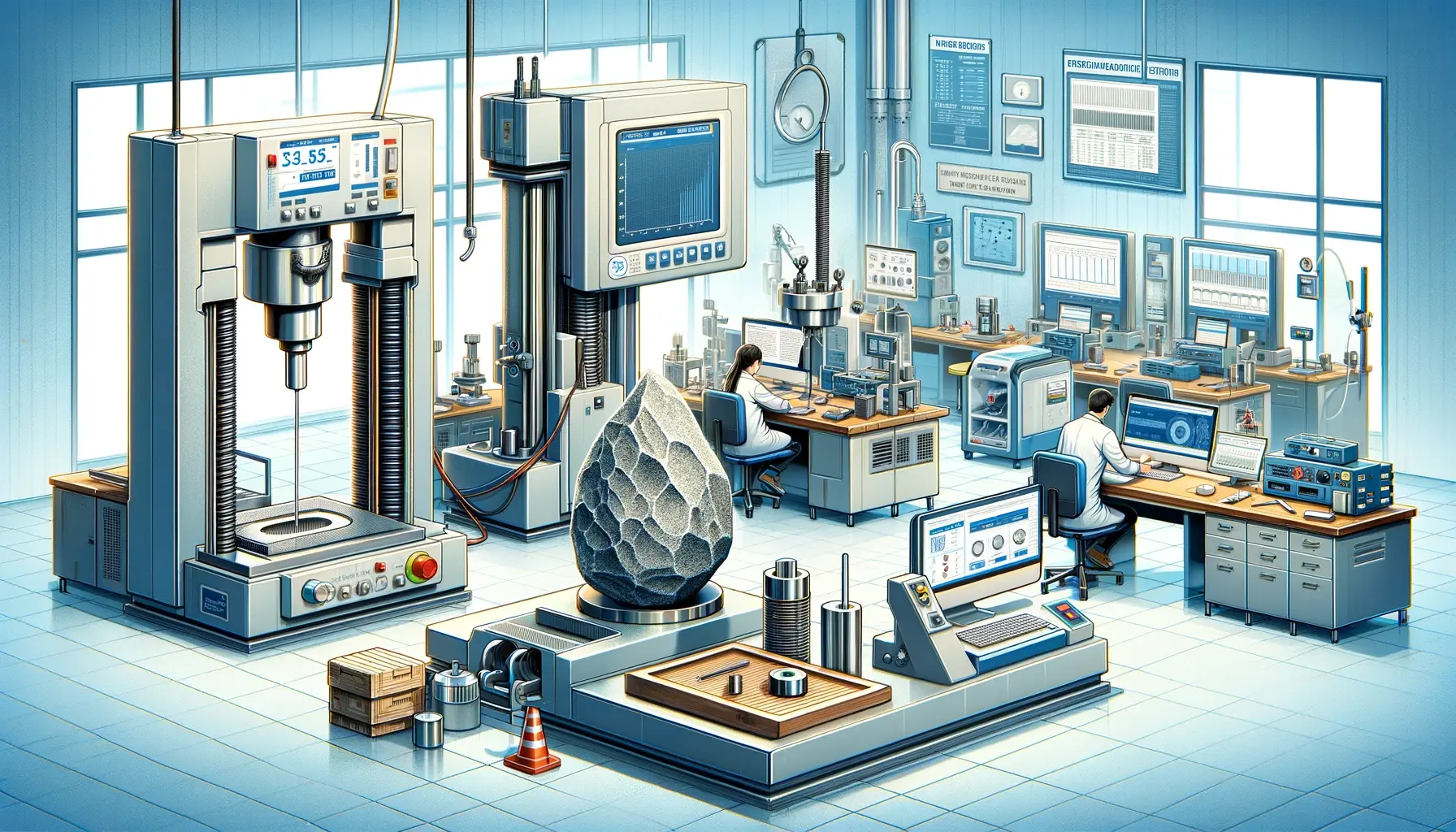
It is crucial to test materials in critical applications, where a failure could cause extensive damage or injury. Among these are safety-critical components in aircraft, bridges, vehicles, nuclear reactors, military equipment, and medical implants. Compliance requirements are set by governments and regulatory bodies, which often specify test procedures to demonstrate compliance.
Furthermore, material testing allows us to determine whether a particular material or treatment is suitable for a particular application. Testing helps narrow down options to the most appropriate choice for intended use since many types of materials and treatments are available. In addition, materials can be certified to meet given standards or specifications or verified to meet other stringent criteria before use.
It is common for businesses to use mechanical testing services when specifying materials for new product designs. The strength, hardness, elasticity, and fracture toughness of materials are evaluated during testing. For example, corrosion testing determines whether a material can withstand certain conditions like humidity or salt water.
For companies committed to selling reliable products and minimizing damage and costs, testing is crucial both in the design and manufacturing processes. In failure analysis investigations, non-destructive testing is fundamental in identifying defective products and inadequate materials.
By 2028, the market for material testing is expected to reach $1,8 billion in the United States. Growth in this sector is largely attributed to its widespread use in key sectors. Testing building materials is a critical part of the construction process. Automotive companies rely on it to develop advanced, high-performance materials. In aerospace applications, material testing ensures the reliability of complex mechanical components. Medical devices and implants use it extensively for evaluating their compatibility and resilience, as well as for evaluating their durability.
3. Which Components Are Tested in Material Testing?
Material testing covers an extensive range of materials, examining everything from nanoscale particles to steel, highly complex alloys, and rugged rock formations. Among other things, this field includes testing substances like water, determining its properties and interactions with other materials in different environments. Based on their physical properties, these materials can be categorized into three groups: hard, soft, and medium.
Hard Materials
Metals: Metals such as steel, aluminum, copper, and their alloys fall into this category. Each metal has unique properties and is tested for specific characteristics like tensile strength and corrosion resistance.
Ceramics: Ceramics are nonmetallic, inorganic materials whose hardness, brittleness, and thermal conductivity are often tested.
Glass: Due to its hard and fragile nature, glass is tested for strength, especially in terms of impact resistance and breakage patterns.
Hard Plastics and Polymers: Some plastics, such as polycarbonates and acrylics, are known for their rigidity and fracture toughness.
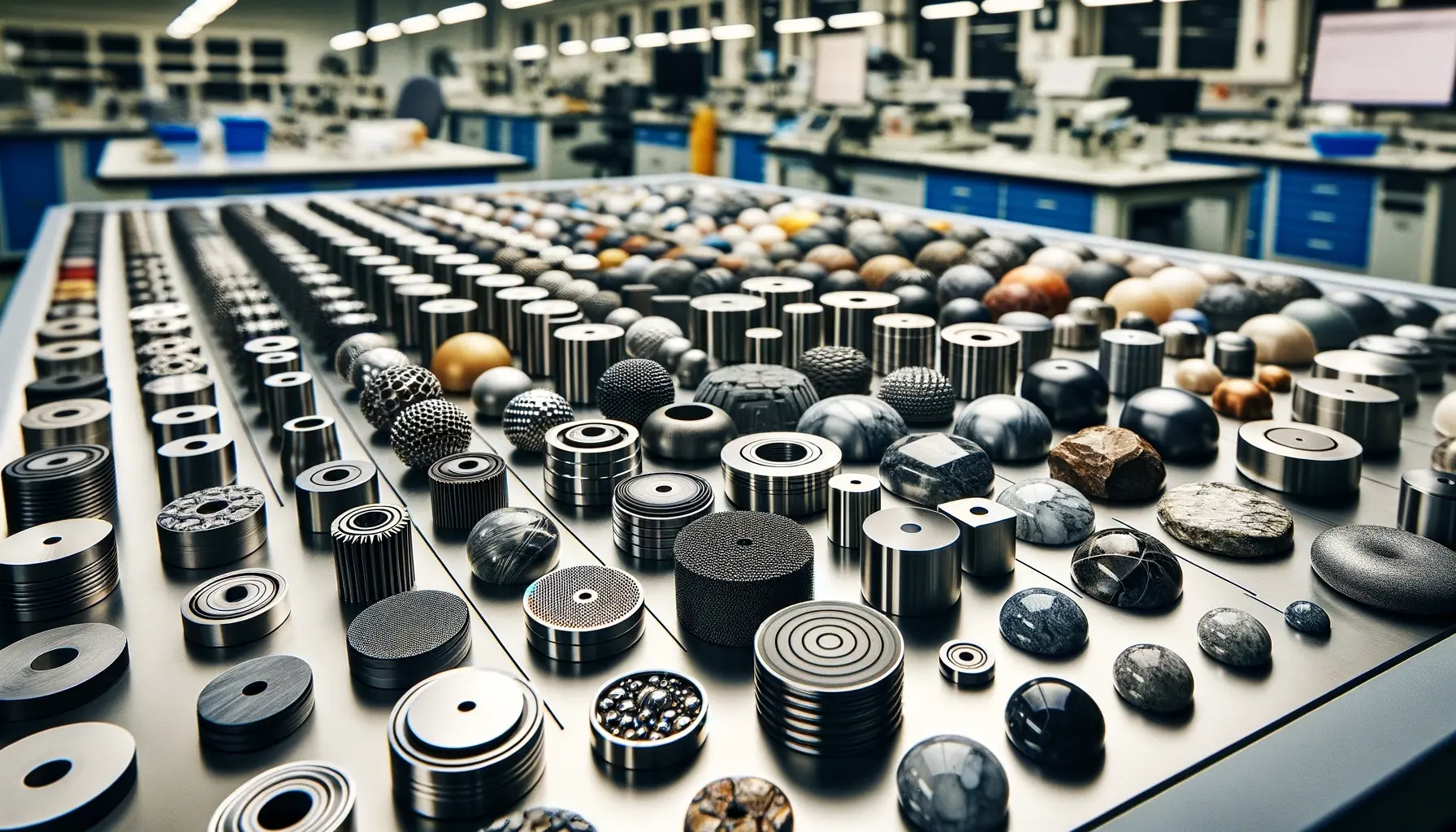
Medium Materials
Composite Materials: Materials made from two or more constituents with physically or chemically differing properties. Tests are often conducted to determine how they interact under varying conditions based on their combined characteristics.
Wood and Wood Products: As a natural composite material, wood is tested for its moisture content, strength, and durability.
Hybrid Materials: Materials with a combination of hard and soft components are tested for their unique combination of properties, such as flexibility and strength.
Soft Materials
Rubber: Both natural and synthetic rubber are commonly tested for elasticity, durability, and resistance to UV light and ozone.
Elastomers: Often tested for stretchability and recovery after deformation, these materials exhibit rubber-like properties.
Soft Polymers and Plastics: Flexible and resilient materials like polyethylene, polypropylene, and PVC are tested for tensile strength, elongation, and compressibility.
Textiles and Fabrics: Materials of this type are tested for tensile strength, wear resistance, and UV resistance.
4. Which Methods Are Applied to Material Testing?
There are two main types of material testing: destructive testing and non-destructive testing. Each method is designed to assess diverse aspects of material properties and integrity. Destructive testing involves altering or destroying the material to analyze its characteristics, whereas non-destructive testing does not cause any permanent damage to the material. Exploring advanced techniques and studying these methods can help gain a more comprehensive understanding of how materials are evaluated and tested.
Destructive Testing
Fracture and Mechanical Testing: This includes tension tests, bend tests, Charpy impact tests, Pellini drop weight tests, peel tests, crush tests, pressure tests, and fracture tests. Materials like welded polymers and plastic pipes are also subjected to such tests.
Aggressive Environment Testing: Materials are tested in corrosive environments, such as those with hydrogen sulfide (H2S) and carbon dioxide (CO2). Material performance can be gauged under adverse conditions by testing it at different temperatures and pressures.
Fatigue Testing: This tests the durability of materials and welded joints under repeated loads in air or seawater. Understanding the growth of fatigue cracks in welds, base metals, and heat-affected zones can be critical.
Tensile Testing: Applying a tensile load until the specimen breaks to determine the tensile strength, yield strength, and elongation of materials. Metals, plastics, and composites are commonly evaluated with this method.
Hydrogen Testing: This test focuses on materials that are susceptible to corrosion caused by hydrogen. Material vulnerability to hydrogen is determined by testing it at different temperatures and strain rates.
Residual Stress Measurement: Post-stress removal residual stresses can either be intentional (for scratch resistance) or unintentional. Structural integrity assessments require their measurement.
Hardness Testing: Determines the resistance to deformation by applying a load and measuring the indentation. Metals, ceramics, and plastics require this to assess their hardness.
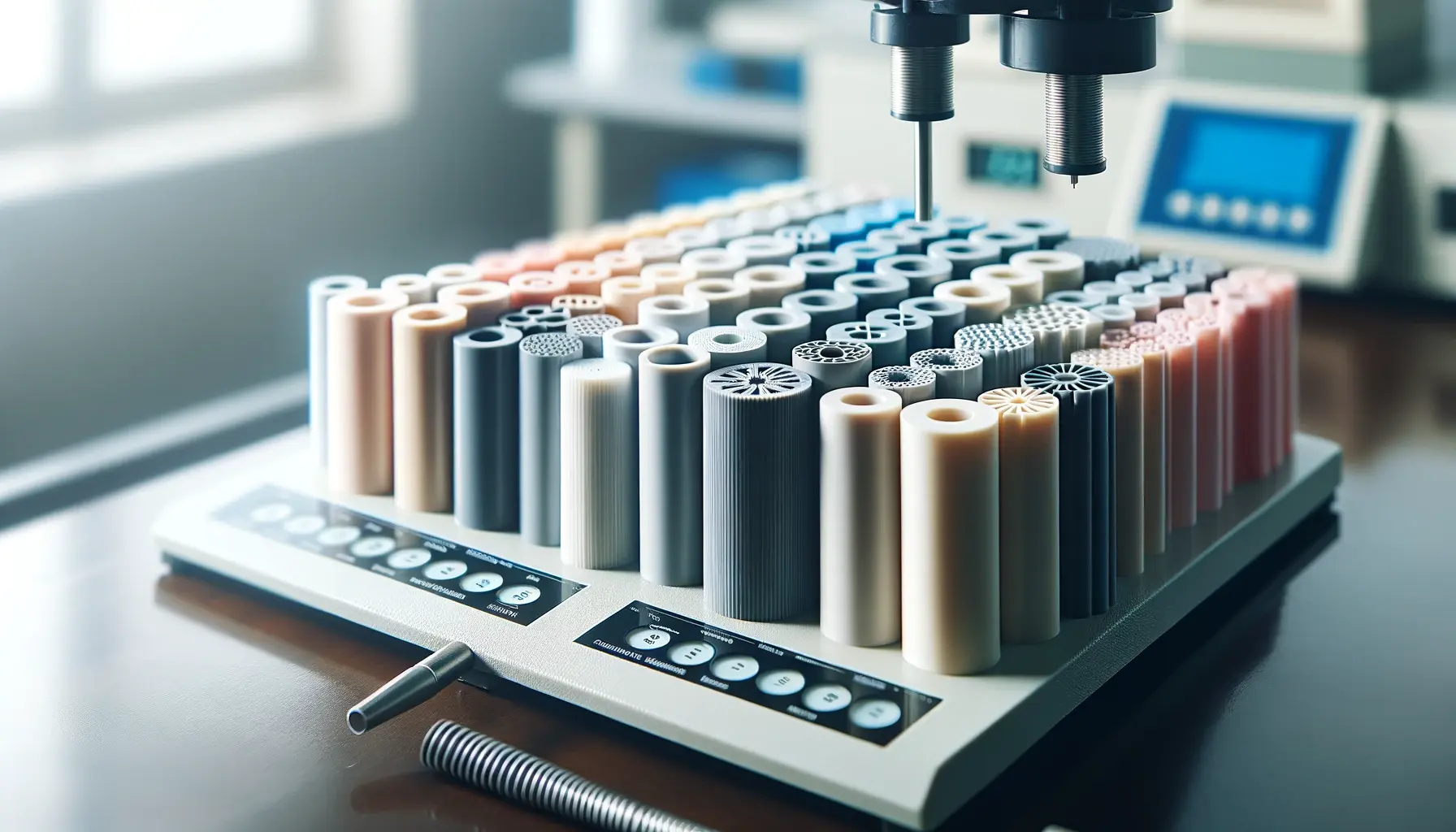
Non-Destructive Testing (NDT)
Ultrasonic Testing (UT): A technique for determining the thickness, size, and location of defects inside materials using high-frequency sound waves. Aerospace, petrochemicals, and automobiles are among the industries that use it.
Magnetic Particle Testing (MT): Detects discontinuities in ferromagnetic materials using magnetic fields. The use of iron oxide particles reveals defects visibly.
Radiographic Testing (RT): Analyzing materials' internal structures with X-rays or gamma rays. Welds and composites are inspected using this method in aerospace and petrochemical industries.
5. What is the Role of Material Testing in Civil Engineering?
Material testing in civil engineering cannot be overemphasized, as it significantly impacts this sector through its comprehensive evaluation of construction materials such as concrete, steel, soil, and aggregates. Modern infrastructure is built on these materials. As an example, engineers perform water-cement ratio analysis and compressive strength tests for concrete to determine the ideal mix and ensure strength compliance. For the same reason, steel, a crucial component of construction, undergoes tensile strength and bend tests to verify its ability to withstand tension forces.
When it comes to building projects, soil testing is also one of the crucial parts of assessing ground suitability. Tests such as soil compaction and bearing capacity analysis ensure that the soil is dense and strong enough to support structures. Similarly, sand and gravel are tested for crushing and impact values to ensure high-quality concrete.
Non-destructive testing (NDT) methods like ultrasonic testing and X-ray radiography, which we referred to in the answer to the previous question, are used to evaluate existing structures' integrity. Engineers can use these techniques to inspect internal structures and detect hidden defects without damaging them. Public safety depends on regular inspections and assessments, such as those conducted on bridges. A visual inspection and a load test determine whether a bridge is structurally sound and identify potential issues.
Skyscraper construction is another essential aspect of materials testing. For these tall structures to be stable against environmental forces, they must undergo tests for wind load resistance. For road construction, California Bearing Ratio (CBR) tests evaluate the bearing capacity of subgrade soils, which is crucial for the durability of roads.
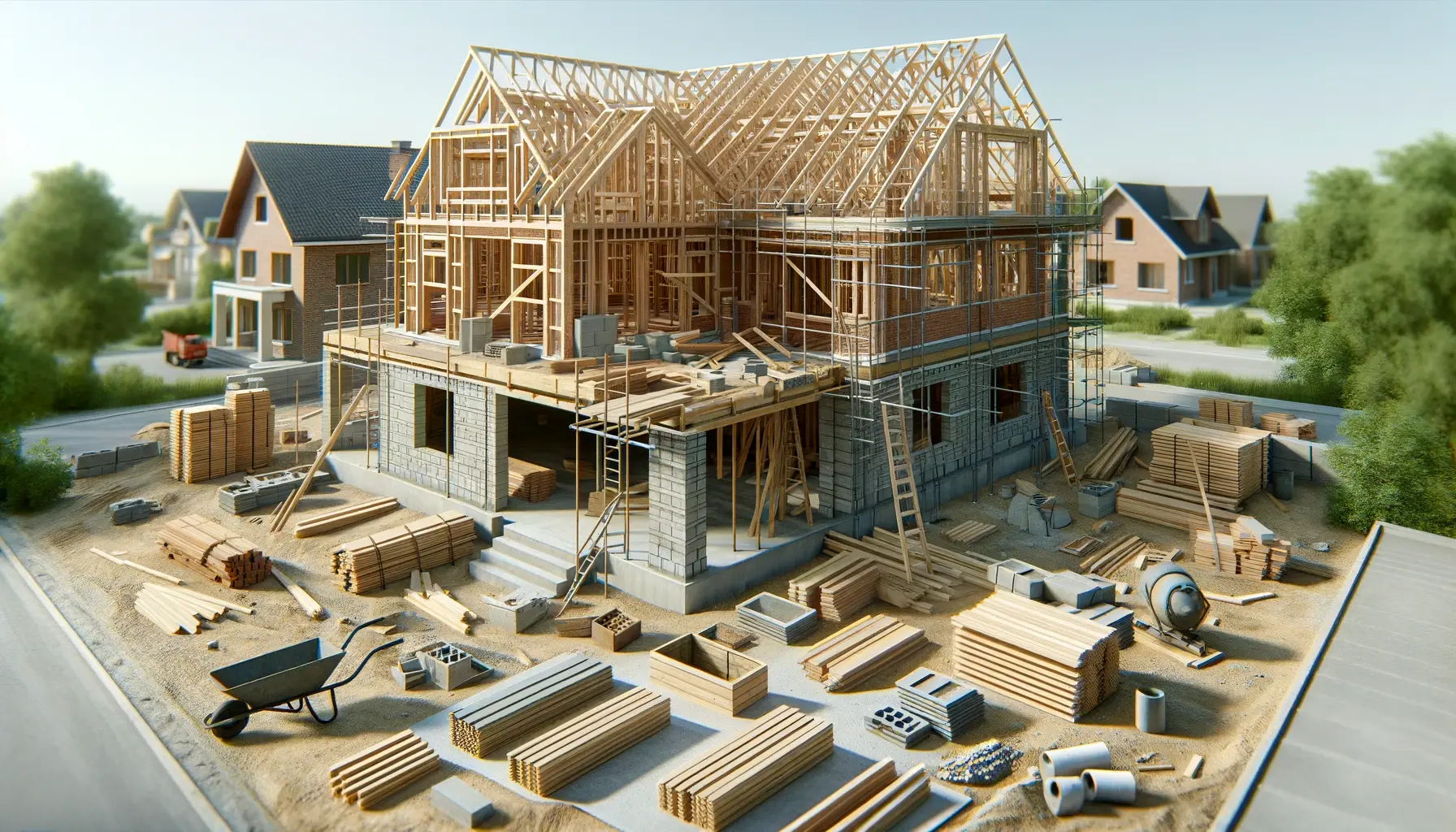
6. Examples of Material Testing Applications
Our daily lives are filled with objects and materials that have undergone material testing processes. Every item that we constantly use, from the seemingly mundane spoon in our kitchen to the critical cables in the elevator to our office, is a product of thorough material testing. Material testing has an array of applications across a number of industries, impacting the functionality and safety of many types of products and structures. Some notable examples are:
Building and Construction: Materials used in construction, from steel in skyscrapers to concrete in sidewalks, undergo rigorous testing. They are tested to ensure that they can withstand everyday stresses and extreme conditions like earthquakes and heavy traffic.
Automotive Industry: Automobiles are constructed from a variety of materials, each of which is carefully tested to guarantee safety and performance. A body frame's metal, an interior's plastic, and a tire's rubber are tested in this manner.
Aerospace: Materials used in aircraft must withstand extreme conditions, such as high pressure and temperature variations. Tests include those on metals for fuselages, composite materials for wings, and glass for cockpit windows.
Consumer Electronics: Mobile devices, laptops, and other electronic devices are tested for durability, electrical conductivity, and moisture resistance.
Medical Devices and Equipment: In order to ensure patient safety and device effectiveness, the materials used in medical devices must be biocompatible, strong, and long-lasting.
Packaging Industry: Materials used in packaging are tested for strength, durability, and their ability to withstand environmental conditions. A box is tested using cardboard, a container is tested using plastic, and a bottle is tested with glass.
Textiles and Apparel: Fabric and clothing materials are tested for tensile strength, elasticity, colorfastness, and wear resistance.
Sports Equipment: Sports equipment undergoes material testing to verify safety and performance. A bicycle's composite parts, rubber's athletic shoes, and gym equipment's metals may all be tested in this way.
Infrastructure: Roads, bridges, and tunnels undergo material testing to be sure heavy loads can be carried and the environment is not damaged by them over time.
Environmental Impact Assessments: Determining the sustainability and ecological footprint of materials requires testing for their environmental impact.
7. What Are Material Testing Laboratories?
Material testing laboratories are dedicated facilities that comprehensively examine different materials to determine their physical and mechanical properties. Nevertheless, they differ from typical medical research laboratories because they have a more dynamic and industrious atmosphere, adapted to the nature of the materials they work with.
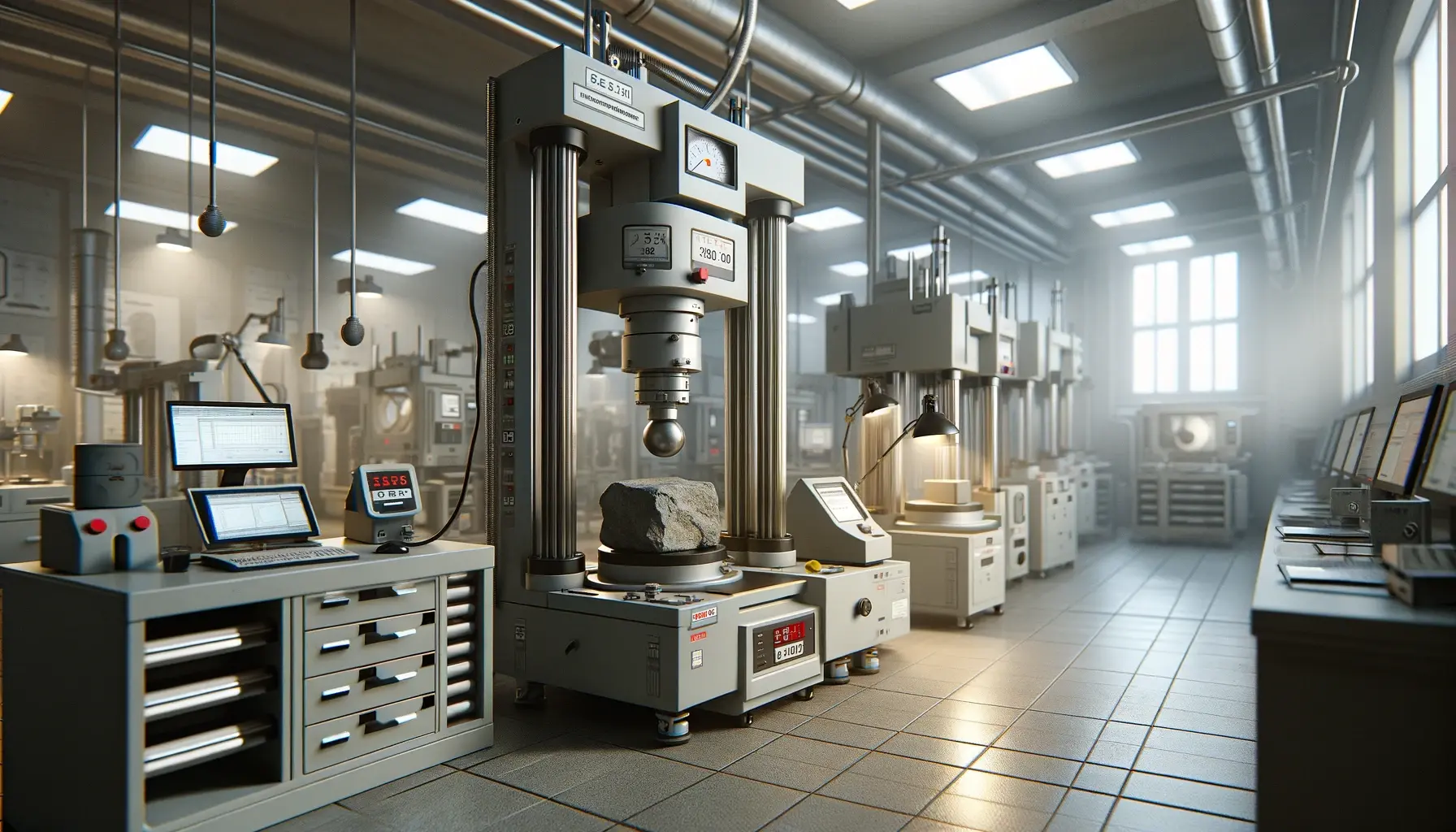
You won't only find test tubes or beakers filled with liquid in these labs. Rather, they are equipped with robust tools for handling and testing a broad range of materials, including metals, wood, and stone. These spaces are usually bustling with activity due to tools such as impact testing machines, tensile testers, and computerized oedometers, which can lead to the accumulation of shavings, dust, and other byproducts of testing.
Material testing laboratories perform numerous tasks. Some labs specialize in specific types of testing, such as tensile testing of metals or soil analysis. Test results from these specialized facilities are highly precise and accurate due to their tools and expertise specific to their chosen focus area.
Many laboratories, however, focus on a range of testing types, encompassing a greater scope of services. From tensile testing to detailed soil analysis, these labs can handle everything. Choosing a specialization depends on the lab's program and resources, as well as the demands of its client base. As a result of this diversity, material testing can be approached holistically, catering to the needs of many industries.
Canada, for example, hosts a number of these laboratories. Besides meeting domestic needs, these laboratories also contribute to international material science research and development. Depending on the industry, the number of labs can vary. However, their presence is vital to developing and validating materials used in everyday life.
8. What is a Material Testing Machine?
Materials testing machines, also known as universal testers or materials test frames, are devices designed to determine the specific characteristics of a material. Each material testing machine is made to meet the testing requirements of a different material. As an example, a universal testing machine (UTM) is versatile, capable of performing various tensile and compression tests on materials, components, and structures.
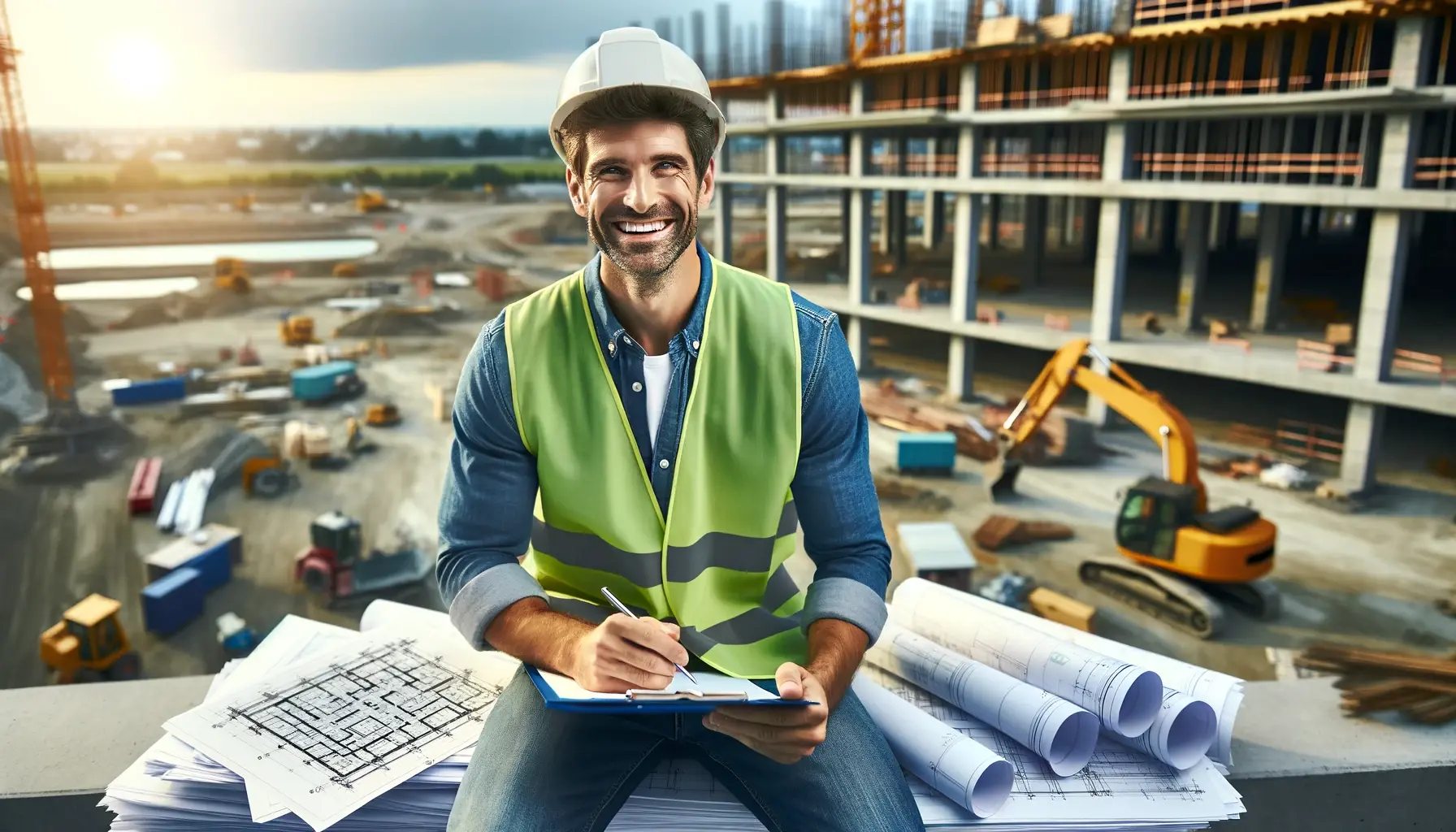
However, some material testing machines require specific samples for testing, reflecting the nuanced nature of the process. A heterogeneous soil composition, for example, makes it difficult to obtain a representative soil sample. In contrast, tensile testing requires specialized samples that are usually round or flat (dog-bone shape). In most testing protocols, specimen preparation machines are used to produce these samples. Based on methods published by standards organizations, machines differ widely in their setup and usage. Their scope ranges from small tabletop systems to large-scale machines with capacities exceeding 53 MN (12 million lbs), attesting to their versatility and widespread use.
9. What Are the Most Common Material Testing Methods?
There are dozens of types of material testing, but which are considered the most common? Here are some of the most frequently used materials testing methods:
Tension Testing
The tension test is a fundamental method for evaluating the behavior of materials under tensile stress. The strain and breaking point of the material are measured by static tension testing or the gradual increase of loading. Metals and polymers often undergo this test on cylindrical pieces or pieces with a narrow middle section. Dynamic tension testing, another subtype, simulates real-world conditions by testing materials under rapid changes or cyclic loads.
Tensile testing follows tension testing as a prominent submethod. Stretching a sample until it breaks is an effective way to measure a material's strength and ductility. Materials like steel, aluminum, and plastic perform better in real-world applications when they are tested under tension, which is why tensile testing is crucial for industries like construction and manufacturing. Quality control and material certification are particularly dependent on this method.
Compression Testing
A compression test determines a material's response to crushing or support loading. It is typically divided into uniform compression testing, which applies a consistent load to the entire cross-section of the specimen, and buckling compression testing, which identifies the load at which a material or structure will buckle. Usually used in the testing of building materials like concrete, wood, and metal, compression testing is indispensable when designing load-bearing elements like beams and columns.
Shear Testing
A shear test evaluates thin sheet materials such as metals and composites like fiberglass-reinforced plastics. Subtypes of this method include single shear testing, in which loads are applied in one plane. Double-shear testing involves forces in two planes, assessing material response to more complex shear stresses. Component design in industries like aerospace and automotive depends heavily on understanding a material's shear strength.
10. What is a Material Testing Company?
Material testing company is a specialized entity that offers assurances to numerous industries about materials and products' quality, safety, compliance, and suitability. They use various tests to analyze the properties and performance of metals, polymers, composites, and ceramics. Globally, material testing is a significant market, reflecting the critical need for these services.
It is common for companies in this field to operate internationally, with laboratories and experts located in multiple countries. As an example, one leading material testing company operates hundreds of laboratories across many countries and employs thousands of experts. Having a global presence enables the company to cater to the diverse needs of its clients.
Diverse industries rely on material testing companies for a comprehensive range of services. These services include mechanical testing to determine a material's strength and durability. They also include thermal and environmental testing to determine how it behaves under different conditions, and fatigue and fracture testing to assess how materials can withstand repeated stress. Furthermore, they provide corrosion testing to check materials' resistance to corrosive environments and metallurgical testing to analyze metal properties. Also key is non-destructive testing, which allows materials to be inspected without causing any damage.
Besides offering these services, material testing companies, such as TensileMill CNC, also provide all the necessary equipment for testing materials. Among them are machines for tensile testing, devices for measuring material hardness, tools for environmental simulation, and non-destructive evaluation instruments. As well as handling flat and round test specimens, they also provide equipment for preparing test specimens.
11. Who Can Own Specialized Material Testing Equipment?
Material testing equipment can be purchased by anyone. For instance, equipment like that is often purchased by construction companies, laboratories, manufacturing firms, educational institutions, and research organizations. Test equipment should be selected based on the materials to be tested and the specific requirements of the test.
A construction company might use this equipment to test concrete and soil, ensuring they comply with quality and safety standards. In laboratories and research settings, including those in educational settings, material testing equipment is used for a variety of destructive and non-destructive tests. Quality control, materials science, and engineering all depend on this.
Even small businesses should also buy and use specialized testers for their products. In addition to ensuring quality and compliance with standards, this also enhances the credibility and reliability of the products. By implementing in-house testing, production processes can be more efficient, and quality control can be improved.
TensileMill CNC offers advanced tensile testing equipment for some industries, catering to a broad range of needs. Our products include high-quality specimen preparation machines for both round and flat specimens, as well as versatile universal testing systems. With our machines, businesses can accurately assess the quality and compliance of their materials and products. By continually innovating, we ensure that our equipment remains an essential tool for companies whose goal is to maintain high levels of material quality and safety.
Putting Puzzle Pieces Together About Material Testing
Throughout our daily lives, material testing influences the functionality and safety of countless products and structures. The process of determining the physical and mechanical properties of materials is essential to many industries, including construction, aerospace, automotive, and even medicine.
Material testing is based on the ability to predict how materials will behave under different forces and conditions. Whether it's the strength of steel used in skyscrapers or the durability of plastics in consumer electronics, material testing ensures that these materials will withstand everyday stresses and extreme conditions.
The scope of material testing extends from hard materials such as metals and ceramics, to medium materials such as composites and hybrid blends, as well as softer materials such as rubber and polymers. Each category of materials presents distinct properties and challenges for testing, ensuring their suitability and performance in various applications. Each material has unique properties that require specific testing, including hardness, flexibility, and resistance to environmental factors. For example, textiles are tested for wear resistance and UV durability, while metals are tested for tensile strength and corrosion resistance.
During construction projects, material testing is crucial to verifying the integrity of materials. Whether it's analyzing the ideal concrete mix for strength and durability or verifying steel reinforcement tensile strength, material testing ensures infrastructure safety and reliability.
The right testing equipment is a necessity for many types of applications, from soil and concrete testing to sophisticated material analyses in laboratories. Our team at TensileMill CNC specializes in creating tensile testing equipment essential to a broad range of industries. Among our collection are specimen preparation machines for round and flat specimens, as well as universal testing systems. Tools like these are vital to maintaining the highest safety and material quality standards. They are also durable, precise, and easy to use. Learn more about TensileMill CNC's innovative solutions and their impact on material testing. Get in touch with us or request a quote to learn how you can improve your business.